The common problem with many low cost inverters is their incapability of adjusting the output voltage with respect to the load conditions. With such inverters the output voltage tends to increase with lower loads and falls with increasing loads.
The circuit ideas explained here can be added to any ordinary inverter for compensating and regulating their varying output voltage conditions in response to varying loads.
Design#1: Automatic RMS Correction using PWM
The first circuit below can be considered perhaps an ideal approach of implementing a load independent auto output correction using PWM from a IC 555.
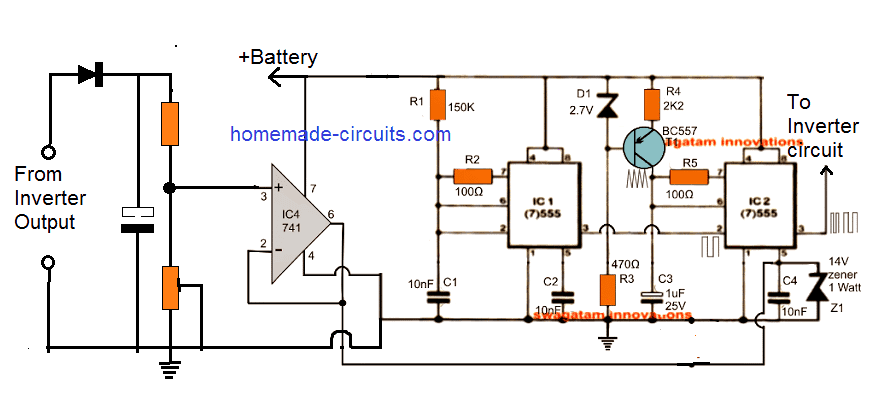
The circuit shown above can be effectively used as an automatic load triggered RMS converter and could be applied in any ordinary inverter for the intended purpose.
The IC 741 works like a voltage follower and acts like a buffer between the inverter output feedback voltage and the PWM controller circuit.
The resistors connected with pin#3of the IC 741 is configured like a voltage divider, which appropriately scales down the high AC output from the mains into a proportionately lower potential varying between 6 and 12V depending upon the output status of the inverter.
The two IC 555 circuit are configured to work like modulated PWM controller. The modulated input is applied at pin#5 of the IC2, which compares the signal with the triangle waves at its pin#6.
This results in the generation of the PWM output at its pin#3 which varies its duty cycle in response to the modulating signal at the pin#5 of the IC.
A rising potential at this pin#5 results in the generation wide PWMs or PWMs with higher duty cycles, and vice versa.
This implies that when the opamp 741 responds with a rising potential due to a rising output from the inverter causes the output of IC2 555 to widen its PWM pulses, while when the inverter output drops, the PWM proportionately narrows at pin#3 of IC2.
Configuring the PWM with Mosfets.
When the above auto correcting PWMs is integrated with the mosfet gates of any inverter will enable the inverter to control its RMS value automatically in response to the load conditions.
If the load exceeds the PWM the inverter output will tend to go low, causing the PWMs to widen which will in turn cause the mosfet to turn ON harder and drive the transformer with more current, thereby compensating the excess current draw from the load
Design#2: Using opamp and Transistor
The next idea discusses an op-amp version which can added with ordinary inverters for achieving an automatic output voltage regulation in response to varying loads or battery voltage.
If you don't want to read the following description, you can watch this video instead:
The idea is simple, as soon as the output voltage crosses a predetermined danger threshold, a corresponding circuit is triggered which in turn switches OFF the inverter power devices in a consistent manner thereby resulting a controlled output voltage within that particular threshold.
The drawback behind using a transistor could be the involved hysteresis issue which could make the switching fairly over a wider cross section resulting in a not so accurate voltage regulation.
Opamps on the other hand can be immensely accurate as these would switch the output regulation within a very narrow margin keeping the correction level tight and accurate.
The simple inverter automatic load voltage correction circuit presented below could be effectively used for the proposed application and for regulating the output of an inverter within any desired limit.
The proposed inverter voltage correction circuit can be understood with the help of the following points:
A single opamp performs the function of a comparator and a voltage level detector.

Circuit Operation
The high voltage AC from the transformer output is stepped down using a potential divider network to about 14V.
This voltage becomes the operating voltage as well as the sensing voltage for the circuit.
The stepped down voltage using a potential divider corresponds proportionately in response to the varying voltage at the output.
Pin3 of the opamp is set to an equivalent DC voltage corresponding to the limit which needs to be controlled.
This is done by feeding the desired maximum limit voltage to the circuit and then adjusting 10k preset until the output just goes high and triggers the NPN transistor.
Once the above setting is done the circuit becomes ready to be integrated with the inverter for the intended corrections.
As can be see the collector of the NPN needs to be connected with the gates of the mosfets of the inverter which are responsible for powering the inverter transformer.
This integration ensures that whenever the output voltage tends to cross the set limit, the NPN triggers grounding the gates of the mosfets and thereby restricting any further rise in the voltage, the ON/OFF triggering continues infinitely as long as the output voltage hovers around the danger zone.
It must be noted that the NPN integration would be compatible only with N-channel mosfets, if the inverter carries P-channel mosfets, the circuit configuration would need a complete reversal of the transistor and the input pinouts of the opamp.
Also the circuit ground should be made common with the battery negative of the inverter.
Design#3: Introduction
This circuit was requested to me by one of my friends Mr.Sam, whose constant reminders prompted me to design this very useful concept for inverter applications.
The load independent/output corrected or output compensated inverter circuit explained here is quite on a concept level only and has not been practically tested by me, however the idea looks feasible because of its simple design.
Circuit Operation
If we look at the figure we see that the entire design is basically a simple PWM generator circuit built around the IC 555.
We know that in this standard 555 PWM design, the PWM pulses can be optimized by changing the ratio of R1/R2.
This fact has been appropriately exploited here for the load voltage correction application of an inverter.
An opto-coupler made by sealing an LED/LDR arrangement has been used, where the LDR of the opto- becomes one of the resistors in the PWM "arm" of the circuit.
The LED of the opto coupler is illuminated through the voltage from the inverter output or the load connections.
The mains voltage is suitably dropped using C3 and the associated components for feeding the opto LED.
After integrating the circuit to an inverter, when the system is powered (with suitable load connected), the RMS value may be measured at the output and the preset P1 may be adjusted to make the output voltage just suitable enough for the load.
How to Set Up
This setting is probably all that would be needed.
Now suppose if the load is increased, the voltage will tend to fall at the output which in turn will make the opto LED intensity decrease.
The decrease in the intensity of the LED will prompt the IC to optimize its PWM pulses such that the RMS of the output voltage rises, making the voltage level also rise up to the required mark, this initiation will also affect the intensity of the LED which will now go bright and thus finally reach an automatically optimized level which will correctly balance the system load voltage conditions at the output.
Here the mark ratio is primarily intended for controlling the required parameter, therefore the opto should be placed appropriately either to the left or the right arm of the shown PWM control section of the IC.
The circuit can be tried with the inverter design shown in this 500 watt inverter circuit
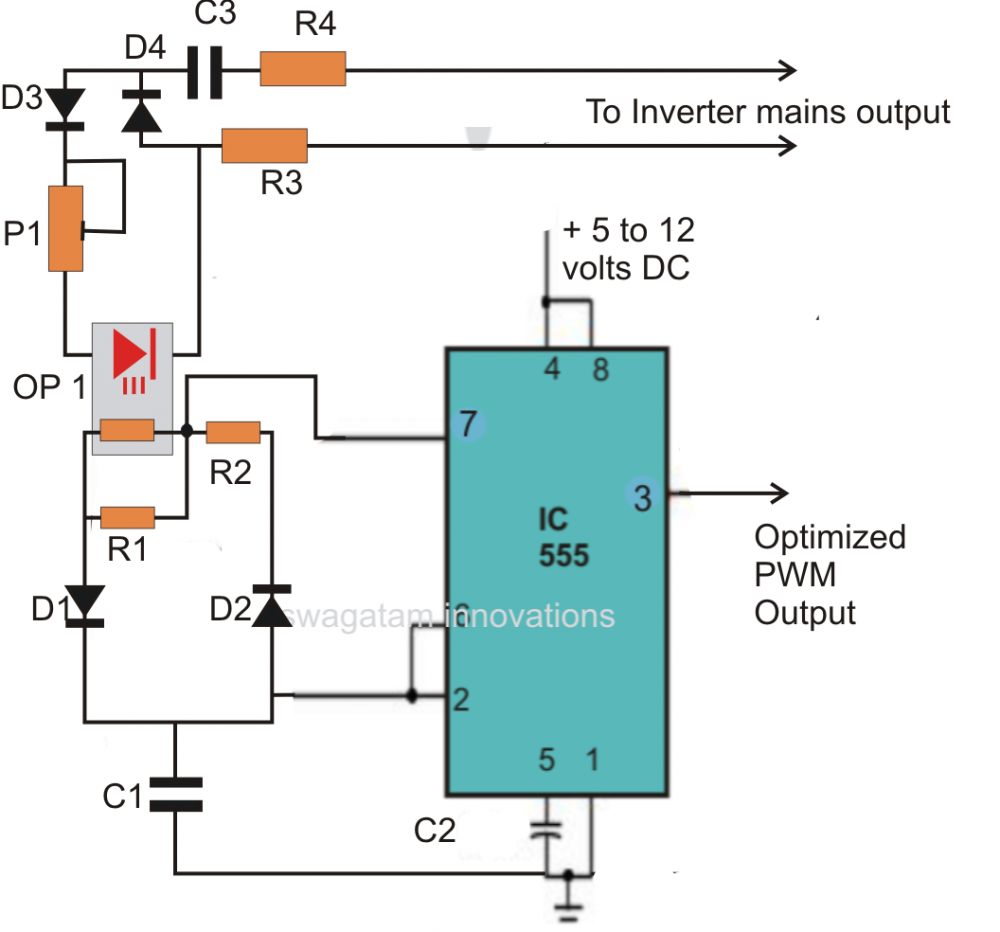
Parts List
- R1 = 330K
- R2 = 100K
- R3, R4 = 100 Ohms
- D1, D2 = 1N4148,
- D3, D4 = 1N4007,
- P1 = 22K
- C1, C2 = 0.01uF
- C3 = 0.33uF/400V
- OptoCoupler = Homemade, by sealing an LED/LDR face to face inside a light proof container.
CAUTION: THE PROPOSED DESIGN IS NOT ISOLATED FROM INVERTER MAINS VOLTAGE, EXERCISE EXTREME CAUTION DURING THE TESTING AND SETTING UP PROCEDURES.
Dear swagatam,
Trust you good?.
My problem is still about the feedback control circuit. Please I need your help. Now, I have designed the arduino sine wave in your description and it is working perfectly. For the last time please where should I connect the output from the feedback control? Thanks in advance for your help.
Thank you Jonathan, glad you could build the inverter circuit.
The connection details of the feedback control circuit with the Arduino inverter is provided under the same Arduino inverter article. Please check it again, and let me know if you have any difficulty understanding it.
https://www.homemade-circuits.com/arduino-pure-sine-wave-inverter-circuit/
Thanks for getting back to me. I will design it soon and when I’m done I will send you a full working picture and a video.
Sure, no problem, all the best to you!
One more question. Please I have 5 mosfets at the low driver side. And if I’m to connect the cathode of the diode directly to the 5 mosfet gates, should I also connect the 50ohms to each of the gates or only one 50ohms to all the gates? Thank you
An H-bridge low side is supposed to have 2 mosfets only, why have you used 5 mosfets, and how are they configured? please let me know…
Swagatam please I said I did full bridge not half bridge. Thank you
H-bridge refers to full bridge….how can you have 5 low side MOSFETs in an h-bridge or a full bridge topology?
Dear swagatam. Please I have made full bridge inverter with egs002 module and I need to control the voltage. Could you please show me which of the circuit to use and where to connect the circuit output to the inverter?. Waiting for your response sir.
Hi Jonathan I would recommend the second schematic using 741 ic and bc547 transistor. You can attach the diodes cathode with the gates of the low side mosfets….make sure that the mosfets have around 50 ohm gate resistors connected with the EGS002 board.
Though it is working but the gates of the mosfets are connected with 4.7ohm so I connected 100ohms from the cathode of the diode to the 4.7ohms of the low side of the inverter. Could this cause a problem?. Thank you for your time
Sorry, that will not work, because 100 ohm is too large compared to the 4.7 ohm resistor therefore the grounding will not happen when the BC547 conducts.
You must replace the 4.7 ohm with 50 ohm, and remove the 100 ohm resistors entirely.
Thank you for your time. It stopped working. Please what about the high mosfet gates too, should I replace the 4.7ohms with 50ohms?. And also I connected 10kohm to the gates and the source of the mosfets should I remove that one too?. Thank you
Only the low side MOSFET gate resistor needs to be replaced with a 50 ohm resistor, the high side resistor can be also changed to 50 ohms but it is not necessary. The 10k across gate and source is recommended, however if you don’t want them you can remove them, it is not crucial.
Much love swagatam. ❤ thank you
You are welcome Jonathan!
Last question. Please where exactly so I connect the cathode of the diode to the gates? Should it be connected after the 50ohms resistor to the gate or before the 50ohms resistor to the gate? Thank you
The 50 ohms are connected between the low side IC outputs and the low side MOSFET gates. The automatic correction circuit diode cathodes must be connected directly to the gates of the MOSFET.
The setup of the second circuit you recommended to me. How is the setup done? And does it need a variable power supply before connecting to the transformer output of inverter? Thanks.
You will have to arrange a 230V or 240V AC source which can be fed to the 220K end of the circuit after which the preset will need to be adjusted until the BC547 just conducts. You can replace the 3 V zener with an LED for the switch ON indication. The 230V or 240V is the desired cut off range at which the circuit should activate and begin deactivating the mosfets for the automatic cut off.
Yes sir I was asking if the setup needs a variable power supply before connecting to the transformer output of an inverter. Or how is the the setup done. Thanks
Preferably you will need a variac for this, or if you have any other method of producing the high level voltage of 230V or 240V or whatever cut off level you require.
So I first apply the 220v or 240v ac to the circuit then slowly trim the preset until the red light illuminates and glue it at that point. That means the setup is complete and ready to feed to the inverter output?
Thanks
Yes, you are absolutely correct.
hello sir, it seems there is a problem in your website because am not getting your latest responses. I was asking after i have paralleled all gate resistors with in4148, i do connect again a common in4148 each side to the bc transistor in the second diagram you had referred to me?
Hello Morris, the 1n4148 you connected parallel to the gate resistors are for protecting the MOSFET from voltage spikes, it has nothing to do with the second circuit explained in the above article.
Yes, you will have to connect the 1N4148 diodes with the BC547 transistor as shown in the second diagram above.
The anodes of these diodes will connect with the LOW side MOSFET gates.
Make sure your MOSFET gate resistors are at least 100 ohms.
Thank you very much sir
You are welcome Morris…
Hello Morris, would love to connect with you if you don’t mind ..
Hae Nik what’s up✋
Hello Swagatam, I first applied 220ac main to the second design before loading it to inverter. I then slowly tweaked the preset but the led I used instead of 3v zena diode was not illuminating. Secondly. I applied again 220ac whn the circuit is connected to a12v batteries and tweaked the preset. The led is still not illuminating. What should be done sir being this circuit is very simple and I wonder why it’s not working.
Hello Morris,
The LED polarity will be opposite to that of the zener, meaning if you use an LED in place of the zener diode, then the cathode must be towards the base and anode towards the the 10k resistor.
If still it does not illuminate please check the voltage across the 10uF capacitor, across pin#3 and ground, pin#2 and ground.
The LED will illuminate only when the pin#3 voltage exceeds pin#2 voltage.
Do I feed only 220 ac or 12v must also be fed to the circuit?
Thanks.
It should be exactly as shown in the diagram, the IC 741 Vcc pin will require a separate +12V DC.
This is good job sir . However concerning the designs especially the first design, are they compatible with Pure sine wave inverters or only for square wave / modified ?
Because was wondering if there PMW of the timer ic won’t affect the output waveform
Thank you Joseph,
Yes the first design can affect a pwm based sine wave inverter
I personally prefer the second design which is easy to build and implement, and can e used in all types of inverters.
I would like to ask for a pure sine wave inverter circuit using SG3525 and two IR2110 i have been trying and always fail all the time please help me
You will succeed only if you build the circuit with proper understanding and with proper measuring equipment, and in a step-wise manner. You can refer to the following circuit:
https://www.homemade-circuits.com/sg3525-pure-sinewave-inverter-circuit/
Thank you for your effort so far, I will give you feed back if l’m done.
No Problem!
Sir, thank you for your respond so far.but another thing, can I use one big transformer for the setting since I can’t get hold of two small transformer.
Yes you can use any transformer rated at 220V primary. However a bigger transformer would mean bigger current, so be careful not to touch any part of the circuit to avoid an electric shock….trim the preset with an insulated screwdriver.
Hello sir, is this what you mean concerning the transformer, (1)-two 12v/220v transformer in use by connecting the two secondary to each other which is the output. (2)-then one primary will go to ac main and the other primary will go to the circuit for the setting.(3)- like you mentioned replacing the transistor base zener diode with LED, meaning once the opamp activate the LED will light up. Please me more on this question.
That’s perfectly correct youngking!
After supplying the 220V, you will have to adjust the preset to a point where the LED just illuminates. This will indicate that the op amp is set correctly to control the AC at the specified level which is supplied from the transformer.
Remember the circuit is not isolated from AC mains, so do not touch anything while the 220V is connected.
Good morning sir, pls explain more how to set the No #2 design that uses opamp and transistor. Or will it require variable power supply for the setting although I have through the comment but it not yet clear.
Hello Youngking, the easiest way is to feed a 220V, or 240V whatever maximum limit is required to the 220k resistor network, and then slowly adjust the preset until the op amp output just activates the transistor. You can replace the transistor base zener diode with an LED for an indication to show when the op amp output changes state.
You can use two small 12V/220V transformers, connect the 12V secondaries with each other, feed 220V AC from mains to one of the transformer primary, and then use the low current 220V from the other transformer to feed the op amp circuit.
Thank you Carlos, I can understand your problem, but you have posted your question under the wrong article. Please post it under the following post, I will try to help:
https://www.homemade-circuits.com/how-to-design-a-stabilized-bench-power-supply-circuit/
Hello sir,my inverter is modified sine wave and I want it to have spwm at the output of transformer and also at the same point controlling output voltage,will the design above with an opto work perfectly?
Hello Herbert, the above circuit can be used for stabilizing the output but it cannot be used to convert the output to SPWM
thank you sir
i mean for dropping 7v to the 741 ic from the220v ac main [pin 3 of the ic]
use 220K resistor on the upper side, and a 22k preset on the lower side
sir,my inverter output is 220v ac and which resistors will be appropate for dropping 7v for the first circuit ?
Hello sir please thank you for responded me but please my inverter in sine wave and it has 4 spwm going to the gate other the full bridge most fest how can I connect this or it should be connect with the low side of the most fest because we have high side and low side?
Hello Daniel, yes you can configure the second circuit with the low side mosfet gates of your circuit. Make sure to use at least 100 ohms for the MOSFET gate resistors
Swagatam,
Thank you for your prompt and excellent response to my query as usual!
It’s my pleasure, Paul!
Swagatam,
I already have a crystal controlled oscillator which provides 50Hz anti-phase outputs to drive the output MOSFET’s but with this arrangement I only get 185volts AC across the output transformer which also drops as more load is applied. I would add that this is a 15-0-15v primary transformer.
I obviously need to adjust the duty cycle of the input waveform to obtain the 230V I need across the secondary. Could this circuit be adapted to control the output but using the crystal controlled oscillator input?
Paul, the above circuits are designed to reduce a high margin voltage output to the desired normal level….these circuits cannot be used for doing the opposite.
Your problem could be the transformer primary rating. You must use a transformer with 70% primary voltage of the battery voltage. So if your battery is 12V, then the transformer primary must have a voltage rating 8.4V or 9 V to get a compensated margin of 30 to 40 V, that is 240V to 260 V.
Once you have this output, then you can apply one of the above circuits to bring down this high margin voltage to a 220V constant level.
Hi Mr swag I need help can any of the above design regulate an inverter output of about 300-400V I to220v will look forward to your quick reply thanks
Hi Ifeanyichukwu, yes they can adjusted to any value, as per any desired specifications
I tried the circuit out and it worked out fine thanks a lot .
But , I also want to a flyback diode accross a 1000w inverter mosfet which diode would be best recommended
You are welcome! the diode can be rated in accordance with the maximum load current the MOSFeT is supposed to handle.
Sorry for asking many questions the first design with a 555 timer how should the optimised pwms be connected to the gates of the mosfets and for the flyback diode I need a 40A type can you recommend one for me thanks I would be looking forward to your quick reply
connect the anode side of a 1N4148 diode with each MOSFET gate, and join the cathodes to connect with the PWM out from the IC2 555
Hello can i send you a schematic by mail?
thank you
OK!
Hi Swag does the pwm rms design2 plugged on center tap of the transformer change the frequency of the inverter?
frequency pwm (44H)
frequency inverter (50hz)
thank you!
Hi Mathieu, how do you plug the PWM to center tap? Please clarify?
Hi Mathieu, I saw the diagram but I don’t think it will work since you have used all N channel mosfet without bootstrapping. The center tap mosfet should be p channel.
Hi Swag what is the voltage margin from 220VAC to 250vac on Design#2 with the 741? (the circuit has a variation from 1v to 11V50!) how can i convert the high voltage 230VAC with the 12v input?
thank you
Hi Mathieu, It can solved by cross multiplication. 220/250 = x / y
where x corresponds to the PWM which produces 230V, and y corresponds to the PWM which will produce 250v
ok thank you
best regards
Hello Swag ive just tested with the scope and i have a 100% dutycyle! the only problem is that i have the frequency who vary and the pwm shouldnt vary in frequency! do you have an idea? maybe changing the values of the capacitors on IC1?
thanks
Hello Mathieu, 100% duty cycle means a straight DC equal to the Vcc level. In the second design frequency will not change the PWM, it is the voltage level at pin5 that changes the PWM. Frequency should never vary because it is fixed by R1, C1 which are constant.
Hi Swag on Design#2 is it normal to have a frequency who varies from 60hz to 860hz? i mean for duty cycle does it works correctly for the pwm on pin 10 of the ic sg3525?
thank you!
Hi Mathieu, frequency is determined by R1/C1 which are fixed, therefore the frequency must be also constant, only PWM value must change if the pin5 voltage changes.
The width of the PWM on pin10 decides for how long the output remain shut off, so it works for controlling the output proportionately. You can try the same on pin9.
Hi Swag on your (Design#2: Automatic RMS Correction using PWM) i have 60HZ to 860hz duty cycle! youve told me for the sg3525 pwm pin :(Hi Mathieu, connect it with pin10 of the IC)
i have connected it but the frequency is unstable! 125 to 320 hz! can you give me an idea? thank you!
have a nice day
Hi Mathieu, duty cycle is measured in %. Do you mean frequency of minimum/maximum pWms, anyway the frequency on meter will show unstable due varying pwm frequency.
please check using an oscilloscope across the output of the transformer, you will find a stable 50 Hz frequency…please don’t check with a meter.
Thanks Swagatham, for popularizing the Power Electronics through off the shelf components accessible at retail ele’ shops and simple enough for do-able by a hobbyist.
When enthusiasts construct circuits interfacing to transformer, it is necessary that the lowest frequency generated is matching the min. frequency for transformer. Else transformer can fail. The timer IC 555 has tendency for such frequency drift. Hence always better to use present resistance to tune the frequency.
Secondly, when connecting the grid tied inverter to mains, synchronizing is important. Also, conducted and radiated noise are to be below regulatory limits.
Thank you AK!
Hi Swag i have put a varistor on pin 5 of ic2 to obtaine 0v on that pin and it varies from 2,3hz and abrubtly monted to 860hz! who is the frequency of ic1(860hz)!if i apply a voltage from the follower there is no change on the frequency!
i dont understand, why apply a voltage from the 741 (1,2V to 11,60V) on pin 5who has a Vcc voltage? how can that works?
thank you!
Hi Matheiu, I am not sure why a varistor may be required at pin5, it is not required. You can put a 1K resistor instead. Varying voltage at pin5 will create proportionately varying pwm at pin3, which in turn will control the inverter output…..I have explained the rest in the article itself.
Hi Swag on pin 5 of IC2 i have +5Vcc! it cause a problem with the voltage follower! can you explaine me the default
thanks!
Hi Mathieu, it should be at 1/3rd of the supply level. However, adding a 1K across pin5 and ground will cause the output pwm to attain minimum width by default, which can be proportionately increased by applying a proportionately rising DC at pin5.
Hi Swag i have problems with the monostable configuration! i have send the schematic on your mail! ive tried differents resistors and caps! i have the signal from ic1 astable but ic2 there is nothing! the 555 is functional!
Hi Mathieu, the circuit using IC1, IC2 in the above article is a tetsed design. When pin5 is modulated with a varying DC the output from IC2 creates proportionate amount of PWM. Remember the monostable output will respond when pin2 is pulsed with a GROUND signal….you can test that manually
Hi Swag i have another question! if the frequency on design2 with a frequency meter is ok (7hz 105hz) but on the scope the result of the pwm is blur! where can be the breakdown from?
thanks
Hi Mathieu, scope blurred output can be due to 3 reasons 1) Your scope is defective, 2) you have not set it correctly, 3) the frequency is beyond the range of the scope. There cannot be any other reason for a blurred output in a scope other than these.
A frequency meter can be wrong but a scope can never be wrong.
Please use a digital oscilloscope, no matter how cheap or small it may be, it will show you the correct results.
Hi Swag, ive tested design2 with frequency meter results: 7hz to 105hz,the following is ok! but with the scope it is a disaster! the pwm is barely viewable!
thank you helping me!
No Problem Mathieu, wish you all the best!
Hello Swag i have finished the two 555 pwm ive tried one in astable with a 741 voltage follower result: 1KHZ to 500hz, with the scope i have 50 to 100 duty cycle!
with the second pwm i have the astable and monostable but the frequency works from 887hz to 450HZ! why does the frequency changes roughly from 887HZ TO 450HZ?
does the circuit is linear from 0hz to 1khz? (1% to 98% duty cylce)?
thank you!
Mathieu, the frequency is fixed by the IC1 astable circuit, so the frequency should not change. The astable decides the number of blocks on the PWM cycles, while the monostable decides the width of the blocks….please use an oscilloscope to confirm that the number of blocks are always constant regardless of the PWM adjustments.
Hello sir swagatam, between the two of the auto voltage corrector circuits,which one is best? I understand u have provided us with two one using opamp741and ne555 and opamp 741 and transistor.
The last one is the easiest and the recommended one!
Thank you sir,I have now understood. But one issue for me, when adjusting the 10k preset until the npn transistor triggers,does it mean for instance if I I connect max voltage limit of 220v and start to adjust,will the output rise above this? Coz u say we should adjust till voltage goes high and npn triggers.
The output will be equal to the pin7 voltage of the IC, which is 12V.
Got it sir swagatam.
Hi Swag, can i send you by email my schematic?
yes you can send it!
Hi. I have a signal been generated out of Arduino pwm pins. It works well as an oscillator for an inverter. But I don’t know how to apply feedback to it. My output keep decreasing when been loaded. How can I implement feedback to the programme? Thanks.
That will require a different program code for the Arduino, which may not e possible for me to create. Alternatively you can add a external control circuit as explained in the last concept above.
HI Swag is it possible to replace on design 1 the optocoupler by a lm741?
if i can post you the schematic, are you ok for check on it?
thank you for your patience!
Hi Mathieu, yes it may be possible by feeding the inverter voltage sample to diode network and pin7 of the IC from IC 741 voltage follower circuit
Hi Swag IC2 on pin 5 is a capacitor for parasite used in astable mode why have you put the voltage fallower (741) to pin 5 of ic2? and a zener cut off on it? pin 5 is normally connected to ground, everything is ok while the irregular frequency when connected to IC2! (IC1 OK 130HZ,741 OK!)
thank you!
Hi Mathieu, if you ground pin5, IC2 will shut down so it cannot be connected to ground. The capacitor is for preventing any stray pick up by IC 2 pin5. Higher voltage on pin5 will produce wider PWM at pin3 of IC2, and vice cersa.
The zener diode ensures that the maximum voltage at pin5 can never be over the supply range at pin4/8 of the IC
Hi Swag for the pwm the frequency varies between 130HZ to 70HZ but looks unstable with my frequency meter! is it ok?
Hi Mathieu, please check the frequency at pin#3 of IC1….
Hello Swag ic1 is a reference frequency in monostable mode of ic2 but the 555 is unstable!can it cause problems for the final stage of the pwm?
thank you
Hello mathieu, IC1 is an astable, IC2 is a monostable. IC1 is configured to provide 95% ON time and 5% OFF time. The design is perfectly stable.
Hello Swag can i use it for 100Khz output ?
Yes you can use it with any frequency of your choice…
Hello Swag, can you tell me about the frequencies of ic1 ic2 and the 741 to have an idea! i have used your 555 monostable calculation but in milliseconds!
thank you
Hello Mathieu, IC1 frequency can be 200Hz for a 50 Hz inverter application. IC2 is a PWM converter, it takes the frequency from IC1
hello Swag onDesign#2 pin 3 of the 741 do i apply a 12V input or a 6V? or do i need to check the good voltage by varing the potentiometer?
thank you
Hello Matheiu, use a DC for the inverter which produces 250V output……. now connect this 250V with the input of IC 741 divider, and adjust the pin3 preset such that the output of the inverter comes down to 230V
Hi Swag on Design#2 what is the input ac voltage? 220V,110V? can it work in khz frequency? can i put a 230vac on input?
thnak you!
Hi Mathieu, it can be 110V or 220V it does not matter. The voltage divider resistors can be set according to the input supply level.
Any frequency can be used.
Hello Swag like the question above on Design#2 you havent tested yet this circuit! what % duty cycle can give this circuit? estimation!
thank you!
Hello matheiu, duty cycle will depend on the voltage level at pin#5. At 0V, the PWM will be almost zero, and at fully supply voltage the PWM will be almost 95% of the supply level.
The IC1, IC2 stage is a fully tested deign
Hello Swag for Design#2:
pin 3 of the second 555 where will it be insert on a sg3525?
thank you!
Hi Mathieu,
connect it with pin10 of the IC
Hi swagatam may the good lord continue to blessed you for the good work that you are doing by teaching the world the practical part of a electronic circuit.
Please what if i should used a rectifier circuit in the transfor terminal before fed into the circuit, wouldn’t it work
Thanks Emmanuel,
yes you can add a bridge rectifier in the last circuit without any changes. It will also provide an isolation between the secondary and primary stages
Hi swag i build inverter circuit using ic sg3525 successfully but only problem there is big delay when city power go off the inverter oscillator take time to switch on and this cause my computers to go off. How should solve this problem please swag!!!
Hi Moses,
Please post this question under the same article which you are referring to, so that I can see the schematic and understand the issue you are facing at the moment…
Good day Sir.
Sir could you help me with a timing alarm circuit.
I want the project to work as follow:
1st, to ring an alarm at 35minuts intarval for atleat 3 times.
2nd, to ring an alarm at 35minuts intarval for atleast 2 time.
3rd, to ring an alarm at 35minuts interval for atleast 2times.
Again, I want another one to work at 30 minuts interval with the above discriptions, that is 1st, 2nd and 3rd.
Thanks for the help Sir.
Aminu, you can try the following concept and adjust the stages accordingly as per your need
https://www.homemade-circuits.com/2013/06/automatic-programmable-school-bell.html
limit the number of timer stages as per your need…..
Thanks for the help Sir.
But I dont mean C3 of IC4093 of the shared link. I mean C3 of the above IC555.
you can use 0.47uF also for C3.
Sir, I built this circuit. But I did not used IC4047, as suggested, I used IC4093 as in this inverter:
http://www.www.homemade-circuits.com/2012/02/how-to-build-400watt-high-power.html?m=1.
And is it necessary to use C3 i.e 0.33uf 400v?
Can I used any of 0.39uf 400v or 0.47uf 400v or any other one?
Thanks Sir.
Aminu, C3, and R7 are responsible for generating the basic 50Hz frequency, you can replace C3 with any other capacitor but then you will have to also change R7 value proportionately so that the 50Hz frequency is not disturbed.
Sir, I have bought the components of this circuit to give it try with the suggested circuit of IC4047 and I will update you on it very soon.
Thanks for your effort to help us Sir.
Aminu, I hope you have understood the working of the circuit and will be able to optimize the results correctly…otherwise it could be difficult to get the intended output.
Wish you all the best
Hi Swagatam, have you tested this circuit?
Hi Wade, I have not yet tested it.
I can just buy any optocoupler and place in this circuit right
no, it's a homemade LED/LDR opto, not the regular ones that are available in the market