In the article below I have explained a compilation of simple yet accurate motorcycle voltage regulator circuits, which can be used for regulating the varying alternator voltage into a fixed DC voltage.
Voltage regulator circuit is very important in motorcycles and two wheelers since they ensure a regulated battery charging thus keeping the battery safe from over voltages. They also help to safeguard the electrical system and lighting system of the motorcycle, preventing them from burning or getting damaged prematurely.
[New Update] High Efficiency, Lossless Motorcycle Regulator Circuit
The following motorcycle voltage regulator circuit ensures very low dissipation and a very high efficiency because it allows the output transistor to switch ON only during the periods when the AC cycle peaks are close to the intended output DC voltage.

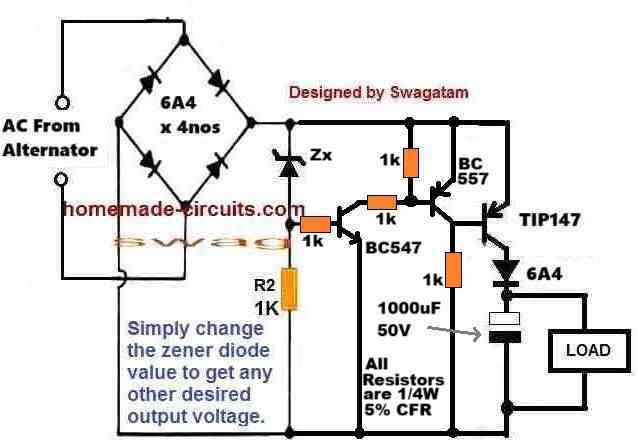
The inclusion of the two BJTs, BC547 and the BC557 convincingly keeps the TIP147 turned off as long as the AC waveform voltage level is above the zener diode breakdown level.
As long as the AC waveform voltage remains above the zener breakdown value, the zener remains conductive which in turn causes the BC547 and the BC557 to remain fully switched ON. In this condition, the BC557 keeps the base/emitter of the TIP147 short circuited, which in turn causes the TIP147 to remains turned off and non-conductive.
Now, whenever the AC waveform voltage dips below the zener breakdown value, the zener diode stops conducting, which means, the BC547 and the BC557 are also turned off. This removes the base/emitter short circuit from the TIP147 and allows it to switch ON fully. In this situation, the available instantaneous voltage at the emitter of the TIP147 quickly reaches the 1000uF capacitor, filling it up and simultaneously providing the operating DC for the attached load.
Next, as the waveform voltage continues its journey and climbs back above the zener breakdown threshold, its turns ON the zener, BC547 and the BC557, turning off the TIP147 yet again, and the cycle repeats.
So, as you can see, the TIP147 turns ON only during the periods when the peak AC voltage is close to the required output voltage, and as we know, for any linear regulator, the device remains cooler and dissipates minimum heat and is more efficient as long as its input supply voltage is close to its output supply voltage, which makes this regulator highly efficient.
Simplest Motorcycle Voltage Regulator using a Single Transistor
The next circuit below explains how to build perhaps the simplest and cheapest voltage regulator using just a single zener diode and a power transistor.
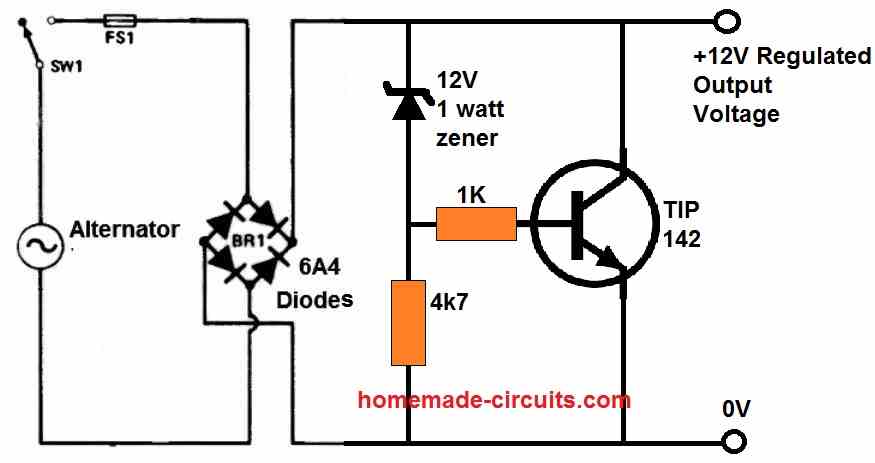
The circuit works in the following way.
As long as the rectified DC from the alternator remains below the zener diode breakdown voltage (12V), the transistor remains switched OFF due to the absence of a base voltage.
Now, as soon as the alternator DC tries to exceed the 12 V mark, the zener diode breaks down and starts conducting. This allows a base voltage to appear across the base/emitter of the transistor.
The transistor now switches ON and conducts.
When the transistor switches ON it short circuits or shunts the rectified DC, causing the alternator voltage to drop, until it drops below the 12V zener breakdown level.
When this happens the transistor switches OFF and the circuit returns to its previous state so that the voltage again starts rising, and yet again the transistor switches ON to regulate the alternator voltage.
The above ON/OFF cycle of the transistor keeps repeating a fast pace causing the output voltage to remain well regulated at 12 V.
The zener value decides the cut off threshold and thus determines the output regulated DC level.
Motorcycle Shunt Regulator Circuit using 2N3055 Transistor
The following design below explains how an op amp and 2N3055 transistors can be used to create a precision automobile voltage regulator circuit for enhanced battery charging.
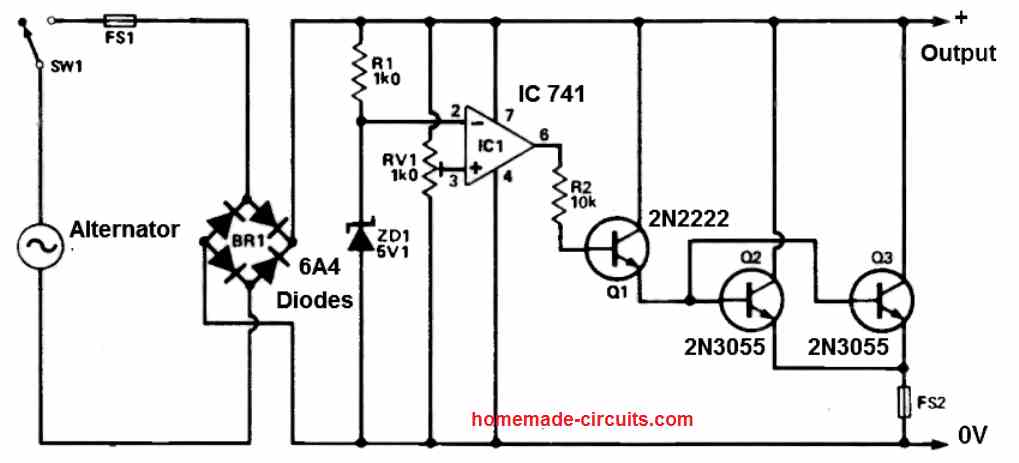
This circuit was developed to ensure control over the lighting system incorporated into an off-road motorcycle lacking lights.
The concept behind it is quite straightforward. Any surplus power generated by the motorcycle's generator is effectively shunted to ground, maintaining a constant and regulated output voltage.
The 741 chip serves as a comparator in this setup. Its output remains in a low state when the supply voltage falls below the desired threshold.
Conversely, when the supply voltage surpasses the target output level, the 741's output goes high, triggering the activation of transistors.
As a result, current is drawn from the alternator, leading to a reduction in the output voltage.
The regulator shunting activation threshold voltage is established by adjusting RV1. A bridge rectifier was opted for to ensure amplified power output during low engine speeds (idle).
To manage heat dissipation, the 2N3055 transistors are affixed to a sizeable heatsink, and the entire circuitry is coated with a protective layer of paint to prevent water infiltration.
Motorcycle Voltage Regulator using SCRs
The next design presented below is a Motorcycle Rectifier plus Regulator for a 3-Phase charging system of Motorcycles. The rectifier is full-wave and the regulator is shunt-type regulator.
By: Abu Hafss
A motorcycle's charging system is different from that on cars. The voltage alternator or generator on cars are electro-magnet type which are quite easy to regulate. Whereas, the generators on motorcycles are permanent magnet type.
The voltage output of an alternator is directly proportional to the RPM i.e. at high RPM the alternator will produce high voltages more than 50V hence, a regulator becomes essential to protect the entire electrical system and the battery too.
Some small bikes and 3-wheelers which do not run at high speeds, only have 6 diodes (D6-D11) to perform full-wave rectification.
They don't need regulation but those diodes are high ampere rated and dissipate a lot of heat during operation.
In bikes with proper regulated charging systems, normally shunt-type regulation is used. This is done by shorting out the alternator's windings for one cycle of the AC waveform. An SCR or sometimes a transistor is used as shunting device in each phase.
Circuit Diagram
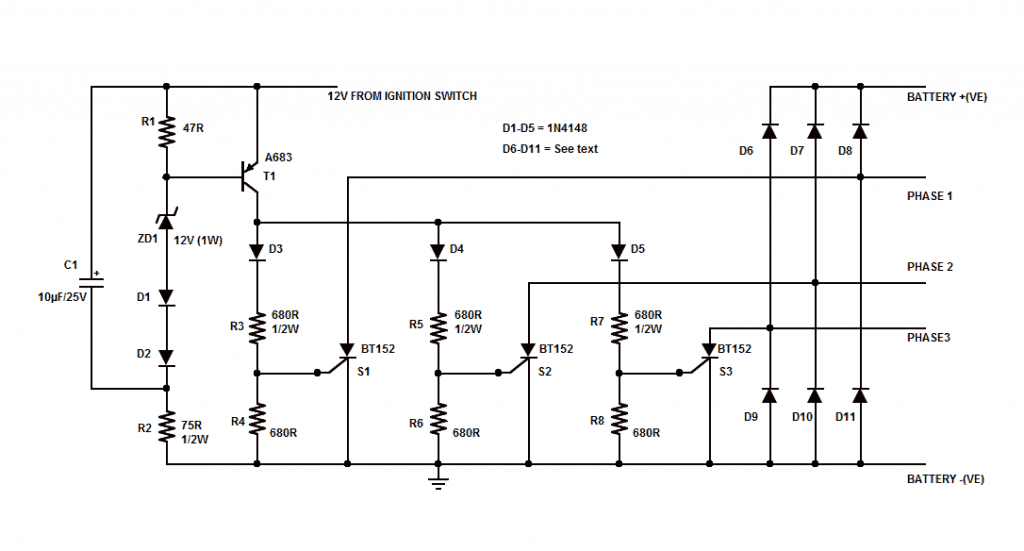
Circuit Operation
The network C1, R1, R2, ZD1, D1 and D2 forms the voltage detection circuit, and it is designed to trigger at about 14.4 volts. As soon as charging system passes this threshold voltage, T1 starts conducting.
This sends current to each gate of the three SCRs S1, S2 and S3, via current limiting resistors R3, R5 and R7. D3, D4 and D5 are important to isolate the gates from each other. R4, R6 and R8 help in draining any possible leakage from T1. S1, S2 & S3 should be heat-sinked and isolated from each other using mica insulator, if using common heat-sink.
For the rectifier, there are three options:
a) Six automotive diodes
b) One 3-phase rectifier
c) Two bridge rectifiers
All must be rated at least 15A and heat-sinked.
The automotive diodes are two types positive body or negative body hence, should be used accordingly. But they might be little difficult to contact to heat-sink.
Using Two Bridge Rectifiers
If using two bridge rectifiers, they may be used as shown.
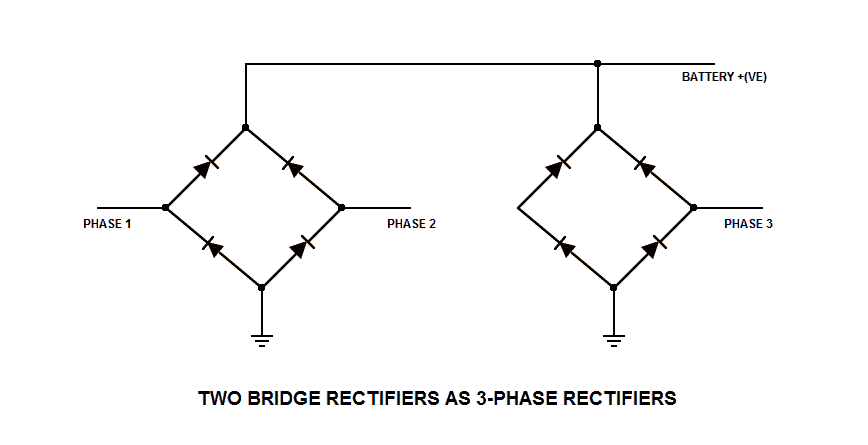
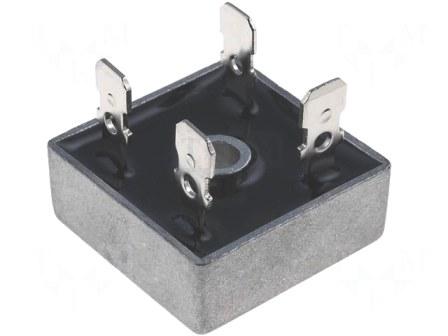
Bridge Rectifier
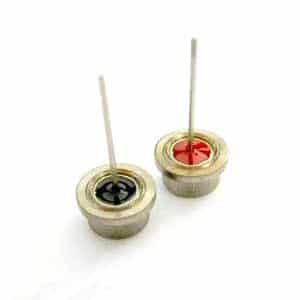
Automotive diodes
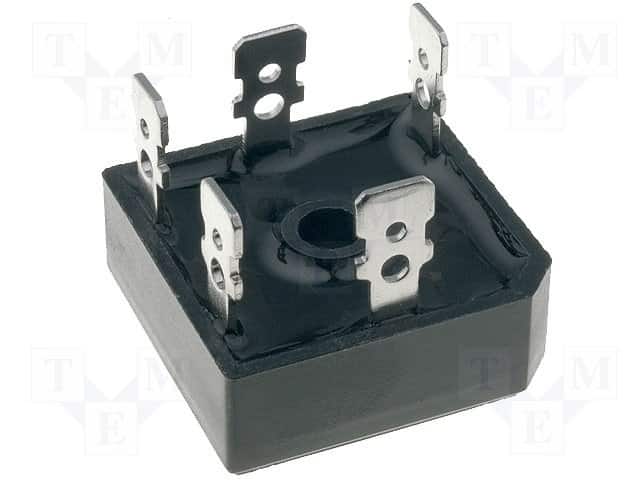
3-phase rectifier
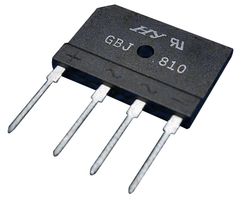
Bridge Rectifier
MOSFET Full Wave Shunt Regulator Circuit
The next post below explains a full wave motorcycle shunt regulator circuit, requested by Mr.Michael. I have explained the circuit functioning in details.
How a Shunt Regulator Works
Shunt regulator is a device which is used for regulating voltage to some fixed levels by means of shunting. Normally the process of shunting is done by grounding the excess voltage, just as zener diodes do in electronic circuits.
However one bad aspect with such regulators is the generation of unnecessary heat. The reason for heat generation is the principle of its operation where the excess voltage is short circuited to ground.
The above practice may be implemented by simpler and cheaper means, but cannot be considered efficient and advanced. The system is based on destroying or killing energy instead of eliminating or inhibiting it.
The circuit of a motorcycle shunt regulator discussed in this article takes a completely different approach and restricts the in-flow of excess voltage instead of "killing" energy and thus stops the generation of unnecessary heat.
Circuit Operation
The circuit functioning may be understood as under:
When the mobike is started, voltage enters across the P-channel mosfet source/drain pins due to the gate trigger that becomes available via R1.
The moment the high voltage reaches R3, which happens to be the sensing input of the opamp, pin#3 of the IC senses an increased voltage.
As per the set reference at puin#2, the instantaneously reacts to the situation and the result puts the output of the IC to a high logic level.
The immediate high logic pulse restricts the negative base trigger of the mosfet, switching it OFF at that particular instant.
The moment T1 switches OFF, voltage at the junction of R3/R4 reverts to the original condition, that is the voltage here now drops below the reference level......this instantly activates the opamp output with a low logic signal which in turn switches ON T1 back into action.
The process repeats at a very rapid speed, keeping the output voltage marked with +/- at a constant level determined by the setting of R2/Z1 and R3/R4.
The above principle utilizes voltage inhibition technique of the excess voltage instead of shunting it to ground, thus saves precious power and also helps to control global warming in some way.
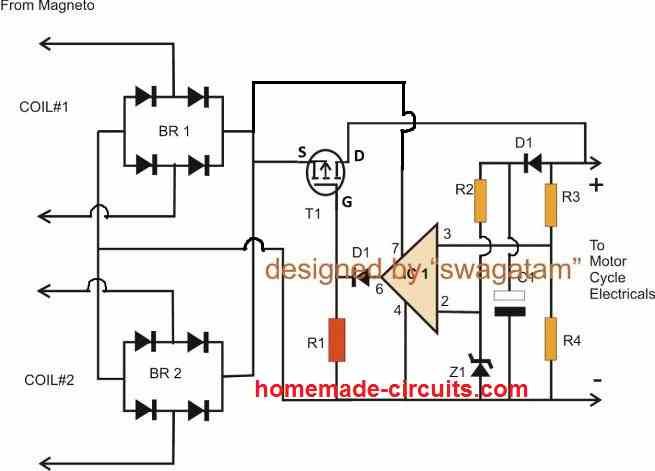
Parts List
- R1, BR2 = 10Amp bridge rectifier
- R1 = 1K
- D1 = 1N4007
- C1 = 100uF/25V
- IC1 = IC741
- T1 = mosfet J162
- R2/Z1, R3/R4 = as explained in this article
Shunting Excess Power to Ground is Recommended in Alternators
When it comes to alternators, the best way to restrict or limit excess voltage is to short the excess power or shunt the excess power to ground. This eliminates the rising current in the armature and protects the winding from heating up.
A voltage regulator using this method can be witnessed in the following examples:
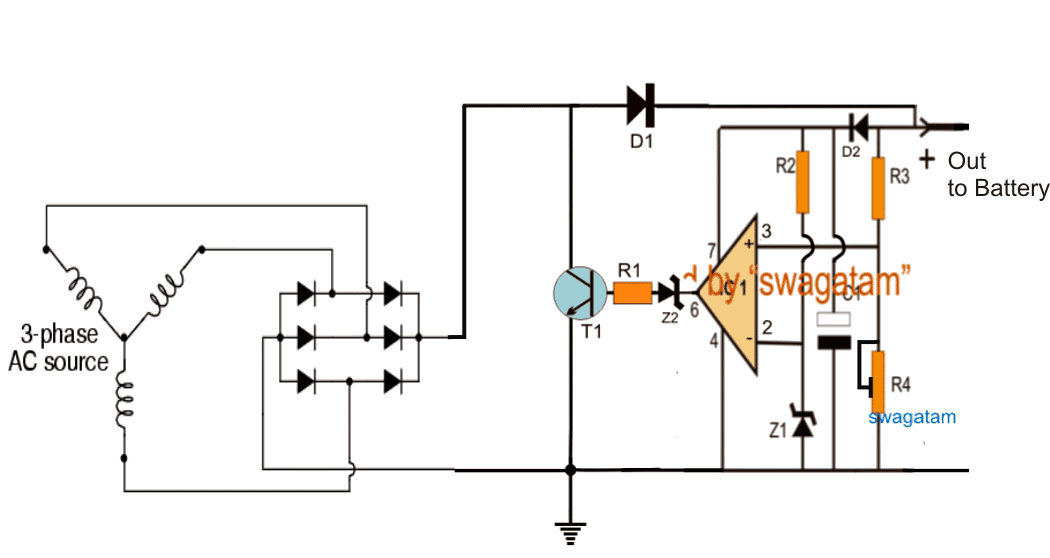
Video Clip below shows an opamp based shunt regulator circuit, and its testing procedure
Parts List
R1, R2, R3 = 10K
R4 = 10K preset
Z1, Z2 = 3V zener 1/4 watt
C1 = 10uF/25V
T1 = TIP142 (on large heatsink)
IC1 = 741
D1 = 6A4 diode
D2 = 1N4148
Bridge rectifier = standard motorcycle bridge rectifier
How to Set up the Circuit
For a 12V system, apply a 18V from a DC power supply from the T1 side, and adjust R4 to precisely set 14.4V across the output terminals.
Simplest Regulator using TL431 IC
An even simpler motorcycle shunt regulator using the shunt regulator IC TL431 can be witnessed below, the 3k3 resistor can eb tweaked to chnage the output voltage to the most favorable level.
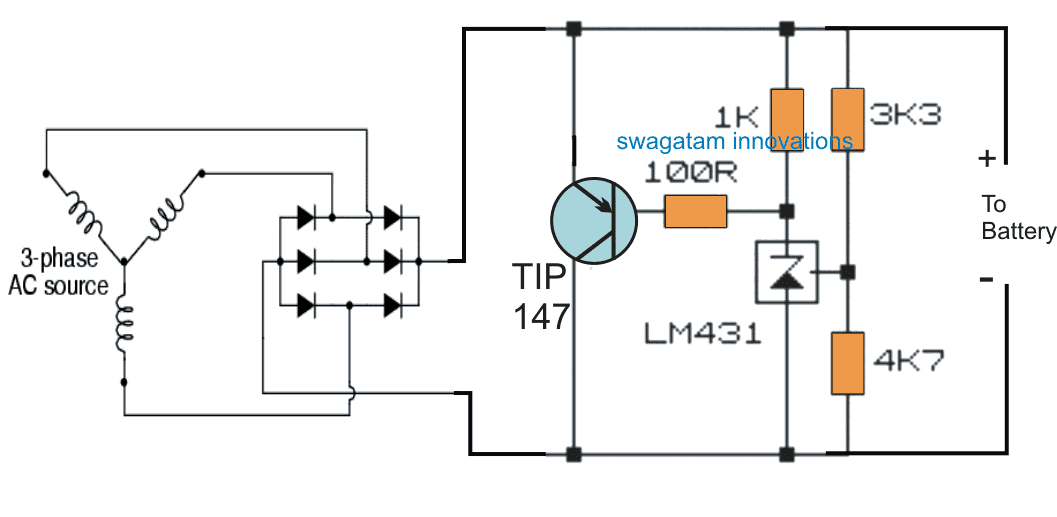
For single phase alternators, the 6 diode bridge rectifier could be replaced with a 4 diode bridge rectifier as shown in the following diagram:
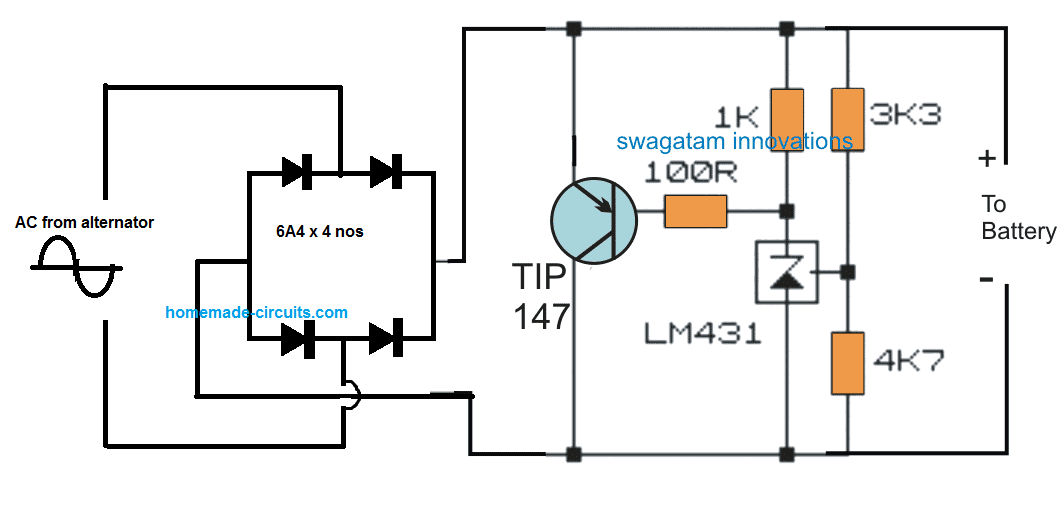
3-Phase Motorcycle Voltage Regulator using IC 555
The next post below discusses a list of PWM controlled simple 3 phase motorcycle voltage regulator circuit which may be used for controlling the battery charging voltage in most two wheeler. The idea was requested by Mr. Junior.
Technical Specifications
hello my name is junior live in Brazil and work with manufacturing and recovery regulator rectifier motorcycle voltage and would appreciate a help u, I need a three-phase mosfet regulator circuit for motorcycles, entreda voltage 80-150 volts, correte Maximum 25A, maximum consumption of the system 300 watts,
I await return
att.
junior
The Design
The proposed 3 phase motorcycle voltage regulator circuit for motorcycle may be witnessed in the diagram below.
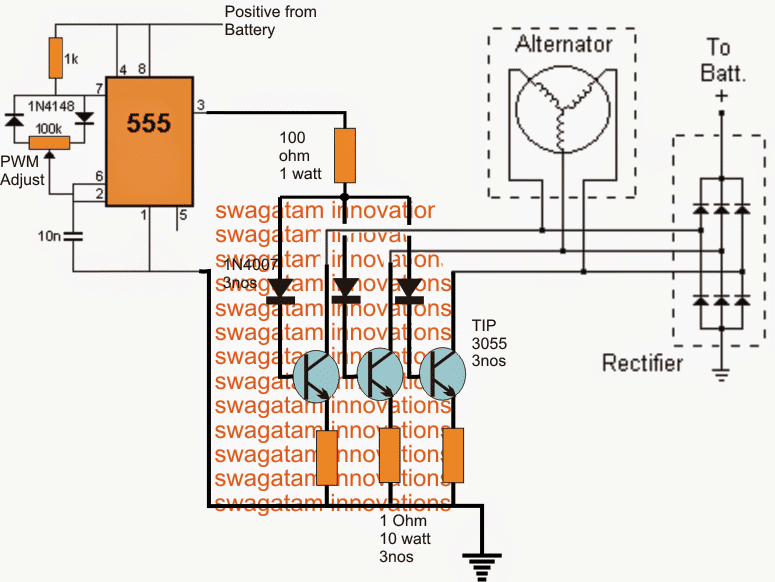
The schematic is rather easy to understand.
The 3 phase output from the alternator is sequentially applied across three power transistors which basically act like shunting devices for the alternator current.
As we all that while operating, an alternator winding could get subjected to huge reverse EMFs, to an extent which could get rip of the insulation cover of the winding destroying it permanently.
Regulating the alternator potential through the method of shunting or shorting to ground helps to keep the alternator potential under control without causing adverse effects in it.
The timing of the shunting period is crucial here and directly influences the magnitude of current that may finally reach the rectifier and the battery under charge.
A very simple way of controlling the shunting time period is by controlling the conduction of the three BJTs connected across the 3 winding of the alternator, as shown in the diagram.
Mosfets could also be used instead of the BJTs, but could be mush costlier than the BJTs.
The method is implemented by using a simple 555 IC PWM circuit.
The variable PWM output from pin3 of the IC is applied across the bases of the BJTs which in turn are forced to conduct in a controlled manner depending upon the PWM duty cycle.
The associated pot with the IC 555 circuit is appropriately adjust for obtaining the correct average RMS voltage for the battery in charge.
The method shown in the 3 phase motorcycle voltage regulator circuit using mosfets can be equally implemented for single alternators for getting identical results.
Peak voltage adjustment
A peak voltage regulation feature may be included in the above circuit as per the following diagram, in order to maintain a safe charging voltage level for the connected battery.
As can be seen, the ground line of the IC 555 is switched by the NPN BC547 whose base is controlled by the peak voltage from the alternator.
When the peak voltage exceeds 15 V, the BC547 conducts and activates the IC 555 PWM circuitry.
The MOSFET now conducts and begin shunting the excess voltage from the alternator to ground, at a rate determined by the PWM duty cycle.
The process prevents the alternator voltage exceeding above this threshold, thus ensuring that the battery is never over charged.
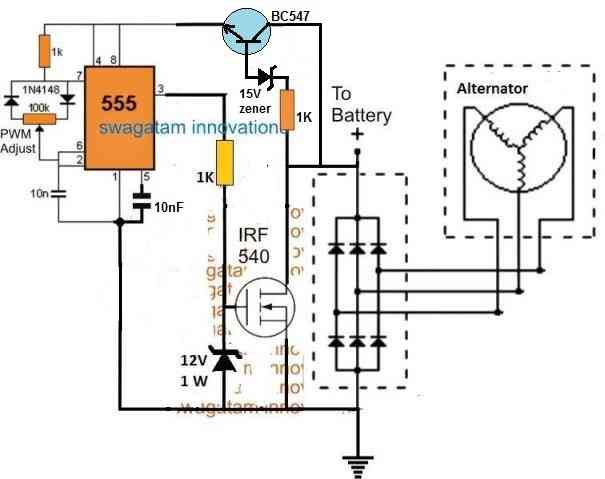
Efficient Battery Charging through Motorcycle Shunt Regulation
The following email conversation between Mr Leoneard, an avid researchers/engineer and me, helps us to learn some very interesting facts regarding motorcycle shunt regulator drawbacks and limitations. It also helps us to know how to upgrade the concept simply into an effective yet cheap design.
Leonard:
You have an interesting circuit, but.....
My motorcycle has a 30 amp alternator, which I'm sure is RMS, and peaks at 43.2 Amps. Your 25 Amp circuit is not likely to hold up long at all.
However.....
In place of the rectifiers you suggest, an SQL50A is rated 50 Amps at 1,000 Volts. It is a 3-phase rectifier module, and should have no problem handling 45 amps peak. (I have two on hand.)
That also means the SCRs will have to handle that Amperage and three HS4040NAQ2 with RMS current of 40 Amps (non-repetitive surge to 520 Amps) should handle that quite well. Of course, they'll require a pretty healthy heatsink, and good air flow.
I'm thinking the control circuit should work pretty much as is.
I've replaced 3 regulators in the last three months and I'm about tried of throwing good money after bad.
The last one lasted a total of ten seconds before it went bad too. I'm about to build my own and if I have to build it to power a battleship, so be it.
Another thing I've noticed, the laminations used in the alternator are considerably thicker than those used in electric motors.
An 18-pole winding, and engine operating at highway speeds means much higher frequency, and far more eddy currents in the iron.
What would be the effect on those eddy currents if using a series regulator that would allow the voltage to go as high as 70 Volts (RMS)?
Would this increase the eddy currents to the point of overheating the iron, and risk damage to the windings of the alternator? If so, it would make sense not to allow the voltage to get above 14 Volts, but I still have 20 Amps coming from the alternator at 1500 RPM.
Me:
Thank you! Yes you must get rid of that high voltage which might put huge pressure on the alternator winding, the best way is to shunt it through heavy duty MOSFETs on heatsink
https://www.homemade-circuits.com/wp-content/uploads/2012/10/shunt-3.png
Leonard:
Actually, I'm not nearly as concerned about the effects of voltage on the windings. They appear to be coated with Poly-Armor Vinyl, which is also used in random wound stators operating at 480 Volts.
I'm far more concerned about the heat from the eddy currents in the laminations, since they are so thick. Here in the States, with 60 htz line current, the thickness of motor laminations are a fraction of what they are in the alternator.
At road speed, the frequency from the alternator can be 1.2 Khtz or higher. In other applications, that would call for a ferrite core to eliminate the eddy currents.
I'm trying to understand the role of eddy currents in this application. As RPM increases, so does the frequency, and the eddy currents as well.
A parasitic load to level off the voltage generated? A means of leveling off current generated at high RPM?
Just how much heat does that generate? Enough to burn out the winding at high RPM?
Located inside the engine, I can understand using engine oil to cool the assembly, however, with the centrifugal force of the flywheel, and the windings located inside that, I can't imagine any real amount of oil getting to them for cooling.
The highest voltage I've been able to read is 70 Volts RMS. That's not enough to arc through PAV coating on the wire, unless heat becomes excessive.
However, in shunting the excess to ground, Is there a counter EMF that opposes the magnetic field from the rotating magnets? And if so, how effective is it?
Me:
Yes, increase in frequency will give rise to more eddy current in an iron based core, and an increase in heat.I have read that shunt control method is good for motor based generators, but this will also mean increased load on the alternator wheel and more fuel consumption by the vehicle.Is fan cooling an option? the current to the fan can be accessed from the alternator itself.
Leonard:
I'm afraid that a cooling fan is not an option for the alternator. That is mounted internal, inside the engine, and on my Vulcan, there are two aluminum covers over that.(Replacing the alternator winding means removing the engine from the motorcycle.)
I do not see any way of reducing the eddy currents because they are induced by the magnets rotating inside the flywheel. However, I can reduce the current shunted to ground by raising the voltage of the shunt to 24 Volts, and following that with a series regulator set to 14 Volts.
In testing the alternator, I do not see much effect from counter EMF in reducing short-circuit current. I can load the alternator to 30 Amps, and by shorting the leads, I still read 29 Amps.
However, if using the eddy currents as a parasitic load to level off the voltage and current at high RPM, it seems to be quite effective.
Once the open circuit voltage reaches 70 Volts (RMS), it does not go higher even when engine RPM doubles. Shunting 20 Amps to ground (as done by factory regulators), increases the heat in the winding in addition to the eddy currents.
By reducing the current through the windings, the heat generated by the windings should also be reduced. That won't reduce the eddy currents, but should reduce the overall heat generated by the alternator, hopefully preserving the winding insulation.
Considering the coating on the windings, I'm not nearly as concerned about the voltage generated. Having worked in electric motor rebuilding for years, I'm aware that HEAT is the worst enemy of the insulation.
The quality of the insulation is reduced as operating temperature increases. At ambient temperature, PAV coating can hold 100 Volts "turn-to-turn". But raise that temperature by 100 C, and it may not.
I'm also curious.
Electric motors use a steel alloy with 3% silicon to reduce the resistance to magnetic field reversal within the iron. Do they include that in their laminations or omit the silicon to further reduce the increase of voltage and current at high RPM?
It does not add to the heat, but does reduce the efficiency of the iron, the higher the RPM. By increasing the resistance to magnetic field reversal in the core, the magnetic field may not penetrate as deeply into the core before it is required to reverse.
So, the higher the RPM, the less penetration by the magnetic field. The eddy currents may further reduce that penetration.
Me:
Your analysis makes sense and appears very much technically sound. Being basically an electronics guy, my electrical knowledge is not very good, so suggesting motor internal working and modifications can be difficult for me.
But, as you said in your last sentences by restricting the magnetic filed, the eddy current can be prevented from entering deep. I tried searching about this issue but couldn't find anything useful so far!
Leonard:
So, having worked with electric motors for 13 years, I have you at a slight disadvantage? Although, my studies have also been with electronics, and so was all my work until I found I could make more money working with motors.
That also meant I did not keep up with integrated circuits, and MOSFETs were delicate little things that could quickly be blown out with the slightest static charge.
So when it comes to electronics, you have me at a disadvantage. I was not able to keep up with new developments.
It's interesting that I have not been able to find much of my information in one place. Sort of as though none of the concepts are related to each other. Yet, when putting them all together, they begin to make sense.
The higher the frequency, the less turns are required to get the same inductive reactance. So the higher the RPM, the less effective the magnetic field becomes. It's about the only way they can keep the output constant once the output reaches 70 volts.
But in looking at the pattern on an oscilloscope, I'm not impressed. A millisecond of charge time, followed by 6 to 8 millisecond of grounded output.
Could this be why motorcycle batteries don't last long? Six months to a year, while automotive batteries go on for five years or more.
This is why I'm opting to "clip" the voltage level to ground at a higher voltage, and that clipping being constant.
Followed by a series regulator to maintain a constant charge rate according to what the battery, lights, and circuits require. Then by designing it to handle 50 Amps, I should never have to replace a regulator again.
I'm working with a 50 Amp rating, but I expect that by using a "clipper" the Amperage should be considerably lower than 20 Amps to ground.
Perhaps as low as four Amps. Then the series regulator allows the (approximately) seven Amps for the battery, lights, and circuits for the engine. All well within the wattage rating of the components and not enough voltage to challenge the coating of the windings.
You wrote a very good article about shunt regulators, but 25 Amps is just too small for my application. Still, it is good inspiration.
Me:
Yes that's right, duty cycle of 1/6 will not charge a battery properly. But this can be easily solved through a bridge rectifier and a large filter capacitor, which will ensure that the battery gets enough DC for effective charging.I am glad liked my article.
However the 25 Amp limit can be easily upgraded by increasing the MOSFET amp specs. Or may be by adding more devices in parallel.
Leonard:
At the same time, I'm trying to keep everything compact to fit into room available, so that large filter capacitor capacitor becomes a problem.
It is also not needed if all three phases are clipped after the bridge rectifier. All ripple is clipped off, and the series regulator maintains 100% charge time.
Your circuit also maintains 100% charge time, however the current you shunt to ground will be much higher because you are clipping it at battery voltage.
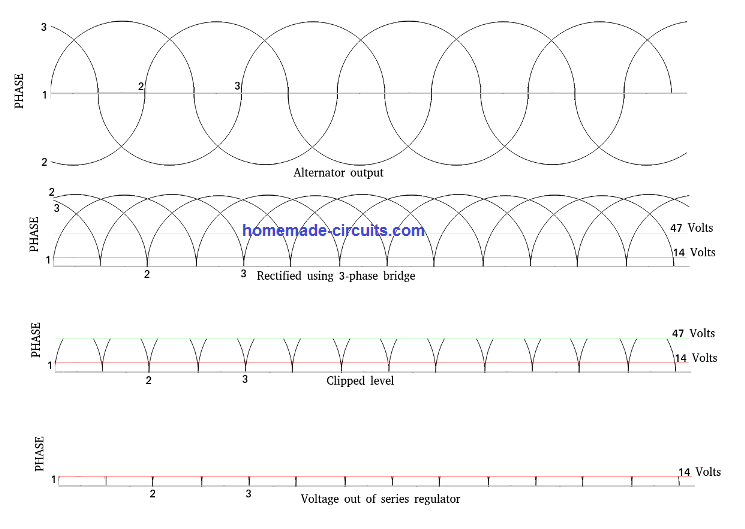
As you can see in the waveforms, there should be no capacitor needed. But by clipping at a higher level, the current shunted to ground should be lower. Then, dropping the voltage across a series regulator should not hurt anything.
There should be more than enough to keep the battery charged.
One note. Optimum charge voltage for a lead/acid battery is actually 13.7 volts. To hold it at 12 volts may not give the battery enough to start the engine. And my circuit is preliminary, and still subject to change.
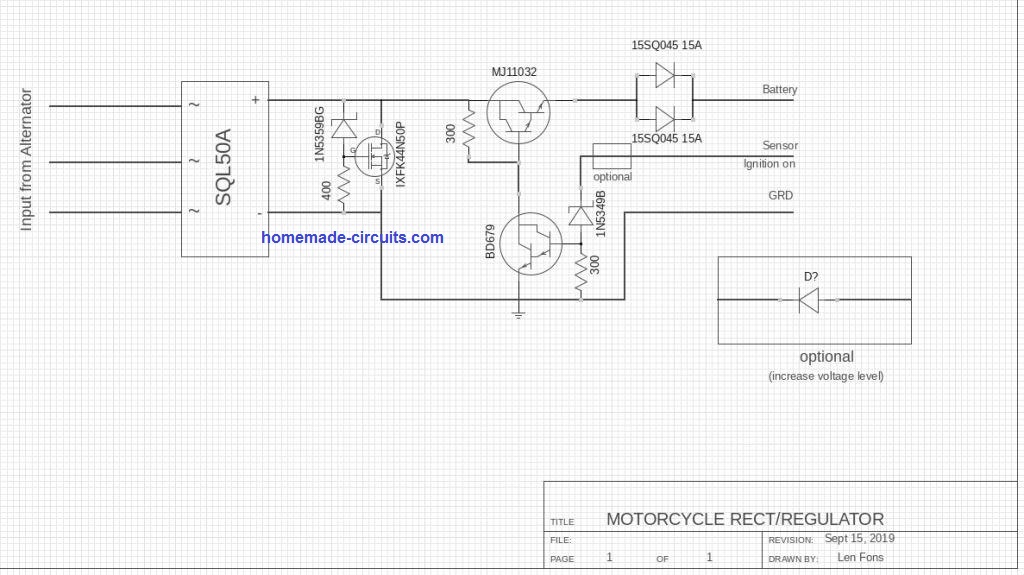
The factory looks almost primitive, in the way it works. Their circuit charges the battery until it reaches the trigger level. then it shunts all current to ground until the battery drops below the trigger level.
The result is a waveform with a short, harsh burst of charge that could be as high as 15 Amps. (I did not measure it) That followed by a longer line with a slight downward slope, and another burst.
I've seen automotive batteries last 5 to 10 years, or longer. As a kid on a farm, my father converted one of the old tractors from six volts to a twelve volt system, using an alternator from a car. Fifteen years later, that same battery was still starting the tractor.
At the school I work with (Teaches motorcycle safety), all batteries need to be replaced within one year. WHY ? ? ?
The only thing I've been able to come up with is the charging system. Most of the batteries I've worked with are only rated for a 2 Amp charge rate, Up to 70 volts, capable of 30 Amps, applied to the battery terminals for short bursts may be causing internal damage and shortening the life of the battery.
Especially, in the batteries where you can not check the fluid levels. The only problem with the battery may be fluid level, but there is nothing you can do about it. If I'm able to check and maintain fluid levels, the battery life is extended considerably.
The leads coming from the alternator would be the metric equivalent of #16. According to the AWG table, that's good for 3.7 Amps as a transmission line, and 22 Amps in chassis wiring. On a 30 Amp alternator with a shunt regulator?
The shunt level and the Amperage should be an inverse proportion, so by clipping the voltage in half, I should reduce the Amperage significantly. In looking at the rectified waveform, the highest concentration of EMF is in the lower half. Logic would suggest the current will be reduced to a fraction. I'll find out when I put it into use.
On a 1500cc engine, I don't expect to notice the reduced drag on the engine, but my fuel economy may improve. And, I remember, back when they first started putting solid-state regulators on automotive alternators, the magic number was 13.7 Volts.
However, I was planning on setting my series regulator at about 14.2 Volts. Too high and the fluid evaporates more quickly.
You were far more helpful than you know. Originally, I had six different circuits that I was considering and was going to breadboard each of them.
Your article eliminated five of them, so I get to save considerable time and concentrate on just one. That saves me a good amount of work.
That makes it very well worth the time to contact you.
You have my permission to experiment with my schematic and see what you come up with. On various forums, I'm reading where a number of people are talking about going to series regulators.
Others caution against too high a voltage destroying the insulated coating on the wire. I suspect the happy medium may be a combination of both systems, but not shunting the full output to ground. The circuit is still simple, with few components, but not archaic.
Thank you very much for your time and attention. One of my sources for technical information is: OCW.MIT.EDU I've been doing engineering courses there for a few years now. You don't get any credit for doing them, but it's also completely free.
Feedback and Update from an Avid reader Mr. Leonard Fons
I've come up with a bit more that needs to be considered.
I'm using a MOSFET (IXFK44N50P) for the clipper and series regulators. Never did much with FETs because when they first came out, the least little static charge would blow them out in a heartbeat. So this is actually my first attempt to use them.
I assumed that, like junction transistors, the more power they handle, the more power needed to drive them. NOT TRUE. In looking again at the datasheet, I see that Gate current is plus or minus 10 nano Amps.
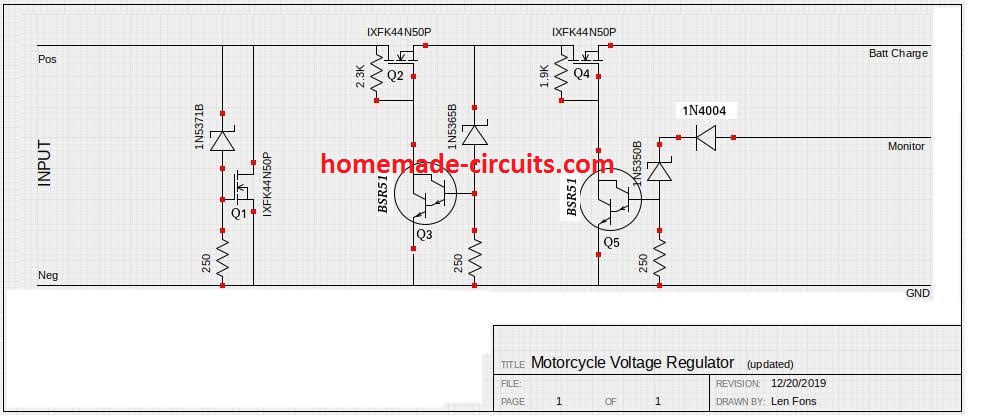
That is ten trillionth of an amp. They do not require a TIP142 to drive them. A one watt, high gain darlington will do the job very nicely. And the entire circuit will fit on one board. I still need another regulator housing for the rectifier. But I'm about ready to put this all together and try it out.
Of course, I will try it out before I actually mount it into the housing, but I don't expect to make any modifications.
Realizing that these FETs use almost no gate current at all makes quite a difference. I'll find out just haw accurate my theory is for the current to ground when clipped at 60 volts, rather than shunting all current to ground.
A when I pot it into the I have to insure that the FETs have no gap to the housing. That was another issue with one of the others. A sixteenth inch space between the components and the housing,
With that gap filled with epoxy, it's not very efficient at dissipating the heat for these motorcycle voltage regulators. By the time the housing starts getting warm, you'd burn your fingers on the components.
One change I may make is the series diode in the monitor line. A green LED located where I can see it while riding will let me know if it's charging.
Hello,
Very nice explanation and diagrams.
I have a doubt that i would apreciate any explanation.
I want to make a 54 Volts voltage regulator to charge 48 v lithium batterys. I want to use a monophasic generator. Can you give me some explanation about the circuit diagram?
Thank you
Thank you for liking the above circuits, I appreciate it.
You can try the following design for the mentioned application:
https://www.homemade-circuits.com/wp-content/uploads/2021/01/simple-pass-transistor-emitter-follower-volateg-regulator.png
R1 = 1k 2 watt
VR1 = 10k preset
D1 = 56V 1 watt zener diode
T1 = TIP142 transistor
Please make sure the input DC comes from a bridge rectifier, and connect a 1000uF/100V capacitor across the emitter of the TIP142 and the ground..
Ok thank you sir. That circuit will be able to drain how much current with out oveheating?
Thank you Sérgio, If you use TIP142, then the transistor will be able to handle 2 amp current without heatsink, and upto 6 amp with a large heatsink.
Good morning engineer, thank you very much for all the answers. Still, I would like to ask you, if you don’t mind, how to limit the output current to 4 amps maximum?
Sure, I will show you how to limit the current to 4 amps, you just have to add another transistor and a resistor as shown in the following figure:
https://www.homemade-circuits.com/wp-content/uploads/2022/04/simplest-bench-power-supply.jpg
See the transistor T3 and the resistor R2, and add the same configuration to the previous circuit suggested by me.
I hope you got it, if not please let me know!
Yes, i think i understood. The colector of the T3 links to the base of the T1, and R2 in this case will be 0,15 ohm. T3 wil be a BC547 and R2 probably 2 watts resistor. Also the condenser will be on the end of the circuit.
Kind regards
Yes, that looks perfect.
Power of R2 will be 4 * 0.6 = 2.4 watts or simply 3 watts
Thank you
Kind regards
Did you meant to say that I need to connect the regulator circuit to the 14V output of the inbuilt charger?
Can I use LM317T since I have that available handy?
Yes, you can do that, LM317 can handle only 1.5 amps, so i would recommend using LM338 which can handle upto 5 amps….
Thank you so much!!!
I Would try this circuit
You are most welcome!
Hello sir, I am Dinesh from new Delhi. I like these diy projects and have built many for my personal use. This was exactly what I was looking for. I have tons of Lithium ion cells laying around in my “Diy Room” So, I am looking forward to replace my bike’s lead acid battery with a Li-ion one but needed a proper charging circuit to charge the lithium pack. I have two doubts :
1. Which is the circuit that I should go with for charging the Lithium pack? Or is there any special circuit that should be used to charge the Li-ion pack?
2 The 3S battery pack configuration provides a peak voltage of 4.2V X 3 = 12.6V, whereas a 4S has 16.8V of peak voltage. Which battery pack configuration should I go with?
Hello Dinesh,
Yes certainly you can replace your bike’s lead acid battery with Li-ion battery for better efficiency.
Ideally you might require a balance charger for series connected battery, however, you try using a normal charger also and monitor the results, if the pack charges correctly, then no need of the balance charger.
The charger circuit must be a constant current, constant voltage type, with an over charge auto cut-off. However if you limit the charger max voltage below the full charge level of the battery then probably the auto cut-off can be eliminated.
For example, for the 12.6V battery you can limit the max voltage from the charger at 12V @0.5Ah rate and for the 16.8V, you can limit the max charging voltage to 16V, @0.5 Ah rate.
Please let me know the specifications of your bike motor and the battery, I will try to figure out which battery will be more suitable.
Hello sir, thanks for a quick reply.
I think you misunderstood the bike with a electric one but it is petrol engine bike. The bike is a yamaha fz-16 v1 and it has got 12v 5Ah lead acid battery. I will be replacing the dead lead acid battery with a Li-ion one for the self starting sinnce it doesn’t have kick start function.
It’s inbuilt charger has total 5 pins in which 3 are AC and 2 are dc output. At idle engine speed the charger outputs 14.12V dc and at full throttle it outputs 14.70V dc. But I got strange AC voltage measurement (I don’t know why) on the three wires of about 8V and 5V which were unstable.
For the balance and overcharge/ overcurren protection I will be using BMS with the battery. Only I need to know which is the best suited circuit having the best constant voltage output for li-ion battery.
You are right Dinesh, I misunderstood it to be an electric bike.
OK, if you are looking for a constant voltage source, then you can simply use an LM338 based circuit, and calculate its resistors to get the intended constant voltage output for your bike battery, here’s the link for that circuit and the calculations, make sure to replace the LM317 with LM338 IC:
https://www.homemade-circuits.com/lm317-lm338-lm396-calculator-software/
The 8V from the alternator could be the RMS AC, which may reach upto 12V upon full wave rectification and filtration….
Hello sir, after a lot of tweaking and playing with bike’s charging system I finally managed to shot the inbuilt regulator rectifier of the bike. Now it is outputting 60-70 volts. Now I think I need to build the lithium charging circuit from scratch. There are total 5 wires coming out from the magnet coil out of which 2 goes to ignition coil and the other 3 goes to the rectifier regulator of bike. Can you provide me a N channel mosfet based charging circuit since I have many power mosfets with me. I need 12.6 V max output voltage out of the charger. And should I use a circuit that shunts the excess voltage to ground in this case as explained by you in the above article?
Hello Dinesh,
I can provide you with a MOSFET based circuit but converting 60V to 12.6V can make the MOSFET very hot.
I would rather recommend you the first circuit from the above article, which can work without getting hot.
You can replace the TIP147 with a P-channel MOSFET.
Let me know your thoughts on this….
Thanks for replying, I have measured dc voltage output by connecting a bridge rectifier and and a 400v filter capacitor to the alternator directly and the dc voltage on capacitor reaches 160 volts on full throttle. And on idle becomes 70-80 volt, will the first (lossless) circuit work on that voltage?
Yes, it will work, but you may have to upgrade the transistor voltage ratings to 200V. The BC547/BC557 can be rated at 200V and 100 ma current, and the TIP147 with 200V and current according to the max load current specifications.
Can you please share a modified circuit with a N-channel Mosfet in place of TIP147?
You can try the following design:
https://www.homemade-circuits.com/wp-content/uploads/2024/10/high-power-high-efficiency-voltage-regulator-circuit.jpg
You may have to tweak the Zx value until you get the required output correctly.
Yes, the new configuration should work just fine.
https://www.homemade-circuits.com/wp-content/uploads/2014/12/lossless-AC-to-DC-voltage-regulator-circuit-diagram.jpg
The circuit will shut off for input voltages above about 16 V.
One small caveat though is that the switching is a little less “lossless” than it may seem at first glance. The integrated Darlington TIP147 will not saturate as a discrete configuration can. The driver transistor in the TIP147
must maintain the base emitter voltage for the power transistor in the package. This will not let the collector voltage drop below this needed voltage. So there will be small amount of voltage on the combined collectors even during maximum saturation.
A single high power mosfet with low RDS ON would be ideal in this application.
Thanks for your feedback! I appreciate it!
By the term “lossless” I actually meant reduced dissipation through the devices, unlike linear regulator circuits.
I hope someone implements the variations and checks the actual results, so we can know how it works in real life.
Yes sir, I think you are wrong in your explanation. There are 2 simple ways to prove this:
1, Put the circuit in any simulator of your choice and model it and measure it and you will see what I mean.
2. Build the circuit and get it running any way you like. Use rectified pulses from a given AC source. This can be from an actual motorcycle generator or even from the secondary of a power transformer, 24 VAC should do, for the purposes of demonstration. Or, even just use a variable DC lab supply that can be turned up to say 20 V or greater and observe what happens as you increase the voltage.
Now, when you have the circuit working as you think it should be, simply remove the Zener diode and watch NOTHING change. And NOTHING will ever change because in this circuit the Zener is NEVER active.
I think you need to look at this differently than you are. First off, understand that the base emitter junction of a bipolar transistor is effectively a just a diode. In the case of a Darlington transistor this is 2 diodes in series. It really is that simple in this case. So, now just take two 1N4007 diodes or any others of your choice and connect these is series. Remove the Darlington from the circuit and take these 2 diodes (effectively the base emitter junction of the Darlington) and connect them across the Zener diode, of course polarized to conduct from + to -, just like the emitter to base of the Darlington that was just removed. Now, when a voltage is applied you will see that the voltage across the Zener diode never exceeds the voltage across the 2 regular diodes. These 2 diodes effectively “short” across the Zener and never allow this voltage to increase much above 1.4 V. So, the Zener diode never actually conducts. It has no function in this circuit, it really is that simple. Of course, it also means that as soon as the 2 diodes start conducting the Darlington would be effectively ON. And as this is the case, there is no regulation of any kind that takes place.
In the circuit, the Darlington is on long before the Zener diode can conduct. The Zener diode dose not need to conduct to turn on the Darlington. The Darlington is on as soon as there is sufficient current flowing in the base emitter junction, same as the 2 diodes, through the 1 k resistor to ground. If here where ever a voltage even close to 16 V across the Zener and of course the emitter to base of the Darlington, the Darlington would be destroyed.
Thanks for your explanation.
The zener diode is not for turning ON the Darlington, it is for turning OFF the Dalington.
I understand that while the zener diode is turned ON, it might not help to keep the Darlinngton turned OFF, that is why I have replaced the zener diode with two BJTs in the improved version.
Ok, let me know your opinion on this, if the zener diode is shorted circuited, meaning if the base/emitter of the TIP147 are short circuited what would happen to the TIP147? Let me know about it.
By the way you can check out the new diagram here:
https://www.homemade-circuits.com/wp-content/uploads/2014/12/lossless-AC-to-DC-voltage-regulator-circuit-diagram.jpg
In regards to:
“[New Update] High Efficiency, Lossless Motorcycle Regulator Circuit”
I don’t follow the description on how the circuit is supposed to work. As I see it, it doesn’t at all and this is why:
Whether a pulsating rectified voltage is applied to the “input” of the circuit or a DC voltage that is increased slowly from 0 V to say 30 V for observation doesn’t matter, what happens is the same. As the voltage is increased, once sufficient voltage is developed across the base to emitter junction of the TIP 147, this being a darlington, this voltage will be approximately 1.4 volts, it turns on and begins to conduct. It’s base current flows through the 1 K resistor. As the input voltage increases further, eventually enough voltage is present to cause the 6A4 diode to conduct and collector current is delivered to the 1000uF capacitor and the load. Current is delivered to the load at input voltages of maybe 2.5 and above or so, satisfying the forward bias need of the TIP 147 and the 6A4 diode.
This condition of the TIP 147 conducting continues with increasing input voltage and increasing output voltage and current into the load. The voltage across the base to emitter junction does not rise much above the previously noted 1.4 volts, even for very high input voltages and output currents into the load. The 16 V Zener diode never comes into play at all. In fact, if 16 volts were ever developed across the Zener diode to cause it to conduct, this voltage would also have to be across the base to emitter junction of the TIP 147. If this has occurred, the TIP 147 would have been destroyed long before this.
A few minutes of work in a simulator should clear up the true functioning of the circuit, showing there is no regulation of any kind.
If I’m wrong, let me know why.
Here’s my explanation regarding the working of the first circuit on top (Lossless Motorcycle Regulator Circuit).
As long as the AC voltage waveform is higher than the zener breakdown voltage, the zener is conducting and allowing the full +supply to reach the base of the BJT, so now the base voltage of the BJT is equal to its emitter voltage.
This means the base/emitter voltage of the TIP142 is not 1.4V, rather it is 0V.
In this situation the TIP142 is not conducting and is switched OFF.
However, as soon as the AC supply waveform drops below the zener breakdown voltage, the zener turns off and cuts off the positive supply to the base of the BJT, which means at this instant the emitter voltage is higher than the base voltage of the BJT and is equal to 1.4V, which allows the BJT to turn ON fully and fill up the 1000uF capacitor, only until the waveform voltage yet again goes past the zener breakdown voltage and the BJT turns OFF.
Let me know if that makes sense or I am wrong?
Hallo! I did the first regulator, but stupidly used 5W zener instead of 1W. Now the regulator gives out approx 18V.
The alternator makes approximately ~70V. The lights are approx 60W. The battery is quite bad, but not absolutely dead.
Could it be healed with a different value resistor? Or should I definately get 1W zener? Or is it more likely I made some other undetected mistake?
Thank You and best wishes!
Hi, a 5 watt zener is better than a 1 watt zener for this circuit, so no problem at all with the zener power rating.
However, can you please tell me what is the output voltage that you are expecting from this circuit and how much is the voltage value of your zener diode?
Let me know this, I will try to figure it out for you!
Hallo!
Can the first “High Efficiency Lossless Regulator” be used without battery? Won’t it do any harm to alternator, to use this regulator without battery? The load will be approx 60-100W. The single fase alternator gave out approx 50-70V at modest revs.
Great many thanks!
Hello,
yes you can use the first circuit without any battery, directly with a load, just make sure to replace the 1000uF with a bigger capacitor, such as a 6800uF or bigger.
According to my assumptions, the circuit will not cause any harm to the alternator…
Hello!
I want to build this:
Simplest Regulator using TL431 IC
https://www.homemade-circuits.com/wp-content/uploads/2012/10/shunt-3.png
Does this have any shutdown function ?
Thanks,
Michael
Sure, you can try this circuit.
When the alternator voltage exceeds a certain voltage limit, it triggers the TL431 and the transistor causing a shunting of the alternator supply terminals which keeps the output supply to the intended regulated level.
Ok, thanks! I will try to use 10k trim pot. What can I add here to protect battery overcharge? the simpler the better 🙂 I use this in motorcycle (12V).
Thanks,
Michael
According to me, there’s no need to add an overcharge cut-off. If you restrict the alternator voltage to a maximum of 13.9 V for your 12V battery, then your battery will never reach the max over-charge level.
Oh yes, that is correct! This is very good, efficient charger. Reason I try to build my own that I have bought several general “motorbike rectifier voltage regulators” from aliexpress and local store and none of them have worked correctly. Usually at idle they output on DC side 7-8Volts which is too low of course and not charging the battery. I don’t understand why and you cant see because they’re filled with epoxy. Even simple AC-DC circuit that I have at home gives enough voltage at idle.
Thank you very much for these circuits!
Regards,
Michael
Yes, that’s correct, however, just make sure that when you build the suggested regulator design just make sure to also attach a 4700uF/50V or bigger capacitor after the bridge rectifier, to ensure that even at lower alternator voltages the battery is able to get an optimal supply for the charging process.
Hi!
Sorry, for me very hard to understand:
Regulators are mostly designed to charge battery with 14.4V – but lighting needs 12V. And the 14.4V is too much for lamps.
How can I feed lights properly with regulated 12V, if the regulator gives 14.4V?
(My moped has simple single phase generator. I will make Your High Efficiency, Lossless Motorcycle Regulator Circuit. Is it good choice for simple single phase moped?
Great many thanks!
Hi, you are right, and there’s a simple way to regulate the 14V or 13V to 12V for the lamps, by using the following circuit:
https://www.homemade-circuits.com/wp-content/uploads/2022/07/simple-voltage-regulator-circuit.jpg
Please replace the BC546 with TIP35, replace 4.7k with 100 ohm 1 watt, and the zener diode with a 12V 1 watt zener diode.
You can definitely try the first design for your single phase moped alternator, but please first confirm the working of the circuit on your work-bench, before the practical implementation…
Hi, thank You!
Which one of these would You rely Your life on?
There’s so many options it absolutely confuses me. Like in the middle of Sahara desert or Siberian taiga? Voltage regulator is a matter of life or death. As a bike chain, headlamp or brakes. Why not make the best one possible.
Thanks for the interesting question,
I would recommend the SCR version, by using BT151 SCRs, this one can be extremely rugged, suitable for all environments.
Hey! I’m putting together a circuit from the article “Shunting Excess Power to Ground is Recommended in Alternators”. My 3 phase DC motorcycle alternator gives 20A at peak. Can I use this circuit? And what is possible to replace the TIP142 with a higher power transistor ?
Sure, please go ahead! You can try this circuit for your 20 amp motorcycle alternator.
You can replace the BJT with a IRFZ44 MOSFET.
Also, please connect a suitable dummy load between the positive line and the MOSFET drain, so that the entire alternator supply is never shorted to ground, rather it is gracefully shunted through the dummy load. This load could a halogen lamp or a high watt resistor.
Let me know how it goes…
Hello,
I read this post because I am in the process of making my own 12V regulator to charge a 12V battery from a 6V single phase alternator (1979 Suzuki TS125 ER).
I still don’t understand the benefit of the shunt regulators as they basically short circuit the alternator when the voltage get too high, resulting in a higher current in the alternator winding.
Would it be more difficult to make a simple full bridge rectification to load a high tension capacitor and then just a step down voltage regulator (buck converter) to give the battery a constant tension feed (with a current limiting device if needed).
I would be real comfortable designing such a regulator (or purchasing it as a DC/DC 110/220V – 15V output module) operating on whatever tension will result at the main high voltage capacitor. Still I want to fully understand the consequences for the generating coil.
As far as high tension, I guess a disconnected output would not ruin the coil and it would be the highest voltage situation. I can see no heat excess beeing generated by reducing the current either… so a shunt regulator looks like a very inefficient system, wasting energy that the alternator has to supply.
Note, the original design works with NO regulation AT ALL as the lighting is 6V AC. In case the lights are turned off the current is sent to a resistor consuming about the same power in order to avoid overtension in the circuit and limit battery charging current (otherwise only regulated by a simple diode !)
Thank you for any comments
yVes Legrand
Hello, thanks for the valuable insights.
Yes, a shunt regulator for an alternator is inefficient but it provides a quick and a cheap solution to control excess voltage in alternators and prevent it from overtension in the absence of an output load.
If you have an arrangement where the the alternator output is diverted to an equivalent dummy load in the absence of an actual load then that’s the best way of solving the issue.
Yes buck converter can be employed for achieving a higher level of efficiency.
hi swagatam
i have built your regulator update version (top Schematic)
i change the PNP power transistor with 2T825B which current rate max around 20A
plus my 2 zeners configuration (series diode) should be on 13.8 Volt
but when i tested it just produce 2.6 VDC
do you have any suggestion for other part value (might need tobe changed,as my transistor is not TIP 147) to achieve my goal at 13.8 volt ?
Hi Andre,
Please convert the transistor into a Darlington by adding a 2N2222 transistor with your 2T825B.
Also, please try increasing the zener value a bit more, until you get the right output voltage.
Let me know how it goes.
This circuit was actually successfully tested by Mr. Ulya, you can read his comment under the following article:
https://www.homemade-circuits.com/cheap-yet-useful-transformerless-power/
Hi swagatam
I was very interested in circuits with tripping using MOSFET transistors. Especially that circuit with two phases from a generator with two bridges. This is on the Honda XR400R motorcycle. There, the generator is divided into 3 parts, these are the ignition winding, the power winding for the head lights and instruments, and the power winding for the sound signal. The last two can be combined by two bridges. But the windings are slightly different in the number of turns of wire and the thickness of the wire. What worries me is some imbalance in the operation if the rectified voltage is combined by bridges in front of the mosfet. And another electronics engineer friend said that an opening circuit with a mosfet on the alternator is quite dangerous, something needs to be done with induction, it can break through the windings with high voltage.
Thank you Michail,
You can connect separate bridge rectifiers for the separate winding of the alternator, and feed the output power to separate loads, through MOSFET regulators.
Let me know if you have any further doubts, I will try to help!
Hi swagatam
I am gonna build your new update schematic of simplest regulator
With addition of your LDO mosfet version few days ago
My goal is
I want voltage charging across my battery is 13.8 volt maximum (for longlive purpose) and passthrough another equipment through the 12 volt LDO mosfet version (as my led indicator,CDI,high lamp will be in 12 vdc)
Will it possible?
Hi Andre,
Yes that may be possible if your load’s total current consumption is less than 7 amps, otherwise you may have to replace the TIP147 with some other high current equivalent.
Here is the link for full of both schematic i wanna build
https://www.homemade-circuits.com/wp-content/uploads/2024/07/voltage-regulator-with-LDO.jpg
I need your suggestion before i buy the component
It looks good to me.
Please test the two stages separately first, and only then integrate together.
Hello Swagatam,
Thank for your very useful article. I have a question, have you or anyone using the Buck converter 10-90vdc to 1.5-60vdc after the rectifier (maybe a capacitor parallel to smooth the DC before the DC-dc buck convertor) instead of using these regulators? Thanks.
Hello Kisuf,
You can use a buck converter after a high voltage linear regulator so that the input voltage to buck converter does not exceed beyond its tolerable limits.
Connecting a buck converter directly to the output of an alternator may not be recommended.
As far as i know with buck is the input voltage need tobe fixed
For example with step-up buck
The input 10v the output will be 20v
But what happen when the input goes to 12v ?
Will the output stay at 20v or it will increase ?
In my case my input dinamycally change but still in range lavel let say 10-15 volt and i want the output stay fixed at 12v whatever input voltage will be, here buck doesnt suit my situation
I guess you are referring a boost converter?
The output voltage of a boost converter will remain fixed if it has a feedback controller circuit, otherwise the output will also increase as the input increases.
Hello people, I have basic knowledge of electronics and many years working with electronic regulators. I get a lot of results when I have to handle high currents in alternators, use SCR as a rectifier in positive output and you can see how to regulate the voltage peaks with it, while I use diodes for the negative. Greetings from Uruguay
Thank you Hamlet, for your valuable feedback…
can you make a series type regulator schematic
You can refer to this link:
https://www.homemade-circuits.com/simple-voltage-regulator-circuits-using-transistor-and-zener-diode/
Swagatam,
I’m trying to make sense of my new bike’s R/R , from the wiring diagram (Honda
CT 125 Trail 2024 with Shindengen 2-condenser / ac-dc Led control R/R). LED
h/l is energized from the ACG single phase negative half cycle , while the positive
half energizes the Battery charging part.
There are 2 thyristors , shown on Shindengen site , that contol the opening/closing of each of those 2 circuits , But no explanation as to the operations of the ‘Control
module ‘ that triggers the 2 thyristors….
From the Shindengen schematic alone , I cant figure it out.
How does thtat Control module ‘know’ that the ACG has entered any one of the two cycles , and switch the proper thyristor on ? ( as it can’t possibly rely on the 0V-
ground side for any valuable ‘signal” ???
Company says Mosfets are used , somewhere, but I see none on their online diagram..
Hmmmm
André , with rather basic electronics.
Hello Andre, I guess you may be referring to the following design:
https://www.homemade-circuits.com/wp-content/uploads/2024/03/Shindengen-schematic.jpg
I think the control circuit could be having opamps configured oppositely to detect the positive and the negative cycles and trigger the SCRs accordingly.
It seems there are other versions also which use MOSFETs.
Dear all. I am planning to build 3 phase 12 regulator rectifier for bajaj three wheeler. Can you suggest perfect regulator type with out cause early damage to stator windings. I have nearly open the old regulator and witnessed there is 6 SCR’s. But I didn’t found that type of rectifier circuits on line. Can you please help me to find correct type of regulator circuit diagram. Thanks all.
Hi, you can try the SCR version shown in the above article, or you can try the following concept:
https://www.homemade-circuits.com/wp-content/uploads/2012/10/shunt-3.png
Hi, I was searching for an early 80’s Yamaha voltage regulator schematic and found this site, which is quite impressive so thanks for your time in creating it.
So, the question is can you direct me towards anything on the Yamaha motorcycle version that used a field coil (rotor) with brushes and a stator to regulate the voltage? I have attempted to open a Yamaha regulator from an early 80’s XJ series hoping to see components but finding it impossible to remove whatever they used to encapsulate it.
Thanks in advance for any help you can give
Hi, Thanks, and glad you found the post useful. I think you can try one of the projects explained in the following article. It appears to be something in line with your requirement:
https://www.homemade-circuits.com/car-alternator-regulator-circuit/
is there an Open type circuit? I want to use open type regulator instead of shunt type. but in the market the price of the open type is very expensive (the model that I know). Several times I tried to make it (from diagrams on Google and YouTube), the results were not satisfactory (the head lamp slightly flickered/vibrated when idling and the speed was above 80kmph).
You can try the LM196 IC:
https://www.homemade-circuits.com/15v-10-amp-adjustable-voltage-regulator/
Hello. The information on this website is very useful. I also am interested in Open type circuit. However, it is complecated, and it is not recognized to have significant advantages compared to the shunt regulator. I personally believe that by changing the open-type regulator to a switching type, it improves fuel efficiency and stabilizes the output voltage, making it suitable for LifePo batteries.
So, Next time, I would like you to design it with an open-type. Also, please use ideal diodes for the rectifier. I look forward to it.
Hi, Thanks very much and Glad you found the post useful. I guess the open type regulator involves electromechanical relays. Since I am not an expert in mechanical systems it can be difficult for me to design this type of circuit, still if possible I will try to gather more info about it and post it soon.
Hello! Great post!
Im curious about the use of 555 to do PWM. This source: instructables.com/How-to-make-a-reliable-motorcycle-voltage-regulato/ seems to replace that whole section with a single zener diode.
To me it seems like this would acheive similar results, could you help me understand the benefit of each solution?
Hi, the 555 PWM allows you t adjust the average voltage output to the battery to the desired levels. In this way it becomes a kind of an adjustable voltage regulator.
Hi
Good morning
Any idea use simple circuit to on the motorcycle engine use of alternator and battery wise verse charging
With regards
Samm
Hi, sorry I did not understand your question….
Hi
Good morning
Now a days Honda use in scooter to start engine without starter motor use tha main alternater as starter motor a second,after than the alternator work as genarator,that company use ecm other circuit to use as,if any idea to use the common relay as such?
With regards
Hi, that looks quite complex, I have not yet seen how it works so I can’t figure it out.
Welcome have a nice day
That’s what happens when you judge something without understanding anything. The circuit will activate only once the alternator output voltage exceeds 15V, and then it will shunt or ground the excess voltage and safeguard the battery from overcharging. The battery voltage needs to reach only up to 14.5V max
I hope you have now learned how the circuit works.
Abstract: High voltage ignition coil driver power integrated circuit low dropout Text: Multifunctional Ignition and Injector Driver 33812 The 33812 is an engine control analog power IC intended, Relay that this IC supports. The Relay Driver and Injector Drivers are identical in operation and, ?? Designed to operate over the range of ~4.7 V a?¤ VPWR a?¤ 36 V 98ASA10556D a?? Fuel Injector driver -, RELAY OR OTHER LOAD INJECTOR VBAT VBAT +5 V IGNOUTH (DARLINGTON DRIVER SHOWN) IGNOUTL, Injector Parallel Input Logic Level input from the MCU to control the injector driver output 14
Hi With ref, to your Fet motorcycle regulator, the addition of the diode for protection to prevent the fet shorting the battery. you have failed to move the feed to the 1k resistor which feeds the 555 timer IC, and to move it to the battery side of the 10amp protection diode. I have built this and found this problem as I have realised that the timer will only be powered from the output of the rectifier. that is not good
Why it is not good if the 555 is powered from the rectifier? The rectifier current is appropriately dropped by the 1k and filtered by the 100uF, then subsequently stabilized by the FET/555 PWM
Hi, that looks much better, I think a fuse in line would also be recommended. my thoughts were if the device went short circuit or the duty cycle changed. then the fet would have been turned on hard and could fail short. at least this way it will only shunt the alternator output. I will try this now and protect the input and output with appropriate fuses in case of a component failure.
I will report back to you when it is complete. kindest regards Pete m
Sounds good! Let me know if you run into any problems!
Hi, Thankyou for your reply, The FET version still shows the transistor wired across the battery. this is not a good situation. as you will try and shunt several hundred amps to ground.
This will have a very dramatic effect, as the device and wiring will catch fire. the circuit needs to be changed or removed before someone who has limited experiance in electronics tries to build it. kindest regards Pete m
Hi, The danger that you are anticipating will not happen at 15 V, since the real voltage of the battery being around 12.8V, the excess voltage will be low in current and will quickly drop as soon as the MOSFET conducts. And as soon as the voltage drops below 15V or 14.5V the MOSFET conduction will terminate.
Still. to be entirely sure about the battery safety, you can add a diode in series with the battery positive as shown in the following image:
The original problem with this circuit was the fet was wired directly across the battery. this had been solved with a 10a diode in the Positive supply line, however this has also removed the regulated supply from the feed to the 555 timer.
moving the 1k from the drain of the fet to the other side of the diode would mean the 555 timer would be on all the time. so the 1k resistor would need to be fed from a switched supply. it would then drive the timer ic with a good flat dc supply.
Sorry still can’t figure out what issue you are referring to?
The 1k is not shifted anywhere, it is still connected with the drain of the FET. Th IC 555 will still be able to get the operating supply from the alternator, which will be stabilized by the 100uF cap and the FET PWM control…everything looks fine in the new design
Hi, My motorcycle regulators have been fine for 20 years on my Kawasaki Er5 too which I have two.
I have fitted the cheap regulators recommended when they were around £12 each. and they lasted only 3 years. now they want £70 or £80 for the same thing. and as they were not very good, I refuse to pay this price for such a basic piece of equipment. and as there is no guarantee of how long it will last. the current one is now only charging at 1 A which is not good when the lights are on.I was intregued with your circuits but I have one concern. The circuit that has the fet, wired directly across the battery. this could get very messy if it was to go short circuit. please let me know if this is an error in the drawing. kindest regards Pete M
Hi, thanks for pointing out the mistake, I have corrected the fault and have updated the new design for your reference.
I need avr circuit for car alternator that could control the output voltage by managing the voltage of rotor
Hello All,
I am trying to develop a 48V battery charging mechanism using car alternator. That would need modifications to be done to the alternator regulator and rectifier too.
Has anyone attempted this before? If so what are the modifications done?
If not, would anyone wish to join me in this R&D ?
hi mr. junior Namaskar I am shaily dubey from India. I have a Royal enfield bullet which head light run by generator. I want to make a ractifier and regulator unit for it. four wire( two wires purple color one orange and one is yellow) come from generator. there are two separate unit in my motor cycle one for battery charging and one for head light operation regulator which give ac current to headlight. I want to give 12 volt dc current to headlight for operating Led head lamp in my motorcycle So please suggest me that how can make a better RR unit for Royal Enfield.
With thanks
You can use the second last circuit from this article:
https://www.homemade-circuits.com/universal-high-watt-led-current-limiter/
make sure to connect a 6A4 diode in series with the positive line, and calculate the resistor values according to the head lamp specifications.
HI I want to build the second circuit that uses MOSFET and my alternator puts out around 90 volts at high RPM and I need a regulator that puts out around 15 at all RPM’s will the 555 timer circuit work the one that uses MOSFET like will it maintain a steady voltage?
Hi, yes it is supposed to maintain a steady voltage depending on the PWM adjustment, however the mosfet could get significantly hot, therefore a large heatsink will become mandatory for the application.
Hi Swagatam,
Forgot to mention that my DC generator is permanent magnet type. So i opine that the circuit built based on your last explanation should work perfectly i guess. Waiting for your expert suggestion please.
BR
Deepak
Hi Deepak, it doesn't make of a difference since the circuit will rectify any form of current applied across the bridge network according to me….whether it's a square wave signal sine wave signal or plain DC…all will be combined and presented across the (+) (-) output of the bridge
Dear Swagatam,
Your last explanation that states "PWM circuit could be corrected by replacing the three BJTs with a single powerful mosfet, and by connecting its drain/ source right across the output of the bridge network….this will solve the issue entirely" seems much simpler and sensible. Please update the design such that other members in this forum are also benefited. Thank you for your time and happy dipawali.
BR
Deepak
Hi Deepak, I have updated the new design for you and all the interested readers.
Happy Diwali to you too!!
Hi Swagatam,
In both circuit diagram, the alternator AC output is directly connected to transistor 3055 collector. Will transistor work on AC? or diodes needs to be connected in series in between?
BR
Deepak
Hi Deepak,
that's a good question, it seems I just missed this point (may be because it was referred from another site)….the transistors will act as half wave rectifier only, while the negative cycles will pass to the battery without processing
In that case I think the last diagram from the following article makes more sense and is much simpler which you can try instead
https://www.homemade-circuits.com/2012/10/motorcycle-full-wave-shunt-regulator.html
…the above PWM circuit could be corrected by replacing the three BJTs with a single powerful mosfet, and by connecting its drain/ source right across the output of the bridge network….this will solve the issue entirely. I'll try to update the modified design soon in the article…
Hi Swagatam,
Thanks for reply. I would be grateful if you could send the final working circuit made by Mr. AHMAD JAUHARI? My mail id is 'basanta.dhakhwa@gmail.com'. I have one more question. To handle the large current of 100A at 48V, i will need sizable capacity of both MOSFET and Diode right? So instead of using high amp MOSFET and power Diode, what if i use SCR which can be fired as required plus does the rectification at the same time. Please suggest.
BR
Deepak
Hi Deepak, All these circuits are perfect according to me, as you may see there's nothing complex or doubtful with their configuration, so please rest assured if you build them correctly and carefully these will work as per the expectations.
for 100 amps only the bridge diodes needs to be rated at much higher above 100 amps (with heatsink), other diodes are not relevant to the 100 amp current so those can be ordinary 1N4007 type.
SCRs are ideally high voltage low current devices, therefore not suitable for your application.
By the way here's another article which you can refer, you can try any of the last two designs for your need
https://www.homemade-circuits.com/2012/10/motorcycle-full-wave-shunt-regulator.html
…if you are using mosfet then please go through the earlier comments on top for knowing which parts can be eliminated for mosfets.
Hi Swagatam,
Can this circuit be used for 48V battery charging with charging current up to 100 Amps. I have a DC battery charging diesel generator and the regulator has gone faulty in it. I wish to build this circuit if it can be replacement for faulty unit. Kindly please advise. And yes i want to use MOSFET instead of BJT for handling high current. Thank you.
BR
Deepak
Hi Deepak, yes definitely you can use it for your a 100 amp application by replacing the BJTs with high power mosfets capable of handling over 120 amps…and mounting them on large heatsinks.
Hi Deepak
First of all, please clarify what is the type of the generator i.e. Permanent Magnet type or Field Coil Type. Both have different circuits.
Deepak
As requested earlier, you should clarify the type of the generator you have. The above circuits are suitable only for a 3-Phase, Permanent Magnet Generator. If it is single phase Permanent Magnet Generator or Field Coil Generator then the regulators circuits would be different. This information is important so that anybody helping you will guide you on the correct track and of course, save time.
Hello.
Can I use your design for a two-phase alternator that is grounded to the engine?
Thanks
yes you can use it for the mentioned application
Sure, but how can I post the image? can I just email the final schematic to Swagatam sir?
yes you can send it though email or upload it in any free image hosting site and provide the link here, whichever is more convenient for you
My email is admin (@) http://www.homemade-circuits.com
My email is abuhafss@hotmail.com
You may send email to Swagatam and cc me. Or Swagatam can forward me your image.
alright then, I will sketch it in eagle this weekend and upload it afterwards
IS it possible to get schematics for me too? my email jurgis.lipsnis (@) gmail.com
Ahmad Jauhari
It has been almost 2 months, I could not get your final schematics. Perhaps you or Swagatam forgot to forward to me.
Hi Swagatam,
Sorry to take long time to post again, so I finally got it working. It turned out I miss connecting the output from the alternator to bridge pins, that's why it looked like it is not working. Now the output voltage measured is maintained at 15V max throughout engine RPM range and it is able to deliver 3A of current at 1K RPM, very nice design.
I do have something in mind i would like to ask.
1. Is the 47K preset value is crucial in the design, because I cant't find any 47K trimpot right now. So I'm using a 50K trimpot instead of 47K, is that okay? the final result is fine thou.
2. What is the main consideration of using 1 ohm resistor between emitter and ground of the BJTs, can I remove it if using a mosfets?
Thanks
Joe
That's wonderful Ahmad, thanks for updating the info!
1) the 47K preset is not critical, in fact I have approximately assumed the value with respect to the 10K on the upper side….you can use any other value ranging from 22K to 100K
The 1 Ohm is related to the max current handling capacity of the transistors, it's for safeguarding the transistors from getting completely shorted with ground.
You can use Ohm's law for determining them for your transistors as per their max current rating.
If the rating of the mosfets is greater than the alternator max current generating capacity, then it those resistors can be eliminated
Ahmed Jauhri
Would you please post the final schematic which work for you.
Thanks in advance.
i already make circuit as you finally design,test without load and battery but mosfet IRF540 is relay hot…..is there something missing in this design?? i try to regulate pwm with turning 100k pot but is the same result
MOSFET will become hot because it is shorting the excess power to ground. You should check the DC voltage at pin3 of the IC while adjusting the PWM. Check whether the DC is varying from almost 0 V to full supply voltage in response to PWM adjustments…if not then your PWM is not working.
Connect the mosfet on a large heatsink to prevent over heating.
Hi sir thank you for your wonderful design,
I am just concern if how can it be possible
if i use an arduino mcu instead of 555 and what is the possible connection?
Can I also use optocoupler to isolate the supply to arduino? TIA
Hi Em, thanks!
you can replace the pin#3 output line with your Arduino output for achieving the same results.
an opto coupler can be used.
Thank you very much sir,
can i also used the part where you placed a zener diode?
can I replace it by an arduino port so i can manage and fixed the output voltage? thanks 🙂
yes that's definitely possible, you can do it.
but the opamp will provide around 12V output voltage swing with R1 = 10K (in the mentioned circuit), right?
I don't realy sure about that short circuiting an alternator output could be equivalent to an open circuit as it is always brings down the engine rpm whenever I manualy short circuiting the output leads. I haven't had time and proper equipment to investigate it thou
yes when the opamp output is triggered high, the alternator is shunted to ground which switches OFF the opamp, and this ON/OFF switching continues rapidly sustaining a constant preferred voltage across the output
right, open circuit means no current flowing while short circuit means full current flowing and shunted, how can both these conditions produce identical results? that does not make any sense
from what I get from the article, there's some sort of magnetic field created during shunting process which cancels the magnetic field from the permanent magnets thus no voltage generated in the stator. it could be true of false, need to prove it thou
Not sure at the moment, I'll have to diagnose deep into alternator working specs to actually confirm the facts.
Hi, can I use the schematic for shunting 2 alternator output in the same connection. I have alternator with stacked windings, that is another winding on top of first windings so I have 2 set of pole in one alternator
Hi, I am not quite sure about it, if it matches the shown the three phase winding then probably you can try configuring them in that manner and see the effect
Hi, you did mention the transistor can use IRF540 instead of shown BJTs. I'm a bit confused with instruction on place 1K resistor across gate and ground, can you email me simple illustration on how to do this (1K resistor placement). And where should the G D S pins go in the shown schematic, I really need to build this regulator as my RR always failing (dunno why but I suspect due to high operational temp from the RR itself in such a confined space. wewh)
It is not difficult, just replace the D with the collector, G with the base, and S with the emitter of the existing BJTs.
connect 1K across all the G and S of all the fets. the 100 ohm from the 555 pin3 can be eliminated and pin3 directly connected with the diodes (optional though)
is the diodes at the G pins still required or it's okay to omit it.
I'm planning to build it this weekend, I will keep you posted for the result on my configuration
I think the diodes could be eliminated, and the gates joined together with pin3 of the IC, and in that case you could even skip the recommended 1K resistors across G and S of the fets, those won't be required now.
If the mosfet replaced with IRF840, is the component values still the same or is it have to be modified again? my seller sent me the wrong mosfet, he sent me IRF840 instead of IRF540. Will the IRF540 survive with slightly higher voltage on high rpms? I'm reading 100-110 volts in high rpm in open circuits AC.
About the stator current measurement, I cant read the amperage with 2 probe type multimeter. It's reading zero but the resistor connected between one of the probe and stator lead is getting hot (1.2 ohm 5 watt). Connecting the probes directly to the leads also can't have fixed reading, briefly connecting and disconnecting the the probes do have some reading and the engine getting slightly stalled when the probes connected directly to the leads.
no changes would be required in the circuit even with an IRF840…
you can use the same circuit…you can try using a moving coil type meter and add a shunt resistor across its terminals for measuring the alternator current. this shunt resistor value and the meter reading together can be calculated for understanding the approximate current from the alternator.
for your present meter it should be in the AC range for reading the current
Hi, I have built the circuit in a bread board and tested it. But it's not working as expected. Maximum voltage regulated is only about 10v at peak 10K rpm, it should be about 100v at peak rpm when not connected to anything.
I tried to check if the PWM function is working by connecting a light bulb to one of the mosfet and it is not conducting in response of the pwm adjust trimpot, the bulb is dimly lit on one full side of trimpot and fully off on the other side. While the other mosfet is like alwas conducting no matter how much I turn the trimpot (the bulb is lit dimly thou).
What did i do wrong with the circuit, is this type of shunting not suitable for this, is it better to use the SCR version of regulator?
I'm pretty much confused now
I think your 555 circuit is not working or has some fault, you can check it separately with a bulb across its pin3 and ground…and by increasing the 10nF capacitor to 100uF, this will slow down the frequency and allow you to see the bulb illumination period in response to the PwM pot setting clearly.
because if the PWM works then the transistors will conduct according to its dutycycle and control the alternator current accordingly.
By the way I also have two more similar concepts using SCRs and a single mosfet which you can refer to through the search box.
It could be the 555 circuit, I will check the circuit again this weekend or next week after ramadhan is over.
The one using mosfet have updated diagram which use BJT instead of mosfet, can I just replace the BJT with a mosfet?
Actually I'm much more interested building the one with the SCR as it is a parallel type regulation and it will prevent the stator from creating very high voltage. What modification should be made if I want to use mosfet instead of scr, It's more efficient and less heat generated in the mosfet (i think)
check out this link below, it tells a story about shunting permanent magnet alternator (most motorcyle is using this type of alternator)
http://www.apriliaforum.com/forums/showthread.php?240785-Facts-about-shunt-based-regulators
Mosfet is good because these are designed to handle high current and lower voltages whereas SCRs are opposite with their specs. Since for a motorcycle alternator the voltage gets restricted to 14V but current is much higher, therefore mosfets look a better option.
However in the linked article, the following line looks controversial:
"Shorting stator coils yields the same behavior of magnetic drag (magnetic reluctance) as open circuiting them, thus no Power is consumed and no drag is felt"
by the way you can try the last circuit from this article, you can replace the BJT with a mosfet, but remember the minimum optimal triggering gate voltage is 10V :
https://www.homemade-circuits.com/2012/10/motorcycle-full-wave-shunt-regulator.html
How can a short circuited alternator output could be equivalent to an open circuit output??
Can 7812 ic handle the power from alternator after rectifier? When the engine start i measure the output voltage of alternator is 14volt AC. Anyway I'll try to do your suggestion.
if the supply is a rectified DC and is below 35V then the 7812 will be able to handle it easily, because here the load is a 555 iC circuit whose requirement is not more than 50mA
Julian, the IC is to be connected with an attached battery…if you connect it with an alternator directly then obviously it will blow off.
alternatively you can try using a 7812 IC regulator between the 555 supply and the alternator or the battery.
Sir, I've tried this circuit. Pwm ic 555 exploded when linked to the alternator and the engine started, what's the problem? pins 4 and 8 on my pcb circuit connect directly to the 3 phase diode cathode. Im using TIP 35 for transistor. Thanks for your help.
Interesting circuit, thanks for sharing. However, I'm not sure if the regulator would work since the alternator works from 1,000RPM to 10,000RPM, hence the frequency of the AC signal is not constant, therefore the PWM signal would not switch the power BJT on time in the whole alternator bandwidth. Also, how can the PWM signal control the average output voltage if you do not have a zero cross detection circuit?
Instead of the 555, I would rather recommend an MCU to add zero cross detection and auto regulated output voltage across the entire alternator bandwidth.
the above circuit allows a safe maximum voltage to be set for the battery, it's not meant to stabilize the voltage, here the shunting of the excess voltage is adjustable as preferred by the user and controls the excess voltage above the set value from entering the battery.
a filter capacitor and an LM196 stage can be added after the bridge in case extreme stabilization is required.
Thanks for the reply.
Could you please explain how the user can adjust the shunting of the excess voltage?
Please correct me if I'm wrong: the 100K trimpot adjusts the duty cycle of the PWM signal, which triggers the TIP3055 and sends _part_ of the sine wave generated signal to ground. Nevertheless, the adjustment would not work for the entire generator bandwidth, since the PWM signal does not change its frequency. The output voltage should be set at 14.5v to properly charge the battery, however the load also changes if the battery is charged or discharged, turning on and off the headlight would also change the load. A motorcycle voltage regulator should keep the voltage within 13.5v and 14.5v at any given engine RPM.
Please be as detailed as possible in your explanation, I would really like to understand your design, since I'm struggling to design a voltage regulator circuit for permanent magnet motorcycle generator (the one used here).
Thanks again.
as I mentioned in the earlier comment the circuit is not designed to produce a constant voltage across the battery terminals, it's designed only to allow the user to choose how much voltage and current needs to be shorted or shunted to ground…this shunting magnitude is variable through the 100K pot.
frequency parameter is immaterial here…rather the pulse widths decide for much long the transistors need to conduct and short the alternator power to ground which in turn determines how much average voltage is allowed to reach the battery for a safe charging.
The second circuit is even more sophisticated as it ensures that a peak voltage not higher than the zener diode value is allowed to reach across the battery terminals under any circumstances.
Hi Mr. Swagatam.
I am newbie on electronics.
Can you explain further how to adjust the PWM pot at the circuit of battery charger above? TIA.
Hi Tia, the PWM decides the average output voltage across the bridge rectifier.
so you can measure the output voltage with a volt meter and simultaneously adjust the PWM pot until the right voltage reading is achieved….
Dear Sir
If we use MOSFET instead of BJT what is the mosfet part number. And what are modifications to do. I'm going to build this circuit because my bike's R/R fails every time and have to charge the battery manually. I thank you very much for your help.
Dear Prabuddha, you can try IRF540 instead of the shown BJTs.
only one change will be required in the circuit, you'll need to put resistors across the gate and ground of each mosfet, the values could be 1K for these resistors
Dear Sir
Do we need to use a heat sink for this circuit ?
first try without heatsink, if you see the transistors getting considerably warm in that case you can think of putting separate heatsinks for all three of them
Dear Sir
Could you please supply a rectifier circuit with detailed part numbers because my bike rectifier and regulator comes as a single unit
Thank you
Dear Prabuddha, you can use 1N5408 and build the rectifier section as shown in the above diagram.
I doubt if 6 x 1N5408 would do the job because they are just 3A diodes. Depending on the electrical system of a bike, they should be capable of bearing at least 10A. And according to my experience the rectifier section needs a good heatsink.
ola ,poderia converter esse circuito para usar o mosfet irfp260n
yes it's possible just make sure each mosfet includes a 470 ohm resistor across their gate/source terminals
could convert this circuit using your tip for mosfet ??
sorry i did not understand..
Hi Swagatam
How will this circuit regulate the battery charging voltage? The transistors should shunt when the input voltage reaches the threshold voltage, particularly 14.4 – 14.7V.
Thanks Abu-Hafss,
I have updated the modified diagram with a peak voltage regulation feature, please check it out.
Hi Swagatam,
Does a FDA20N50F works and may be plug and play to replace IRF540 ?
Which is the best schematic, the one with just 1 mosfet or the one with 1 mosfet by phase ?
Best regards,
Phil
Hi Phil, did you compare the IDS and VDS of the two mosfets? If they both match with each other approximately, then you can replace them with each other…
The following circuit is the recommended one according to me:
https://www.homemade-circuits.com/wp-content/uploads/2020/09/bike-alternator-shunt.jpg
Thanks for your reply Swagatam,
Could you tell me the capacitor value between the legs 1 and 5 of the 555?
Why do you use a 15V and not a 12V zener diode to the base of the BC547?
What capacitor technology do you advise for this rather rough application due to the high temperature?
I think that those of 100 µF don’t leave much choices than electrolytic or tantalum which may be the weak point of your schematic.
No problem Phil, the capacitor at pin#5 is 0.01uF.
15V zener is used so the 12V battery is able to get the required 14.3V correctly.
Capacitor breakdown strength is determined by their voltage rating which can be 1.5 times more than the maximum voltage applied against them….so any type of capacitor will work as long as the voltage rating is adequately selected….the rule is same for the electrolytic caps also…