The IC 555 is an extremely useful and versatile device which can be applied for configuring many useful circuits in the field of electronics. One very useful feature of this IC is its ability to generate PWM pulses which can be dimensioned or processed as per the needs of the application or the circuit.
What’s PWM
PWM stands for pulse width modulation, a process which involves the control of the pulse widths, or the ON/OFF periods or logical outputs that's generated from a particular source such as an oscillator circuit or microcontroller.
Basically PWM is used for dimensioning or trimming the output voltage or power of a particular load as per individual or application requirements.
It is a digital way of controlling power and is more effective than analogue or linear methods.
There are many examples which illustrates the effective use of PWM in controlling the given parameters.
It's used for controlling the speed of DC motors, in inverters for controlling the RMS of the output AC or for producing modified sine wave outputs.
It can be also seen in SMPS power supplies for controlling the output voltage to precise levels.
It's also applied in LED driver circuits for enabling LED dimming functioning.
It's extensively used in buck/boost topologies for deriving stepped down or stepped-up voltages without using bulky transformers.
So basically it may be used for tailoring an output parameter as per our own preferences.
With so many interesting application options, does it mean the method may be too complicated or expensive to configure??
The answer is definitely, no. In fact it can be very simply implemented using a single IC the LM555.
There are basically two methods through which the IC 555 can be used for generating pulse width modulation output. The first method is using only a single IC 555, and a few associated parts such as a diodes, a potentiometer and a capacitor. The second method is by using a standard monostable IC 555 configuration and using an external modulation signal.
IC 555 PWM using Diodes
The first method is the simplest and effective, which uses the configuration as shown below:
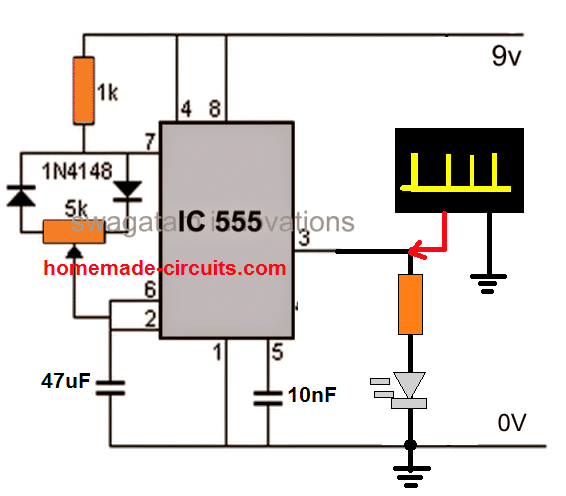
Video Demonstration
The working of the above shown two diode IC 555 PWM circuit is quite simple. It's in fact a standard astable multivibrator design with the exception of an independent ON/OFF period control of the output.
As we know that the ON time of the IC 555 PWM circuit is decided by the time taken by its capacitor to charge at the 2/3rd Vcc level through pin#7 resistor, and the OFF time is determined by the discharging time of the capacitor below 1/3rd Vcc through the pin#7 itself.
In the above simple PWM circuit, these two parameters can be independently set or fixed through a potentiometer and through a couple of bifurcating diodes.
The left side diode which has its cathode connected with pin#7 separates the OFF time, while the right side diode which has its anode connected to pin#7 separates the ON time of the IC output.
When the potentiometer slider arm is more towards the left side diode, it causes the discharge time to decrease, due to lower resistance across the discharging path of the capacitor. This results in an increase in the ON time, and decrease in the OFF time of the IC PWM.
Conversely, when the pot slider is more towards the right side diode, it causes the ON time to decrease due to lowering of the resistance of the pot on the charging path of the capacitor. This results in an increase in the OFF period, and decrease in the ON periods of the IC output PWMs.
You can replace the timing resistors with a single potentiometer if you want to alter the duty cycle while keeping the frequency constant, as depicted in the following figure.
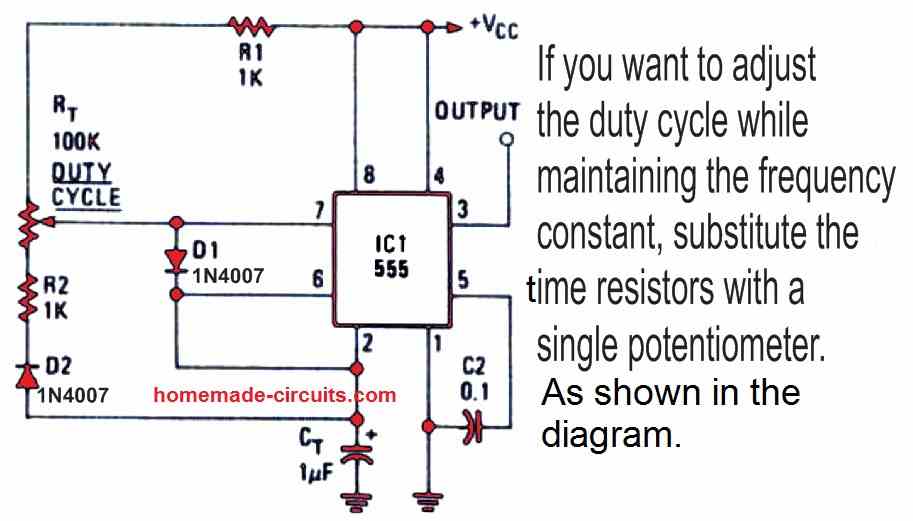
The 555 circuit may be adjusted as illustrated below to change the frequency while keeping the duty constant at around 50%.
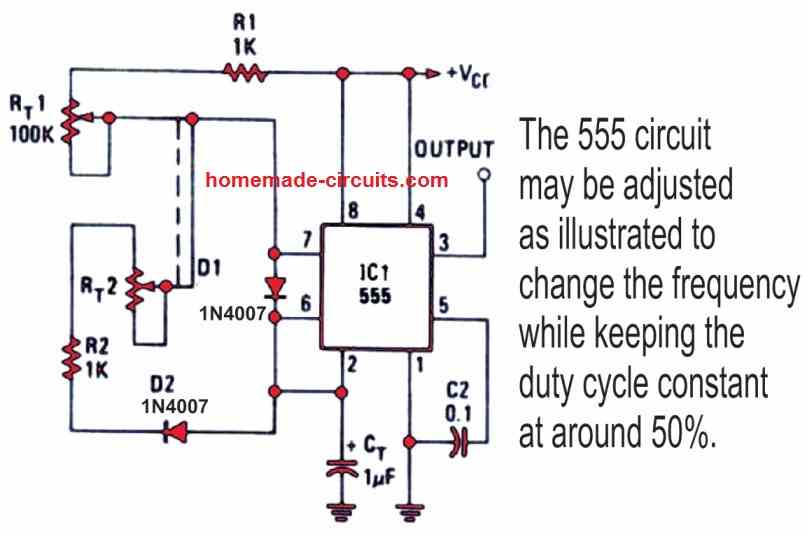
2) IC 555 PWM using External Modulation
The second method is slightly complex than the above, and requires an external varying DC on pin#5 (control input) of the IC for implementing the proportionately varying pulse width at the IC output.
I will explain the following simple circuit configuration:
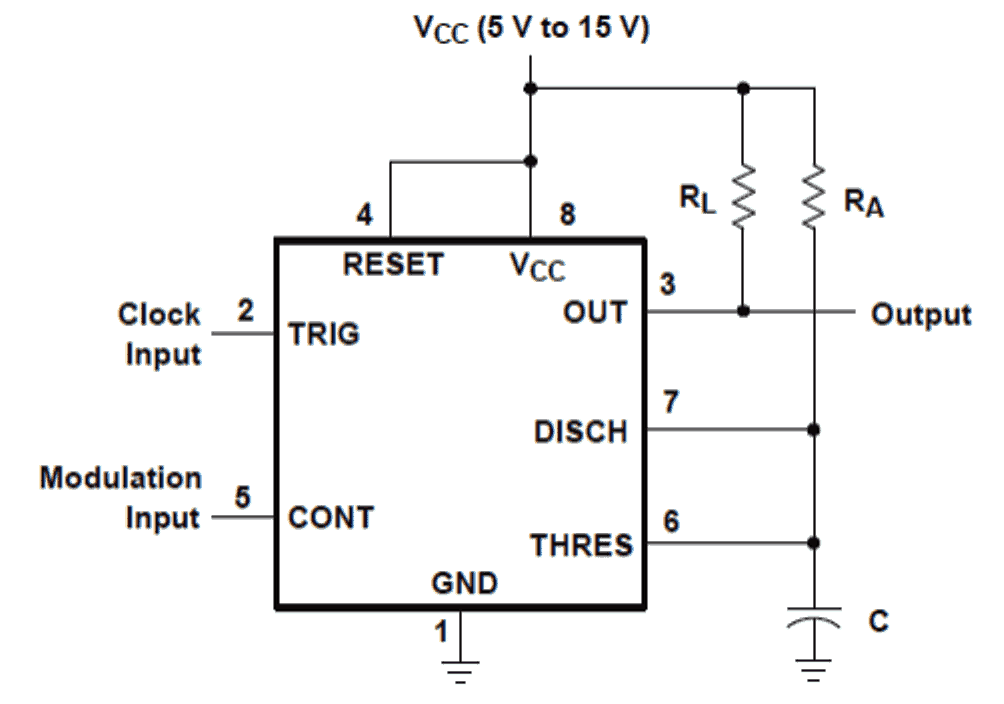
IC 555 Pinout
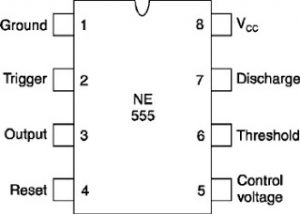
The diagram shows the IC 555 wired up in an easy monostable multivibrator mode. We know that in this mode the IC is able to generate a positive pulse at pin#3 in response to every single negative trigger at its pin#2.
The pulse at pin#3 sustains for some predetermined time period depending upon the values of Ra and C.We can also see the pin #2 and pin#5 assigned as clock and modulation inputs respectively.
The output is taken from the usual pin#3 of the chip.
In the above straightforward configuration the IC 555 is all set for generating the required PWM pulses, it just requires a square wave pulse or a clock input at its pin#2, which determines the output frequency, and a variable voltage input at pin#5 whose amplitude or the voltage level decides the pulse width dimensions at the output.
The pulses a pin#2 generates a correspondingly alternating triangle waves at pin#6/7 of the IC, whose width is determined by the RA and C timing components.
This triangle wave is compared with the instantaneous measure of voltage applied at pin#5 for dimensining the PWMs pulses at pin#3 output.
In simple words we just need to supply a train of pulses at pin #2 and a varying voltage at pin #5 for achieving the required PWM pulses at pin#3 of the IC.
The amplitude of the voltage at pin#5 will be directly responsible in making the output PWM pulses stronger or weaker, or simply thicker or thinner.
The modulation voltage can be a very low current signal, yet it would give the intended results.
For example suppose we apply a 50 Hz square wave at pin#2 and a constant 12V at pin#5, the result at the output will show PWMs with an RMS of 12V and frequency of 50Hz.
For reducing the RMS we just need to lower the voltage at pin#5. If we vary it the resultant will be a varying PWM with varying RMS values.
If this varying RMS is applied to a mosfet driver stage at the output, any load that is supported by the mosfet will also respond with correspondingly varying high and low results.
If a motor is connected to the mosfet, it will respond with varying speeds, a lamp with varying light intensities while an inverter with modified sine wave equivalents.
The Output Waveform
The above discussion can be witnessed and verified from the given waveform illustration below:
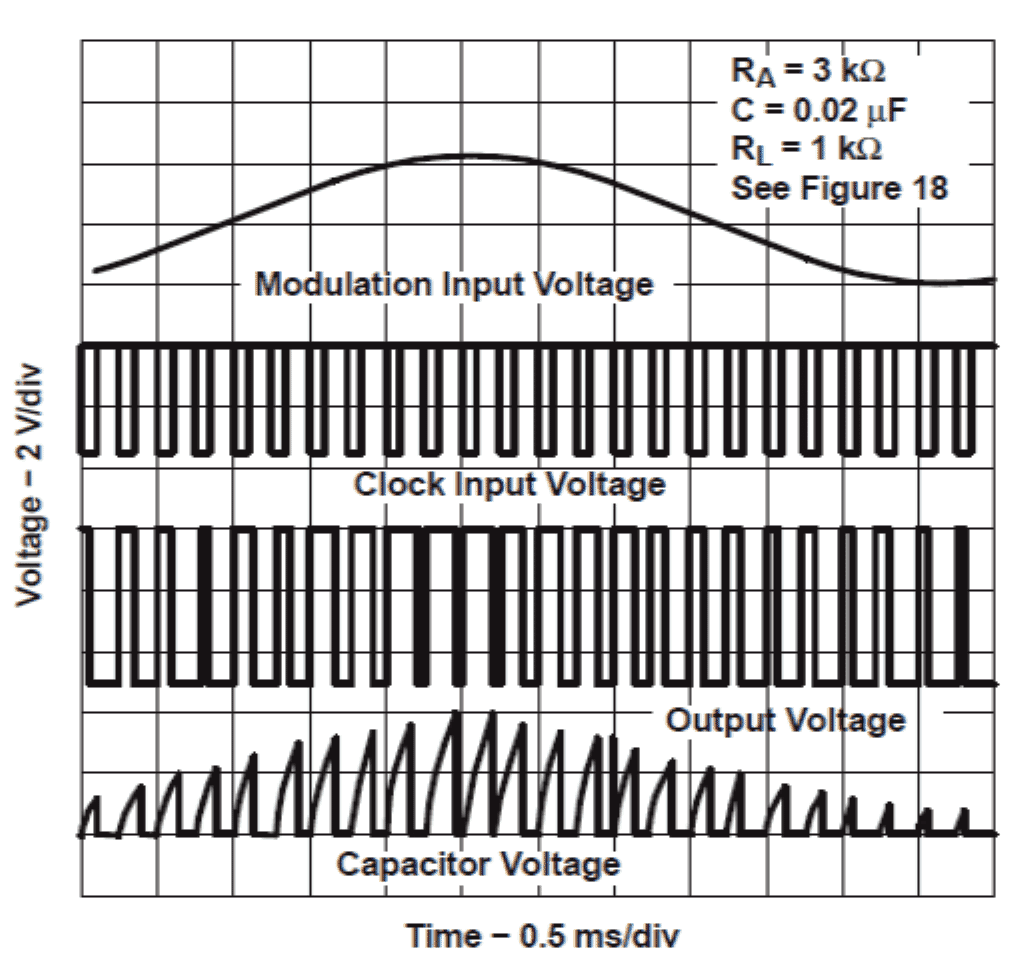
The topmost waveform represents the modulation voltage at pin#5, the bulge in the waveform represents the rising voltage and vice versa.
The second waveform represents the uniform clock pulse applied at pin#2. It's just for enabling the IC to switch at a certain frequency, without which the IC wouldn't be able to work as a PWM generator device.
The third waveform depicts the actual PWM generation at pin#3, we can see that the width of the pulses is directly proportional to the top modulation signal.
The pulse widths corresponding to the "bulge" can be seen as much wider and closely spaced which proportionately becomes thinner and sparse with the fall in the modulation voltage level.
The above concept can be very easily and effectively applied in power control applications as discussed earlier in the above article.
How to Generate a Fixed 50% Duty Cycle from a IC 555 Circuit
The following figure shows a simple configuration which will provide you with a fixed 50% duty cycle PWMs across its pin#3. The idea was presented in one of the IC 555 datasheets, and this design looks very interesting and useful for applications which need a simple and quick 50% fixed duty cycle generator stage.
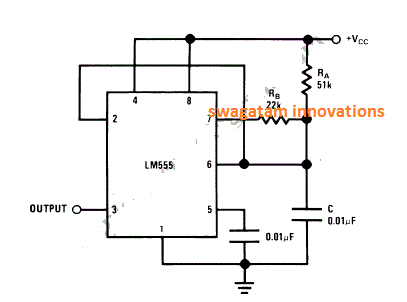
Swagatham, Would it be possible to use the 555 to control the voltage output of a 220vac transformer? I am a little familiar with the concept etc, in that I know I would need a zero crossing circuit to trigger the the 555 and then the output would have to trigger a solid state relay. So how can I vary the pulse width with a potentiometer that would stay in phase with AC? Any suggestions would be greatly appreciated.
Hi Phil, If you wish to have a 555 PWM control with an SSR, you can use the first concept from the above article.
However, I would rather suggest you to implement a triac based AC control as explained in the following article:
https://www.homemade-circuits.com/simple-ceiling-fan-regulator-circuit/
Thank you for your help. Your explanations of how the 555 works is great! I’m sure I am in over my head trying to fix this old welder. It has a 50A solid state relay mounted on a suitable heatsink. The SSR has an input trigger of 3 – 30 vdc. The primary (220vac) is already connected to the SSR. The control board that that controls the signal going to the welder is bad (in part.) Other functions of the board work, just the HEAT (or power output) does not turn on the SSR. I have tried replacing components on the PC Brd (and replaced the SSR) but still does not work. The welder already has a potentiometer for control. I think it is 5k but I could change this. So what I am trying to do is come up with a fix for my old reliable welder. I have repaired this in the past by replacing the PC Brd but they are obsolete now and 3rd party replacements are out of my budget. I think I already know how to make the zero crossing circuit and I assume I could apply that to the trigger of the 555 to turn it on in phase with the 60 Hz AC. What I don’t know how to do is to get the potentiometer to adjust the output pulse of the 555 so as to control the pulse width when triggered by the zero crossing circuit. There is also a 24 vac power going to the original board. I am familiar with voltage regulators and rectifiers etc I may need, but it is this darn pulse width I am struggling width. It is taxing my 77 year old brain!
Hi, Thanks very much! Glad you liked the explanation.
I think I already have a relevant circuit idea which closely matches your requirement.
Here’s a PWM zero crossing controlled 555 circuit which can be used with your SSR to control the load with PWM.
https://www.homemade-circuits.com/wp-content/uploads/2013/10/solidstatetransformerlesspowersupplycircuitsurgefree.png
The BC547 and the SCR section can be replaced with your SSR configuration.
If you need I can redraw the circuit with an appropriate SSR included in the design.
Thank you very much for your quick response! Your designs all look amazing! I just wish I could remember what I learned 55 years ago about passive and active networks. I turned into a digital only kind of guy and still retain much of that. As for the circuit you suggested, I was hoping there might be a way to use the 24 vac transformer instead of connecting 220vac to the circuit design. Or I see that you have a 12v zenor to power the the 555. I think I could rectify the 24 vac and use a LM7812 to supply the 12v. What do you think? I hate to impose on your time and good nature so if I am asking more than I should – please accept my apology.
No problem at all. Please feel free to ask as many questions as you want, which will help us to share and gain more knowledge.
Yes, a 24 v ac supply from a transformer could be used to power the circuit and that would make the circuit much safer to handle. However the base potential divider might need to be modified so that a 12v or higher can be achieved from it to power the 555 stage. A 7812 might not be necessary, since the 12v zener would work without any issues with the low current voltage from the potential divider. Let me know your thoughts on this.
I believe I know what you mean.You are referring to voltage at the junction of the 47k and 20k resistors not being high enough? If that is the case I do not know how to recalculate those values.
Yes that’s correct. I have redesigned the circuit, which I think should do the job for you. You can find it in the following link:
https://www.homemade-circuits.com/wp-content/uploads/2023/12/zero-crossing-controlled-555-pwm-circuit-with-ssr-for-welding-control.jpg
Wow! Thank you so much! I will give this a try and let you know how it turns out. It looks to be exactly what I need.Maybe now I can get my garden cart welded and working again.
I doubt I could ever give you any technical advice on anything, but below you will find a couple of links where I have posted some instructional projects of my own.
I am currently working on another project for my wife who does stained glass and glass fusing. I am constructing a kiln from scratch.
Thanks again. Rare to find someone so willing and happy to help others.
hackster.io/pitg2000
instructables.com/member/pitg2000/
No problem Phil, I am always glad to help and all the best to you. Hope you succeed with the project.
Let me know if you run into any problems.
Swagatam. So I tried the circuit design and I do have some problems, and maybe I am causing them myself. First off, I did not have any 10nf capacitors and I substituted 1nf instead. I also did not have a 20k resistor and substituted a 22k. That having been done I was seeing a 1ms trigger occurring every 8ms.The trigger pulse width was variable as expected. The trigger went from ground to 8vdc, but when I connected it to the SSR it dropped down to 2vdc. Not really knowing exactly how to get the signal strength up above 3vdc required for the SSR, I played around with the series resistor going to the SSR. I managed to get the signal up to 5v. At this point the SSR was turning on and staying on but the voltage output did not vary any when I adjust the phase control.
I am really confused with this problem I am having because the original control board in the welder is sending almost an identical signal (albeit it goes from ground to 15vdc.) That signal does not turn the SSR on at all! I have tried 2 new Crydom SSRs.
This leads me to ask – don’t the SSRs have a zero crossing already built into them? If that is the case, what happens when you are already sending in a signal that is starting at zero volts? In the case of the original welder control board, it almost looks like the SSR gets turned on and back off at the same time!!
I realize that this is the holiday season so I am not expecting any prompt response. I am retired so every day is Saturday!
Have a nice holiday!
Thank you Phil,
It seems the monostable operation of the 555 IC during the zero crossings is happening correctly.
In that case the SSR must also switch the output at an identical rate. But as you say that is not happening.
Is your SSR built using MOSFETs or triac?
If it is MOSFET based then it should respond to the 1ms ON 8ms OFF time generated by the 555 output. However a triac based SSR may not respond to any PWM generated between the zero crossings and the peak of the AC wave cycles, because the triac will get latched and switch OFF only at the zero crossings, so the 1ms turn OFF after the zero crossing will never turn off the triac.
Regarding the voltage drop, SSRs are supposed to have high input impedance, so the voltage at their input must not drop, that’s strange?
SSRs do have zero crossing, but that is only to safeguard the load from switch ON transients.
However using the 555 circuit, it does not matter whether the SSR has a zero crossing or not because the 555 output will always switch ON the SSR only at the zero crossings.
So, if possible could you buy a MOSFFET based SSR? MOSFETs will not get latched and will respond and instantly turn OFF whenever the input is turned OFF at any point of the AC mains waveform.
Swagatham, so sorry for the late response and a BIG thank you for your repeated help. It appears as though the email address I have been using is not forwarding my messages. I will have to deal with that, so I will give you another email address in this reply.
I think you may be on to the real problem! I have both a cheap SSR I bought on Amazon (uxcell $14.00) and also a more expensive one (CRYDOM D2450). I dismantled the cheap one and you are correct. It has a BTA24 triac. I just looked on the datasheet for the D2450 and it has a SCR with zero crossing.
I was so sure that the original SSR in the welder was a D2450 but now I’m thinking I could be mistaken.
I don’t have to put a SSR back in the welder. I could use something else. There is already a fan cooled heatsink I could mount it on. Seems like the low power MOSFETs are inexpensive. I am not sure on 200v or 400v ones if that is the case. Can they be used in parallel to increase the current?
Actually I see looking through your website that you have an lesson on SSRs and MOSFETS. I need to study this in more detail.
No problem Phil, thank you for your reply!
Yes if the SSRs are built using SCR or Triac then they won’t be applicable for PWM switching.
MOSFETs will respond to PWM correctly, however single MOSFFETs might not work with an AC load.
In that case you may need a bidirectional MOSFET based SSR.
Let me know what you think about it?
My gosh! I am digging a hole deeper and deeper into this problem welder of mine. First let me say that I use to be the authorized repair center for this welder and replaced this circuit board and SSR literally hundreds of times. In the parts description for the welder it is called a “triac relay” and the part number is a 216-062-666. A couple of reputable dealers for welder parts sell the relay. They want $300 for it! They both show a picture of the relay. In the picture of one of them I see that it is a CRYDOM A2450 and can clearly see printed on the relay that the control input is 90 to 280vac. This can’t be the correct relay they are showing cause the control board for that part number (216-062-666) is the very same one I have in my welder and there is no way that it has any control voltage over 15vdc! Also, according to the CRYDOM data sheet it is SCR and not triac.
I don’t know whether this makes a difference or not, but the control output of the welder pc board is what I would call “negative logic.” The SSR has +15vdc on the pos+ and the signal goes to the -neg. Obviously the A2450 will not work, but assuming they meant to show the picture of the D2450 (which has a 3 to 30vdc control) can you see any scenario where either one of these would work.
Thanks Phil,
These SSRs are great for normal ON/OFF switching.
However since an SCR or Triac is involved, standard PWM control might not work correctly. Because SCRs and Triacs will latch up after each zero crossings, and will remain latched until the next zero crossing..
There’s one possible way where a PWM switching can be implemented to these devices, it is through PWM time proportional concept.
https://www.homemade-circuits.com/triac-phase-control-using-pwm-time/
A practical example of this concept can be seen in the first schematic of this article:
https://www.homemade-circuits.com/3-phase-induction-motor-speed/
Another thing to consider is, why not eliminate the SSR entirely and instead apply a triac phase control using a standard light dimmer principle?
https://www.homemade-circuits.com/simple-ceiling-fan-regulator-circuit/
Hi Swagatham, I need your help with a pwm circuit for an HHO generator. Can you show me a diagram for a circuit that converts 110 volts AC to DC, and then, let’s the operator change the pulse width through a potentiometer.
If possible please provide a list of components needed for building the circuit, and a detailed diagram of the circuit layout.
Many thanks for your assistance.
Hi Gary,
You can try the following design:
https://www.homemade-circuits.com/wp-content/uploads/2023/09/HHO-gas-pwm-controller-circuit.jpg
Hi Swagatam,
I’ve found this nice circuit (method 2) here, which I have also designed a few years ago for the voltage to pwm converter for my class D amplifier. I have some remarks from my experiences.
RL is not required for the CMOS versions of the 555 timer.
You can use one RA / C combination for multiple pwm converters. I have used one for both stereo channels of my class D amplifier.
The clock generator can be build up very similar to the converter circuit. Only the trigger pin (pin#2) must be also connected to the midpoint of the RA / C combination. And you have to set a reference voltage for 100% duty cycle to the modulation pin (pin#5).
If your application depend on linearity (as in the case of class D amplifiers) you need to substitute RA by a constant current source. I have used a current regulating diode (Siliconix CD056 in my case) as constant current source. So I have used a single CRD / C combination for the clock generator and both pwm converter circuits.
Thank Gunter,
I greatly appreciate your valuable feedback and information. Hope the other readers will find it useful.
Sir, in the first diagram where resistors are shown in orange color, connections on pin 7 (if I am not wrong) are looks wrong as variable resistor is looks short circuited.
I think R1 should not be connected to pin7 directly.
Hello Mohsin,
I cannot see anything wrong in the first circuit. The circuit is a tested design, you can see it in the video.
Thank you sir, pls I do not mean connecting the output pin 3 of spmw ICs
above directlyy to sg 3525 in the inverter. I will follow your directive to connect the pin to mosfet gates with individual diodes. What I mean sir is, is it safe or will it work if I use the first method of generating spmw explained in the above article in an sg3525 inverter. That’s an inverter that has sg3525 as it’s main IC Thanks.
Michael, As already mentioned in my previous comment, the above circuits will not generate SPWM, they will only generate uniformly divided PWMs.
Please read the article carefully to understand its working.
You can use the second concept for generating SPWM by connecting pin#4 50 Hz output from SG3525 with pin#2 of the IC555, and then feeding pin#5 of the IC 555 with 300 Hz triangle waves, which can be obtained from another IC 555 astable circuit from right across its timing capacitor.
Hello sir, pls under this explanation you did, which said by ” connecting the output pin 3 of the IC…….. pls there are many circuits here, is it under the first method which has a 555 IC with a pin 3 output connected to a red arrow and yellow stripes, also still under that circuit of the first method, there are two wires out tagged “9v” and “0v”, pls where do these wires go. Lastly still under this first method’s circuit, I want to use it in an sg3525 inverter, should I go on thanks.
Hello Michael, all the diagrams above will generate a pwm controlled output at pin3 of the ICs, so you can use any one of them. Connecting to SG3525 will not help to get sine wave output because the above pwms are not SPWMs, they can be used only to control the RMS of the inverter output. The 0 and 9V can be connected to the battery of the inverter.
Thanks sir for your Swift response, pls I want to enquire, can I use the 12v d.c. from a normal or advanced car alternator rotating at it’s normal or highest possible rpm to power a 2k watt or at least a 1k watt Inverter. That is the inverter will only be powered by the current from the alternator in place of a battery. If it’s feasible, like how long can that arrangement last with little or no harm to the inverter or the alternator itself. If there are pros, pls let me know also through your reply. Thanks, will be waiting for your reply. Merry Christmas to you and your people ❤️
Michael, an inverter just needs a DC supply to convert the DC into mains AC, it doesn’t matter from where the DC is coming. If you can convert the alternator AC to Dc to feed the inverter then the inverter will do its job normally, as it would do with any battery. However to operate a 1000 watt load the alternator output power will need to be much above this value.
Pls sir under method one on how to create pmw circuits, can you apply it to all inverter circuits e.g inverter circuits with sg 3525, also sir pls still under that first method diagram what’s the output wires, also which place in my inverter will I connect the output wire to create the simulated sine wave. Then lastly sir still under that first diagram pls I don’t understand that yellow stripes connected with a red wire or outline to the third pin of the IC 555
Thanks for answering. God bless you.
Michael, you can use the second 2) explanation for inducing sine pwms into any inverter, by connecting the output pin3 of the IC to the gate of the MOSFET through two separate 1N4148 diodes. The cathodes of both the diodes will connect with the pin#3 of the IC, and the anodes will go to the respective gates of the MOSFETs.
The yellow lines are rectangular waveform as seen on an oscilloscope, please see the video to understand the waveforms.
You can read the following article for more info:
Sine wave PWM (SPWM) Circuit using Opamp
Great circuit!
Thanks!
Ken
Thank you, glad you liked it!
Swagatam,
I have used a crystal controlled oscillator and divided it down to give a very accurate 50Hz square wave which I have further cleaned up using Schmidt triggers. However, the duty cycle of the output pulses are too long causing the inverter I am using it with to draw too much current and produce too much voltage.
Would it be possible to use the square wave pulses to drive a PWM circuit and control the duty cycle using feedback from the output of the inverter?
I am assuming that opto-couplers could be used but given the high voltage on the secondary they would have to be carefully utilised.
If you have such a circuit available it would be much appreciated.
You can chop the MOSFET gate with feedback voltage as explained in the following article:
Automatic Inverter Output Voltage Correction Circuit
Swagatam,
Thank you for that; presumably I need two of these circuits to handle the anti-phase outputs of my oscillator circuit?
Sorry Paul, I cannot perfectly figure out the mentioned circuit.
At which point we have to connect led for blinkiy
Hi engineer Swagatam, I have completed the circuit (3kva inverter using IC SG3525) It works. Thank you very much. Now, sir, I want AUTOMATIC battery charger/changeover circuit, overload cut off, Battery full cut off, Battery low cut off. When the light from grid comes it will automatically change to changing and vise vasal, to elongate the life span of the battery used. I will be looking forward to your prompt reply. Once again, I am very grateful.
Thanks Yusuf, I am glad you could complete it successfully, you can try the second concept from this article to convert your design into an UPS
https://www.homemade-circuits.com/making-ups-tutorial/
hi good work sir
Hi Swagatam
My name is Ezekiel
I want you to show me a schematic diagram of a soft start AC motor pump using a monostable 555 timer to
have automatic control of start up AC motor pump
Dear Sir
Possible to explain to me how to use the 555 as a speed controller in PWM, to control a 48v DC fan draw 350mA.
Thank You
Dear Johan, you can try the following simple design for implementing your application
https://www.homemade-circuits.com/2012/05/make-this-pwm-based-dc-motor-speed.html
make sure to step down the 48V to 12V for the IC section.
Dear,
In the circuit diagram given by you, i see the 100K pot connected with the diodes.
Does this pot only change the duty cycle OR change both frequency and duty cycle?
Thanks
Hi Sherwin, Only duty cycle is changed, not frequency.
Then how pwm frequency can be calculated?.
Is the standard formula will be used or something difference
Dear Guru,
I have been through various circuits on the web regarding 50% duty cycle generator using IC555 timer where people have connected diodes in series with the timing components and proved to show that they are sucessful in doing so.
I have even searched the datasheet of the above timer regarding the duty cycle generation but in the features section it just says ADJUSTABLE DUTY CYCLE and it doesn't mention it like say 0-100% OR 50-100% or whatever.
Many other people have made the 555 oscillator and some say:
1. It is possible to trim down the duty cycle less than 50%.
2. It is not possible to bring the duty cycle less than 50%.
3. It is possible to generate 50% duty cycle.
All these people have shown diagrams and videos and proved the above.
There are questions from my side regarding the above:
A. Is it possible to generate a fixed 50% duty cycle at the output of 555 by connecting diodes?
B. Are we forcing a component to generate something more precise and accurate regarding to what it can in general output freely without stress.
The datasheet dosen't show any diodes connected in the 50% duty cycle schematic.
I need some clarification regarding this.
Thanks
Hi Sherwin, It is good to see that you have reposted your comment, please refer to my reply as given in the above comment.
the 555 duty cycle and frequency together depend on its R/C component values, so while creating the 50% duty cycle we are basically adjusting the R/C components precisely to set the duty cycle
you have removed the comment, that's not good…you must be patient getting the reply from me.
Hi Sherwin,
It is possible to adjust and vary the duty cycle of a 555 IC circuit from 1% to 99% by using diodes in conjunction with the pot of the circuit as shown below
https://3.bp.blogspot.com/-L9gXRB3GcDc/Vvek1mJUGOI/AAAAAAAANZE/ocPbYVXjnQMDKpxwDB0sd2fu5uqlJkutw/s1600/pwm%2Bcircuit.PNG
fixed 50% is also possible, you can find a simple design updated just now by me in the above article
sir i need help in spwm technique for inverter using arduino
bhavin, you can refer to the following article
https://www.homemade-circuits.com/2016/12/simple-arduino-sine-wave-inverter.html
Hello sir,
I have a few queries could you please clarify that,
Is this possible to control the load of 24v using PWM if possible can you please send the circuit diagram.
my requirement is "on" and "off" the load depends on the time period like 2 minutes "on" and 1 minutes "off", and 3 minutes "on" and 1 minutes "off", the time duration for "on" and "off" is should variable.
Thanks in advance.
Hello kumar, the above explained concept cannot be used for your application….a programmable timer referred below will be much suitable instead:
https://www.homemade-circuits.com/2012/04/how-to-make-simple-programmable-timer.html
Dear Swagatam Sir,
Is the circuit given alone capable of producing PWM signals?or should we take the output from pin 6(triangle wave) and compare it with the input signal using 741/311?
Dear Faris, Pin#2 needs to be fed with a square wave pulse and pin5 with some constant DC voltage, that's all….the resultant will be a dimensioned constant PWM equivalent in RMS value to the DC input at pin#5…the PWM will vary as the pin#5 DC is varied, if it's in the form of a sinewave then the PWM will follow this and produce a equivalently varying PWM train at pin#3
hello
swagatam i need a help from u pls
i want pwm ciruit diagram with specificitions 0-24v dc using 555ic and mosfet output upto 30amps using controling preset r variable can u help me pleace
hello suman, you can try the following simple design:
https://www.homemade-circuits.com/2012/05/make-this-pwm-based-dc-motor-speed.html
Hello,
Many thanks again.
Please do accept my apologies but electronics is not really my strength point and I struggle with some concepts.
I understood what you said with creating the PWM, however I don't see where can I input my own varying signal onto the IC-555? In addition, the second link gave me the page of a Tachometer, I didn't manage my way through to be honest 🙁
It's just an idea that I have suggested, I am myself not sure if the idea would work.
The input will need to be applied at pin5 of IC2 in the referred first diagram.
In the tachometer, see only upto the transistor base, ignore the left side ignition system.
The PWMs from the first diagram could be applied to the base of this transistor for getting an equivalent sine wave across C8
Hello Sir ,
is this variable duty circle pwm train only enough to couple to mosfets for for high power inverter?
Hello Patrick, it can be applied alternately. When one set of SPWM is applied on one MOSFET gate, it should switch OFF and move to the next MOSFET and repeat the set. This must go on alternately across the two MOSET gates.
Hello Mr Swagatam,
Many thanks for your prompt reply.
I didn't quite understand what you meant by connecting pin-2 to a square wave source, is it the feedback connected back from pin-3 through a resistor? This is how I have designed my circuit:
Pins 2 and 6 are connected together and joining a capacitor to the ground, pin-2 is connected through a resistor to pin-3 to have the same charge and discharge path through same resistor and by this way I can obtain 50% duty cycle.
My input to pin-5 is actually an analog signal with a voltage range that I choose (between 2 –> 8 Volts), if I do understand correctly then the lower the control voltage on pin-5 the higher the output frequency and vice versa, true?
In addition, some experimental studies referred to the usage of electrolytic capacitors on pin-3 to generate an average sine wave, what do you think?
Hello Ahmed,
My idea is to convert the input varying signal into varying PWMs and then convert these PWMs into a proportionately varying sinewave
referring to the diagram as given below, see only the IC1/IC2 stages, ignore the BC547 section, here if a varying voltage (from 0 to supply level) is fed will generate a correspondingly varying PWM on pin3 of IC2:
2.bp.blogspot.com/-9KJbHVJRM50/VEi8zi9XYFI/AAAAAAAAIfM/NVyjPFtj7ho/s1600/treadmill%2Bcontroler%2Bcircuit.png
Next these PWM can be fed to the base of the transistor T2 of an integrator as shown below, and the waveform can be analyzed across C8
easy-electronic-circuits.blogspot.in/2014/02/simple-tachometer-circuit-or-revolution.html
Hello Mr Swagatam,
Many thanks for your article which I came across because I am looking to construct a very basic VCO which has an analog input variable voltage that should be converted to an alternating sine wave corresponding to the input voltage.
I was thinking of using the 555 to generate a square wave corresponding to my varing voltage and convert it to a sine wave, what do you think?
Many thanks in advance.
Hello Ahmad,
Yes it's possible, first the varying may be applied at pin5 of the IC 555 (pin2 connected with a square wave source) for generating a correspondingly varying PWMs, and then these PWMs may be fed to another 555 IC integrator circuit for converting them into correspondingly varying sine pulses…..wider the PWMs higher the amplitude of the sinewaves and vice vera.
Hi Swagatam,
This is a great post, with some inspiring information. I have a question if I may. I have a SMPS converting 230vAC down to 24vDC @ 40A. I need to control the output voltage from 0-24v. I'm looking into using PWM and so would the 555 be the right solution? i'm not an electrical engineer but I need to have a clue about whats possible before I try and commission the product.
Many thanks.
David
Hi David,
Yes it can be done. Pease reer to the following diagram. The upper section is what you need to make, ignore the lower IC/mosfet section its not required. Pin3 of IC2 555 will produce the required PWMs
The above output can be configured to a mosfet stage for controlling the load, the PWMs then may be adjusted by varying the 10k RMS pot or preset.
…sorry here's the link:
1.bp.blogspot.com/-M-7Ep_6ceTg/UeOHwdVvZeI/AAAAAAAAE1A/OKN0F_jVmkw/s1600/pure%20sine%20wave%20inverter%20circuit.png
Hi Swagatam,
I was wondering if you could help me with my project. I need a pwm motor speed controller for my 12V, 3A motor and I want to run it 1 minute ON and ~5 minutes off to save battery power. I have a 4060 ic that can be used on the timer part but not sure if you can use it for PWM?? Thanks in advance.
Hi Charlie,
For PWM control you can try the last circuit shown in this article:
https://www.homemade-circuits.com/2013/02/how-to-make-simple-220v-transformerless.html
ignore the 4 diode bridge circuit, simply connect your motor across the positive and the mosfet drain.
The 10k preset can be used for controlling the motor speed.
correction: the above link is not the correct one, please refer to this link:
https://www.homemade-circuits.com/2013/09/simple-electronic-load-controller-elc.html