This simple, enhanced, 5V zero drop PWM solar battery charger circuit can be used in conjunction with any solar panel for charging cellphones or cell phone batteries in multiple numbers quickly, basically the circuit is capable of charging any battery whether Li-ion or Lead acid which may be within the 5V range.
Using TL494 for the Buck Converter
The design is based on a SMPS buck converter topology using the IC TL 494 (I have become a big fan of this IC). Thanks to "Texas Instruments" for providing this wonderful IC to us.
You may want to learn more about this chip from this post which explains the complete datasheet of IC TL494
Circuit Diagram
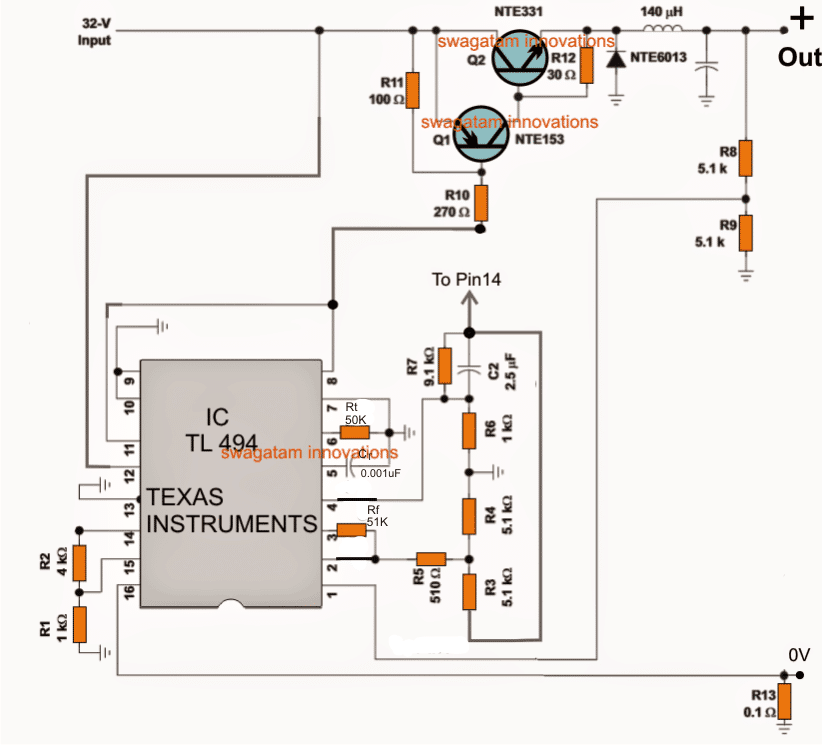
We know that a 5V solar charger circuit can be easily built using linear ICs such as LM 317 or LM 338, you can find more info on this by reading the following articles:
Simple current controlled charger circuit
However the biggest drawback with these linear battery chargers is the emission of heat through their body or through case dissipation, which results in wastage of precious power.
Due to this issue these IC are unable to produce a zero drop voltage output for the load and always require at least 3V higher inputs than the specified outputs.
The circuit of the 5V charger explained here is completely free from all these hassles, I have explained how an efficient working is achieved from the proposed circuit.
Referring to the above 5V PWM solar battery charger circuit, the IC TL494 forms the heart of the entire application.
The IC is a specialized PWM processor IC, which is used here for controlling a buck converter stage, responsible for converting the high input voltage into a preferred lower level output.
The input to the circuit can be anywhere between 10 and 40V, which becomes the ideal range for the solar panels.
The key features of the IC includes:
Generating Precise PWM output
In order to generate accurate PWMs, the IC includes a precise 5V reference made by using bandgap concept which makes it thermally immune.
This 5V reference which is achieved at pin#14 of the IC becomes the base voltage for all the crucial triggers involved within the IC and responsible for the PWM processing.
The IC consists of a pair of outputs which can be either configured to oscillate alternately in a totem pole configuration, or both at a time like a single ended oscillating output.
The first option becomes suitable for push-pull type of applications such as in inverters etc.
However for the present application a single ended oscillating output becomes more favorable and this is achieved by grounding pin#13 of the IC, alternatively for achieving a push pull output pin#13 could be hooked up with pin#14, we have discussed this in our previous article already.
The outputs of the IC has a very useful and an interesting set up internally. The outputs are terminated via two transistors inside the IC.
These transistors are arranged with an open emitter/collector across the pin9/10 and pins 8/11 respectively.
For applications which require a positive output, the emitters can be used as the outputs, which are available from pins9/10.
For such applications normally an NPN BJT or an N-mosfet would be configured externally for accepting the positive frequency across the pin9/10 of the IC.
In the present design since a PNP is used with the IC outputs, a negative sinking voltage becomes the right choice, and therefore instead of pin9/10, we have linked pin8/11 with the output stage consisting of the PNP/NPN hybrid stage.
These outputs provide sufficient sinking current for powering the output stage and for driving the high current buck converter configuration.
PWM Control
The PWM implementation, which becomes the crucial aspect for the circuit is achieved by feeding a sample feedback signal to the internal error amplifier of the IC through its non-inverting input pin#1.
This PWM input can be seen hooked up with the output from the buck converter via the potential divider R8/R9, and this feedback loop inputs the required data to the IC so that the IC is able to generate controlled PWMs across the outputs in order to keep the output voltage consistently at 5V.
Other output voltage can be fixed by simply altering the values of R8/R9 as per ones own application needs.
Current Control
The IC has two error amplifiers set internally for controlling the PWM in response to external feedback signals.
One of the error amp is used for controlling the 5V outputs as discussed above, the second error amp is employed for controlling the output current.
R13 forms the current sensing resistor, the potential developed across it is fed to one of inputs pin#16 of the second error amp which is compared by the reference at pin#15 set on the other input of the opamp.
In the proposed design it is set at 10amp through R1/R2, meaning in case the output current tends to increase above 10amps, the pin16 can be expected to go higher than the reference pin15 initiating the required PWM contraction until the current is restricted back to the specified levels.
Buck Power Converter
The power stage shown in the design is a standard power buck converter stage, using a hybrid Darlington pair transistors NTE153/NTE331.
This hybrid Darlington stage responds to the PWM controlled frequency from pin8/11 of the IC and operate the buck converter stage consisting of a high current inductor and a high speed switching diode NTE6013.
The above stage produces a precise 5v output ensuring minimum dissipation and a prefect zero drop output.
The coil or the inductor can be wound over any ferrite core using a three parallel strands of super enameled copper wire each with a diameter of 1mm, the inductance value can be anywhere near 140uH for the proposed design.
Thus this 5V solar battery charger circuit can be considered as an ideal and extremely efficient solar charger circuit for all types of solar battery charging applications.
For Higher Voltages up to 60V Solar Panel
For solar panels with higher voltages, such as 60 V solar panels, the design can upgraded by adding zener diode regulator at pin12 of the TL494, as shown below:
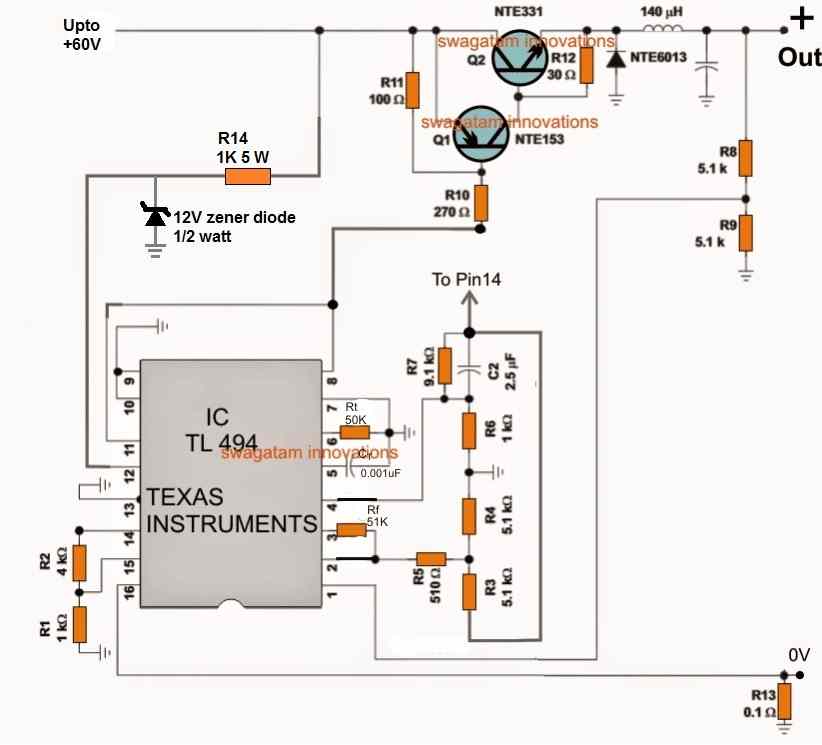
Hello sir, I want a 3 stage charge controller with current adjust ( 0-5 A ) for 12V CCTV UPS to increase battery life, power voltage is about 13.8V and battery is 12V sealed acid, Can you help me to design this charge controller with transistor?
Hello Ruhollah,
I will design it soon and let you know…
Thank you, I will wait for your favor
Here’s the circuit diagram which i have designed, I will write the description also and let you know once it is finished:
" rel="ugc">
Hello, Thank you for circuit design. how much the P3 and P4 Variable resistance? how much the most current that this circuit can support ( 5A or up )? please change circuit without current limit too.
I have added the full description under the following article, please check it. But i think the LM338 current limit cannot work using a single LM338 IC, instead you may have use two separate LM338 current limiter stages for the current limit #1 and #2:
https://www.homemade-circuits.com/make-this-3-step-automatic-battery/
Maxx current is 5 amp if LM338 are used.
Without current limiting won’t make sense in this design…
Hello, Thank you for Description about circuit, How much resistance that connect to input +14.5V And Tip3055 IC?
Hi, it can be 50 ohm 2 watt…
Hi, thank you very much for design the circuit, description that and reply all questions. I don’t forget your favor. Be in the protection of God
You are welcome!
Hello sir, it’s me again Daniel. So, it finally worked, but it charges the phone at a slow rate and it’s a 15w 12v solar panel. Is there anything I can do to increase the charging speed?
Glad it worked, Daniel,
You can try connecting two panels in parallel and check the response, or you can increase the power of the solar panel rating
Hello Mr Swagatam! I’m in a place where there is no electricity, so I took with me a 12v solar panel which I will use to charge my phone or a lead acid battery for storing power when I’m not around. I used a USB QC 3.0 DC-DC buck converter charging step down module which can take 6 to 32 volt maximum as the input and give out 5v as the output, so I then plugged in USB type C to charge my phone it indicated charging but the phones percentage wasn’t increasing. So what do I do?
Hello Daniel,
That means your mobile phone is not accepting the charge from the source.
Please confirm the output with a meter to ensure it is 5V DC, or you can add a 7805 IC at the output and check the response.
Hi Sir Swagatam! It’s me again, Charm! I already have this circuit produced in a PCB. For the transistors, I used TIP32C and TIP31A which are TO-220 package. The NPN transistor (TIP31A) heats a lot. And I will be converting 24V input to 5V output. I would like to ask you about heat sink recommendations and specifications that I could use.
Thank you Charm,
The transistor must not heat a lot, otherwise it would defeat the main purpose of a buck converter. Can you tell me the current specifications of your circuit…it shouldn’t be more than 1 amp. And did you use an inductor with the correct inductance value?
Hi Mr. Swagatam! the current of the circuit is 1A. I used the same inductance value of the inductance. When I put my battery as the load/ output. the transistor Q2 heats a lot that I couldn’t touch it.
Hi Charm, what is the battery Ah rating, is it drawing more than 1 amp? Also, check the input side voltage, if it drops significantly then your circuit might not be working correctly.
I have 2 batteries arranged in parallel. Each battery has specifications of 3.7V, 2600 mAh.
The input side voltage remains 24V when I turn on my circuit. The output voltage gives me a steady 5V.
OK, that means the current draw is much above 1 amp. Those two batteries can draw more than 3 amps if not restricted.
Try with a single battery and check the heat, if the heat is manageable that would clarify the circuit is OK.
In that case you can replace the TIP31 with a TIP35, and then use two batteries.
hi Sir! I tried with a single battery which has specification of 3.7V 2600 mAh. the TIP31 is still getting hot. Any recommendations?
OK, in that case, please try replacing only the TIP31 with TIP35, and check the response.
Sir, What should be the voltage and ampere of TIP35? I have seen 100V 25A, 80V 25A, 60V 25A
Charm, Since your max circuit voltage is 24V, you can use the 60V version.
Hi Sir! When my battery is fully charged, will this circuit cut the charging process? If no, can you please suggest a way to cut off the charging when the battery is fully charged. Thank you so much appreciate your help
Hi Charm, auto cut off is not included in the above design. However, an auto cut off may not be needed if you keep the full charge supply to the battery a shade lower, for example at 4.1V (4.2V being the full charge level for a 3.7V Li-Ion battery).
Anyway, with 0.125 amp supply input your battery may take ages to get fully charged.
Hi Sir! To achieve the 4.1V as my input voltage, do i need to add an external step-down converter to reduce the 5V to 4.1V?
For the solar panel, i will change my solar panel input that has more power to generate atleast 600mA. Thanks a lot!
Hi Charm, you can add the following regulator at the output of your existing circuit. For the zener diode you can use 5.1V zener. Make sure to put a 1k across the output of this regulator while adjusting and measuring the 4.1v. Adjust the 1k preset for adjusting and getting the 4.1v output.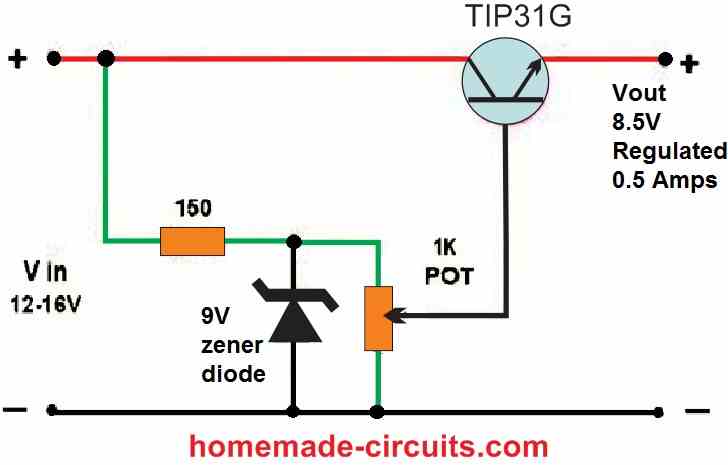
" rel="ugc">
Hi Sir! Please clarify the part where I need to put a 1k across the output of this regulator. Do you mean that after the Vout + and – I will put a 1K ohm resistor and after that will be my new Vout?
You are right Charm, It should be connected BETWEEN the Vout and the (-) of the previously linked circuit. The (-) of this circuit must be also connected with your PWM circuit’s 0V line.
Hi Sir! Do you mean, I will add a 1k ohm resistor after the Vout (+) and (-) of the PWM circuit. And after the 1K ohm resistor I will connect the Vin (+) and (-) of the voltage regulator using emitter follower transistor. And then connect my battery.
Hi Charm, you must connect the 1k across the emitter of the regulator transistor and ground. The output of the pwm circuit will connect with the input of this regulator circuit.
Hi Sir, I have an available buck converter module here, it uses lm2596. Can I use it to generate 4.1V? Thank you
Yes, you can use it to generate 4.1v, I had earlier suggested you the very same converter which is one of the easiest and most efficient.
Hi Sir! 18650 li-ion batteries work with 1A current output. If I want to charge my 18650 batteries using this circuit, how can I generate 1A? I read the article that said its output current is 1A.
The output current will depend on the input current, and the inductor wire thickness. Please let me know how much input current are you suppling to the circuit?
Since I will be using a 1.5W 12V mini Solar Panel, my calculated input will be 0.125A. I am not sure if this current can trigger charging my 18650 batteries.
A 12V 0.125 amp input will not produce 5V 1 amp current, you will need at least 12V 600mA input to get 1 amp out.
hi Sir! I was able to generate 5V output with 24V input. My next question is, can I directly charge 2x 18650 li-ion batteries arranged in parallel with 3.7V using this circuit? If yes, what is the output current of this circuit to be able to charge the 18650 li-ion battery?
Hi Charm, Glad you could get the circuit working, and I hope you are now getting the intended frequency at pin#11 and pin#8.
You can charge Li-ion batteries using this circuit. The output current will depend on the input current.
Hi Sir. I will be testing the frequency at pin#11 and pin#8 at school tomorrow. I will let you know.
Sure, no problem Charm.
Hi Sir! I am thinking of the problem with my transistors and diode connected to my pin#8 and pin#11. I changed my transistors from NTE331/NTE153 to TIP31C/TIP32C. I changed the Diode NTE6030 to Schottky 45V 6A. And my capacitor is an electrolytic 2200 uF 35V. Can you advice if there is a problem when i connected this to my IC. I already changed my IC 2x to be sure my IC is not damaged.
Hi Charm,
Do one thing, remove the transistor connection from pin#8 and 11 and check the frequency without anything connected to these pins.
If still there’s no frequency then you will have to investigate the IC connections and configuration deeply.
Hi Sir! Do i need to connect pin#8 and pin#11 to VCC to test the frequency?
You don’t have to connect those pins to positive, just keep them connected with each other, and test the frequency across their junction and the ground, with a frequency meter.
Hi Sir! I tested this circuit with a 12V input with a power supply, however, instead of getting a 5V output, I am getting a 12V output. I am confused whether I will get 5V output despite having an input of 12V. Please help
Hi Charm,
Is your IC correctly oscillating and generating the required PWM frequency at the base of the transistors? Please check whether the IC is generating frequency at pin#8 and pin#11 or not. Try altering the RT, CT values and check whether the frequency is changing or not.
Once you confirm the above, next try reducing the value of R9 and check if that reduces the output voltage or not.
Hi Sir Swagatam! I changed my transistors from the NTE153/NTE331 to TIP31C/TIP32C because I could not find the NTE153/NTE331. At the base of the transistors TIP31C/TIP32C I am getting 12V output when I supply the circuit with 12V. Also at pin#8 I am getting 0.44V and at pin#11 I am getting 12V.
Should I expect 5V even if I have 12V input?
Hi Charm, With 12V at the input you should be able to get 5V at the output if R8 and R9 are appropriately set.
If you are getting 12V at pin#8 and pin#11 that means your IC is not oscillating and something’s wrong with the IC or the circuit connections.
You must check the frequency with a frequency meter or preferably using an oscilloscope.
Pin#8 and pin#11 are joined together with the base of Q1, so how are you getting different voltages at those points?
Hi Sir, I rewired my circuit in the IC. I used 24V input, I am getting 24V in pin#8 and 24V in pin#11. I am getting 5V on pin#14. But, my output is still 24V constant. Should it work like this? Do I need to add a separate voltage regulator to get 5V?
Hi Charm,
If you are getting 24V at the IC output that means your IC is not oscillating and is not working as required.
You must check the frequency across these outputs using a frequency meter or an oscilloscope.
No external regulator is required, since this buck converter itself is supposed to regulate the output voltage to the desired levels.
Hi Sir! My R8 and R9 have 5.1K ohms each. Will there be any effect in the circuit with changing the transistor from NTE153/NTE331 to TIP31C/TIP32C?
i will re-wire my circuit with my IC to see my connections.
No, that will not have any effect on the new transistors.
Dear Sir Swagatam,
For the CT, I could not find an electrolytic capacitor that has a value of 0.001 uF. According to the data sheet, this is the Capacitor used to set oscillator frequency. Kindly let me know if I can use a ceramic capacitor instead of electrolytic in this project.
Thank you!
Hi Charm, CT and C2 are actually non-polar capacitors, so you can use any ceramic or PPC capacitor for these capacitors.
Hi Sir! Thank you for sharing a much better circuit, but I already ordered components and did my breadboarding. The only component that is missing is the 2.5 uF. If I change the C2 to 2.2 uF, do I also need to change the resistance of my R7?
Hi Charm, R7 is not related to C2 so it can be as given in the diagram. R6/R7 determines the dead time.
C2 decides the soft start level of the output or for how long the dead time can be held to maximum until it returns to normal.
So C2 is also not crucial and a 2.2µF can be used without altering R7.
Here’s what the datasheet says:
Initially, capacitor C2 forces the dead-time control input to follow the 5-V regulator, which disables the outputs
(100% dead time). As the capacitor charges through R6, the output pulse width slowly increases until the control
loop takes command. With a resistor ratio of 1:10 for R6 and R7, the voltage at pin 4 after start-up is 0.1 × 5 V, or
0.5 V.
The soft-start time generally is in the range of 25 to 100 clock cycles. If 50 clock cycles at a 20-kHz switching
rate is selected, the soft-start time is:
t = 1 / f = 1 / 20kHz = 50µs per clock cycle
The value of the capacitor then is determined by:
C2 = (soft – start-time) / R6 = (50µs x 50 cycles) / 1k = 2.5µF
Hi Sir Swagatam!
I cannot find an Electrolytic Capacitor with 2.5 uF (C2 in the schematic diagram). Can you suggest any other alternative capacitor value? Also, if I change my C2, what could be the value to replace my R7.
I am breadboarding my project and really need your help on this matter. Thanks a lot.
Hi Charm,
I think you can use a 2.2uF instead, that won’t affect the working by much.
By the way there’s another much better circuit which you can try instead, here’s the link of that article.
https://www.homemade-circuits.com/0-to-50-v-adjustable-switching-power-supply-circuit-using-ic-lm2576/
Let me know your thoughts on this.
Hello Swagatam
Can tl494 be replaced by SG3525 bcs I don’t have the tl494 ic
Hi Klinton, that may not be possible, both ICs have different pinout functions.
Hi Sir Swagatam! I would like to ask if I can add a way to charge my batteries by plugging them in AC power, just like power banks so when there is no sunlight, I can still use my solar charger. Can this circuit handle AC?
Hi Charm,
If you want to use AC outlet to charge your cell phone then you will have to associate an SMPS mobile charger with the solar module. The SMPS charger can be any normal mobile phone charger.
Hi Sir! It’s me again Charm! I would like to ask what is the specification of you diode as I cannot find NTE6013 in the market.
Also, you have mentioned that I can connect both my back-up batteries and USB in the output marked +5 and 0V. Does that mean that when the PWM charge the back-up batteries, at the same time I can get power from the batteries through the USB; or the USB will directly get the power from the Solar Panel since both outputs – back-up battery and USB – are connected to the output?
Your kind response is much appreciated for my project.
Hi Charm,
You can use any 6 amp schottky diode instead of the indicated one.
The solar panel will charge both, your 12V batt as well as the USB batt, as long as sufficient sunlight is available.
I think you should consider trying the following circuit instead which is much more reliable and easier to build:
https://www.homemade-circuits.com/0-to-50-v-adjustable-switching-power-supply-circuit-using-ic-lm2576/
Hi Mr. Swagatam! Noted on the diode. I actually need to do a project that is a PWM solar charge controller that can also function as a power bank. So, I’m thinking of adding another circuit after the solar charge controller charge the battery so the USB can harness power from the battery. However, I would like to ask if the battery is charging through the solar panel, can I simultaneously draw power from the battery to charge my phone?
Hi Charm,
If your solar panel and the PWM controller components are adequately rated then it should be able to simultaneously handle both the batteries.
You can definitely another small buck converter circuit to harness the required 5V from the 12V source.
Hi Swagatam! Thank you for sharing this amazing circuit. I am working on a PWM Solar Charge Controller. I would like to know if I can use this PWM Circuit for a Charge Controller with a built-in Solar Panel and Batteries, like a solar power bank principle?
Thank you!
Thank you Charm,
Yes, you can use the above PWM charge controller for your application, it should work.
Thank you for your response Swagatam. Can you please tell me where should be the connection of my batteries? As I understood, the 23V input is from the Solar Panel. I wonder about the connection of the Batteries. Thank you
Charm, The buttery should be connected across the outputs marked as Out(+) and 0V. R13 value decides the max current output.
Almost forgot to mention my concern about tripping the overvoltage protection in the inverter which is why I mentioned pulling battery out of bank and using the diode to keep any of the high frequency PWM from sending too much voltage to that. It gets real close as it is with stuff like it is when the solar voltage goes over 14.5 which it does once in a while. I loose AC power until it drops back below. I’ve had to put extra draw on inverter a couple of time to pull the V down. But that is wasting power from my array that could be put in batteries if they would just take it and keep everything else running along nicely.
Me again, I see others have mentioned solar panels and other issue. What I need to do is use a pair of 12v nom. 25 watt panels as a source for a high voltage compared to normal voltage from a 12v charge system to work with a pulse width system, such as this TL494. I have a set of sulfated batteries I need to get brought back asap but I am having issues with my inverter system due to not being able to hold a voltage level adequate for the inverter during the night if I put anymore load on it from what I do getting through the darkness in my off grid RV. I have 400 watts of panels and a new MPPT which has made a significant improvement and another 200 watts of panels arriving any day now, planning on another 200 next month. I will be switching to a 24 volt bank beyond those 800 watts to stay with the same wiring installed now as the MPPT would be maxed out at just under 800. As far as I can figure, the max is rated at 750 but since there are inherent loses in the system, I should be able to get by, hopefully(?),or at least pull out 200 watts of panels until I can afford the 24v to 12v step down box. If I can get a working desulfator system functioning without having to purchase something like a NOCO Genius smart charger, I really want one of those anyway but it’s a money issue, which way to jump first? Buy, build? Winter is coming and my batteries are suffering but I must get them working again or else, more money I don’t have. So If I use 2 of the 25 watt panels to get the higher voltage needed to knock the sulphate crystals off, and build the PWM either by using a simple 555 circuit or a TL494 as is done here, I have some power supplies from computers I might be able to salvage parts from, along with the other stuff I have on hand. I would use either a linear regulator on the Vcc to keep 12v and work with the 42 volts OCV the panels would make during the off cycle which would be pulled down on account of the basically 12 or less in the battery until things hopefully snap out of it. Probably will be near the end of the month and then will have the funds to just get the NOCO. I might be able to get away with pulling out 1 battery, connect a blocking diode into the + terminal to keep the pulses from the desulfator going to any of the other batteries while running the inverter at night, just a little more draw. This is getting too deep to keep all lined out in my head. Anyhow, a little to chew on for now, maybe your engineering mind can do better than mine. Thanks in advance, and if you have some other idea, glad to look at it. I get into too much trouble with this stuff for my own good I know.
Thanks for the detailed explanation!Your knowledge seems to be better than mine, so i guess what you are doing is correct and should work.
Can this circuit be modified to deliver up to 12 volts and 30amps?. I’m currently working on a circuit like this but I don’t know how to modify this circuit to suit my spec of 12v 30amps, please I will appreciate you if you’ll help me out. Thanks
It can be modified to 12V 30 amps by upgrading the Q2 transistor to 50 amps, and the accompanying diode also to 50 amp. The inductor will also need to be upgraded to 30 amps
Nice work Mr. Swagatam
For Solar Charge Controller how do this circuit isolate/float/stop charging at full charge of battery?
Thank you Sammy.
This circuit will not auto cut off or provide float charge. For these features you may have to add external circuits.
This circuit will only convert a high DC voltage into a low DC voltage with maximum efficiency.
Hi my name is John and I am looking for a circuit for a mppt charge controller circuit to work with high voltage input say 36-48 volts and supply 12v output around 30-40 amps can you help
Hi John, I am sorry, I do not have the specific circuit you are looking for. MPPT is a difficult subject otherwise I could have tried to design it for you!
can i replace the npn transistor at the end with npn mosfet. for example like irfz44n or irf3205
The above circuit is designed to work with power BJTs so I don’t think the NPN can be replaced with a MOSFET. You can try some other equivalent power transistor if the indicated transistors are not available.
okay thank you my best teacher for the information. can you tell me the schematic that uses the npn mosfet to me. or tell me what should i change if i want to use mosfet as power
Thank you zen, I think if a N-channel mosfet is used then there won’t be any need for Q1, R11, R12. The mosfet gate can be directly connected to R10. R10 may need to be reduced below 50 ohms.
OK, I’ll try to change it. And I’ll let you know the results. thank you my best teacher
sure, no problem!
hey my best teacher i have tested this circuit. however I failed to replace the transistor with an NPN mosfet. but i managed to make this circuit with transistor. as you have explained. my question. why is there a ringing sound when the circuit is loaded with 5 amps and above? where is that sound coming from? I used a used choke inductor that was on ATX with yellow and red enamel. Then I combined the enamels in series to get more twists. all work fine when load is applied. and the temperature is also not too hot in all parts. yes it’s just a little heat in the bridge diode. because I installed 4 6A diodes. And I know it’s not high enough to support 15 amps. the output can also vary from 4-24 volts from the 30 volt input. what should i change if i want it to be variable from 4-28 volts? i’m using a 10k pot that i tied with 5k1. before you answer all my questions. i want to say thank you very much to you. with your guidance through your website I can get to know the world of electronics better.
Thank you Zen. I am glad you could build the above circuit successfully.
However I am not sure how to stop the ringing sound? Did you use a 140 uH inductor as suggested in the diagram?
Regarding making the circuit adjustable, as far as I know changing the value of R9 will allow the output to adjust the voltage accordingly.
You can try replacing R9 with a 10K pot and check how it responds.
ok thanks for the response. I really don’t know the exact size of the inductor. aha.. I’m starting to understand what the problem is. Up here I am satisfied with the results of this circuit. and that makes me very happy. now i will see another circuit in your website and i will try to build it
No problem Zen, Glad to know the above circuit is working for you! All the best to you!
Zen, I see this is a fairly long time since this was posted but I will give my thoughts on this. I am currently working on a circuit that is buck converter myself. 24v/12v, so in this circuit there is a final Q to drive an inductor also, the base of the Q is being triggered by a diode/capacitor voltage doubler. This section of the circuit is to hard trigger the Q to get it to turn on as high as possible so the loses are reduced. The thing is, BJT’s are current dependant triggering while MOSET’s are strickly voltage dependant so if the voltage applied to the Gate is increased, Not beyond the point of tolerances, they are fired very efficiently. Since MOSFET’s are generally so much more efficient at conducting over BJT’s ( much less power loss in heat) it is obvious why they are preferred in high power circuit. The big deal is choosing P or N channel. One usually work better for specific application than the other based on how the circuit is designed on paper first. You need to know differences in function based on High/LOW side arrangements.So, with that, consider including a voltage doubler section driven by the IC to trigger the FET, this is a good idea also if you wish or need to parallel FET’s to increase power capacity, obviously adding inductors also, each can be used modularly and be sure to include low R values between the output of the doubler and each G of FET so that all FET’s are sharing the load equally. Values around 0.1 to 1r should work,I think. I’m not an EE, this is just what I have read and seen in the past. Feel free to contact me if you have any replies or comments. We are all in this together and communication is key to innovation.
Thank you Bret,
I think the Q1 transistor being a PNP and its emitter hooked up with the input suply will have enough voltage to drive a MOSFET, if the Q2 is replaced with a MOSFET. However if Q2 is replaced with a MOSFET its gate will need to be safeguarded with a zener diode to prevent a high gate voltage, therefore R12 will need to be replaced with a 12V or 15 V zener diode.
I will try it later I will tell you the results
Hi Swagatam, I was searching for information on how to step down voltage and came across your Homemade Circuit Project page by accident. It is very informative but sadly it’s mostly Greek to me. I’m looking for info: I wanted to use a 12v auto battery on a trickle charge to keep a cellular device 3.8v Li ion constantly charging without damage to the battery or the cellular device. The cellular device battery only lasts about 3-4 hrs because of the distance of the cell tower. The instructions that came with the cell device says you must remove the charger once the battery is charged. Is doing what I want to do possible? Or is it the same as keeping a charger plugged in continually? I found this XL4015 5A DC Buck Step-down Adjustable Voltage Power Converter w/ LED Voltmeter on Ebay.
Specs on this converter:
Input volt range: 4-38V, DC
Output volt range: 1.2-36V,
DC Max output current 5A
Max Continuous Output Current: 3.5A
Current Conversion: DC to DC
I thought this might work? The problem I have with all of this is I know nothing about this type of work. I’m a Millwright, Mechanic, Hydraulic repairman & Bagpiper. 🙂 Thank you for your time
Have A Blessed Day
Jim
Thank you Jim, you can use the XL4015 buck converter for your purpose.
The full charge level of a 3.7 V Li-Ion cell is 4.2 V, and the charger strictly requires to cut off once this voltage level is reached. However, if you adjust the charger to produce only 4.1 V, that would allow you to get rid of the cut off circuit, since at 4.1 V the cell can be kept connected to the charger indefinitely. The only downside is that the cell will be charged only up to 80 to 85%, which is not bad actually considering the fact the this condition has more benefits than losses.
However the current can be an isssue, whch must be ideally adjusted to 0.5 C, meaning at a current level that is 50% of the mAh rating of the cell.
Hi Swagatam, thank you very much for explaining everything to me about the charger & settings. I will certainly give it a go in making this step down charger. What I’m understanding about the battery is if I change to other batteries that have different mAh, I will have to change mAh current according to the particular battery I am using, am I correct in this thought? Thanks again for your time Have A Blessed Day! Jim
You are welcome Jim! Yes that’s correct, for every battery, the mAH value will need to considered and the input current adjusted accordingly.
Hi Swagatam,
My input voltage from solar panel is about 40v instead of 32v in the diagram. What is the implication of this? Can I still use the circuit for the solar panel?
Hi Joe, the maximum tolerable voltage spec of the IC is 40V, so it won’t be safe to use 40 V as the input
I need your advice on this:
I got a cheap buck converter that can charge my 12v 100AH battery but the issue is leaving it permanently connected to the battery even while I am away. Will the solar panel draw the battery voltage when it is night? Do i need to connect a diode at the input and output?
The buck converter is the SZBK07 DC-DC converter I don’t know if you know about it.
Features:
– Input voltage: DC 6-40V (10-40V recommended)
– Output voltage: DC 1.2-36V
– Output current: DC maximum 20A (15A recommended)
– Output power: maximum 300W
– DC-DC converter: step down (buck)
Hi, yes you will need a diode to protect against the reverse drain of the battery through the panel, during night time.
so does it mean I need 2 diodes or just one? Input or output or both?
And again, what value of diode can you suggest?
Thanks for you help
Just one diode on the positive line is enough…
Hi Hi Swagatam,
Can I use an inductor coil that is 150uH without a ferrite rod or core. The one I got is only wire (copper) coiled.
You can try it, might work
Hi Swagatam,
Please I need clarity on the negative input and output points. Will both points be taken from 0v or ground?
Hi Joe, all the ground symbols correspond to the negative line, and this line is common to both input and output
Hi Swagtam you might worng. The ground is not common for both input and output. Output gnd is connected with 0.1ohm shunt resistor and output gnd comes frm that other pin of shunt resistor.
Also where could I got 4K, 5.1k, 510 ohm and 51 K.?
The datasheet of TL494 also shows. however we can build custom resistor with series. but that is not feseable.
Hi Chandrashkhar, yes you are right, in the above circuit there’s a current limiter resistor which I totally missed. But normally in other DC circuits the ground is the negative common line for all the stages.
You can build custom resistors by connecting other available resistors in series and parallel, appropriately.
Also I wanted to be sure: the 2.5mf capacitor is electrolytic right? What should be the volts?
In place of the NTE6013, can I use 6A4, byx71 or in5408?
yes the 2.5uF is an electrolytic capacitor, its voltage can be 50 V. You can use any rectifier diode whose current rating is minimum 2 times the load current.
Hi Swagatam,
If I may ask, what is the value of the capacitor at the output near the L1 inductor coil?
Also can I use 51k in place of 50k?
Hi Joe, that capacitor is the filter capacitor, should be a high value capacitor above 2200uF
Hi Swagatam,
Can the circuit be redesigned to charge 12 VDC batteries? It seems that reference voltages and other components must be changed. What do you think?
Hi Pablo, it can be done by replacing R9 with a 10k preset, and adjusting this preset to get 14V at the output
Dear Swagatam,
For the 10k VR, which of the pins will be connected since we have 2 points in the diagram?
Hello Joe, you can use the center lead of the preset and any one of the other leads, and leave the third lead unconnected.
Thank you Swagatam for your interest and reply. I welcome your suggestion. I will build the circuit. We meet. Greetings to you.
No problem, Abuesak!
Greatly appreciate all of your examples and certainly learning lots from you. I am currently working on a charging circuit that can be plugged into a 220 or 3 phase power connection. I have a 5kW transformer that can take the 220 Volt and provide 100 amps in current. I am currently using the 120 to 120 output and connecting to a rectifier. I want to charge 144v battery sets at 100amps but the output is 180 dc with capacitor filter. How can I bring the voltage down from 180vdc down to lets say 150vdc without restricting the current so that I can can charge multiple sets of 144 batteries at maximum current. Otherwise I will have to break it down to 48vdc sets and recombine which will make it hectic swapping more batteries and increase current handling requirements. Thank you very much
Thank you, and glad you are finding my articles useful.
You can try applying the last concept from the following article:
https://www.homemade-circuits.com/low-dropout-5v-12v-regulator-circuits-using-transistors/
However, you will have to upgrade the transistor numbers accordingly so that they are rated to handle up to 200V
The wattage of the 20k will be 10 watts, and the zener will need to be 150V, whose value will decide the output voltage
Happy day I hope you are fine Swagatam, I would like you to help me complete my battery charger project with TL494 to Buck Converter and clarify the numbers Q1, Q2, R8 and R9 value which corresponds to my application, Greetings to you.
Thank you Abuesak, I would rather suggest you to first make the smaller basic design as given in the above article. If you are able to build it successfully, then you can simply upgrade the transistors and the coil accordingly through a quick online search regarding these parts
Thank you Swagatam for giving me the info to implement a buck converter circuit to charge my 6 volt and 500 amp batteries, but excuse me for not understanding why you said I can upgrade the transistors. Do you mean to implement the circuit without any modifications and with the same numbers Q1=NTE153&Q2=NTE331? I thank you.
You are welcome Abuesak, I wanted to say that the transistors will need to be changed with higher rated transistors to handle the 500 amp current, and same must be done for the inductor wire thickness also, so that it doesn’t burn due to the high current. Rest everything can be same. The resistors R8, R9 will need to be tweaked for adjusting the output voltage to the required levels.
Good morning sir, thanks for your well explained job…pls can the design be adjusted to output 13V/16amps, if yes how can be achieved?
Again does the pwm depend on voltage?
Thanks
Hi Onyeka, yes you can adjust it to the mentioned output value by adjusting the values of R8/R9
Aright sir, i have a small problem….after switching the input voltage using the transistor, i thought that the output of the bulk converter supposed to be a square wave(AC) of a very high frequency…..how then did we manage to converter it to a steady DC
You can see there’s a filter capacitor at the output, this must be of a high value around 3300uF or more, and this will convert the pulsating DC to stable DC.
Wow!, Good to know, thank you very much
But can use a high frequency transformer and a rectifier at the output of switching transistor to get a stable DC too?
The transistor switching output is not an AC, it’s a pulsating DC, so rectifier is not required.
Good morning sir, thanks for a great job well done, pls can output of about 13V and current of about 16Amps be gotten using TL494???
13V/16amps
Onyeka, TL494 is only an oscillator circuit, the current output will be decided by the power devices (MOSFETs) connected with the TL494…so yes it is possible.
Oh! Thanks, so which means i need datasheet to determine the one to use….. U just mentioned mosfet but what i can see in the circuit diagram is BJT.
Again You made mention of controlling the output voltage using R8 and R9, what the idea behind it..does the pwm adjust with shift in voltage?
That’s right, these are BJTs in the above shown circuit, you can change them to BD140 and TIP35 for more current, along with the wire gauge of the inductor.
Thankz for the response sir…pls lastly…. You made mention of controlling the output voltage using R8 and R9…..i got it, but what’s the idea behind it..does the pwm adjust with shift in voltage?
You can find all the details in the following link:
https://drive.google.com/file/d/1WhfgYYkcJTVgIZXJlgk7PWnVwNJ_SApU/view?usp=sharing
I tried this circuit, the problem I have is that when the output voltage is set it drops to reset again. All are properly grounded.
You can find many buck converter circuits online which you could try and see which one works for you.
Good day Engineer, please i find it difficult to find high efficient high current buck converter online, I request for a favourable response for some switching regulators ICs i may use. thanks for always being there.
Favour, you can try this:
http://www.ti.com/lit/ds/symlink/lm2679.pdf
Please can I use 103uf ceramic or polyester capacitor, for 0.001uf
103 = 0.01uF it’s not the same, so you can’t use it….
Yes Sir, I made a mistake ,can I use 102 ceramic or polyester
You can use ceramic or polyester both will work…
Thanks for the assistance, i got it, please. How can i upgrade it to serve 40amps instead of 10amps
By upgrading the BJT rating and the coil wire thickness accordingly.
How can I adjust the current control to 40amps and also get the appropriate number of turns for the inductor
What is the input current and voltage??
37v solar input, 36amps
You can try the formula presented in this article:
https://www.homemade-circuits.com/how-to-design-and-calculate-ferrite-core-transformers-for-inverters/
please i want to ask these questions sir,
i connected this circuit buck converter and ordinary charge controller i bought(not mppt), when the battery voltage was around 14.4v( wasnt around since morning), the tl494 circuit read 1.21A while the bought controller read 6.47A. i used 360W/12v panel for each.
1. why such difference
2. how best to operate buck converter.
thanks
A buck converter is used to convert excess voltage to current…if there’s no excess voltage then it’s pointless to use a buck converter. When your input is same as the battery charging voltage it’s better to connect the panel directly to the battery, no need of any converter.
please, how will i calculate the current control with a voltage divider as in pin 14 &15
Calculate R13 instead. When pin16 voltage exceeds pin15 voltage then output will shut down
Please how can I disengage the current control for now.to check
short circuit R13
Thanks sir, the efficiency I got was 52%, is there a way To improve this and minimize losses
Hi Favour, the efficiency should at least 90%, otherwise a buck converter will not make sense. The inductor and the PWM are the two aspects which need to be optimized for maximum efficiency.
Please how can I use this circuit for 100w panel for 12v battery
If your panel has higher voltage than 20 V, then you can use it
My panel has 18.65v
Is this at peak sunshine or average voltage
Peak
In that case you don’t need any converter. Just connect the panel directly to your battery.
If you intend to use one, you can try the above circuit but you may have to adjust the inductor turns a bit to optimize the output correctly.
ok sir, please how can i optimise the inductor coils, is it by adding to it or reducing
You can build the exact same circuit as shown above, and test it with a 24V/5 amp input from a power supply, and check whether it works or not as specified in the diagram. It should work because the circuit is designed by the ti.com engineers.
Once confirmed then you can gradually decrease the input voltage and proportionately reduce the turns and verify whether the optimization works or not.
can i use tip147 for nte331 and tip41c for nte153 and ba159 for nte6013. we dont have 0.001uf and 2.5uf what can i use
You can replace the transistors and the diode as mentioned by you, but the capacitors must be kept exactly as specified in the diagram to avoid confusions.
hello,
thanks for sharing. never came to the idea to use that for solar applications.
i used to create that circuit a while ago but was using bd244 and bd243 transistors. sadly the output voltage drops a lot even with light loads. do you have any idea or advice
Hi, Glad you liked the idea! In buck boost toplogies optimization becomes very crucial since the the output efficiency greatly depends on how well the coil and the PWM specs are adjusted. Next is the wire thickness and configuration which decides the current output. If all these are set correctly then the output is as intended otherwise it could go severely wrong.
i am guessing we use bc 547 and bc557 thanks i will try it and see what transpires and i will let u know thanks again so much for your blog and especialy for your time bruce
yes that’s right, wish you all the best! the capacitor and the base resistor values will decide the output timing.
The diagram needs a correction, it should be in this way: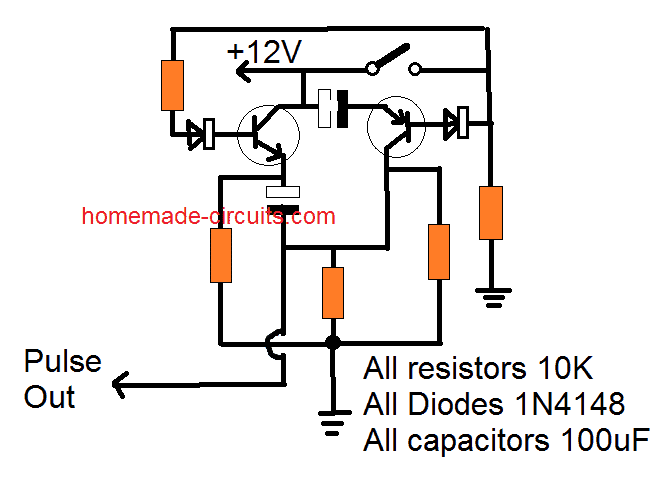
" rel="ugc">
the switch is a standard on/off switch like a lite switch….. the device i need to control with it requires a momentary contact for 3 seconds to turn on…… and another 3 second momentary contact to turn off______ what i am doing is hooking an inverter to the thermosat of a freezer. i have disconected the thermostat from the freezer wireing but left it in the freezer i then wired the compressor always on if i have the thermostat turn the inverter on it will only have to be on when the freezer needs to be on !! way more eficent than having the inverter in stand-by until the freezer needs to come on. my problem is the thermostat as you know is thermoly operated but just a standard switch like a lite switch but the inverter is momentary contact 3sec for on 3 sec for off
you can try the following concept
" rel="ugc">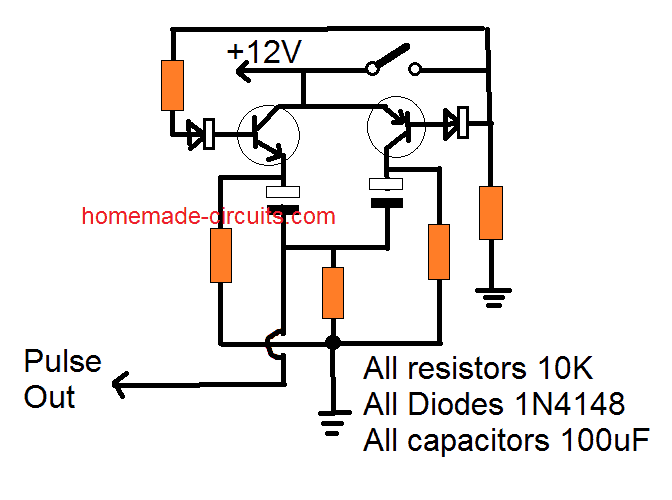
what i need is a 3 second pulse when a switch is turned on and a 3 second pulse when that same switch is turned off i will use this pulse and a relay to simulate a momentary contact switch turning something on and off thanks so much for your blog and your prompt response!!!
the switch is ON/OFF switch or a push button?
i have a inverter that has a momentary contact switch to turn on and the same to turn off (switch needs to be held for 2 to 3 seconds) i would like to hook this inverter to the thermostat of a freezer (i have already isolated the thermostat from the ac line) thanks so much for your blog i have fallowed it for a long time and made many of your ckts. bruce
Thanks Bruce, but this is a solar battery charger, it is not an inverter, you might have been mistaken
There was no mistake. i had to switch browsers for the java to work (thanks chrome) so i hit the first post comment i found when i switched to post my request. i need a ckt. that will give a 3 second pulse when a switch is turned on and a second 3 second pulse when the same switch is turned off ? thanks again!!!
OK it was actually my mistake I thought you were referring to the above circuit.
You mean to say you want a relay circuit which can be toggled ON for 3 seconds in response to a momentary push button pressing, each time this push button is pressed the relay will hold for 3 seconds and then go off….??
Quick question about SMPS chargers. Since they have a fairly constant output voltage, if I wanted to implement a 3-stage charging algorithm, how can it be implemented with the constant output voltage nature of these Switched Mode Chargers?
Thanks.
for implementing 3-stage charging only the current will need to be modified at the various steps, voltage will automatically adjust as the battery gets charged
Hello sir, what is the maximum current of the circuit and how can i reduce it to the required current it want. Thanks
The current handling specs of the circuit can be reduced by using thinner coil wire, and by selecting BJTs matching the required output current specs….
Sir in these ckt 32v is input voltage (collector voltage of NTE331 ) and gate voltage the same transistor .
As far as my buck convertor input is 300v . So shuld i got 300v as gate voltage of my IGBT.
yes that’s right but make sure your IGBT is rated to handle that much voltage….to be safe do it exactly as indicated in the linked diagram, for Q1 you can use any ordinary PNP BJT such as STX93003
I am using this to step down 24v to 12v DC to dc…
Source 28v lion pack battery 40ah
…
Pls help me with the values of a variable resistor I need to adjust to gv me the adjustable output …
And sir how many amp can it handle at its output
Thank you in advance
you will have to do it by practically experimenting with the resistor values and simultaneously checking the output response.
the current will be 10amp if the mentioned BJTs and inductor are used…
Hello,
did you confirm the working of the circuit before using it with the battery? Any new circuit needs to be first confirmed with its voltage and current parameters before implementing it for the actual job.
This is a buck converter circuit with many crucial parameters which needs to be first verified using a multimeter and a dummy load.
If you are having difficulty optimizing the above design you can try a simple IC 555 based design as shown in the following article. try the second buck circuit:
https://www.homemade-circuits.com/2015/10/calculating-inductor-value-in-smps.html
you will need to optimize the pots perfectly in order to get the expected results
Hello Sir,
The Cct was working fine
I used a 10K variable at R8…… and 9.1K at R2
O/P sliding between zero and input voltage (19V).
It charged four Li-Ion cells……. at constant voltage of 14.8 V.
Suddenly ,diode got short and Q2 heated up…..i replaced SB560 diode with YG911S3R but variable stopped working and O/P is varying B/W 19.2 Vand 18.1 V……….
Any suggestion plz……..transistors are fine TL494 is OK………
Hello beacon light,
check Q2 also, and if possible replace it with a new one.
a diode could become faulty if its current exceeds the safe operating limits….or probably if the device is a duplicate quality.
also make sure you have selected R13 correctly for proper current control functioning
hello sir , you have mentioned "to pin 14" at two points in cct diagram…..will u please define ,is the resistor configuration at pin 2,3&4 is connected to PIN 14 or what??
Same is the case with PIN 1 ??
waiting for your response ………
I'll correct the diagram and post it soon, thanks!
Ok Sir thanks a lot, but i have assembled almost all components……your guidance required in this regard…..as i got confused at the mentioned two points….
|| I have used TIP35A NPN and TIP36B PNP in place of NTE331&NTE153……is that ok??
||| If i skip 12Amp diode at output ,my required O/P is somewhere around 4Amp…..It will work for me ???
Instead of TIP36, I would recommend BD140 or 2N2907 or any other similar smaller BJT.
for 4amp requirement can replace the NTE6013 with a 6 amp fast recovery diode….the diode is a part of the buck converter and cannot be removed.
thanks sir,i got it ……diode is necessary part of buck converter……
Hello Sir pls. Which of the resistors is the R8, Rt or Ref. Thanks
Please click the diagram to enlarge, and you will be able to locate them easily
Sir I want to know solar panel specification required for charging mobile battery
you can try a 8V, 500mA panel, but make sure to a voltage regulator with it
What about for 12V battery?
adjust R8
can you suggest a nearest value for R8?
you will have to verify it practically, you may replace it with a 10k preset and set it accordingly.
ok thank you..
I am gonna make solar projects. But never bought a solar panel. How much in rs the solar panel of 12v
you can easily find out the specs and the rates from any online source, there are plenty of them on the web….the cost will depend on the V/I specifications of the unit.