
Whether a newcomer or a professional, if you are looking for the best electronic circuit projects, as per your specific needs, then you have reached the right destination. You not only get the best assorted circuit projects from this website, you also get an active online support for solving your queries and doubts related to electronics.
Here, you get the opportunity to understand the various engineering concepts as much as possible, through a 24/7 online support.
The site also helps the users to design and build customized electronic circuits, as per the desired specifications.
What is an Electronic Circuit Project?
An electronic project is basically a circuit project built using a handful of passive and active electronic parts, by soldering them on a printed circuit broad or PCB.
The passive components are those components which do not have semiconductor material inside them such as resistors, capacitors, inductors, etc. These are called passive components because these components are not able to actively work with electricity or electrons.
On the other hand active components are those components which are internally built using semiconductor material. These components include all types of diodes, transistors, and integrated circuits.
These are called active components because the semiconductor material inside these components are able to actively work with electricity or electrons. For example diodes can rectify an AC, transistor can amplify current and voltage, whereas ICs can do similar tasks which are even more complex.
Some of the best electronic circuit projects you can learn from this website are provided below:
Latest Posts (Learn More)
- Unijunction Transistor (UJT) 2N2646 Datasheet
- IC LM358 Datasheet and Specifications
- Adjustable Voltage Regulator Circuit using LM324 IC with Over Current Protection
- LM35 IC Temperature Controller Circuit with Push Button
- Flashlight Circuit with Long Backup and High Efficiency
Circuit Projects for Beginners and School Students
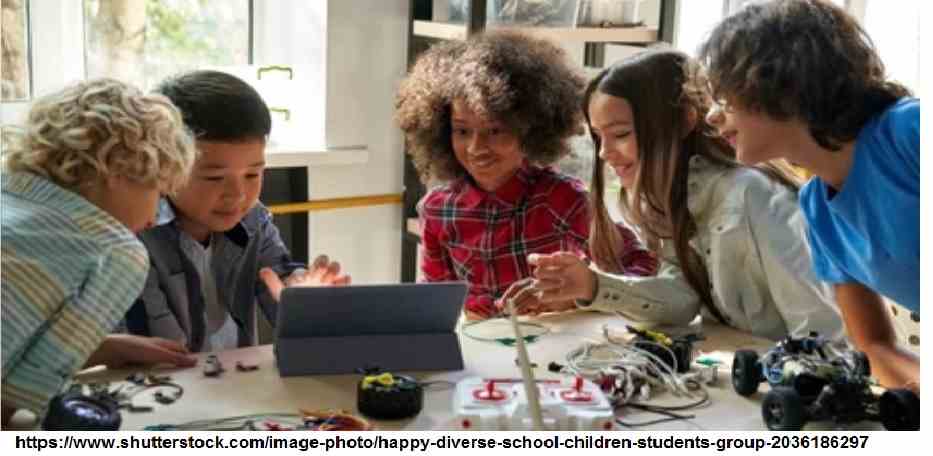
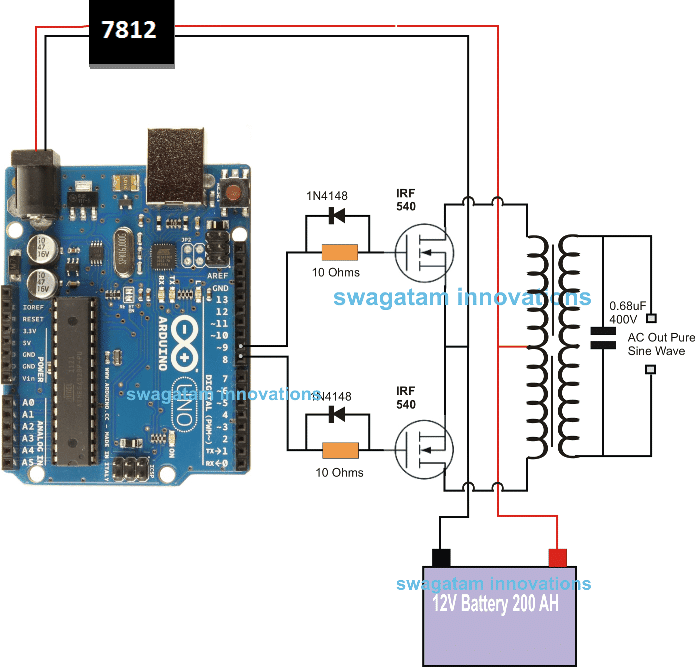
Arduino Pure Sine Wave Inverter Circuit
Learn how to build a pure sine wave inverter circuit using Arduino and very basic coding.
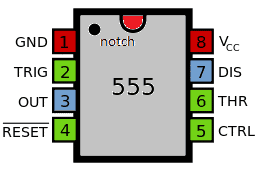
IC 555 Pin Description
Learn how each IC 555 pinout works and understand basic IC 555 oscillator and timer circuits and their calculations.
Disinfecting Home using UVC Rays
Various Electronic Circuit Projects
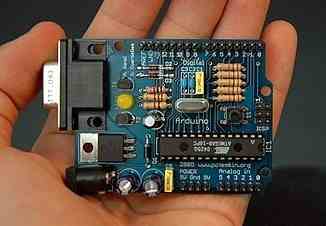
Arduino Programming: Learn Arduino programming from the scratch. Basic Arduino coding tutorial and Arduino projects for all Arduino enthusiasts.
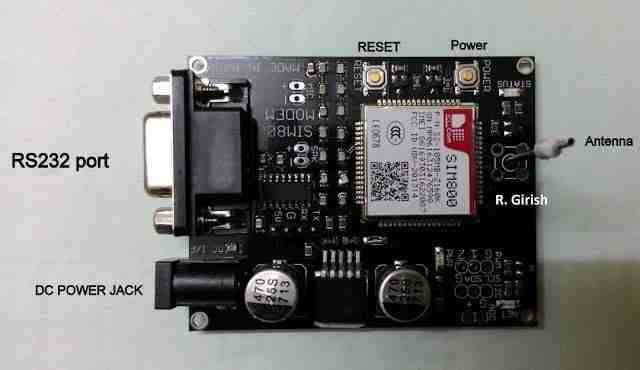
GSM Projects: Best GSM electronic projects for cars, vehicles, and home automation. Learn how to use GSM modules for controlling a desired application.
ARDUINO PROJECTS: It's a system in which the IC can be programmed to implement a set of specified electronic operations. Some very useful microcontroller automation projects with program codes can be found here.
IC 555 CIRCUITS: Easy to build IC 555 based circuits for leisure and fun. This device may look trivial and limited to hobby projects, but the fact is there hasn't been a single substitute for this IC in the past 40 years...
BATTERY CHARGER CIRCUITS: If circuit is the brain, battery is the heart of any gadget. But these devices need controlled charging and discharging. Simple to the most enhanced battery charger projects for home and industry.
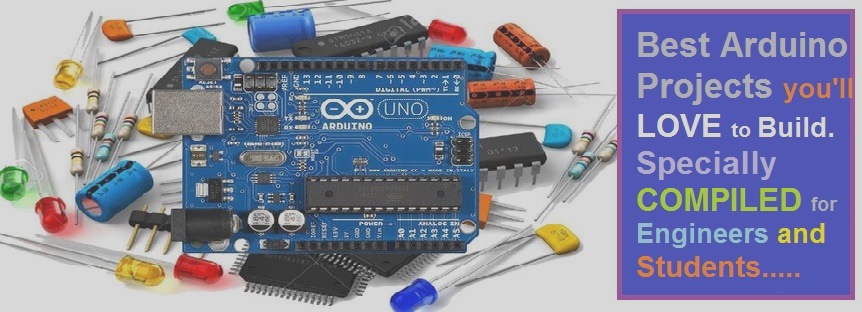
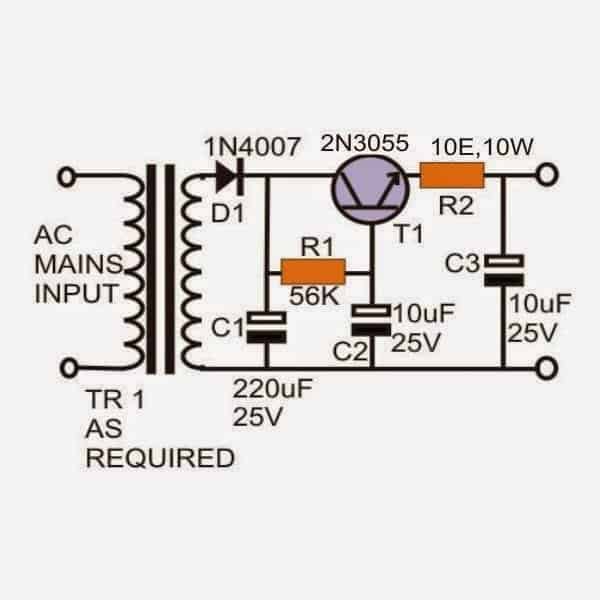
POWER SUPPLY CIRCUITS: Fixed type and variable voltage and current power supply circuits are given here... best circuit projects suited for workbench testing.
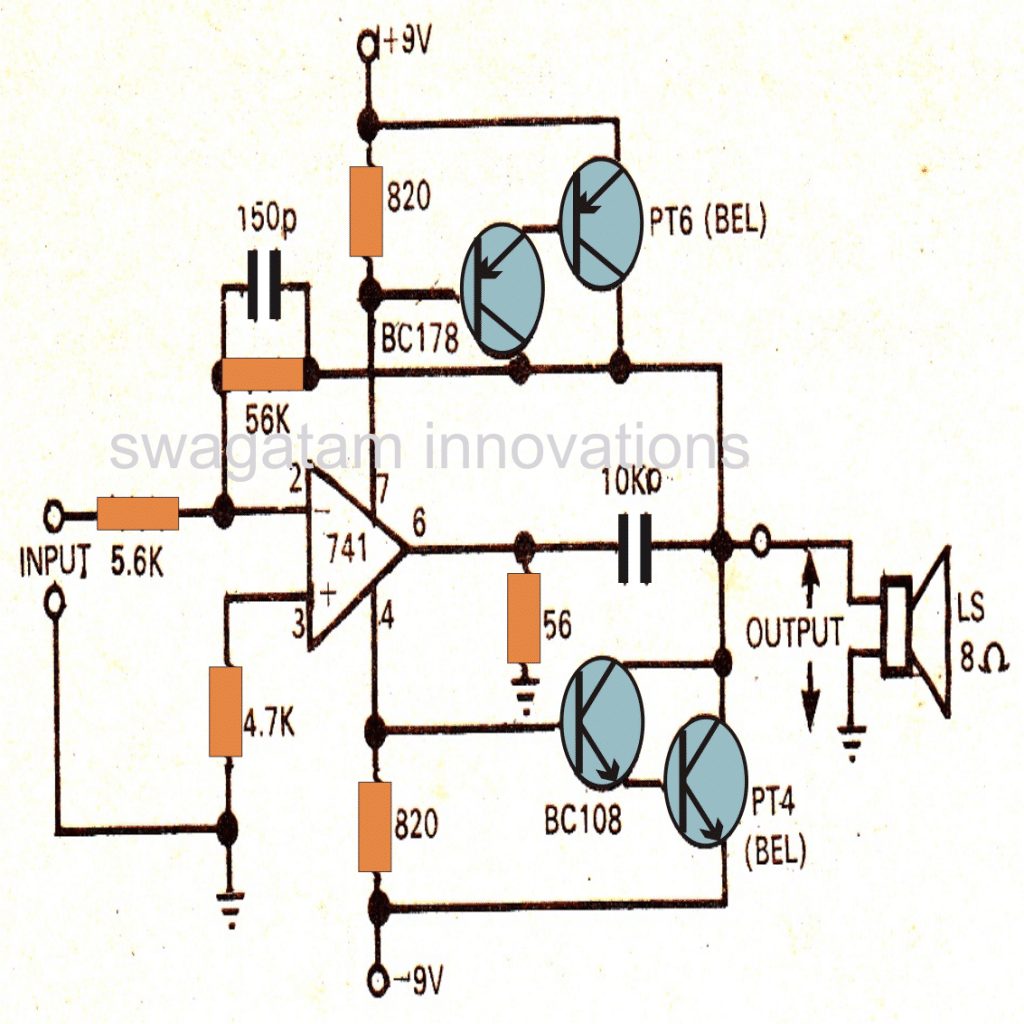
AMPLIFIER PROJECTS: Projects to amplify small music inputs from ipod, cellphone or an SD card to get 100s of watts on loudspeaker. Boom your surrounding with the help of these projects.
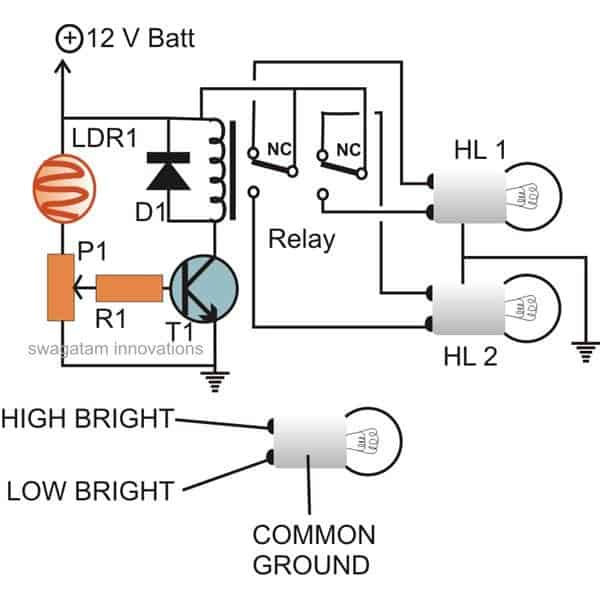
AUTOMOBILE ELECTRONICS: Not satisfied with the default enhancements provided by your car manufacturer? No problems, these handy looking electronic projects can be used for enhancing your vehicles aesthetic looks even further.
STRING LIGHTS: Festive season is near, make these stunning lighting projects for your home and office. String lights, chaser lights, sequential lights, flashing lights, music lights...all under one roof.

LED PROJECTS: Fascinated with the power of LED lights? There's actually a lot more you can do with these simple DIY LED projects explained here.
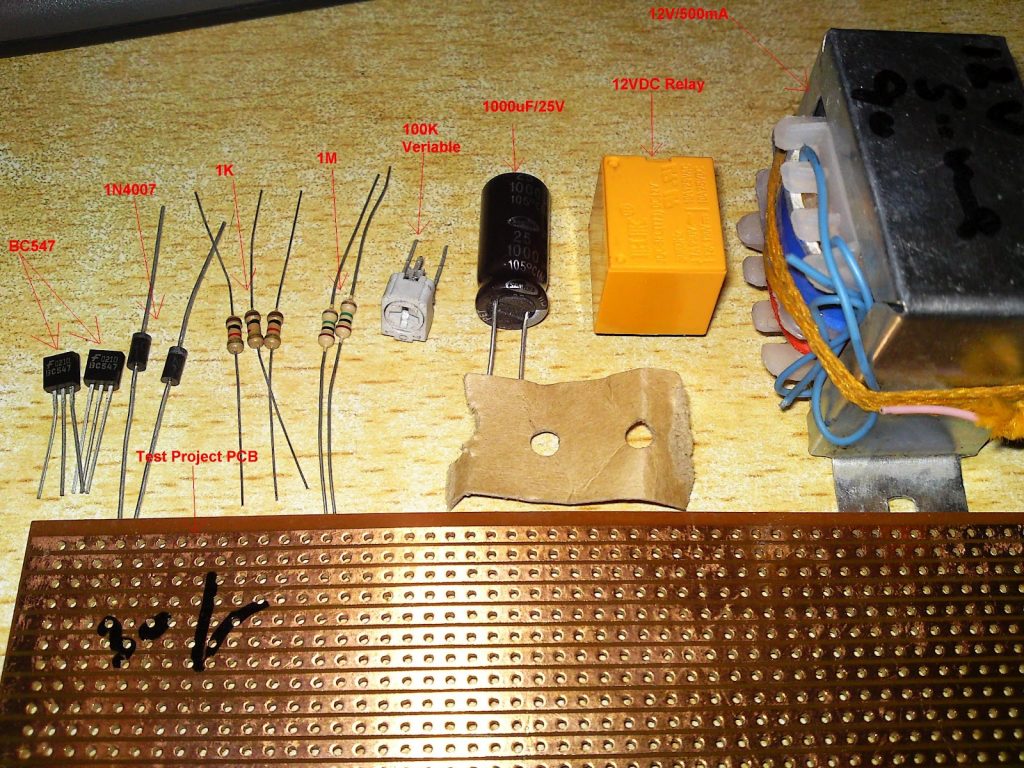
ELECTRONIC PROJECTS: Electronic parts may look simple externally but internally they may be much more complex. Learn everything you wanted to know about these devices.
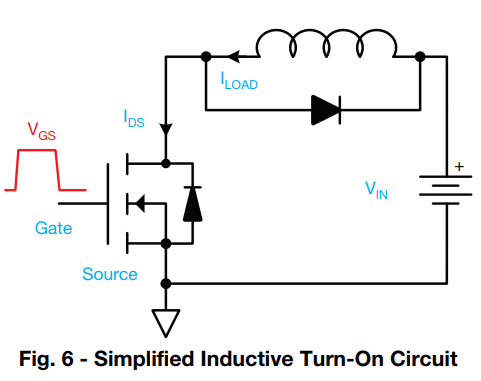
SEMICONDUCTOR THEORIES: Semiconductors are the soul of electronics. Learn their complex working through easy to understand projects.
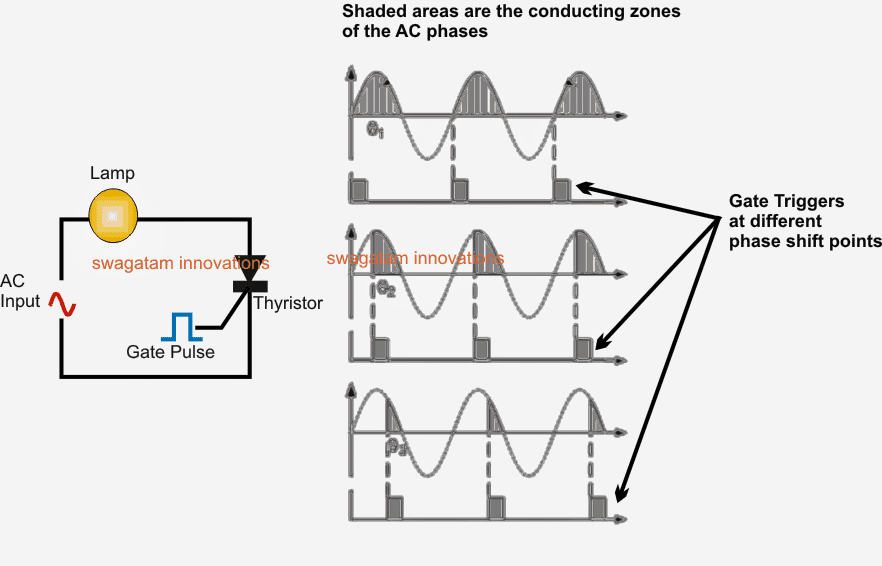
TUTORIALS: Building electronic circuits can be impossible unless you have all the necessary tutorials in hand with you. Here's a great opportunity to learn and gain expertise.
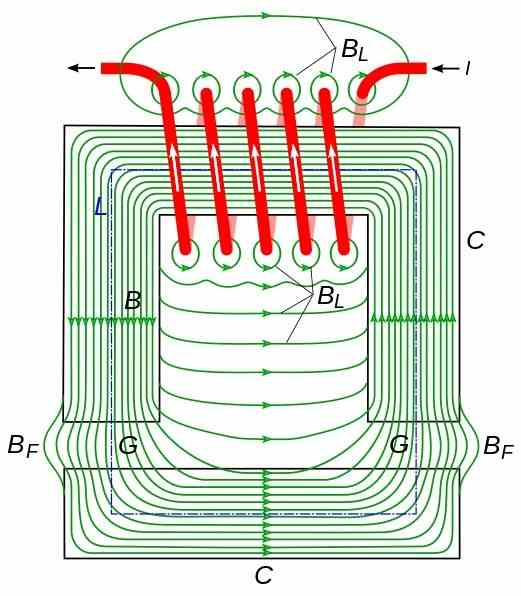
FREE ENERGY CIRCUITS: Free energy projects may look controversial and unrealistic, but a few proven results do make them very intriguing...
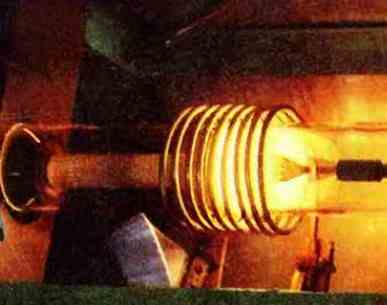
HEATER CONTROL: Heaters demand huge power which require precise control for better efficiency. These projects accomplish the need perfectly.
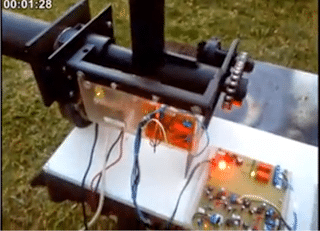
HOME ELECTRICAL: It is actually possible to enhance your home with customized electronics. Electronic projects when integrated with home electrical can do wonders.
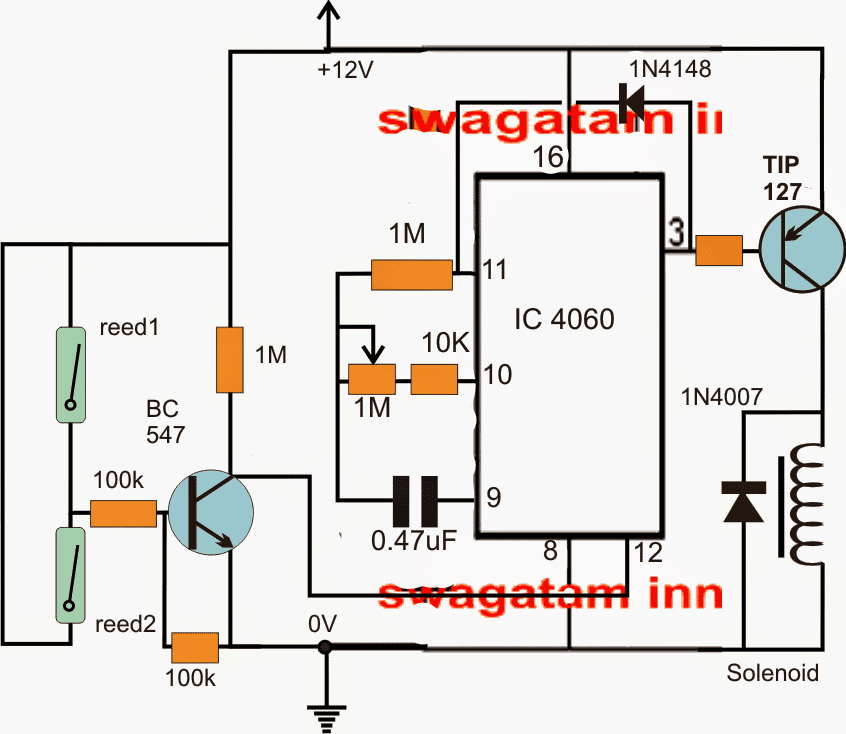
INDUSTRIAL PROJECTS: Today factories and industries are not just about heavy iron machinery, rather these are controlled with precise electronics. More such electronic circuit projects are shortlisted here.
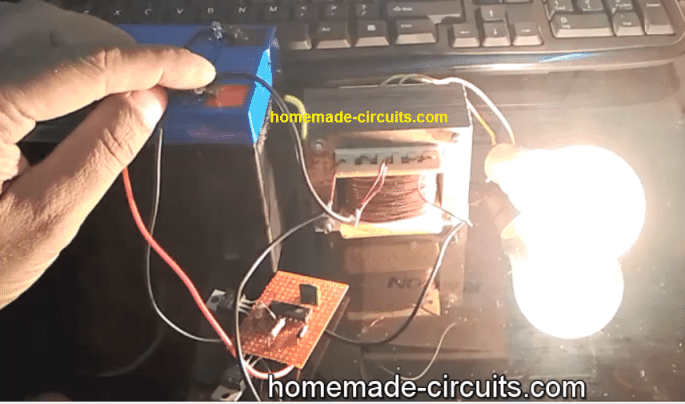
INVERTER CIRCUITS: These projects will convert any high current DC to 220V AC. Learn from the scratch how to build these awesome power generating gadgets.
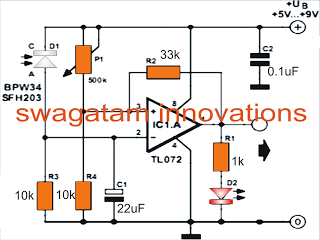
LASER CIRCUITS: Lasers are popularly used for disco lighting but did you know these can be also applied for security applications?
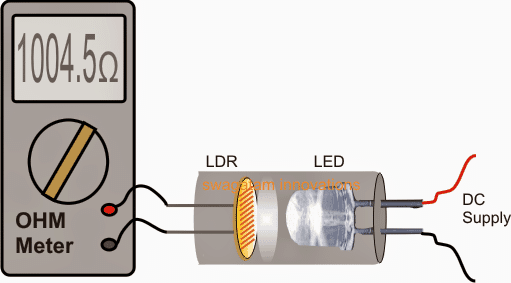
METERS AND TESTERS: Although digital multimeters today is sufficient for most electronic troubleshooting, having a set of hand built testers can make the job even easier...
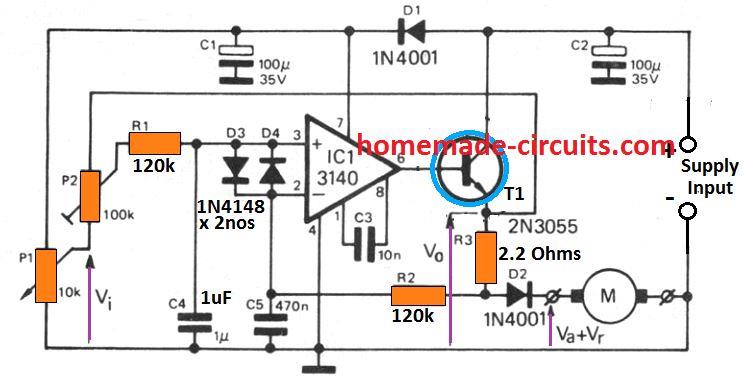
MOTOR CONTROL PROJECTS: Whether for home or industry, motors are indispensable. However, these require to be controlled for accuracy and power saving. More related projects can be found here.
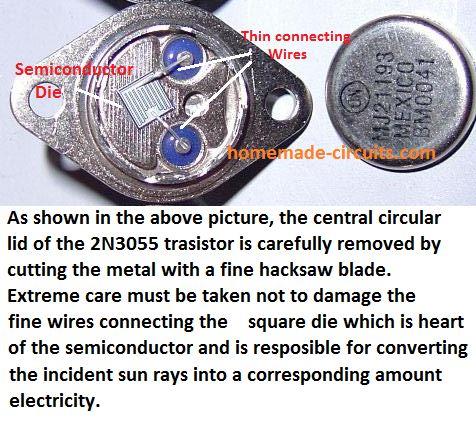
SOLAR CONTROLLERS: Sun generates trillions of mega watts every second. Harnessing this gigantic power house into electricity can be implemented with some simple electronic concepts described here.
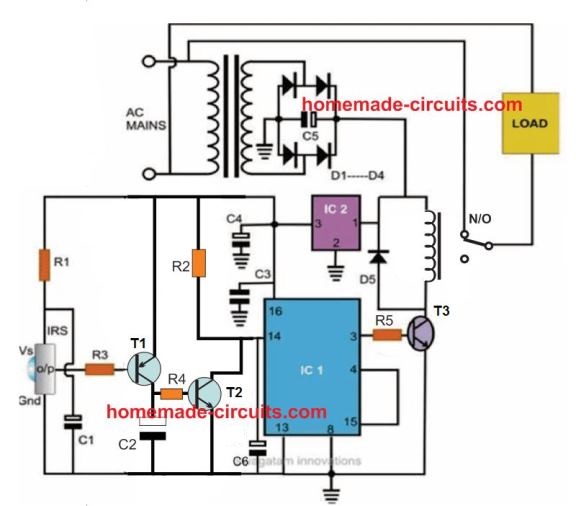
REMOTE CONTROL CIRCUITS: Controlling a device from distance remotely can be a lot of fun, which additionally saves the user's precious time and effort. A few cool projects presented here, are specially designed for the same.
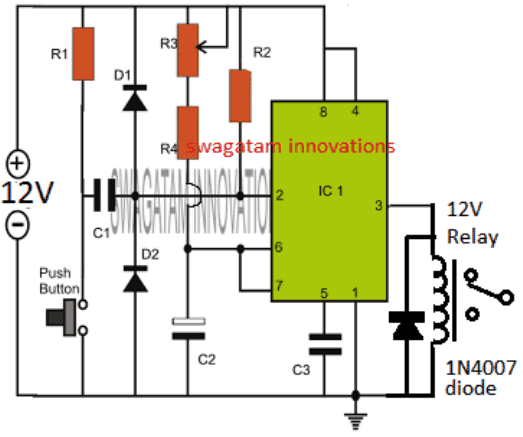
Timer Projects: A small timer which can switch a load ON or OFF after a preset delay can be a very useful device for a specified application. Many such hand-picked delay timer projects can be read here.

Transmitter Circuits: Wireless communication system may sound complex to build, but actually it is the among the easiest projects a hobbyist can possibly try. Communicating remotely through a homemade walkie-Talkie can be extreme fun.
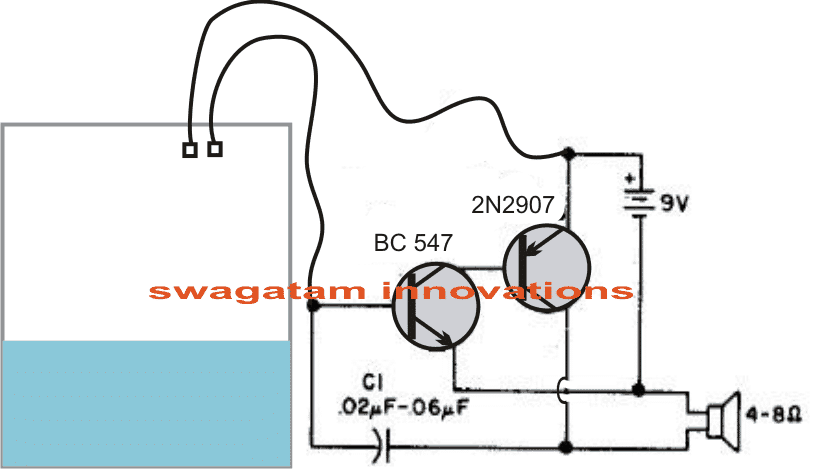
Water Level Controllers: Water is perhaps the most vital element on this planet for all living creatures. Controlling water not only prevents water spillage, it also helps to save this precious resource from getting unnecessarily wasted. Many related electronic projects for this are described here.
All Posts
All posts from this blog can be found in the following links. You can find any desired circuit diagram of your choice and specifications in the following stemap list. After clicking the links you can find the desired posts by pressing Cntrl+F and then typing the specific keyword of the circuit that you are trying to find. If you have any difficulty in finding the right circuit idea of your choice, you can always comment under any one of the relevant articles and I will make sure your query is solved ASAP.
Sitemaps
- https://www.homemade-circuits.com/post-sitemap.xml
- https://www.homemade-circuits.com/post-sitemap2.xml
- https://www.homemade-circuits.com/page-sitemap.xml
Latest Comments
You are welcome Larry!
That's great Neeraj, Now you can attach the LM35 at pin#2 of the opamp and check the results, as per…
Motionless Electromagnetic Generator https://patents.google.com/patent/US6362718B1/en The Motionless Electromagnetic Generator operates in accordance with an extension of Faraday's Law, indicating that an…
Hi Swagatam: Thanks so much for your speedy reply. I truly appreciate it! Larry
Congratulations sir we have made it 🎇 Everything is fine and working super efficiently and I have understood the function…
Have Questions? Please Comment below to Solve your Queries! Comments must be Related to the above Topic!!