In this post I will explain how an effective and efficient, yet very cheap, and stabilized bench power supply can be designed by any electronic hobbyist for safely testing all types electronic projects and prototypes.
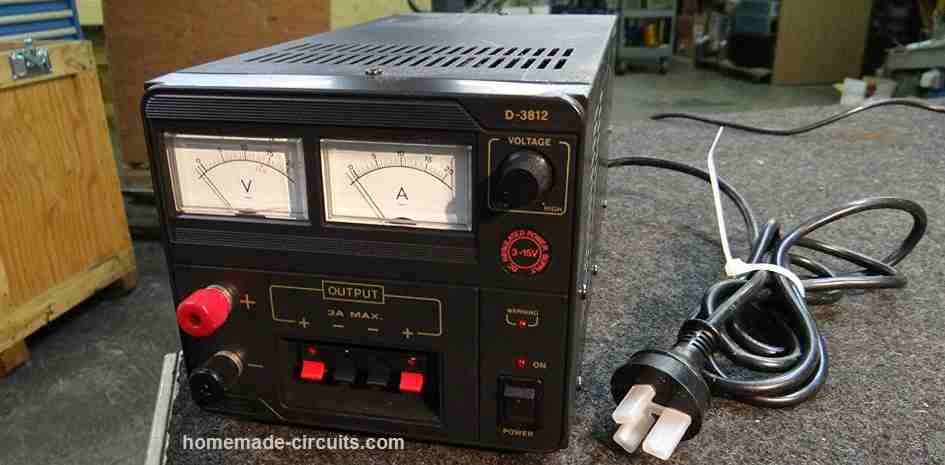
The main features that a bench power supply must have are:
- Should be built with cheap and easily available components
- Should be flexible with its voltage and current ranges, or simply must include the facility of a variable voltage and variable current outputs.
- Should be over-current and over-load protected.
- Should be easily reparable, in case a problem arises.
- Should be reasonably efficient with its power output.
- Should facilitate easily customization as per a desired specification.
General Description
The majority of the power supply designs thus far incorporate a linear series stabilizer. This bench power supply design uses a pass transistor which works like a variable resistor, regulated by a Zener diode.
The series power supply system is the more popular, possibly due to the fact that it is a lot more efficient. Except of some minor loss in the Zener and feed resistor, noticeable loss only happens in the series pass transistor during the period it is supplying current to the load.
However, one disadvantage of the series power supply system is that these do not provide any kind of output load short-circuit.
Meaning, during output fault conditions the pass transistor may allow a large current to flow through it, eventually destroying itself and possibly the connected load also.
That said, adding a short circuit protection to a series pass bench power supply can be quickly implemented through another transistors configured as a current controller stage.
The variable voltage controller is achieved through a simple transistor, potentiometer feedback.
The above two additions enables a series pass power supply to be highly versatile, rugged, cheap, universal, and virtually indestructible.
In the following paragraphs we will briefly learn the designing of the various stages involved in a standard stabilized bench power supply.
Easiest Transistor Voltage Regulator
A quick way of getting an adjustable output voltage is to hook up the base of the pass transistor with a potentiometer and Zener diode as shown in the figure below.
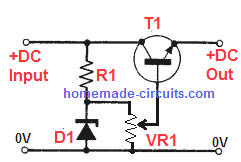
In this circuit the T1 is rigged as an emitter-follower BJT, where its base voltage VB decides its emitter side voltage VE. Both VE and VB will precisely correspond with each other, and will be almost equal, deducting its forward drop.
The forward drop voltage of any BJT is typically 0.7 V, which implies that the emitter side voltage will be:
VE = VB - 0.7
Using a Feedback Loop
Although the above design is easy to build and very cheap, this type of approach doesn't offer great regulation of power at the the lower voltage levels.
This is exactly why a feedback type control is normally employed to get an improved regulation throughout the entire voltage range, as demonstrated in the figure below.
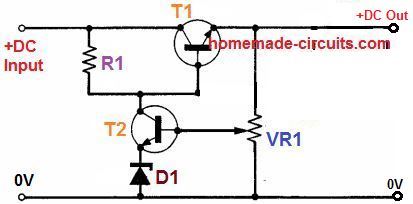
In this configuration, the base voltage of T1, and therefore output voltage, is controlled by the voltage drop across R1, mainly due to the current pulled by T2.
When the slider arm of the pot VR1 is at the ground side extreme end, T2 becomes cut off since now its base becomes grounded, allowing the only only voltage drop across R1 caused by the base current of T1.
In this situation the output voltage at the T1 emitter is going to be almost same as the collector voltage, and can be given as:
VE = Vin - 0.7, here VE is the emitter side voltage of T1, and 0.7 is the standard forward voltage drop value for BJT T1 base/emitter leads.
So if the input supply is 15 V, the output can be expected to be:
VE = 15 - 0.7 = 14.3 V
Now, when the pot VR1 slider arm is moved to the upper positive end, will cause T2 to access the whole emitter side voltage of T1, which will cause T2 to conduct very hard.
This action will directly connect the zener diode D1 with R1. Meaning, now the base voltage VB of the T1 will be simply equal to the zener voltage Vz. So the output will be:
VE = Vz - 0.7
Therefore, if the D1 value is 6 V, the output voltage can be expected to be just:
VE = 6 - 0.7 = 5.3 V, so the zener voltage decides the minimum possible output voltage that could be obtained from this series pass power supply when the pot is rotated at its lowest setting.
Although the above is easy and effective for making a bench power supply, it has a major disadvantage of not being short circuit proof.
That means, if the output terminals of the circuit is accidentally short circuited, or an over load current is applied, the T1 will quickly heat up and burn.
To avoid this situation, this circuit could be a simply upgraded by adding a current control feature as explained in the following section.
Adding Overload Short Circuit Protection
A simple inclusion of T3 and R2 enables the bench power supply circuit design to be 100% short-circuit proof and current controlled. With this design even an intentional shorting at the output will not cause any harm to the T1.
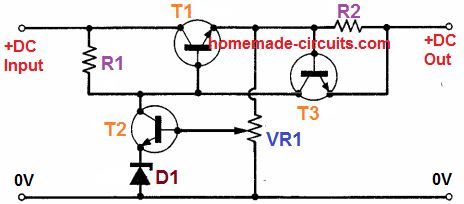
The working of this stage could be understood as follows:
As soon as the output current tends to go beyond the set safe value, a proportional amount of potential difference across R2 is developed, enough to switch ON transistor T3 hard.
With T3 switched ON causes T1 base to be joined with its emitter line, which instantly disables the T1 conduction, and this situation is maintained until the output short or overload is removed.
In this way T1 is safeguarded from any undesired output situation.
Adding a Variable Current Feature
In the above design, the current sensor resistor R2 can be a fixed value if the output is required to be a constant current output.
However, a good bench power supply is supposed to have a variable range for both voltage and current.
Considering this demand, the current limiter could be made adjustable simply by adding a variable resistor with the base of T3, as shown below:
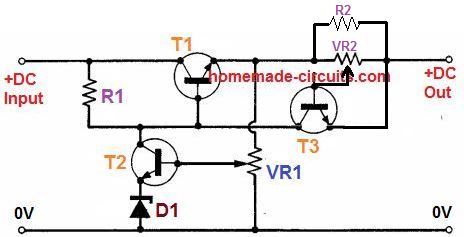
VR2 divides the voltage drop across R2 and thus allows the T3 to switch ON at a specific desired output current.
Calculating the Part Values
Let's start with the resistors, R1 can be calculated with the following formula:
R1 = (Vin - MaxVE)hFE / Output Current
Here, since MaxVE = Vin - 0.7
Therefore, we an simplify the first equation as R1 = 0.7hFE / Output Current
VR1 can be a 10 k pot for voltages up to 60 V
Current limiter R2 can be calculated as given below:
R2 = 0.7 / Max Output Current
Max output current should be selected 5 times lower than T1 maximum Id, if T1 is required to work without an heatsink. With a large heatsink installed on T1, the output current can be 3/4th of T1 Id.
VR2 can be simply a 1k pot or preset.
T1 should be selected as per the output current requirement. T1 Id rating should be 5 times more than the required output current, if it is to be operated without a heatsink.
With a large heatsink installed, the T1 Id rating should be at least 1.33 times more than the required output current.
The maximum collector/emitter or VCE for T1 should be ideally twice the value of the maximum output voltage specification.
The value of zener diode D1 can be selected depending on the lowest or the minimum voltage output requirement from the bench power supply.
The T2 rating will depend on the R1 value. Since the voltage at collector of T2 will be always equal to Vin, the VCE of T2 should be higher than the Vin or the input supply.
The Id of T2 should be such it is able to handle the base current of T1, as determined by the value of R1
The same rules apply for T3 also.
In general T2, and T3 can be any small signal general purpose transistor such as BC547 or maybe a 2N2222.
Practical Design
Having understood all the parameters for designing a customized bench power supply, it's time to implement the data in a practical prototype, as shown below:
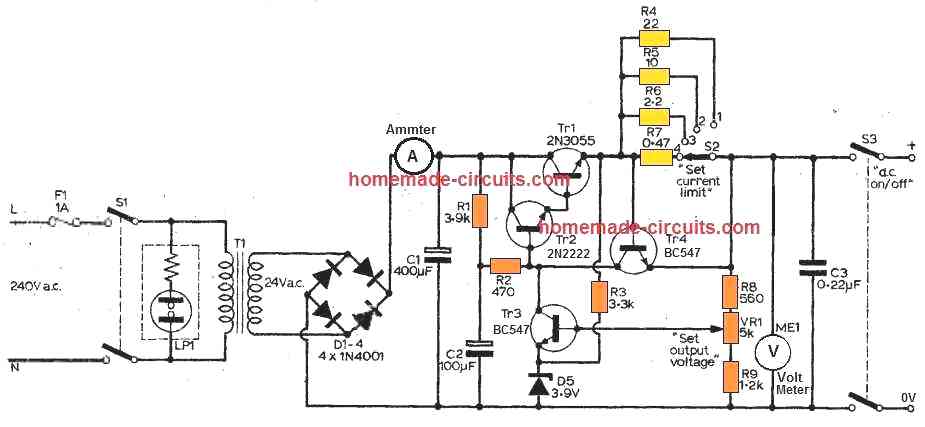
You may find a few additional components introduced in the design, which are simply for enhancing the regulation capability of the circuit.
C2 is introduced to clean any residual ripple at the T1, T2 bases.
The T2 along with T1 forms a Darlington pair to increase the current gain of the output.
R3 is added to improve the zener diode conduction and therefore to ensure better overall regulation.
R8 and R9 are added to enable the output voltage to be regulated across fixed range, which are not critical.
The R7 sets the maximum current that can accessed at the output, which is:
I = 0.7 / 0.47 = 1.5 amps, and this appears quite low compared to the rating of the 2N3055 transistor. Although this might keep the transistor super cool, it may possible to increase this value up to 8 amps if the 2N3055 is mounted over a large heatsink.
Upgrading to 100 V 10 Amp
The above bench power supply circuit can be upgraded to handle upto 100 V 10 amp as shown in the following diagram. Current can be set using the following formula:
R = 0.7 / Max Current
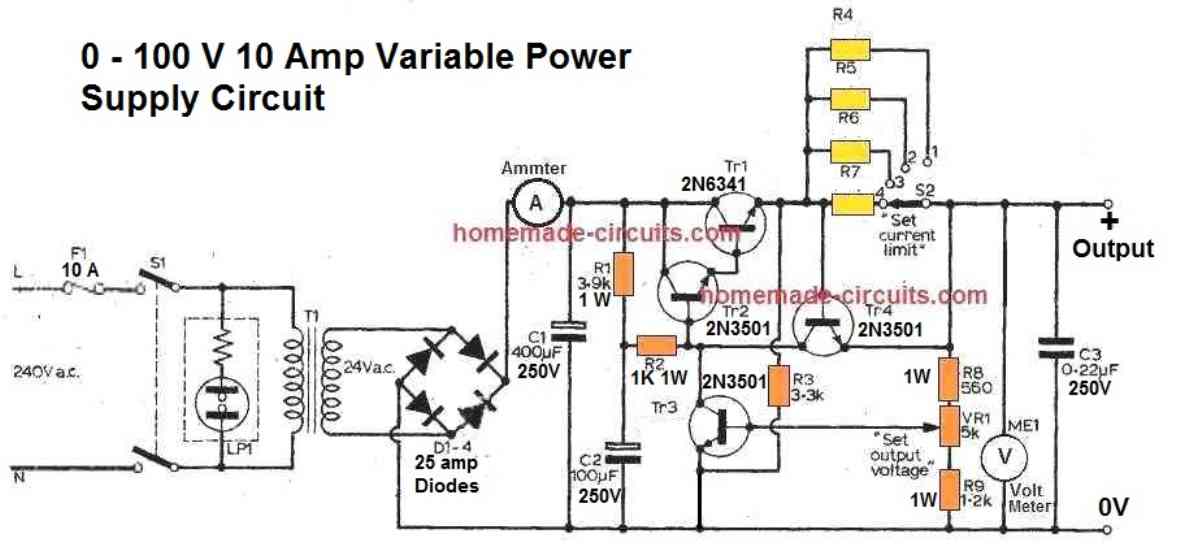
Decreasing Dissipation to Increase Efficiency
The biggest disadvantage with any series transistor based linear regulator is the high amount transistor dissipation. And this happens when the input/output differential is high.
Meaning, when the voltage is adjusted towards lower output voltage, the transistor has to work hard to control the excess voltage, which is then released as heat from the transistor.
For example if the load is a 3.3 V LED, and input supply to the bench power supply is 15 V, then the output voltage has to be lowered to 3.3 V which is 15 - 3.3 = 11.7 V less. And this difference is converted to heat by the transistor, which could mean a efficiency loss of more than 70%.
However, this problem can be simply solved by using a transformer with tapped voltage output winding.
For example the transformer may have taps of 5 V, 7.5 V, 10 V, 12 V, and so on.
Depending on the load the taps could be selected for feeding the regulator circuit. After this, the voltage adjustment pot of the circuit could be used for further adjusting the output level precisely to the desired value.
This technique would increase the efficiency to a very high level, allowing the heatsink to the transistor to be smaller and compact.
Very Simple Bench Power Supply Circuit with Constant Current Output
This benchtop power supply circuit shown below is a simple and inexpensive option for hobbyists, yet is able to provide a continuously adjustable DC output with a constant current.
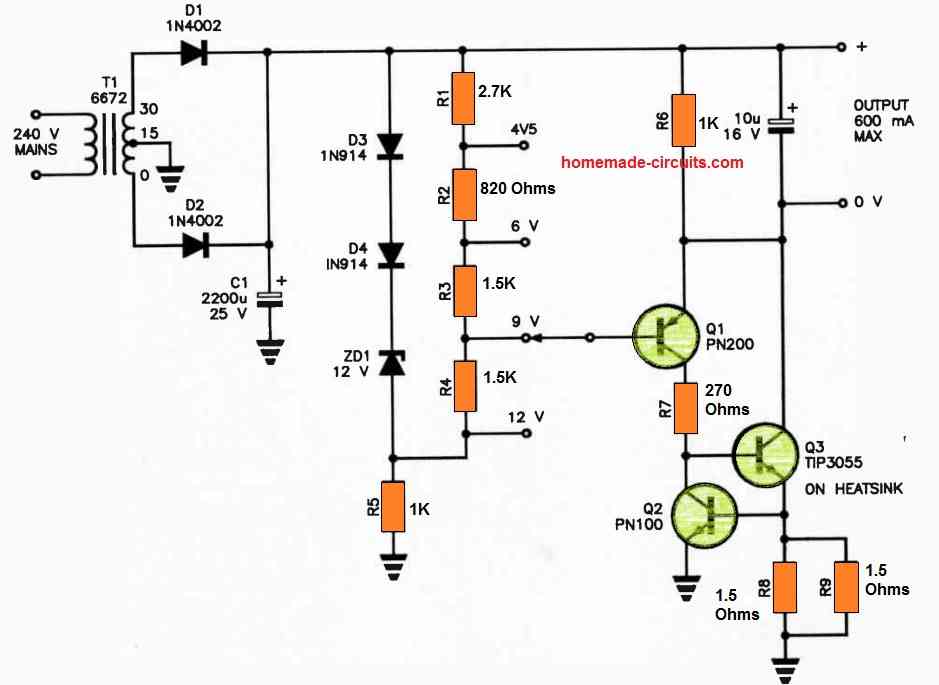
All of the components are readily available at electronics retailers. The simple 15V step down transformer is used which allows it to deliver up to one amp of output current.
A full-wave rectifier converts the AC input voltage to unregulated DC. A zener diode and two other diodes provide a regulated reference voltage for the regulator circuit.
Resistors R1 through R4 are connected to the reference voltage to produce output voltages of 4.5, 6, 9, and 12 volts. Resistor R5 provides bias current for the zener diode.
Three transistors, Q1 and Q3, form a conventional series regulator. A 10uF capacitor across the output terminals helps to reduce the AC impedance of the power supply.
Q2 along with the resistors R8 and R9 constitute the current control circuit stage which enables a constant current output.
Resistors R8 and R9 determine the output current limit, or simply the constant current value.
Op Amp Controlled Precision Bench Power Supply
The working procedure of the opamp controlled bench power supply circuit is fairly basic uncomplicated, since regulated power supplies can be simply as particular forms of feedback amplifier.
In this concept, the R1 and R2 generate a refernce sample signal from the output supply, which is by another reference voltage created by D2.
The resulting correction signal is supplied back through the 741 on the series pass transistor Q1.
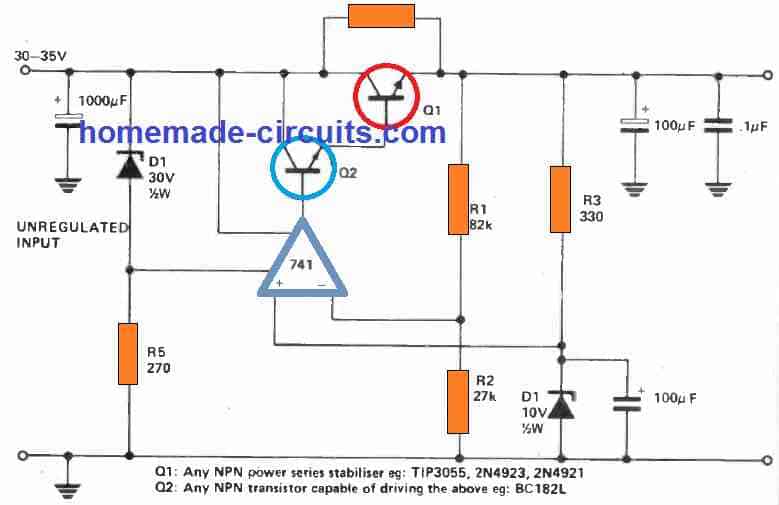
Observe that the circuit stability has been enhanced by providing the reference source R3 -D2 through the stabilized output rather than from the unstabilised input as is usually done inother bench power supplies.
To ensure that the circuit initiates as soon as switched on, a leakage resistance R4 is placed in parallel with the series pass device.
This means that the feedback loop begins to run as soon as power is switched ON.
Absolutely no regulation is sacrificed because of R4, since it is the general output which is sampled by R1 -R2, therefore, the impact of the ripple current moving through R4 gets adjusted through the feedback.
Making the Output Adjustable
The output may well be made adjustable by changing R1-R2 with a potentiometer, however in its existing layout, the circuit can't be forced to regulate under the zener voltage value of D2.
When uninterrupted adjustment of the output voltage is necessary, the reference source R3-D2 should be furnished through the unregulated input, with accompanying minor lack of stability.
The quantity of power the circuit is able to offer will be limited primarily by the current handling capacity of Q1 and the maximum power capacity of the unregulated supply.
More Elaborate Bench Power Supply Circuit
A regulated bench Power supply are normally a useful gadget for any hobbyists or engineer.
Despite the truth that IC based voltage regulators have become very easily accessible, a circuit only employing ordinary discrete components can be appealing.
In order to save power, and to restrict the dissipation across the series regulator, the entire 0-30 V control range is further divided into 3 scaled-down voltage ranges.
All the 3 ranges matches with a suitable secondary supply voltage (determined by the position of S1a) and a proper reference voltage (determined by S1b).
So that you can get a consistent control of the output voltage to a minimum of0 V, a negative auxiliary supply needs to be added.
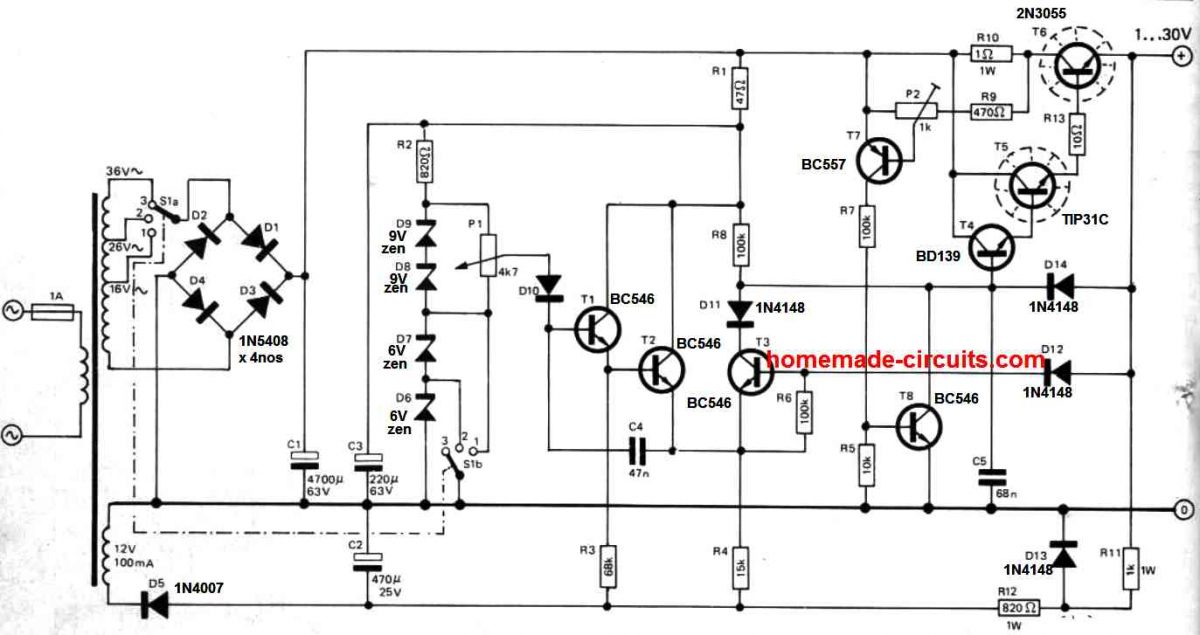
In this bench power supply circuit, this is extracted (by means of D5 and C2) via a different 12 V winding over the mains transformer. A different option could be to incorporate an additional separate mains transformer.
The final results tested on the bench prototype are pretty decent: ±35 V mains voltage swing induced just ±25 mV swing of the output voltage, with full load 1 amp load attached to the output. The A.C. ripples of the output (hum) had been lower than 15 mV.
How it Works
The circuit functions in the following manner.
A reference voltage, extracted through the zener diode(s) D6 -D9 and fixed using pot P1, is directed to the transistor T2 base by means of D10 and TI.
T2 and T3 work like a differential amplifier; wherein the base of T3 receives the output voltage by means of DI2. This differential amplifier's output is applied, through D11, on the base of the combined series regulator made up of transistors T4, T5 and T6.
Although the configuration might look a bit complex, it works like a typical regulator circuit; it maintains the output voltage virtually fixed over an extensive range of output currents.
Transistors T7 and T8 along with connected parts form the current limiter stage. As soon as the voltage over R10 gets to a particular value (as fixed by P2) T7 begins conducting.
This, consequently, causes transistor T8 to get biased and starts conducting; which reduces the base drive to transistor T4, and the situation decreases the output voltage hence the output current continues to be inside the predetermined boundary.
When S1 is selected at position 1, that compares to an output range of 0-10 V, setting at 2 allows 10-20 V and adjusting at position 3 provides an output range of 20-30 V. P1 is used for tweaking the range as fixed by S1.
The highest amount of output current can be established using pot P2. This P2 pot could be either pre-programmed to supply a highest output current of 1 A or employed like a variable output current control.
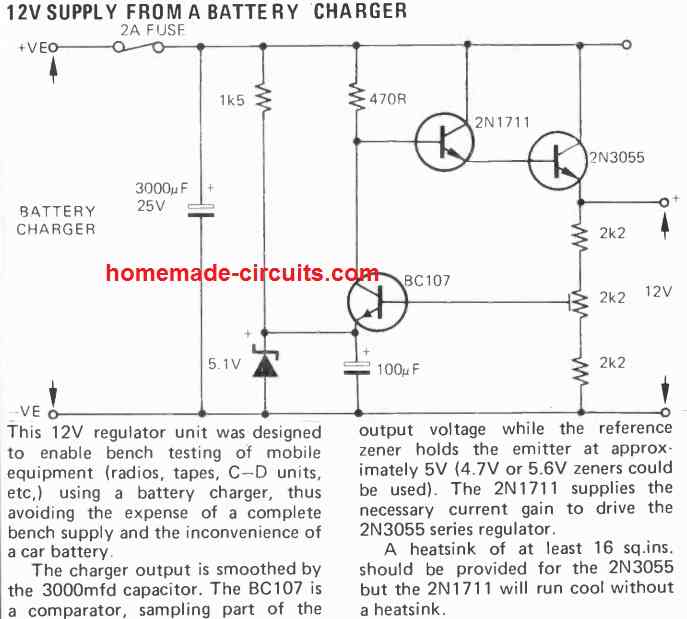
Good day Sir,
Why is the Ammeter on the practical circuit above positioned immediately after rectifier instead of at the out put. So that it is in series with the load.?
Hi NGANG,
The ammeter must be always in series with the load, so yes here the ammeter is in series with the load and also the entire circuit.
It means, in this position the ammeter will not only indicate the load current but also the current consumed by the circuit itself, if any.
hello Mr Swagatam;
My batteries group are : 6 x 12V= 72V and 80 A each.
But I have only the charger with 2,5 A capacity. When I measure the current I read about 6 A
on the multimeter while charging.
This may be harmfull to the charger or no problem?
Hello Suat,
For a 80 Ah lead acid battery, the minimum recommended charging current is 8 amps, so 6 amp will not cause any harm.
I see 6 amp would be not cause any arm. Charger unit is also safe? since it is only 2,5 amp. Thanks
Yes, but a 2.5V charger should not produce 6 amp current.
that was the problem so I had written for your comment then maybe my multimeter is wrong or I used AC current side I will check again
OK no problem…
Hello Mr Swagatam I am Oklama, I have been reading through your work and testing some of your circuits I must say this is good work and thanks for putting it out here for us to see. I have built a LPS before but now I am tasked to build a SMPS, I have a multi output transformer which will be connected to the outlet, it has a maximum current output of 1A and maximum output voltage of 18V AC. my power supply is suppose to have a back up battery which should be charging when the main power supply is on. it is a 12V rechargeable lithium battery, I need at least 4 output voltages some of which have to be negative, if you do not mind sir could you please provide me with the list of components with specifications together with a possible circuitry I can get in order to accomplish this task. I would really appreciate your response if you need more information about this please let me know. Thanks a lot Sir.
Hello Oklama, I appreciate your question, and I really wish I could help you, however I am sorry, I don’t think the specific SMPS that that you have asked is available with me. Therefore I am unable to solve your requirement. Moreover a readymade transformer cannot be used for an SMPS, the transformer has to be specifically calculated and designed for an SMPS circuit.
i have bench psu 30volt 10 ampere but when connecting it to 220v source, the output is above 40volt.. how to find the wrong circuit?
on the pcb shown 2 relay, op amp ic lm324 driven by lm7818 but only 11volt out to opamp ic. i show lm723, then transistor a940, but the two final transistor is not shown the code.. i think it 2 noss 2n3055.
would you like to share how this circuit problem, it will help if it get the schematic diagram for troubleshooting.
thanks
Are to able to adjust the power supply output from 3 V to 40 V? If yes then your power supply is working good.
In that case please check the voltage input after the bridge rectifier or across the input filter capacitor. The bridge rectifier and the filter capacitor could be increasing the output voltage to 40 V.
no… those potensiometer not working both of voltage adjustemnt and also current limiter not work..
Then I think the IC has gone faulty.
which one ic has fault, opamp lm324 or lm723.. ?
I cannot judge that because I cannot check your circuit practically…so it is difficult to troubleshoot for me.
ok friend.. i will tear down it step by step tonight, checking in out voltage, and also final transistor… may be i have to learn how that circuit working first. before replacing final transistor.. i dont want to make it blown…
but.. how to determind voltage and limitiler circuit working without final transistor
Yes hilman, you will have to first learn how your circuit works only then you will be able to troubleshoot the fault. I cannot suggest much because I cannot check your circuit physically.
ok thanks sir… thanks for answer.
ok sir thank u ur gud suggestions
No problem Sreenivasulu.
sir transsister 2n3501and 2n3055 both are same or not
No, they are not same, 2N3501 is just a 300 mA BJT whereas 2N3055 is 15 amp.
sir transformer primary side LP1 means mov protection or ptc
LP1 is a neon bulb, it is not required, you can ignore it.
HI!!! how to add remote sensing to LM317?
Can you please elaborate, I did not understand what you meant by adding remote sensing to LM317?
Hi Swagatam;
I have used C1 as 470 uF and D5 as 2V4 zener and 500 Ohm pot instead of the R9. My transformer seconder is 24 V too.
The minimum voltage of my circuit is about 1 volt. This value is normal or less than the expectation since we use 2V4 zener diode?
Best Wishes
Thank you for the update Suat,
That looks good, Glad the circuit is finally working fine for you.
Hi Swagatam;
Ref. to above “practical design” circuit. I have got 2 transformers as the input of the circuit. One is mine which has 24 volts AC output and other one is 12 volts DC output. My circuit works well if input is from the DC 12 volts transformer. However whenever I use my own transformer then i see sudden burnt of the TR3. Meanwhile i used kbu4 type brdige rectifier and 470 uF filter capacitor with my own transformer and i measure its output voltage is DC 33 volts when plugged.
I should also give the information that i used 1000 uF instead of C1. Please share your opinion about the siuation if possible.
Best Wishes.
Hi Suat,
which transistor did you use for TR3? Try a 60 V or 100V transistor, it will never burn. You can try BC546, it is a 60 V transistor but it can handle only 100 mA. If that doesn’t work, you can try a BC639 which is a 100V, 1 amp transistor.
Thanks for the explanation Swagatam. This time i have used the 4 pcs of 1n5408 diodes instead of the instant bridge rectifier type(gbu4) and removed the filter capatitor at the transformer side since there was already at the circuit as the C1. Then now the circuit works well when 24 volts applied. But i can not explain the former faulty. Thanks anyway one more time.
That’s great Suat, Glad it is solved now. However if you use BC546 for TR3 that would be much safer and reliable.
Hi Swagatam;
I know that the above circuit is tested and works good. But I have used 1000 uF instead of C1 and zener 2v4 instead of 3v9. And no current limitation resistor is used on my circuit.
My test input voltage is 12 Volts DC but i see max 6,5 Volts and min 6 volts at the output. I mean 5 k pot is able to drop the voltage no more than 0,5 volts. It seems all the parts are not defective but there is nearly fix voltage about 6 and 6,5 volts at the output.
It is possible to say some critics or if there is any check points values where i can control.
Regards
Hi Suat,
The TR3 is responsible for the variable voltage output. Try the following.
Ground the base of TR3 and check the output, it should give full output voltage.
Alternatively you can disconnect the collector of TR3 from the base of TR2 and check for the same results.
Also you can remove R9 and replace it with jumper to ground. This will allow complete switch OFF of TR3 when VR1 is rotated towards ground, and to get full output voltage.
If the above procedures does not produce full output voltage would indicate a faulty TR2 or TR3, or incorrect pin connections.
Thanks a lot Swagatam.
The result :
Grounding the base of TR3 is not responding. But disconnecting the collector of TR3 is responding and voltage raises to about 11 volts.
OK, that means your TR3 is faulty, try another transistor, preferably a BC547, and check the response.
as you mentioned TR3 was faulty and now changed. However its pins value thru multimeter : base-collecter is 665 (i think that is normal) but base-collector beeps and value is 047 like short contact.
The result is:
Voltage reaches up the maxiumum 11 volts but now VR1 is not responding namely out is always 11 volts.
In that case it indicates a faulty TR3 again. Base to collector, and base to emitter must show almost the same value when checked with the diode range of the multimeter.
amendment to my previous message it should be base-emitter is short contact, i am sorry
Hi Swagatam;
I have received 2N2222A and its body material is black plastic not metal. When i measure the value between the legs thru multimeter diode level, no doubt mid leg is base(pin2). And the value between pin 2 and pin 3 is always grater than the value between pin 1 and pin 2 is. So to my opinion pin 3 should be the emitter leg. However, most 2N2222 datasheet shows contrarily pin 1 is emitter (at the pictures web site). I need your support since i am confused on the matter.
Best wishes
Hi Suat,
What datasheet is showing is correct. You can refer to the following datasheet:
https://www.onsemi.com/pdf/datasheet/p2n2222a-d.pdf
Hi Swagatam;
Ref. to above practical design; please advise if possible to protect the 2N3055 in the circuit for instant by adding any part like diode?
Best Wishes
p.s: i will use 2 parallel 2N3055
Hi Suat,
you can connect a reverse 1N4007 diode across the emitter/collector of the 2N3055, but actually it is not required as the utilization of this diode for the protection can be negligible.
Over current protection is the crucial protection which is already added in the design.
Hi Swagatam;
At the pcb and soldering progress i made some mistakes and all 2n3055 in my hand were defective. At the moment I have decided to use either tip31 or bd135 or may be bd139 instead of 2n2222 and also I may use tip3055 instead of 2n3055. However before starting the process i need your comment.
Regards
That is perfectly fine, Suat,
All the best to you!
Hi Swagatam;
Please do not consider my previous message since i have realized the ecxess solder at the 5 k pot legs that causes short contact and so limits the output voltage.
Regards
Thank you Suat, for updating the information. I am glad you could troubleshoot the issue quickly.
Hi Swagatam;
I have used 2v zener diode (D5) and 1K pot (R9 for fine adjustment) and 2200 uF at the output side instead of C1 and temporarily double parallel 3A diode (location Switch 2) instead of 6A diode.
I have also double entrance one is for transformer and other is for any DC adapter input.
Circuit is in perfect condition for me. But at the moment minumum voltage is about 3 Volts. Please advise how it may be diminished about 1,5 Volt.
Regards
That’s great Suat!
To decrease the minimum voltage level, you can replace the D5 zener with a 1N4148 diode. The cathode side will be towards ground and the anode towards the emitter of the transistor.
Hi Swagatam;
I think the entrance / filter C1 capacitor with the value 400 uF is the minimal value. So for instant it is possible to use 6800 uF 63 V capacitor instead of it is better or not?
Best Wishes
Hi Suat,
Yes that’s correct. However I think the present C1 position can cause the input DC to increase to its peak value and cause more stress and heat in the TR1 transistor.
My idea is to shift the C1 at the output side after a diode. This will allow the load to get the required filtered DC, and will simultaneously allow minimum stress on the TR1 transistor which will now only have to handle the average 100 Hz ripple from the bridge and the not the full continuous peak voltage.
I am indebted for your all kind supports so far.
So, what i understand is :
remove the c1 but c3 will remain. Place the flyback diode plus 6800 uF capacitor at the area where s3 switch is located.
You are most welcome Suat.
C1 can be removed and C3 can be replaced with a 6800uF capacitor. Just make sure to add a 6A4 diode just after S2
Hi Swagatam;
My transformer is 4 amps and I used double 2n3035 parallel connected and tip3055 instead of 2n2222 so i think i should change the 1n4001 diodes to the 4 amps diodes capacity / bridge rectifier.
And also my question is that if i change the transformer then to what extent my circuit can be of the maximum output current capacity?
Best wishes
Hi Suat,
For 4 amp transformer the bridge rectifier must be at least 6 amp rated so you must use 6A4 diodes.
With two 2N3055 transistors, the maximum current from the transformer must not exceed 8 amps, and the 2N3055 must be mounted on large heatsinks.
Hi Swagatam;
Re. to above practical design circuit. I think it is possible to place ammeter at the (-) negative output side of the circuit, (instead of sw4) since i will use digital display?
Regards.
Hi Suat,
Preferably an ammeter must be connected in series with the positive supply, so i would recommend connecting it at the positive line, you can eliminate the S3 switch, it is not required, or you can connect the ammeter after the S3 switch on the positive line.
Hi Swagatam;
Re. to above practical design of the bench power.
I need to test my prototype circuit before soldering the parts. And as a test purpose i would like to apply dc 12 volt as an input power so i think i should remove the 400uF capacitor while testing since the input will be dc and filtered. I need your confirmation.
My other question is that the bench picture shows that it has only one switch but on the the circuits there is also s3 switch at the output so i am confused.
Best Regards
Hi Suat,
With a DC input the 400uF capacitor can be removed or can be included as it is, it does not matter. In fact if you keep it connected it will enable further filtration of the input DC.
The switch S3, S4 are unnecessary so these were not considered in prototype.
Thanks for the reply Swagatam;
The test result after the input as 12 volt DC.
At the beginning minumum voltage was 4 volts (by trimming the 5K to min position) and max. voltage was about 7 volts.(by trimming the 5K to max position)
And then i changed the 3.9V zener diode with the 2.4V and this time min. voltage was about 3,4 Volts.
So please, advise if the above results are all right? (Then i can proceed).
Best Wishes
Hi Suat,
The results looks correct to me. You can remove R9 completely and directly connect the VR1 lower end with ground, this will allow you to get around 11V max at the output.
Hello again swagatam, I’m working on a low current bench power supply based on your practical design using mains power supply instead of a transformer.
I’m using a 10k resistor for R1, and a 50k to ground to reduce the voltage to ~140 volts.
I have a 12v Zener diode for D5.
Tr2, Tr3 and Tr4 are 2sc3855.
Tr1 is a 2sc5200.
Could you help me calculate the proper values and ratings for R2, R3, R8, R9 and VR1?
Hello Alastair,
Calculating the resistive parameters can be bit difficult and confusing, so i would recommend solving it with some trial and error, since the values are not very critical.
R2 can be a 4.7K 2 watt initially. This high value should work since the transistors are Darlington with very high gain.
R3 can be 10K 1 watt
R8 can be 1K 2 watt
R9 is not required and may be removed.
If any of them heats up, then you can upgrade them with a slightly higher value substitute
Okay thank you for all of the help ???????? I’m starting to understand things a bit better in comparison to when I first contacted you.
Is there any benefit to adding a low value resistor say 8 or 16 ohm on the collector of tr1/tr2?
And could vr1/r9 be replaced with dual potentiometers? Similar to this design http://www.h4ck.de/content/CFPoti/dICF_Schematic.png
1k for r8
500k for vr1
And a 50k dual gang potentiometer for fine adjustment
You already have a 10K resistor in series with the input supply, so adding a low value resistor will not make any difference.
Do you want to use 500K for VR1 that looks too high. A 5K would be sufficient.
I could not understand your diagram, because I cannot see any potentiometer symbol in it, and I also cannot understand why a dual ganged pot would be required. For fine adjustment you can probably replace R9 with a 1K pot.
In the diagram I provided r1/r2 would be half of the 50k dual potentiometer. While r3/r4 would be the 500k. What this does is it allows for a perfectly linear 10% adjustment.
Scroll down to the extended coarse/fine with dual gear for a better explanation of what I’m trying to do.
http://www.h4ck.de/content/CFPoti/CFPoti.html
500k/50k is what I have readily available. If they’re too big I’ll have to go and get some new ones later today. But ideally the dual pot would be 1/10th of vr1.
OK, thank you. However, I have never practically used a dual gear potentiometer so I am not so well versed with its functioning.
If you think it will work for you, you can definitely try it and let use know how it works.
No problem ! I believe this design should work so I’ll let you know how it goes. Last few questions.
Could tr1/tr2 be replaced with a mosfet like an irfp260?
And what should the voltage ratings of tr3/tr4 be for mains input?
Yes a MOSFET can be used in place of TR1, in that case TR2 won’t be required and the circuit configuration will change significantly. TR4 can be a BC547 transistor, no problem with that. TR3 might not be required at all.
You can refer to the following article which closely matches the application which you are trying to implement.
https://www.homemade-circuits.com/0-300v-variable-voltage-current/
Just to make sure I understand correctly. This negative feedback method of voltage control can be implemented using a mosfet correct?
So if I kept tr3 the potentiometer would be connected the same as this diagram?
And would I need two Zener diodes? One from gate to source like the 0-300v diagram. As well as d5 to limit the minimum output voltage?
Yes, what you saying is correct, however the earlier link which I provided is a much easier option and will do the same function.
Ive tried to replicate the diagram in the link provided, but have run into issues. When the circuit does work, it doesn’t provide enough current to even turn on the limiting. So I’m hoping that the feedback based method will work better for what I’m trying to do. My load resistance varies wildly since I’m trying to use this supply for titanium anodizing.
I’d rather use a single mosfet instead of a Darlington pair if possible but it seems like it’s turning on too slowly or I’m just not understanding how it works still. I tried increasing the size of the gate resistor, but it seems that just leads to blowing potentiometers.
In the video I uploaded in the previous linked article shows the circuit powering a 100 watt bulb, so high current output is definitely possible.
MOSFETs are never Darlington, that is why I suggested to eliminate TR2.
The above bench power supply circuit is not designed for a 140V supply and MOSFET, so I am not sure about the consequences.
I would recommend the previous MOSFET based power supply circuit in the other article which has been tested by me using a 220V 100 watt bulb.
Hi Swagatam;
Re. to the bench power station.
My transformer has a current capacity with 4 amps. In case I would use it to charge an accumulator 100 amps then it should be that power station will use its whole capacity of 4 amps. So, it is a risk of overload to station? or no problem? Or it is safer to limit the voltage for instant 3,5 amps for such situation?
Best Wishes
Hi Suat,
It solely depends on the rating of the main pass transistor of the power supply, if it is rated to handle upto 10 amps or 15 amps then 4 amp is absolutely no problem.
Hi Swagatam;
Regarding current adjustment section of the above bench power supply”, we see the resistors R4, R5, R6 and R7 there.
Please advise if it is possible to use individual single variable pot resistor with the value like 1K or 5K (for output current as between 0 and 5 Amps) instead of R4, R5, R6 and R7 and if it is possible so then which amendment at the other sections should be made at the circuit?
Best Wishes
Hi Suat,
The current limiting resistors R4, R5, R6, R7 are supposed to be high wattage resistors of around 5 watt each. If you can arrange for an equivalent pot with this wattage range then you can use this single variable pot resistor instead of these fixed resistors. No other changes would be required in the circuit.
Hi Swgatam;
Ref. to bench power supply;
There are 2 pcs of 2N3055 and one pc of tip3055 in my stock. I would like to place 2 pcs of 2N3055 in parallel connected instead of one 2N3055 and also place the tip3055 instead of 2N2222 since I do not have any 2N2222 in my stock. So please advise if it works?
Best Wishes
Hi Suat,
Yes, you can proceed with the mentioned modifications. Just make sure to mount the two parallel 2N3055 over a common heatsink and close to each other, so that both can share their heat dissipation and both can conduct uniformly.
Hi Swagatam;
How we would be able to transform / convert the above bench power supply to only variable voltage output but not variable current. In other word voltage remain variable and current is not variable but fixed.
If possible please issue a circuit picture to the page.
Best Wishes
Hi Suat,
You just have to remove R4, R5, R6, and use R7 for the fixed current limit.
Hi Swagatam;
On the above circuit as Bench Power. Please I need your comment for the belows;
1- Tr1 2N3055 is NPN type but we see positive voltage at its collector? Also input voltage is not at the emitter side but at the collector side it does any matter?
2- If there would be any differences when we use second 2N3055 in parallel with the Tr1 2N3055 (to increase the current gain)
3- If there would be any differences when we use another 2N3055 instead of Tr2 2N2222. (to increase the current gain)
4- What value R7 should has for the 5 Amp. output capacity? (I = 0,7 / X = 5 and R7 = 0,14 Ohm is true approach?)
Best Wishes
Hi Suat,
For NPN transistor, the positive input is always on the collector side, and the emitter is towards the ground side. Here the emitter of the 2N3055 is linked to ground through the load so that the 2N3055 can work like an emitter follower. For a PNP transistor the positive input is towards the emitter.
If you want to add a parallel 2N3055 then the 2N2222 should be replaced with a high gain transistor such as TIP122, and make sure to mount both the 2N3055 over a common single heatsink close to each other.
Replacing the 2N2222 with a 2N3055 would be wasting an extra 2N3055, because the driving transistor can be a smaller transistor like 2N2222, and this driving transistor must have a high gain, so using a 2N3055 in place of the 2N2222 is not recommended. Instead you can use a TIP122.
R7 = 0.14 ohms is correct, and this should be 0.7 x 5 = 3.5 watts or 5 watts
Hi Swagatam;
Thanks for the kind reply.
I am sorry since I have misled you about the transistor base and collector voltage relation.
To my understanding:
As a principle; transistors have the opposite voltage at its bases and collectors.
If base is negative (PNP type) then collector is positive, if base is positive (NPN type) then collector is negative.
As to the above “Bench Type Power Supply Circuit” and the point makes me confused is:
Although 2N3055 is NPN type, I see positive voltage either at the collector or at the base side. I mean why not collector is negative but positive since base is positive?
Best Wishes.
Hi Suat,
For a NPN transistor, the positive supply is always fed from the collector side, and the emitter is tied with the ground or the negative supply.
For NPN transistor small positive supply is required to pass from the base to the emitter so that the high current positive from the collector can flow towards the emitter.
In PNP the positive supply is required to pass from the emitter to the base so that positive supply from the emitter is able to flow to the collector which is the negative.
Please let me ask a final question; as far as I know.2N3055 is NPN type. then it is possible to use not NPN but PNP type Transistor instead of Tr 2N3055 here on the Bench Power Supply?
Regards
No, PNP cannot work in this set up because the polarity of the transistor would change and the PNP would never conduct, in fact it could get damaged.
Sr. what changes can I do to get 12 or 20Amps output?
Above 5 amps is not recommended for this design because the pass transistor can get immensely hot and burn.
It is possible to add more transistors in parallel but that can make the circuit hugely bulky and difficult to manage.
Thank you for your response. I wonder if I would find a diagram at lest 10Amps 40V. I have seen some posted but not tested.
For handling 10 amps you can replace the 2N3055 transistor with TIP35, with a large heatsink on it.
Perfect, thank you
Hello sir please suggest another simple variable power supply circuit that can use 12v DC as the input , that can produce 15v and more at the output.
Yougking, No power supply will boost 12V to 14V. You will need a boost converter for this. You can try a 0-12V transformer, and rectify its 12V AC to 15V Dc using bridge rectifier and a filter capacitor
Hello sir, since I will be needing someth ing 15v at the output the zener diode will be around 15v. So what do you sugge st on that.
For 15V output, the input has to be 16V. The zener can be used to set anything below 15V.
Could you please simplify the following equation and explain how you get to the value of 3.9k as used in the “Practical Design” circuit.
R1 = (Vin – MaxVE)hFE / Output Current
I have built the circuit and it works really well, my transformer outputs a larger voltage and the end result is around 28vdc at the output using the values given, also is it viable to replace R7 with just a wire giving maximum output ? or will that give me problems.
Thank you for your time.
The formula was actually is created by me. I tried a lot to find the formula for the emitter load from other online sources but I couldn’t get any, so I decided to deduce it myself.
I derived this formula from another formula which provides the base resistor value for the collector current. Here’s that formula:
R = (Supply Input Voltage – Transistor base/emitter forward voltage)hFE / Collector current.
If we assume the above formula works for emitter load also, still we don’t get 3.9K by solving the above equation.
The “practical design” was contributed to me by a external author, probably it was taken from some magazine.
Hello sir,let say I go with the one you tittle (Easiest Transistor Voltage Regulator) T1=bc547, R1=1k 1watts resistor. D1and VR1 is what value. So DC input must be from battery, so if one use 12v battery can one get reasonable output.
Hello Youngking,
VR1 can be a 10K pot.
The zener diode value decides the maximum output voltage that you may need when the pot is at its highest resistance. However this maximum output voltage cannot be higher that 11.4V if a 12V input is used. So the zener value can be anything lower than 11.4V.
hi Mr. Swagatam
I would like to thank you for your scientific efforts
But I still don’t understand how the values of the resistance R1 were calculated in the circuit of title:Easiest Transistor Voltage Regulator
and also in the article: Voltage Regulator Circuits using Transistor and Zener Diode
of title: Getting Fixed Voltage from Transistor Regulator
which sometime 180-270-330 ohm
Sorry I’m a newbie in electronics
thanks for you
Thank you Sayed,
R1 is actually not critical for low current applications. It decides how much current the transistor will be allowed to pass through it.
I have explained the procedures in the above article under the the heading “Calculating the Part Values:
Let me know what you cannot understand in the formula.
Thank you so much for all of your circuits you have gone over on your websites. I have looked at many and follow the new and am particularly interested in your battery charger and power supply circuits. I have a broken ego lithium ion battery charger and from what I can tell the rectifier is placed before the large capacitors which then feeds a transistor before feeding a transformer. Battery is 14s so fully charged voltage should be 58.8v. Voltage after the capacitors is ~74v. I was wondering if a circuit similar to the 12v power supply from battery charger would work for a larger voltage power supply. Also if you have posted a similar circuit I would love to see it. Again, many thanks for all of your work and helping me understand how common circuits work.
Glad you liked them Kevin, thank you very much for visiting this site!
Yes a simple transistorized regulator can be used for charging your Li-Ion battery, as shown in the following diagram. Just be sure to keep the input charging current below 50% of the battery’s Ah rating. The zener can be a 59V zener diode customized using a few series connected zener diodes:
https://www.homemade-circuits.com/wp-content/uploads/2021/11/single-transistor-voltage-regulator.jpg
Thanks so much for the response Swagatam! That would allow me to charge the batteries in a pinch. I’m assuming the best spot would be to tap in after the output capacitors on the circuit. What about using the unit to make a low amp 60v power supply?
You are welcome Kevin! Yes you can extract DC after the output capacitor. A low current 60V unit should also work nicely, no issues with it.
Hello Swagatam,
Thanks very much for your tutorial on the Op Amp Controlled Precision Bench Power Supply. Please can you specify the value of series pass resistor R4?
(and how to calculate it)
Kind regards,
Rob
Thank you Thomas,
The R4 can be simply a 1K 1 watt resistor. It doesn’t need to be calculated because any value between 1K and 10K can be used here. It is basically to activate the feedback link to the op amp circuit, when power is switched ON.
Hello Swagatam,
Thanks for the information.
Kind regards,
Rob
You are welcome Thomas!
Great step-by-step DIY !
This article should have been published earlier !
Congrats Prof.Swagatam.
All the best in assisting all learners from your blog.
Thank you Imsa, Glad you found the post useful….appreciate your feedback.
Hi Mr Swagatam thank you for your quick response. I want to tell you that I finally found the problem of voltage drop with small loads. The problem was the R4 shunt. I put 3 resistors in parallel… Two of 0.22 and one of 0.1 the three are 5w. Now the power supply works very very well, the voltage only drops 200mv with 4 amps. Thank you very much in advance for all your help. Greetings from Argentina
That’s great Carlos, yes it seems we completely missed the current limiter resistor which was blocking the passage of higher current, and dropping the output voltage. Glad it is solved now.
Hello, good afternoon, My name is Carlos. I am a faithful follower of his website. I have a problem with a variable power supply from 0v to 30v x 5A. The problem is when I connect a load of for example 500ma the voltage drops as 2v…. For example 12v drops to 10v. Only with 500mA… Will you have a circuit to connect to the output and correct the voltage? The source is built with 2 Lm358, one for current adjustment and the other for voltage where can I upload the circuit so you can see it. Thank you very much
Hello Carlos, if it has an emitter follower type linear regulator, then you will need to increase the rating of the output transistor, and also replace it with a Darlington transistor as explained in the above article. Also make sure that the input supply from the transformer is adequately rated, otherwise the output will drop due to lack of current.
By the way without seeing the schematic it can be difficult to suggest the right solution.
Hello sir Swagatam thanks for the quick reply. transformer is 7A the circuit is here
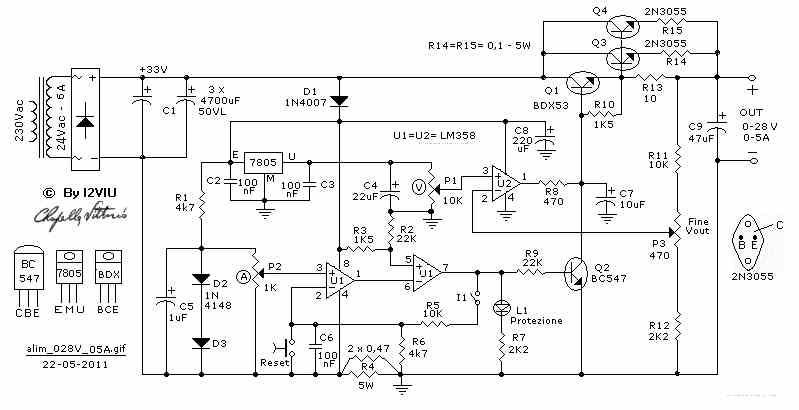
Hi Carlos, you design uses two 2N3055 and one BDX53 in Darlington mode which together can provide high power and high current output. It may be difficult for me to understand the fault in your circuit, unless it is checked practically be me which is not possible…however this circuit should be easily able to handle loads upto 4 amps. Please check if everything is hooked up correctly or not….otherwise you can try the simple bench power supplies explained in the above article, which will provide similar results.
Hello dear Sir Swagatam
Thank you very much for your friendly guidance. I should go out to buy the necessary components for “PWM Solar Battery Charger Circuit”
Best regards
No problem Kevin, I wish you all the best!
Hello dear Sir Swagatam
I believe that this is the best way but I will search your blog to find a simple variable circuit based on 2N3055 which can deliver up to 4A. my present 15V transformer delivers 3A and seems good.
Thank you very much for your response, dear Sawgatam.
Best regards
You are welcome Kevin, however a 2N3055 linear power supply will create a lot of heat, so a buck converter may be more suitable, for example the last design from the following article:
https://www.homemade-circuits.com/dc-to-dc-converter-circuits-using-sg3524-buck-boost-designs/
or the following design:
PWM Solar Battery Charger Circuit
Hello dear Sir Swagatam
I never imagined that you would respond to my letter and so soon. I am so astonished and happy of course.Thank you very much Sir. I did as you had ordered but The motor did nit run with IC7805 or 7806. I built your circuit under title “Connecting Voltage Regulators 78XX in Parallel for High Current”. 3 Nos. of 7805 ran it but the speed of motor was low, heat sink got to hot and voltage dropped to 1.5V . I did another test and used 9 Nos. of 1N5408 diodes in series with power supply. It was interesting that voltage drop without load after the ninth diode was only 2V (13 of 15) and when I connected to motor, the voltage dropped to 2V and diodes got very hot. Do you think that there may be a solution to run it safely with needed current? It seems that motor needs much current. I took the said motor out of a Black & Decker dust buster WV4815.
Thank you again and wish you the best
Best regards
Thank you Kevin, I am glad to help you!
The 78XX ICs can deliver a maximum of 1 amp current when mounted on large heatsinks.
So maybe your motor requires current a lot higher than 1 amp.
In that case it is better to employ a transformer based power supply rated at 3 amp or higher current, and preferably rated at 6 V, so that no voltage regulator is required for the conversions.
Hello dear Sir Swagatam
As an interested follower of your Site, I have a question which could be somehow related to this page of course. I am sure you are kind enough to help me who know nobody to get answer.
I have a 6 volt DC motor . it needs to 4 nos of medium size rechargeable batteries (which are out of order) to run with maximum speed. when I connect it to a 15 volt power supply, the voltage drops to 6 volt but, motor runs with maximum speed which means that the power supply possesses enough current.
Won’t this 15v power supply damage the motor? If it will damage, Can I use a few Nos. of 1N5408 diodes to reduce the voltage instead of using transistors or ICs? and my third question please: Am I obliged to do reduce 15 V to 6V?
With many thanks
Thank you Kevin, for being a dedicated follower of this blog. Yes definitely, a 15V supply can do a lot of harm to a 6V rated motor in the long run, therefore you must drop the voltage to the correct levels. If you use diodes, then you may have to use many of them to reach 6V from 15V….doesn’t appear to be a great idea. Instead you can try 7806 IC or the concept explained above.
Hi,
I am new to this so bear with me 🙂
The D1 diode is on the emitter of T2 to ground, and is a lower voltage limit for when the VR1 wiper is at min, so it’s only serving as a minimum voltage limit.
Normally (in series regulators) when T2 does not exist, circuits have a zener diode between R1 and ground to stabilize the voltage going into the base of T1 when load is applied.
In the case of this feedback loop, that zener diode is no longer needed? so when the circuit is loaded and there is a drop in the voltage , wouldn’t there also be a drop at the base of T1?
Hi, your assumption regarding D1 diode is correct.
If suppose the input voltage is 12V, and the output is adjusted to 6V with the potentiometer, and if the input supply drops by 2 to 10V due to a load at the output, there will be no change in the 6V output value, because there is still a margin of 4V above the 6V
But this will need to tested through experimentation, as I am not entirely sure about it.
Hi Swagatam,
I have built your power supply cct “Practical Design”. I would like to know if I can modify the cct to also adjust voltages between 0V & 5V. At the moment the lowest I can go is 5V.
Your assistance will be much appreciated.
Regards Jan
Hi Jan, first you will have remove D5 and R9 and replace them with direct links which will allow you reach the minimum 0V level, then you may have to experiment with the value of R8 until you get the maximum level of 5V output
Swagatam,
Does that mean that I will get the full range from 0V – 24V?
Yes, if your input is 24V then the maximum output will be around 23V, and the minimum can be reduced to 0V. For getting 5V maximum you may have to adjust the R8 value accordingly.
Hi Swagatam, I just want to confirm with you. I have removed D5 & R9, now R3 will go directly to 0V. Also if I connect a 20W load with the voltage set to 24V then the output voltage will drop to 20V and TR1 will get extremely hot within about 2-3 sec. I am suspicious about R3, but when I remove it then I can not adjust the voltage.
Your assistance will be much appreciated.
Regards
Jan
Hi Jan, the resistor R3 had been used for biasing the D5, since D5 is removed R3 becomes meaningless now, so it can be removed entirely from the circuit. But make sure to connect the emitter of TR3 to ground line after removing D5.
Also, you can connect a 1K resistor in series with the base of TR3, and then remove R8, R9 both from the circuit.
Since this a linear regulator the main transistor will become hotter as the difference between input and output voltage increases. Moreover, the maximum input current should be 1/3rd of the collector current rating of the transistor. For example if the collector current rating of T1 is 15 amps, then the maximum current through T1 should not exceed 5 amps. Even at 5 amp the 2N3055 can get very hot so a heatsink will be required.
Hi Swagatam,
Referring to your Practical Design. Can you please give me R4-R7 wattage or how to calculate it.
Regards
Jan
Hi Jan, you can calculate it by multiplying 0.6 with the maximum current limit value associated with the specific resistors.
Just have a few questions regarding your practical example:
1) I’m using TIP142 as T2 and T3 where only min. Hfe = 1000 is available . How would you calculate R1? Using your formula with Output current 2A gives R1= 350 ohm, does that sound correct?
2) you are saying that the voltage drop over R1 is always 0,7V, why is that?.
3) In your practical example you have introduced R2=470 ohm, but what is the reason behind?
Hope you can help me
1) the formula is (supply input – supply output)hFE / 2, if this is giving you 350 ohms then it is correct.
2) where did I say voltage drop across R1 is 0.7V? 0.7V is the drop across base/emitter of the pass transistor.
3) Electronics is not critical, there can be little bit difference in part values, the final diagram was taken from a magazine, i have not calculated the parts values for it, but I assume they are as per my given formulas.
Thanks for your answers, just some clarifications:
1) Could you just use the forward voltage drop (2×0.7V for Darlington) instead of (Vin-Vout)? I was more wondering if using the min. hfe value is correct?. The real Hfe value is properly much higher.
2) In the section regarding calculating the parts:
“Since the voltage across R1 will be always 0.7 V, the VCE of T2 becomes immaterial, and can be any minimum value. The Id of T2 should be such it is able to handle the base current of T1, as determined by the value of R1”. I’m asking because I want to calculate the power rating of R1.
3) Just don’t know what the purpose is of R2 🙂
Thank you so much of sharing the great design and spending time answering my questions.
Br, Michael
You are welcome!
1) For Darlington the Vin-Vout will be 1.4 V or 1.2 V
2) The statement is wrongly mentioned, the voltage across R1 will depend on the load, and the value of R2.
3) R2 is the current limiting resistor for the load
Thanks for sharing the design. Would it work with a TIP142 replacing TR1 and TR2 and BC546 instead of BC547?
yes, it will work!
Hi sir, may I know what’s the resistor watt that you use and 400uf and 100uf what is the rated voltage you recommend?
Hi Desmond, power is equal to voltage drop across the resistor multiplied by the load current through it. The voltage rating of the filter capacitors should be at least 1.5 times the DC from the transformer
what’s S2 component call?
Sir I wanted to make a 0-50 v dc & 10 amp variable power supply. Can you send me a ckt diagram for this.
Hello Ratnadip, you can use the theory explained above to design and build the required power supply easily.
For the main pass transistor T1, you can use a TIP35 with BD139 as a Darlington, with a large heatsink.
In order to keep the transistors cool, use tapped transformer, at 9 V, 18 V, 24 V, 35 V, 50 V. Depending on the output voltage you can select the appropriate range on the transformer, this will ensure that the T1 is much cooler always.
It seems excellent, I will try it!
Here in Cuba everything has to be DIY, I have for years one based on the old honorable 723.
I will comment on you. Here, from Cuba, we also follow you 😉
Thank you so much! I wish you all the best with the project!
Loved the circuit very nice classic schematic
Thanks Bob
Thanks, Glad you liked it!
Sir pls my question is a bit off,,, I want to convert a 19v laptop charger to a +19,Gnd,-19,,,,,,,,,,,, pls how do I do it,, help me
Hi MD, you can try the IC 741 based circuit or the IC LM324 based circuit from the following post, and modify them according to your specification:
https://www.homemade-circuits.com/dual-power-supply-3v5v6v9v1215v-with/