In this article I will explain a step by step tutorial regarding designing your own homemade basic induction heater circuit, which can be also used as an induction cooktop.
Basic Induction Heater Concept
You might have come across many DIY induction heater circuits online but nobody seem to have addressed the crucial secret behind implementing a perfect and a successful induction heater design. Before knowing this secret it would be important to know the basic working concept of an induction heater.
An induction heater is actually an extremely "inefficient" form of electrical transformer, and this inefficiency becomes its main advantageous feature.
We know that in an electrical transformer the core needs to be compatible with the induced frequency, and when there's an incompatibility between frequency and the core material in a transformer, it results in the generation of heat.
Fundamentally an iron cored transformer will require a lower range of frequency around 50 to 100Hz, and as this frequency is increased the core may shown a tendency of getting hotter proportionately. That implies, if the frequency is increased to a much higher level may be over 100kHz would result in the generation of extreme heat within the core.
Yes, this is exactly what happens with an induction heater system where the cooktop acts like the core and therefore is made up of iron material. And the induction coil is subjected to a high frequency, together this results in the generation of a proportionately intense amount of heat on the vessel. Since the frequency is optimized at significantly high level ensures a maximum possible heat on the metal.
Now let's proceed and learn the important aspects that may be required for designing a successful and technically correct Induction heater circuit. The following details will explain this:
What you will Need
The two bare basic things required for building any induction cookware are:
1) A bifilar coil.
2) An adjustable frequency generator circuit
I have already discussed a few induction heater circuits in this website, you can read them below:
Solar Induction Heater Circuit
Induction Heater Circuit Using IGBT
Simple Induction Heater Circuit - Hot Plate Cooker Circuit
Small Induction Heater Circuit for School Project
All the above links have the above two things in common, that is they have a work coil and a driver oscillator stage.
Designing the Work Coil
For designing an induction cookware, the work coil is supposed to be flat in nature, therefore it must be bifilar type with its configuration, as shown below:
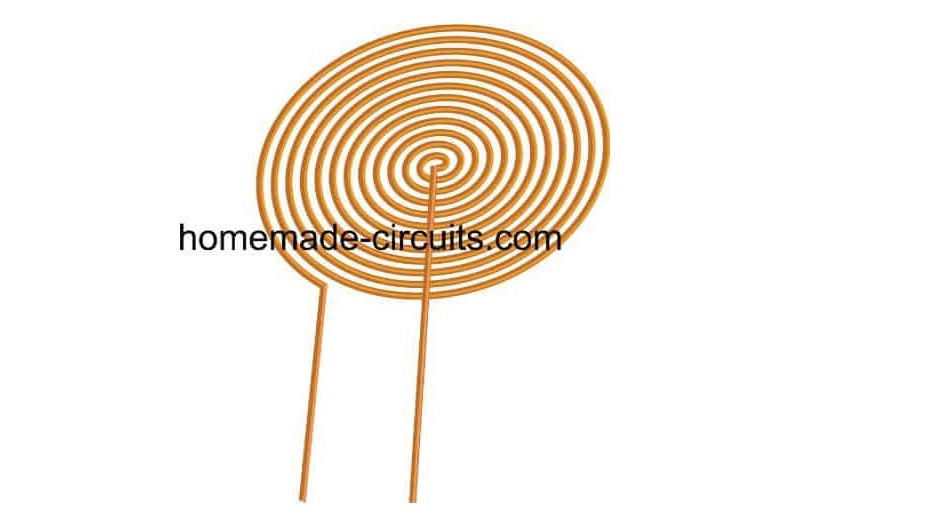
The bifilar coil type design shown above can be effectively implemented for making your homemade induction cookware.
For optimum response and low heat generation within the coil make sure the wire of the bifilar coil is made using many thin strands of copper instead of a single solid wire.
Thus, this becomes the work coil of the cookware, now the ends of this coil simply needs to be integrated with a matching capacitor and a compatible frequency driver network, as shown in the following figure:
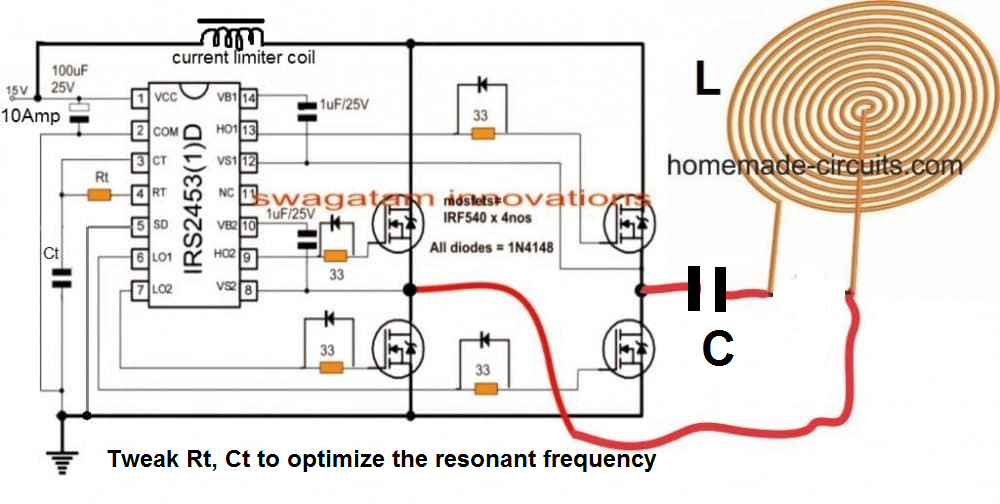
Parts List
- 33 Ohms 1/4 watt 5% = 4 nos
- Rt = To be determined by experimentation.
- 1uF/25V Electrolytic = 2 nos
- 100uF/25V Electrolytic = 1 no
- Ct and C = To be determined by experimentation.
- 1N4148 diodes = 4 nos
- MOSFETs IRF540 = 4 nos
- IC IRS2453 = 1 no
- Work Coil = As shown in the diagram. Diameter will need to be experimented.
- Current limiting Inductor = Can be between 1 mH to 5 mH. Again this one will need to be experimented.
- While experimenting the unknown components make sure to use a 12 V, 50 watt watt bulb in series with the DC supply line, to avoid accidental damage to the MOSFETs.
Designing the H-Bridge Series Resonant Driver Circuit
So far the information should have enlightened you regarding how to configure a simple induction cookware or an induction cooktop design, however the most critical part of the design is how to resonate the coil capacitor network (the tank circuit) into the most optimal range so that the circuit works at the most efficient level.
Enabling the coil/capacitor tank circuit (LC circuit) to operate at their resonance level requires the inductance of the coil and the capacitance of the capacitor to be matched perfectly.
This can happen only when the reactance of both the counterparts are identical, that is the reactance of the coil (inductor) as well as the capacitor are approximately the same.
Once this is fixed you can expect the tank circuit to operate at its natural frequency and the LC network reaching the resonance point. This is called a perfectly tuned LC circuit.
This concludes the basic induction heater circuit designing procedures
You may be wondering regarding what is resonance of an LC circuit.?? And how this may be calculated quickly for completing a specific induction heater design? We will comprehensively discuss this in the following sections.
The above paragraphs explained the fundamental secrets behind developing a low cost yet effective induction cooktop at home, in the following descriptions we will see how this can be implemented by specifically calculating its crucial parameters such the resonance of its tuned LC circuit and the correct dimension of the coil wire for ensuring an optimal current handling capacity.
What is Resonance in Induction Heater LC Circuit
When the capacitor within a tuned LC circuit is momentarily charged, the capacitor tries to discharge and dump the accumulated charge over the coil, the coil accepts the charge and stores the charge in the form of magnetic field. But as soon as the capacitor has discharged in the process, the coil develops an almost equivalent amount of charge in the form of magnetic field and it now tries to force this back inside the capacitor, although with an opposite polarity.
Image courtesy:

The capacitor is again forced to charge but this time in the opposite direction, and as soon as it's fully charged, it yet again tries to empty itself across the coil, and this results in a back and forth sharing of charge in the form of an oscillating current across the LC network.
The frequency of this oscillating current becomes the resonance frequency of the tuned LC circuit.
However due to inherent losses the above oscillations eventually die out in the course of time, and the frequency, the charge all come to an end after sometime.
But if the frequency is allowed to sustain through an external frequency input, tuned at the same resonance level, then that could ensure a permanent resonance effect being induced across the LC circuit.
At resonance frequency we can expect the amplitude of the voltage oscillating across the LC circuit to be at the maximum level, resulting in the most efficient induction.
Therefore we can imply that, to implement a perfect resonance within an LC network for an induction heater design we need to ensure the following crucial parameters:
1) A tuned LC circuit
2) And a matching frequency to sustain the LC circuit resonance.
This can be calculated using the following simple formula:
F = 1 ÷ 2π x √LC
where L is in Henry and C is in Farad
If you don't want to go through the hassles of calculating the resonance of the coil LC tank through formula, a much simpler option could be to use the following software:
LC Resonant Frequency Calculator
Or you may also build this Grid dip meter for identifying and setting the resonance frequency.
Once the resonance frequency is identified, it's time to set the full-bridge IC with this resonance frequency by suitably selecting the Rt, and Ct timing components. This may be done by some trial and error through practical measurements, or through the following formula:
The following formula can be used for calculating the values of Rt/Ct:
f = 1/1.453 x Rt x Ct where Rt is in Ohms and Ct in Farads.
Using Series Resonance
The induction heater concept discussed in this post uses a series resonant circuit.
When a series resonant LC circuit is employed, we have inductor an (L) and a capacitor (C) connected in series, as shown in the following diagram.
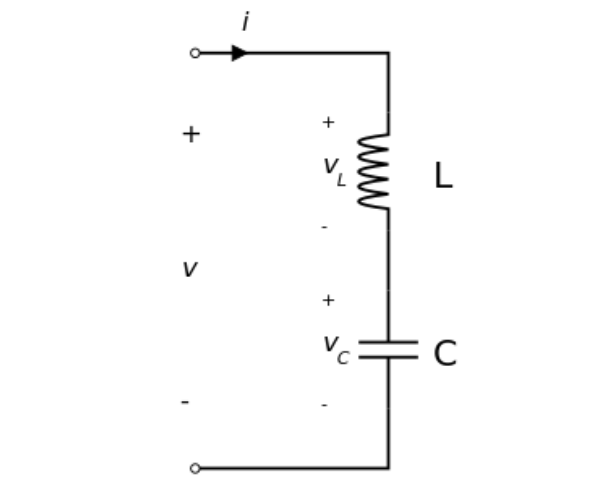
The total voltage V applied across the series LC will be the sum of the voltage across the inductor L and the voltage across the capacitor C. The current flowing through the system will be equal to the current that's flowing through the L and the C components.
V = VL + VC
I = IL = IC
The frequency of the applied voltage affects the reactances of the inductor and the capacitor. As frequency is increased from a minimum value to a higher value, the inductive reactance XL of the inductor will proportionately increase, but XC which is the capacitive reactance will decrease.
However, while the frequency is being increased there will be a particular instance or threshold when the magnitudes of the inductive reactance and the capacitive reactance will be just equal. This instance will be the resonant point of the series LC, and the frequency can be set as the resonant frequency.
Therefore, in a series resonant circuit, the resonance will occur when
XL = XC
or, ωL = 1 / ωC
where ω = angular frequency.
Evaluating the value of ω gives us:
ω = ωo = 1 / √ LC, which is defined as the resonant angular frequency.
Substituting this in the previous equation and also converting the angular frequency (in radians per second) into frequency (Hz), we finally get:
fo = ωo / 2π = 1 / 2π√ LC
fo = 1 / 2π√ LC
Calculating Wire Size for Induction Heater Work Coil
Once you have calculated the optimized values of L and C for the tank circuit of the induction heater and evaluated the exact compatible frequency for the driver circuit, it's time to calculate and fix the current handling capacity of the work coil and the capacitor.
Since the current involved within an induction heater design could be substantially large, this parameter cannot be ignored and must be correctly assigned to the LC circuit.
Using formulas for calculating wire sizes for an Induction wire size may be a little difficult especially for the newcomers, and that's exactly why a special software for the same has been enabled in this site, which any interested hobbyist can use to dimension the right size wire for your induction cooktop circuit.
Hi Swagatam;
I have a hair dryer core heating resistor as known there are double resistors spring / coils and a thermal fuse. Multimeter shows the resistor value as about 35 Ohm.
And also 0.22 uF capacitor is connected between mains. And shunt resistor on the capacitor is 1M Ohm.
I assume that it is about 1500 Watts. I would like to convert it to hot air soldering gun but removing the thermal fuse and adding a strong enough dimmer circuit at first.
So I need your support / opinion accordingly.
Best Wishes.
Hi Suat,
Yes you can connect the load with a light dimmer circuit rated to handle 20 amps or above.
You can refer to the following post for the circuit designs:
220V Light Dimmer and Ceiling fan Regulator Circuit [Using Triac and Diac]
I am grateful for the support however to your opinion it is possible to say that hair dryer resistor absolutely would be efficient to some extent of melting the solder?
Best Wishes
You are welcome Suat, yes ,
if the hair dryer temperature is able to reach above 200 degrees Celsius, and if the hot breeze is held very close to the solder then definitely it will be enough to melt the solder
Hi
Apologies for a potentially dumb question that’s more ‘weird idea confirmation’ than technical. I hope it’s ok and that you can help. I’ve a potential use case for induction heating. I’ll have a long, thin piece to be heated (a cylinder approx 120-150mm by 3mm). The induction coil will necessarily be somewhat elliptical and orientated such that its coil is in line with the piece to be heated (long axes aligned) and separated by approx 30-50mm.
If (by some miracle) I’ve made this all clear enough to understand, is it even realistically possible to controllably heat the piece? Will the distance and orientation of the piece to coil make it impractical?
Thank you so much for any input you can give. I very much appreciate your taking the time to help out.
Hi, the material to be heated will need to be placed inside the induction coil, and not outside. If you place it outside the coil then it won’t heat up optimally. Otherwise there are no issues for heating the element. To have a controlled heating you will need to control the current input to the induction heater from an external source.
Thank you for that. Yes, the material to be heated will be inside the coil, just separated from it by around 40mm. I just wanted to get a feel for the feasibility of heating a long(ish), thin piece from that distance without some industrial-scale hardware. ???? Didn’t want to embark on a project that was doomed to failure. Thanks again.
No problem, the intended longish metal can be heated using conventional induction heater circuits.
Thank you again. ????
Hello ! I would like to recreate this heater for my end-of-semester project. May I know all the materials that were used for the circuit?
Hi, I have added the parts list under the circuit diagram. However, please note that the above design has not been verified by me practically, so please proceed only if you have understood the concept perfectly and are confident about its working.
Hello
my induction cooker at home is 1200watts. I want to modify the same for 200watts.
How to do?
Hi,
You simply have to reduce the input current from the power supply so that only 200 watts can reach the induction heater.
Hello
to reduce current I have to reduce the DC voltage . Now it is 330V DC. What will be the best method with minimum loss to reduce it to say 100V DC ? By using mosfet switching ; I see loss of power which is not acceptable. If it can be done without power loss ?
thanks
Yes a PWM switching can help to reduce the output current to the desired lower limits. You can use a 555 IC and mosfet based PWM switching.
The circuit from the following article can be tried. You will have to replace the mosfet with a 500V mosfet, and supply the 555 circuit with a separate 12V Dc. The lamp can be replaced with the induction heater.
https://www.homemade-circuits.com/dc-lamp-dimmer-circuit-using-ic-555/
It was very nice and How can i make it my self
Thank you, the easiest way to make is to buy a ready made unit and learn the concept and then replicate the parts.
Thank you so much.
So, how to find a solution in this circuit to solve this problem.(in case of very high voltage on resonant coil and capacitor). Is the purpose of the diodes and current limiter coil in this circuit to prevent this?
Also my second question, how can we decide whether the inductance of the current-limiting coil in your circuit, Should it be equal to the coil in the load or how many Henrys this coil should be?
Thanks in advance.
I have only presented an experimental design. The exact values of the coils and the capacitors are unknown and will need to be found through experimentation.
For current limiting you an modify the Ct of the IC through a BC547 transistor as shown in the following diagram:
https://www.homemade-circuits.com/wp-content/uploads/2021/12/h-bridge-induction-heater.jpg
Hello , I have three question. Please could you answer these?
How many mh is the coil you used in this load?
And the impedance increasing with high frequency that you apply on the coil and capacitor , does not damage the mosfets and the driver? How did you prevent this?
And if we connect the pwm generator from the outside, what kind of change should we make in the circuit?
The coil mH is not known, you will have to experiment it with some trial and error. You can use a 200 watt bulb in series while testing which will ensure that as long as the resonance point is not found the bulb absorbs all the current and prevents the mosfets from burning. As soon as the resonance point is hit the lamp illumination must decrease and fade out, indicating that the resonance has been achieved. Adding pwm will be a complex thing but you can do that by chopping the low side mosfet gates.
The damage to the mosfets can be also prevented by using a current controlled input power supply, whose current must be lower than the mosfet’s maximum handling capacity.
Thank you for your answers.
For example, 5 kw(2500 (wl) empedance and 2A) load occurs on the resonant coil and resonant capacitor , does this affect the other side of the circuit(mosfet side ) ?Because in resonance total empedance is very low , so we can drive 2a to coil with low power (maybe with 250W).
As the load increases the resonance effect will tend to get weaker due to lack of current and then the mosfets will have to pump the resonance effect by supplying more current to the LC circuit, in this way the mosfets will be affected and will need to maintain the required amount of current to the LC circuit to sustain the resonance effect.
Hello again, Can the coil and the transistor series resonate with the pwm produced by driver?
Shouldn’t there be ac voltage in the circuit for resonance? Or , Can this resonance be achieved with PWM and DC supply?
Hi, there’s no PWM here, only rectangle wave frequency from the IC which can be adjusted by adjusting Rt, Ct values. The output across the coil and capacitor will be AC since the mosfets are arranged in a full bridge network
Sir I will be highly obliged if you can kindly send me the electronic diagram of induction heater . Thanks in advance
Kayomarz, you can find the diagram in the following link:
https://www.homemade-circuits.com/simple-induction-heater-circuit-hot/
Thankyou Mr Swagatam
You are welcome Kayomarz.
what would be best way to build 500 watt induction coil in 120mmby 80 mm size pancake form? Should we use two coils or 24 coils in 20mm dia all in series to get uniform heating ?
Designing induction heater coil will require a lot of calculations, or it can be done by checking a ready-made induction heater….judging the coil specs manually may not be possible.
Sir plz tell me how measure calayand indutor value and work coils turn and also tell how use igbt
hello, first of all I liked your article very much, it is very descriptive, I need a controlled induction circuit, for example I want 4 stages as 500w-1000w-1500w-2000w, how can I do it, can you design it for me, thank you very much in advance.
Thank you, glad you liked it. Designing a working prototype of your project might require practical checking and verification, which can be quite difficult, and cannot be done theoretically.
Swagatam,
Looking for a PCB designer and manufacturer who can produce a simple coil circuit for Interra Sciences.
Please email me at
Can send photo of the prototype circuit if you send your email.
Thanks,
David Newman
Hello David, I do not have a PCB designer with me at the moment, if I find one will surely let you know…
Thanks for the quick reply Swagatam.
DN
Hello Swagatam ; Hope that you are fine.
Suppose my solar panel voltage varies from 6V to 20V and I want to charge my 12V Ld-acd battery. I want to go-cheap and not using solar charger and instead I have to use some buck and boost DC DC converter. 2596 module is for BUCK and XL6009 for BOOST. There are some both buck-boost module but costly and equivalent to charger. So if I connect 2596 and 6009 both in paralle with diodes in output ? What is your idea?
thanks
Let us be happy with all odds of life!!
Hello Jayant, I will surely try to solve your query but only if you ask the question under a relevant article. The above article is about induction heater, and you are asking about solar charger.
Please put your question under a solar charger or battery charge article, I will try to help
Hi swagatam
I got your blogging site impressive..your descriptive content abt induction heating is helpful.we are an induction based company in pune
We need your practical consultation in our company.I also mailed u.plz revert back.
Thank you Zahid, I appreciate your interest and truly wish I could provide my consultations, however due to work pressure and lack of time it may not be possible for me at this moment of time.
Dear Swagtam, I decide to give 60V from solar panel direct supply to IR2153 . I think pin-1 needs some 5-20mA current. I see that people use 33k for 320V input. For 60V it should be then nearly 6K. Do you think it is OK? Calculation can be like R= ( V – 15.4 )/ 10mA. Let me choose some 10mA for internal supply.
OK
Hope you fine
thanks
Hi Jayant, Your calculation is correct, you can use 6K for the purpose!
Hello swagatam
what I think 7812 is a linear device.Hence low efficiency. Instead we can also use
PWM devices like LM2596 module with 92% efficiency or more. Direct supply with resistor also fine.
Hope you fine
J K
Hello Jayant, I think a high value resistor is all that is required for optimal working of the IC. A PWM circuit will be an overkill and may not be necessary.
Thanks for a prompt answer.
For direct supply to IR2153 ; We have to put resistance and it will eat some power say 1/2 to 1 watt max.
same thing happening at LM7812. Any how we have to sacrifice some but very little power. No problem ! it is accepted.
Thanks
God bless you
You are correct, however,I think we can increase the value of resistor to a level where the heat is minimum.
Hello ; hope you fine.
I find that in your circuit for induction heater using IRS2153 your solar volatge is 24V and you are using LM7812 to supply 12V to IR2153. It can bear upto 600V . Then why not to supply 24V directly ? There will be loss in LM7812. I think it is not required. Am I right?
J K
Hello, yes that’s correct but the 600V must be given through a 33K ot 47K resistor to the Vcc pin. Even 24V must be given through a 10k resistor, otherwise the IC may burn internally.
I have 5oowatts induction cooker. How to modify its coil and capacitor for 200watts?
Any other method ?
apply less input current, the output will automatically reduce…
Hello Sir
i found the article very rich.i have some few questions.
pls is it possible to use a copper pipe as a working coil?
is’t also possible to use the MOSFETs IRFZ44 to produce high frequency?
if yes i want to know and if no i want to know why.
thank’s
Hi Alex, yes you can use a copper pipe as the work coil, and use IRZ44 as the MOSFETs. All Mosfets are high frequency devices, it is their power handling capacity (voltage and current) which is actually important and must be selected as per the load specifications of the circuit.
Swagatam:
Are there any limits on the power needed to heat relatively large object? I think I need about 3KW of power to heat a 1″ Square steel tubing.
Please contact me at your earliest.
I would share my whatsapp phone and may be we could chat abit and you could help.
Larger objects will need larger amount of power to heat. You can try the first concept from this article….I could make a 1 cm diameter screwdriver red hot within a few seconds
https://www.homemade-circuits.com/simple-induction-heater-circuit-hot/
Dear Swagtam,
As per the theory explained above, the resonance is created by adjusting the impedance value of inductor and capacitor. At equal value of impedance of inductor and capacitor, the high frequency electric field is created. Which induces the high current eddy current.
Then, what is the role of mosfet or IGBT? How can we increase the intensity of magnetic field so that we get high induced eddy current, by not changing the value of inductor and capacitor?
Dear Prakash, the IGBTs are for creating the oscillation frequency across the tank circuit. Without the oscillations resonance cannot take place. For increasing the magnetic field, you will have to increase the current across the tank network and then optimize for maximum resonance peak
Yes, with increase in I/P current the magnetic field intensity increases in series LC circuit.
But how to increase magnetic field in parallel LC circuit? The overall current passing through inductor and capacitor becomes zero at resonance and circuit works as an open circuit. In this situation, the current doesn’t play a vital role in parallel LC circuit. Pls correct, if I am understanding wrong.
The input current matters for both series and parallel resonant induction heaters, because if the input current is not sufficient, the output cannot supply the equivalent heat.
At resonant frequency the magnetization will be maximum which will cause maximum eddy current to develop on the load, which will in turn demand higher current at the input to sustain the heat on the load. If the current is not sufficient, the voltage will drop reducing the heat proportionately
Dear Swagatam,
Thanks for your quick reply. Please check in attached video..
And the theory also states the same, the series LC circuit works as short circuit and parallel LC circuit works as open circuit. In parallel LC circuit, the overall current becomes zero, then how can we increase the magnetic field intensity by increasing the current? Please explain. I really need help to understand this logic.
Dear Prakash,
In parallel resonant circuit, the capacitor draws a huge current at the initial switch ON period, and then this current is switched to and fro between the inductor and capacitor at the resonance level and only a small current from the supply source is required to sustain this resonance.
But as soon as a load is inserted within the coil, the current that’s being exchanged across the LC now gets converted into eddy current and is transferred to the load in the form of heat. When this happens the LC losses the initial high current and tries to get it from the supply source, and hence the supply source has to now provide the specified excess amount of the current to sustain the heat on the load.
Thanks dear. Well explained.
You are welcome Prakash!
Hi Swagatam.
I’m trying to use the induction cooker to heat the steel pipe. The original induction cooker coil is used in a such way that is unwrapped from it’s original position and wrapped around plastic pipe (just to keep it in place) through which a steel pipe is running. Original coil shape is pancake type with a single wire (here a single wire is the term I’m using for original cooker’s Litz wires) placed in two layers.
I have used the same wire but as a solenoid type. Temperature sensor wasn’t attached to the steel pipe. I left an air gap between the plastic and the steel pipe to prevent the heat to melt the plastic pipe.
Induction cooker has a few power levels and I was using the minimum power which is 200 W (60 degC) to power the coil. After a very short time (maybe a few minutes) the bridge rectifier burns out.
Any ideas why did the rectifier burned? I suppose that the new coil arrangement caused to pull more current then the system could handle a the time since the required power level was 200 Watts. Could this be true?
I’m planning to use two (Litz) wires in the same arrangement as above and connected to the same terminals of the cooker. Can I expect the rectifier to burn out again?
Hi Mario, yes it is happening because the inductance of the new coil is not matching with the original value. If you want to change the shape of the inductor then you must ensure that the inductance value is not altered, and remains the same as the original.
OK. Thanks for reply.
Dear Swagatam
I would like to warm up a very thin nickel cylinder until 200 centigrade
Its thickness is about 0.1 mm and its diameter is 20 cm.
I don’t know suitable frequency and power of heater
Dear Mohammad, you can use the first circuit from the following article and fulfill your requirement.
https://www.homemade-circuits.com/simple-induction-heater-circuit-hot/
thanks
I purchased below ready module that you advised
https://www.homemade-circuits.com/wp-content/uploads/2019/08/induction-heater-circuit.jpg
when i attached to 10v power supply, current increased to 15A and smoke raised from one of mosfets
what is my mistake?
It seems your induction system is faulty. Did it work initially or this happened at the first attempt? In any case it looks like the unit your purchased is faulty.
Because the unit must work without issue regardless of whether or not a load is introduced in the coil.
at first attempt smoke raised from one of mosfets and I disconnect unit and try again and again with and without load but one of mostets heat up and raise smoke .
seller say that this units are checked.
I think that they check unit without asambel coil and only attend on LED light up.
can this check up destroy unit?
who can I repair unit?
thanks for your attention
Unfortunately, your circuit seems to have gone faulty, either due to manufacturing fault or some other unknown reason.
You can try replacing the blown MOSFET, and check the results….if possible you can replace both the MOSFETs, and also check the capacitors if they are fine, before powering.
can I purchase 4 mosfet and parallel two by two to increase power of unit
First try with a single pair, if it is working good, then you can consider more in parallel
they said that if we conect unit to switching power supply and then power it up, may be damage our unit. therefore we have to power up our power supply then connect it to our unit.
what do you think?
You can see in the video in the earlier linked article, I used a 12 V 20 amp SMPS, and switched it ON directly and my induction heater circuit worked perfectly, without blowing anything. May be you can use an SMPS which has a slow start feature, so that the voltage rises slowly instead of a sudden rise
Dear Swagatam,
How are you? I need some help from you. Actually, we are trying to make a induction heater by using this schmtaic:
We have connected everything properly as per video. We have used same 16 gauge copper wire for making ferrite core. All the components are exactly same as described.
But The problem is, our mosfet is heating like anything and blowing, within 20 sec. We also do not get any output and the inserted object do not heat.
Can you please check and suggest smth..
Your fast reply is appreciated.
Thanks in advance!
Dear Prakash, it can be difficult to troubleshoot without testing your connections practically.
But it seems the design is similar to the one explained in the following artcile:
https://www.homemade-circuits.com/simple-induction-heater-circuit-hot/
So I would recommend you to first try the smaller version as explained in the above link, and then you can upgrade it to 2000 watts by adding mores MOSFETs in parallel, and by applying higher voltage and a 7812 IC.
Hi Swagatam,
Last week I tried making the simple induction circuit suggested by you under link. We used same components IRF540 and diode UF 4007. Unfortunately our circuit was not responding with IRF 540 Mosfets. Then we replaced the Mosfets with IRF 3205. After replacing the Mosfets the circuit wires are heating extremely fast and melting also. Yes, we are making the open circuits on varo-board.
We face the same problem, when we make 2000 Watt circuit with 4 Mosfets.
Just want to know that, does the circuit depend upon number of turns and dia of work coil? We are using 12 gauge copper coil with 8 to 10 turns, just for testing. After successful run of circuit, we plan to have more number of turns in work coil.
As I understand, the LC circuit works on Inductor and capacitor. These 2 things we keep same as described in your post and in video, correspondingly.
If you want, we are ready to share the video of our circuit, for your analysis. You can send me an email for sending you the circuit video.
Thank you!
BR
Prakash
Hi Prakash, as you an see there’s hardly any components in these circuits so it should start working immediately. Burning wires means your circuit is not oscillating, which is again difficult to diagnose, since the circuit is a self-oscillating and self-resonating design.
Yes it strictly depends on the number of turns for the resonance to lock in. The LC values determine the resonance frequency of the circuit.
I would recommend you to buy a ready-made sample and check the details of the PCB and components positioning, and compare your design with the original for finding the differences and the faults.
It the number of turns or the inductance of the coil, and the capacitance of the capacitors which are two crucial parameters, the wire thickness decides how much current the coil can handle, or the load wattage.
Hi
I managed to produce the induction heater circuitry 1 and i am now working with induction heating 2 because the heating in 1 was pretty much slow. How may i increase the speed of heating and hence the power delivered to the load. How can i also improve the quality factor of the LC tank circuit for maximum efficiency.
Hello Sir
In the induction heater 2 circuitry, is is possible to replace the 2u2 400V(film) capacitors with 1000 microfarad 400V(electrolytic) capacitors?
For the purpose of my project, I would also like to know the purpose of the RC(4R7 and 4n7) network across the LC tank.
Correct if im wrong the RC network across the MOSFETS are snubber circuits.Thank you very much in advance SIr. I appreciate your work.
Dear Swagatam!
Thank you for your article!
I have built your circuit (except the current limiter coil). I would like to drive a coil with 125kHz for inductive wireless power transport (I know your BJT circuit for that, but I would like a push-pull circuit so I chose this one).
On the output there is a square signal (as expected) when the load is ohmic. But as I replace the ohmic load to CL (in series) load, the circuit goes mad. If I don’t limit the current on my power supply, the H bridge and the FET driver burns down. (I placed 300nF in series with my power transmitter coil, which is 6.8uH).
If I reduce the value of the maximum current on the power supply, the circuit doesn’t burn down, so I can observe it… and the output signal is terrible. Nothing to do with a sine form. Even the signals on the FET’s gate also goes wrong…
Do you have any idea? I can send you oscilloscope screenshots and pictures of the circuit in email.
My only idea is: it is now implemented on a breadboard, and between the FET driver IC and the transistors there are 50mm long wires… maybe it is too much, I don’t know…
Thank you for your help in advance!
Adam Pinter (mechatronic engineer MSc)
Thank you Adam,
I think the current limiter coil plays an important role in stabilizing the current consumption and also in preventing the MOSFETs from blowing, so it must be included with some trial and error. Or initially you can replace it with a 500 watt filament type bulb for the same results. These might also help to correct the waveform
Yes 50mm wires at 125 kHz can be a problem to the MOSFETs and blow the MOSfeTs by creating stray inductance loops, and a lot of harmonics.
Also, did you try optimizing the resonance, because as the resonance reaches its peak the current consumption will reduce proportionately?
And make sure to add a 1K resistor across the gate/source of each MOSFET, which will further help to prevent the MOSFETs from getting damaged.
I hope these points might guide the procedures in the right direction.
Dear Swagatam!
Thank you for your fast reply!
– I placed a limiter coil and the things became much better. But now I run the IC from a separate 15V power supply (the ground is common with the other power supply), because the FET bridge (with the transmitter coil on its output) still consumes too much power, therefore the power supply’s output goes down to 1VDC (I set an 1A current limit on the power supply). BUT now at least I have a sine-like output (it is a 10V peak-to-peak sine output, when the input of the brigdge is 1VDC).
– I will learn your article on MOSFET blow you linked and try to get closer to the solution.
– Now I have a sine output, but (as I mentioned) I have too much current consumpltion, and I also have strange overshoots on the FETs’ gate signal, which also cause huge noises that are superimposed on the sine output. There is no cross-opening, I don’t see such a thing with oscilloscope, but something is not OK yet. Maybe the wire lengths…
– I will try to optimalize the resonance also, as you recommended.
– I have added resistors to the FET gates (I had expperienced it formerly that without a resistors they can go mad), but thank you for the advise!
Thank you for all your recommendations and yout time!
If I will have exact question or if I reach a solution, I will update here in a reply comment.
Thank you again!
Adam
Thanks Peter, Glad my suggestions helped! Yes the resonance is the critical factor in this concept, unless this is achieved the circuit can consume power like heck, resonance is something which has to be optimized with the help of the formulas or through some trial and error, by experimenting with the frequency of the circuit…….I wish you all the best!
Thank you!
I will keep in mind that resonance is a critical factor, and I will pay more attention to that. You are right, the circuit consumes surprisely much power, so now I know that this is the reason.
One more question: what value current limiter inductor do you recommend?
Thank you! Adam
No problem! The value of the current limiting coil or the DC link inductor will need to be experimented a bit. You can start with a 2 mH coil wound over a ferrite core, the wire could be a 0.6 mm super enameled copper wire. Begin with 6 V and check the amplitude and the current….gradually increase the voltage, simultaneously checking the current and the amplitude, at some point the current should reduce and the amplitude should become maximum. On the same lines you can also try changing the inductor value, and repeat the procedures until the most favorable response is obtained.
Hi I’m mercy from Nigeria, I wanna design an induction oven for drying fish.
My question is can those factory induction stove run on DC as I just intend to power with solar panels.
I will also like to know how to calculate induction heating coil so I can pair it with a board.
I don’t like electronics that much
Thanks
Induction heater will run on solar Dc supply if the current and voltage are correctly matched…
Hi Swagatam,
thanks for the articles and previous comment responses with additional links.
I have the need to heat a piece of sheet metal which will be inserted into a vacuum chamber made of PVC plastic. It will be large enough relative to the PVC pipe that the sheet metal will curve around the inside of the pipe, like a hollow cylinder. Since the chamber has vacuum, I cannot heat this piece reliably with conduction methods like a hot wire wrap. Thus I am considering induction. Being the item will be approx 60 cm tall and 80cm circumference… it seems I would need quite a lot of wire to build a coil which will encase the entire sheet metal piece. Rough calc is (60cm tall / a coil wrap per 2 cm) == 30 wraps of coil. (30 wraps * 80 cm) == 24 meters!!! Does the table in this page for wire current calculation cover my application? I should mention, the sheet metal only needs heated to approximately 35 to 50 C… much much less hot than I think most DIY induction heater target temperatures. Thanks again!
Sorry Nathan, I have no idea how this application can be customized, and the related wire current calculations, because it looks too huge and might require some complex calculations…
Hi Swagatam,
Just want to know, Why is necessary the capacitor C in parallel with the main coil?
I mean, why a resonant circuit (tank) is necessary if you are using the IRS2453 to generate the frequency?
Hi Cesar, without the capacitor, the inductor will not be able to generate resonance effect, it is possible only when a capcitor is added with the inductor. When the two come in parallel the applied frequency gets enhanced to a great extent, enabling the output to produce high intensity pulses with minimum consumption.
I see… With a fixed LC values, is it possible to use a PWM to drive the power?
I think Charge and discharge must be 50% and 50% time… or am I wrong?
Yes it may be possible by experimenting with the frequency and with 50% duty cycle.
hi sir.
can i use 20 amp igbt instead 30 amp. igbt in induction chullah.
plz sir.
Hi Jatinder, yes you can, just make sure your input supply current is less than 20 amps
Hello
kind of new to these circuits and have some questions.
first of can i use this circuit to build a small desktop smelter (i’m a metallurgist and planing on some experiments).
second is this circuit more efficient since it is more timed? compared to the more common 2 Transistor no oscillating IC that is the most common circuit that i keep to stumble upon that has constant power feed?
Hi, yes this circuit is extremely efficient due to ZVS concept.
To melt the job you will have to upgrade the coils with thicker wire or tubes, and use a higher equivalent current for the supply.
Ahh ok then my notion was correct i will use copper tubing and a cooling pump since the heat will be quite intense after a while. then i think i found my circuit i prefer efficiency over simplicity.
I will look around for power-supplies and if i am brave and extremely careful maybe convert a microwave transformer, but i look around a bit for solutions on that part.
Thank you for taking your time.
No problem, wish you all the best!
thank you founder
hi sir how can i select the values of each components for example the values of R C L and types of diod and mosfets for the induction heater
Hi Zeabeni, I have explained it in the article, please see the bottom section of the article.
Hi Swagatam, thanks for laying this out clearly in a post. Haven’t found as clear a resource as this to understand basic induction heater design. Just one question – the link you have posted to help beginners select wire dimensions seems to be private (this one – https://circuitcalculators.blogspot.in/2017/10/wire-thickness-and-current-calculator.html).
Can you help provide an alternate public link to this?
Thanks once again for posting this here and sharing your knowledge so freely!
Thank you Arjun, please check it now, I have changed the access to public.
Hi
Your tutorial was so helpful. please what is the key deference between using low voltage and high voltage for induction heater, and which is preferable.
I am glad you liked it…there’s no difference in the working principle of the design for different voltages.. If your requirement is for generating extreme heats over large objects then you might need very high wattage for the process, which will require the use of higher operating voltages.
so it basically depends on the power output, for reasonable values low voltage can be used, but for bigger jobs higher voltage may be required.
Dear swagtam:
here i should add that my problem is concerning the induction heater with 4 IGBTs and the coils with air core.
thanks a lot
Dear Saeed, in that case you should have posted the comment under that particular article, for so long I thought you are referring to the above design
here’s the link of the original design
danyk.cz/induk3_en.html
Dear Swagatam:
I have just LITTLE heat although the 4.7 k volume has been adjusted as precisely as possible but still the 300 w lamp is illuminating so brightly . on the other hand ,
i cant find the Sd pin of the IC although checked with the datasheet.
the circuits has been built exactly in conformity with the plan introduced by you
please tell me:
1- what pin you mean by SD?
2- if the coil is OK. it is 4 turns of 4.5 mm wire with 9 mm diameter.
by the way the only thing to adjust is the volume, so i dont have any more idea of how to regulate the circuit. i have used the shortest wires and four ferittes at the tip of the wires connected to the bases of IGBts.
the last connection points of the caps have been connected to the coil and with thick wires.to me everything is ok but unfortunately the IGBTs will blow out if i use more wattage lamp. for example i lost three of them and one IC today when i used a 800 watt lamp.
please guide me by telling
if the coil is OK and what pin you meant by SD.
your Sincerely Saeed
Saeed, The SD pin is pin#5 of the IC, just under the Rt pin…. it is clearly visible in the diagram, I am wondering how you could not find it?
By the way where is 4.7K, are you referring to the Rt resistor selected by you as 4.7k??
Please try using the following formula for selecting the coil, capacitor and frequency parameters
F = 1 ÷ 2π x √LC
F can be determined by adjusting Rt/Ct, C can be randomly selected, once F and C are determined L can be calculated by solving the above formula.
Frequency will need to be confirmed using a frequency METER across the output pins of the IC.
As long as resonance is not achieved the circuit will not work optimally, and you will keep losing mosfets and IGBTs
Alternatively you can go with the existing set up, connect an arbitrarily selected Capacitor for “C” and Ct, and then tweak Rt until you find the heat to be maximum and illumination on the 300 watt bulb minimum.
Remember you must do the above by attaching an iron plate with the coil, if you keep the coil air-cored then the circuit will never work, I have already cautioned about this in my previous comment.
try a 7 turns coil, this will allow a lower frequency and stable operations
Dear Mr. Swagatam:
I am not a new comer , as i have been working on electronics over 30 years but mostly practical and rarely theorycal so I need your help with making this circuit. as a matter of fact i have made it and works, however with a 300 watt lamp in series and the lamp illuminates so brightly and I have just little heat in the metal inside the coil. as i have burnt out a few expensive IGBTs , I fear to use more powerful lamp. the 4.7 volume has been regulated so precisely. however, the coil i have used is 9 centimeters diameter(for i need this size of the coil) and 4 turns with 4.5 millimeters thickness of the wire. the caps are almost 2.3 uf. Do you think i have to make some changes in the coil or it could be OK?
meanwhile, as the wider a coil , the more useful the circuit could be, i want persistently to use it. please tell me:
1- is the heat OK with the 300 watt lamp?
2_ by what i mentioned can I use more powerful lamps? or i have make changes in the coil?
thank a lot \
Saeed Mahdavi Asl
Dear Saeed, If your 300 watt bulb is illuminating brightly, then it is not good. Your circuit might not be working correctly
At resonance your lamp must have minimum illumination and the load must have maximum heat.
Were your able to achieve the correct resonance for the design??
It has to be done by attaching a magnetic plate with the coil, and then tweaking the frequency until the heat maximizes and the lamp illumination minimizes.
By the way did you connect the SD pin of the IC to ground? Otherwise the system will not initiate.
how to get value of Rt and Ct thank you sir !!!
It is explained in this post
https://www.homemade-circuits.com/2014/01/simplest-full-bridge-inverter-circuit.html
Hi Iam from Ecuador my name is Paul Cardenas Gordon.
I came to your website because I am looking for a magnetic induction circuit. I must thank you for having found several options. You can tell me which design I can adapt to get a power of 1kw maximum output.
And how could I do to vary the output power.
I do not study electronics, I study mechanics but I am struggling to understand the circuit.
Thank you for visiting my site Paul!
You can try the following design
https://www.homemade-circuits.com/2017/01/induction-heater-circuit-for-labs-and.html
in this circuit you can limit or change the max power output by appropriately calculating Rx value.
But please remember that this concept is suitable only for experts in the field of electronics, and is not recommended for any newcomer, therefore make sure that you have an expert electronic engineer with you while constructing and testing this circuit.