In this article I will try to explain the making of a 1500 watt simple heater controller circuit at 25 amp current rate using an ordinary triac based dimmer switch circuit
Using Advanced Snubber less Triacs
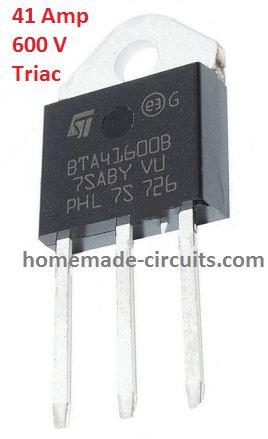
Controlling heaters rated as high as 1500 watt requires stringent specifications with the controlling unit for safe and effective implementation of the intended operations.
With the advent of advanced snubber-less Triacs and Diacs making heater controllers at massive watt levels has become relatively easier today.
Here we study a simple yet entirely suitable configuration which may be utilized for making a 1500 watts heater controller circuit.
So I will explain the given circuit diagram with the following points:
How the Triac/Diac AC Controller Works
The set up of the circuit is pretty standard as the the wiring is very similar to the ones which are normally employed in ordinary light dimmer switch circuits.
The standard triac and diac set up can be seen for implementing the basic switching of the triac.
The diac is a device which switches current across itself only after a certain specified potential difference is reached across it.
The following network resistors and capacitors associated with the diac are chosen such that they allow the diac to fire only as long as the sine curve remains below a certain voltage level.
As soon as the sine curve crosses the above specified voltage level, the diac stops conducting and the triac is switched OFF.
Since the load or the heater in this case is connected in series with the triac, the load also switches OFF and ON in accordance with the triac.
The above conduction of the triac only for a specified section of the input sine voltage curve, results in an output across the triac which has the AC chopped into smaller sections, making the overall RMS of the resultant drop to a lower value, depending upon the values of the relevant resistors and capacitors around the diac.
The pot which is shown in the figure is used for controlling the heater element which initiates the above explained procedure.
The greater the resistance, the longer it takes or the capacitor to charge and discharge whih in turn prolongs the firing of the diac/triac pair.
This prolongation keeps the triac and the load switched OFF for a longer section of the AC sine curve which results correspondingly lower average voltage to the heater, and the heater temperature remains at the cooler side.
Conversely when the pot is adjusted toward to produce a lower resistance, the capacitor charge and discharge at a faster rate making the above cycle rapid which in turn keeps the average switching period of the triac at the higher side, resulting a higher average voltage to the heater.
The heater now generates more heat due to the increased average voltage developed across it via the triac.
Circuit Diagram
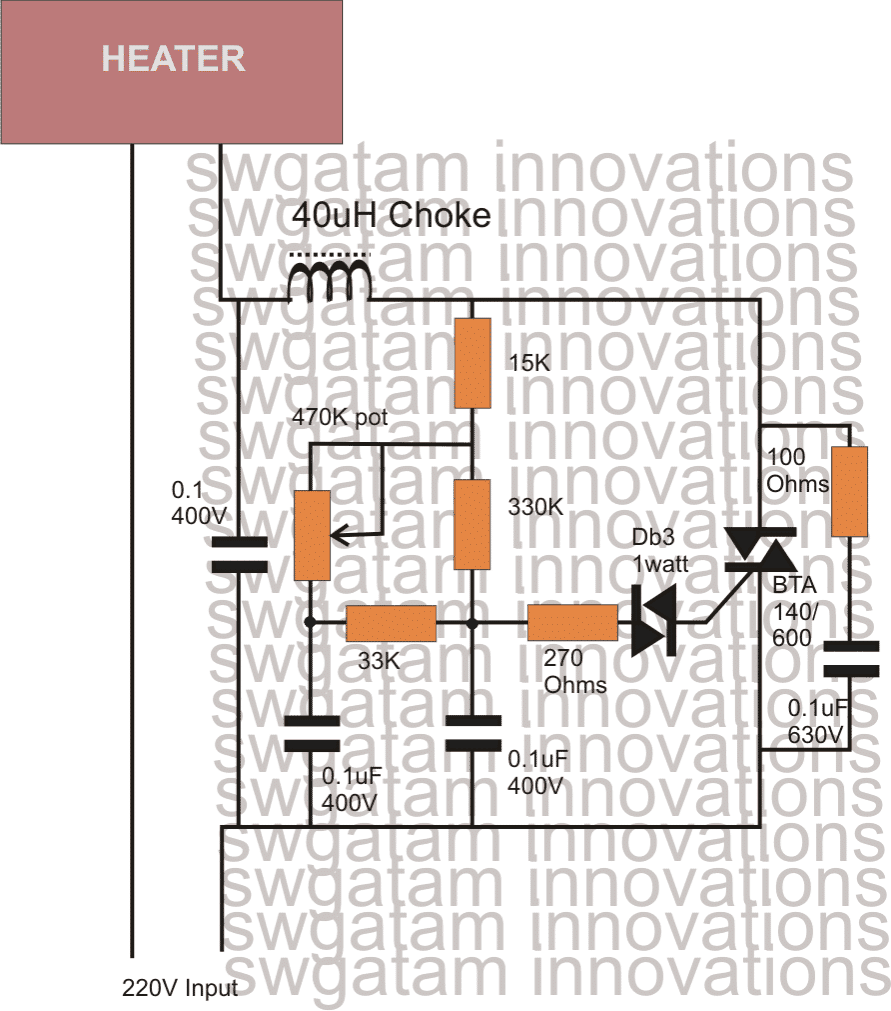
Parts List
Resistors 1/4 watt 5% CFR
- 15k = 1
- 330k = 1
- 33k = 1
- 270 ohms = 1
- 100 Ohms = 1
- Potentiometer 470k linear or 220k linear
Capacitors
- 0.1uF/250V = 2
- 0.1uF/630V = 2
Semiconductors
- DB-3 = 1
- Triac = BTA41/600
Inductor 40uH 30 amp (optional)
Controlling through Arduino Pwm
The above simple 220V dimmer switch control can be also effectively implemented using an external Arduino PWM feed through the simple method shown below:
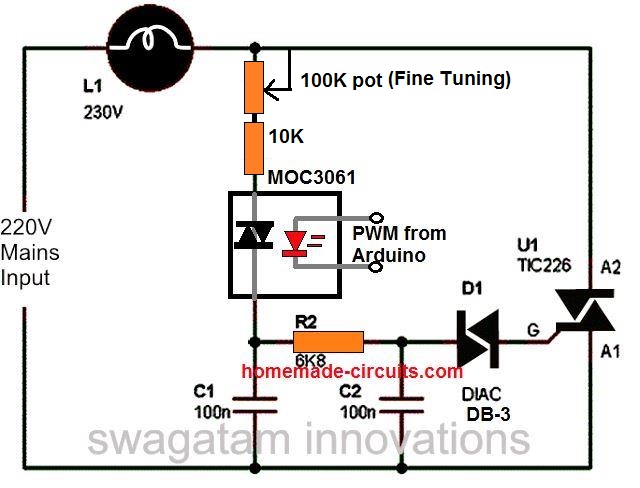
Advanced Heater Controller with Snubber and RFI Elimination
As soon as the voltage around C2 increases over approximately 30 volts (during any phase cycle), the Diac (D1) breaks over and produces a trigger pulse for the gate of the Triac (TR1).
This leads to the Triac switching ON and it applies the entire AC line voltage to the load hooked up to SO1.
Adjusting the potentiometer R2 varies the phase (timing) of the trigger pulses applied to the Triac and therefore modifies the average power level going to the heater load.

Resistor R5 along with the capacitor C3 works like a a snubber network over the Triac to safeguard it from the reverse EMF voltages spikes created by inductive loads every time the Triac is switched OFF.
Inductor L1, which is a 50 µH choke, and capacitor C4 are configured like an interference suppression filter, that enables the elimination of the RF noise commonly generated by this type of light dimmers or heater controllers.
The preset R3 adjusts the minimum starting range of the heater temperature, and helps the user to ensure that the power to the heater always starts from the minimum power when R2 is moved to the minimum position, and the heater gets maximum power when the R2 is moved to the maximum adjustment point.
PCB Design
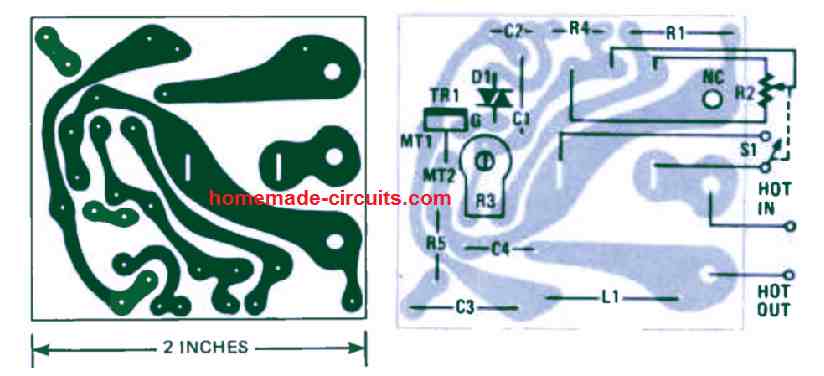
1000 watt Light Dimmer
Nearly all light dimmers that you can get from the common electrical products stores can simply manage pretty small electric power.
A few hundred watts is normally the handling capacity. The straightforward dimmer circuit demonstrated below is designed to control a power as high as 1 kW.
There is nothing much to be explained regarding the details of the circuit.
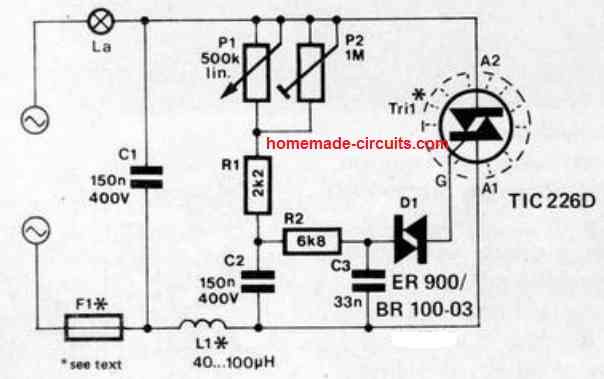
This high power light dimmer includes one triac, a single diac and an RC network where the period of the charging and discharging of capacitor C2 could be fixed using potentiometer P1.
Noise disturbances and transients are kept under control through capacitor C1 and the inductor L1.
How to Set up
Setting up of the circuit requires adjusting the pot P1 so that it reaches its maximum resistance, and then preset P2 must be tweaked until the attached lamp is just at the verge of shutting down.
In case a lamp higher than 100 W is utilized the triac should be attached to a heatsink having a heat transfer specification rate of about 6 °C/W.
When the circuit is used like a 1000 W dimmer, suppressor coil L1 should be rated to handle a current of 5 A with an inductance value that may be up to 40uH, while fuse F1 must be rated at 6.3 amps.
Heater using Transistors and Resistors
This unique heater circuit which involves transistors and resistors for the heat dissipation instead of a heater coil was designed by Mr. Norman, but he faced an issue with the circuit.
The problem and solution for the design can be understood from the following discussion:
Problem:
I designed a small heater using LM7812 voltage regulator and Tip31c transistors and resistors.
I tested it over several hours and found a problem. The last two 56R resistors got extremely hot and burned and scorched the pcb. I am attaching a schematic.
I couldn't find a similar project on your website, so I am trying to contact you through this contact point. Thanks!
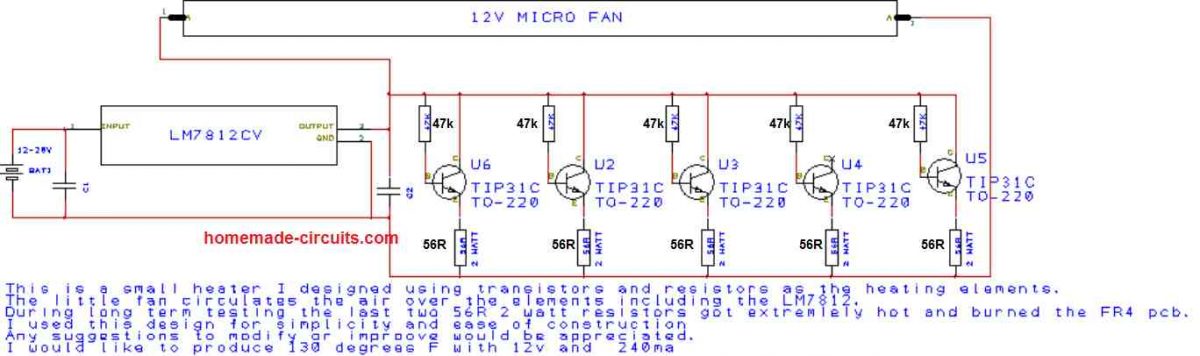
The Solution:
That looks very strange because the 56 ohm resistors at the emitter of the transistors should force the transistor to dissipate the heat equally among the resistors and the transistors.
The last two 56 ohm resistors getting hotter means that the last two BJTs are conducting more freely than the remaining transistors.
The easiest way to tackle this problem is to mount all the transistors over a common aluminum strip, so that the transistor exchange their body dissipation uniformly with each other and thus all the transistors conduct and dissipate equally.
Hi, i found your great post, that for sharing.
My purpose for using this is for controlling a water boiler of 1200w that heats up too fast. Its water heating block from an old automatic espresso machine. Its a boiler that heats the water as it passes trough the block. As it is its heating the water faster than the pump passes it trough.
My idea is to use the first sketch and adjust the pot to heat enough for the water to have a specific temperature when it exits. Just to see if it works.
My if that works as intended my next step is to move it in to a arduino and have a temp sensor at the exit adjust the effect to the heater to keep the exit temp fairly consistent regardless of the water pumps pressure.
Do you have any suggestions how to implement that. My idea is to use a Waterproof DS18B20 to measure the temp.
Thanks, and Glad you liked the post.
You can definitely try the first schematic.
However my Arduino knowledge is not good, so helping with Arduino code may not be possible for me.
Nevertheless, I can suggest a simple op amp based heater controller with a sensor, no need of Arduino.
That would be great. Many thanks.
You can try the last circuit from the following article:
https://www.homemade-circuits.com/lm35-circuit/
When the LM35 is heated by the heater temperature, it reaches a certain point (as per the adjustment of the 4k7 preset) the op amp triggers ON the relay which switches OFF the heater and the process repeats.
In the first circuit why is some parts in parts list has different values?
Also is it possible to use the first circuit for a heating coil which was 1500w but is cut to half it’s length somehow? Or can you design a simple circuit like the first one for the above heating coil I mentioned. Please do respond.
The parts list shows 0.1uF/250V and triac BTA41 which are also correct and can be used in the circuit without any problems.
If you cut 1500 watt wire into half, then its wattage becomes 3000 watts. Assuming the voltage is 220V then the current will be 3000/220 = 13 amps. So the first circuit will still work and can be used for your requirement.
I wish to make a polyfoam cutter. I tried using a length of nichrome 26 guage (400mm length) 4.2 ohms in series with a 600w light dimmer wired to ac voltage of 20 volts. It did the job, but the nichrome wire drew 5.6 amps, making the dimmer hot.
Please tell me how to wire this up.
The dimmer was connected to the secondary side of the 230volt stepdown transformer.
Thank you,
Nanshir
Kuala Lumpur,
Malaysia
Using high wattage load at high voltage can keep a triac cooler, due to lower current. In your case you are doing the opposite, you are using low voltage and high current, that is why the triac is getting hotter. The only way to solve the issue is by using a higher rated triac, and then mount it over a large heatsink.
Another great idea is to connect the dimmer on the primary side of the transformer, and connect the nichrome wire on the secondary side of the transformer. So your dimmer controls the primary winding at 220V, and the load is controlled via a correspondingly varying secondary voltage of the transformer.
Yes, Swagatam, thank you. I tried as you suggested. Works perfectly.
Thank you again.
Victor nanshir
My pleasure Victor, glad it worked!
Hi Swagatam,
On heater controller circuit above with 470K potensio, at highest resistor adjusted, does it reach 0V, by meant it cut off Triac current?
Thanks
Hi Awak, yes it will reach 0V but 0V is not recommended. Therefore use 220k instead of 470k so that it doesn’t go below 10% heat at the lower limit.
Thank for respond. I have built a dimmer with other circuit where use 500K potensio, the lowest voltage is 95V, actually I need 0V or at least close to 0V. My purpose with that circuit is to control my step down transformer for battery charging, use BTA41 triac. Please advise, what is proper potensio to get this purpose? Is 1M enough?
Thanks for help.
You can try a 1M pot, or increase the two 0.1uF capacitors around 33k to 0.22uF….but this will not allow proper starting of the load….the load will not start until 150V is reached.
Ok thanks. This mean just to start the circuit, don’t we? So, after that, we can adjust to the lowest voltage, right?
Yes, that’s correct.
Hi! Swagatam,
I made the change of adding the 1k preset from pin 5 to ground and it allowed me to reduce the output below 700ma. It was real touchy to adjust, so I took it off and replaced the 5k preset with a 10k preset and it works perfectly with a 12v supply.
I have a second circuit that uses a 20v-5Ah battery, so I have a 7812 reducing the 20v supply to power the 12v micro fan and to power the two 12v-25 watt pad heaters in parallel. The 20v supply also powers the 7809 for the control circuit. I have a 334 capacitor on the power in to both 78xx ic’s. I have a 104 and a 10uF capacitor on the power out of the 7809. I have a 104 and a 2200uF capacitor on the power out of the 7812. I can only get a max of 540ma out of the circuit. As I increase the milliamp draw above 540ma, then the 12 volts begins dropping dramatically. I am puzzled by this as it appears the 7812 is not passing enough power. I first had a 10uF cap on the 7812 output and changed to a 220uF which helped, so I tried a 1000uF and then increased to the 2200uF. Any suggestions as to what may be a solution of having more adjustment of the milliamp output of the circuit?
Hi Norman, the 7812 can deliver full 1 amp @12V only as long its case temperature is below 40 degree Celsius according to me. So make sure the 7812 temperature is below 40 degrees C. Otherwise you can try LM338 for the regulator, or the following fixed variant
https://www.homemade-circuits.com/12v-5-amp-fixed-voltage-regulator-ic/
Hi Swagatam! I built the heater circuit and it worked. I had to increase the milliamp draw to 1000ma to get the two 12v 25 watt heaters in parallel above 100oF. The transistor I used was a TIP33 because that is what I had on hand. The temperature of the TIP33 was over ranging even with a heat sink and a micro fan blowing on it, so it was thermal cycling. I noticed on one of your motor speed control circuits you used a mosfet. I had a FQP30N06L Mosfet, so I replaced the TIP33 with the mosfet and it worked great. The mosfet stays really cool. The problem is I had to adjust the 5K variable resistor to limit the amp draw and the least amount of milliamps I can get is 700ma. How can I change the circuit to be able to reduce the amp draw down to 500ma? Thanks!
Hi Norman, glad it is working, however the issue that you are facing looks strange because the circuit is supposed to provide a PWM control from 5% to 95%.
You can try adding a 1 K preset between pin5 and ground, and check if its adjustment provides you the required reduction in the PWM
Thanks! Swagatam you are the greatest! Fast complete response! I hope everything is going well for you and your loved ones.
Thank you Norman, we all are good here, appreciate your kind thoughts very much!
Hi Swagatam! I have a small silicone pad heater that is rated 12v @ 25 watts. If hooked up to 12v it draws 1.3 amps and gets to 200 oC. It is made up of nichrome wire between two sheets of silicone. I would like to have two of these heaters in parallel and control the temperature to about 130 oF at 240ma each. I am supplying 20v with a 5 Ah lithium ion battery and plan to reduce this voltage to 12v to control a 25mm fan for air distribution. I think maybe a PWM circuit might work as it will reduce the ma output. I want 240 ma to each of the two heaters to make my battery last 10hrs. these heaters are touching expanded polystyrene which will collapse at much over 150 oF. The battery circuit has a low voltage cutoff set at 15.3v to protect the battery for over draining. I may have to have separate circuit for each of the heaters. Safety is a real concern as these will be attached to my house. I cannot stand for the heater to run away with itself and burn something up. Your perusal and suggested modifications are required. Thanks!
Hi Norman, you can use the following simple IC 555 PWM circuit, for fixing the heater temperature to a constant level, through the pot adjustment. The 7809 IC is important which ensures that the PWM is always constant regardless of the input voltage variations:
Complimenti bravo continua cosi!!ottimo lavoro Grazie!!
Hi,
I want to build a coffee roaster, and I want to use a 2,000 watt heat gun heater (220 v). Will this circuit handle that element? If it won’t, what mods need to be made to handle that much electricity?
Thanks.
Hi, yes you can use the above circuit for controlling a 2000 watt heater element. Make sure to use the triac that’s shown in the first image, and put a large heatsink on the triac
Hi Swagatam!
I want to build a 1000watt water boiler by putting a heating element around a steal pot (not bottom). I want it to power it using 12v DC battery.
Which heating element do you recommend for it? And how can I make a circuit for it?
I was considering using PTC heating element but that might take a long time to heat the water.
Your suggestion will be very helpful!
Hi Shraddha, using a PTC sounds a good idea as these are self optimizing and do not depend on external systems for the temperature control. Yes the heating effect will be delayed a bit as they are not designed to heat beyond 300 degrees Celsius. Perhaps, using an aluminum or copper pot may help speed up the process even with this heat, considering that this heat will all around the pot..
But the actual problem will be the supply source which will need to be rated at 83 amps if a 12 V is used. This will call for a 12 V 800 Ah lead acid battery or a 12 V 100 Ah Li-ion battery
Thank you for the response. I see, do you recommend on any other heating element I could use ? That will probably boil the water faster than PTC element.
The other option could be the standard Nichrome type heater coil, which will need to be controlled through an external circuit to prevent overheating
You show in the parts list 2 capacitors 0.1 µF/630V but only one in the schematic.
Is the other 630V capacitor the one right at the heater?
Thanks.
Actually both can be 630V or 400V, but not less than 400V
I am interested in making this heater control circuit to power my electric samovar. 10 Ohm heater coil, 110 V Ac
Could you forward a parts list. Amazon seems to have most of the items, but I am not sure which ones to use.
I was an electronics tech in the Air Force 1972-75. Much has changed since then.
The first circuit above can be applied for your heater. I have added the parts list below the diagram. Please make sure to add a heatsink on the triac
What is the value of R2?
It is 6.8k
I am still trying to find out the purpose of 330k and the 33k resistors. My guess is they are used to bias the diac. Could you explain the purpose of those resistors.
The RC network is specially configured to ensure a gentle step-wise firing of the diac and to make sure the triac is never allowed to go through sudden and abrupt switching.
Good day Swagatam
Please give suggestions on how to convert the circuit so that I can use a 3 to 20 Ma loop to controll the heater element
Looking at 4 to 5 kw element
Thanking you in advance
Chris
Hi Chris, sorry I do not have much idea regarding how to create a 3 to 20 mA loop to control heater element.
I’m using a solar array (and someday, a wind generator) to recharge a 540 Ah lead-acid battery bank on an ocean-going sailboat. Due to the charging profile of the lead acid batteries, I often have excess power available in the afternoon and I’d like to use this to run the AC heating element in my hot water tank, via an inverter. However, that AC heating element is 1600 watts, which would be well in excess of the power my panels can produce and will drain my battery bank quickly. I need a way of manually adjusting the current going to the AC heating element so I can balance the power to the heating element with the power produced by the solar array. I’m not an engineer so building circuits is not really my thing, so is there an off-the-shelf current adjusting mechanism that would lower the power to the element from 1600 watts to 800? Or better yet, be widely variable so I can adjust it?
What is the voltage spec of the heater? Here’s one design which could be modified for your application:
https://www.homemade-circuits.com/solar-water-heater-with-battery-charger/
You will have to adjust RV1 so that the op amp A output goes high when the battery is fully charged and the solar panel voltage tends to exceed this level.
Conversely, RV2 must be adjusted to ensure that the op amp B output goes low whenever the battery gets fully charged
First, i thank you for your reply .
Hello to you again .
About the lionel train of my son, ( YES ) i know that is realy important to calculate the exact A C output
voltage so i done that .
So, a hobby shop telling me to install a 50 watts-30 ohms rheostat on the ZW big lionel transfo as 275 watts -60 cycle , i was doing this but the rheostat start to work only when i reach the half way on the wire wound ,so,
another person explaned to me that my rheostat have too much ohms ans suggest to me to reduce the
ohms to only 10 ohms that supposed to be enough ,so , do i have to reduce only the ohm or the wattage and ohm like an 25watts-10 ohms or keep same wattage and only change ohms like an 50 watts – 10 ohms ??
P.S: I think that the wattage is important too!
What is the big difference from a TRIAC and a RHEOSTAT ??
Thank’s again .
Dan.
Hi A rheostst is a high watt variable resistor, which will reduce current and voltage by converting the excess power into heat, whereas a triac is like an electronic switch that will control power without power as heat. You can try a dimmer switch between the power source and the railway tracks for efficient power control
Hello again.
Just tried the version for PWM you have a diagram of.
It sort of works, and I believe it may be because of the trimpot, which is 100k, and when it’s turned to maximum I get response (and even off) from my Arduino, but it’s only allowing me to set in the range of 210-ish volts to 213 or thereabout.
I would’ve experimented, but I was foolish enough to mount the sucker on a prototype board since I didn’t have any heatsink to spare and it has adhesive tape on it, so I mounted the thing on top of it, with the board above. Also, to stabilize it I soldered a couple of flanges on it so it doesn’t move.
Makes it kinda difficult to dismount since I have to remove the Triac to access the circuit board.
Anyways, I get it to start by turning the knob to minimum, but it’s only like a millimeter to absolute lowest setting where the limit is. At the moment I don’t have any other potentiometer to test with, so I thought I’d check here first.
What’s funny is that I’ve tried connecting it directly to the output pin on the Arduino, as well as through a transistor, both in series and in parallel with the existing LED that I have there, a 2.8v Red diode, and that behaves kind of like expected: 0v input = Off (Arduino), but the Triac doesn’t see that, it’s either the millisecond the LED is lit, then it’s on, with very little variation as I mentioned on the mains side.
The components used are MOC3052M, BTA16-800SW3G and DB3 and other than those I’ve followed the diagram to the letter…
I do suspect the pot being the culprit, but the strange thing is that the second I remove the plugs on the input of the opto-coupler it shuts off, so I essentially have a switch, but I can’t get the full 230V at the same time. At least some more than mere 213V I would expect.
Loads I’ve tested is a light bulb and a radiator which has two modes 750W and 1250W.
Thankful for some insight.
OK, thanks for the feedback, if the last concept is not working correctly, you can try another option, replace the MOC with a LED/LDR opto, and then illuminate the LED with the PWM and see how it performs.
Well. Got some different results. I just tested with an LDR in parallel with the opto-coupler and I was able to adjust it a lot better.
However, I get a voltage drop to around 200V when a load is connected, measured across the load.
I get full 230 without. I suppose some losses are to be expected, but I think it’s little high. Tried both the lamp and the heater and got about the same results.
Another thing that bothers me is that I get a flicker of about, guessing 25-30 Hz, at the lowest input on the LDR (which is a 18-50k) and the pot set at highest resistance which gives the most juice out.
As I lower the resistance the light fades, but becomes less responsive on the LDR and the output maximum voltage drops considerably from 200 down to 70 I think, and flickers the lower I go.
I can’t see the flickering when I’m above, guessing 20-40% duty cycle or the LED’s starting to become bright.
*On a side note about this page (And probably others like it), it would be nice to see a timestamp for each post. Gets a bit confusing when we can’t see which is first as the posting is at the bottom.*
I guess the flickering could due to diac firing issue, you can try adding a 100 ohm in series wit the diac, and check the results.
Or if you wish to have perrefct results then you may go for a PWM/MOSFET configuration, and by supplying a rectified 220 V to th MOSFET via the load.
to know the post publishing sequence, you can check the following link:
https://www.homemade-circuits.com/blog/
Ok. I’ll try that resistor. I think I’m going to test another pot with higher resistance too. Your schematic said 100k, but it would seem it’s a little too low. I’m gonna tinker some more with it.
About the timestamps, I was referring to these posts, not the publishing date of the articles.
OK thanks!
To who it may concern. Hi to you.
I have a question for you (even or not even to help ) here is my story . Not long time ago , my grandpa give me an old lionel train set from the 50’s but i remarked that the transformer not having a variable control knob on it ? So, a guy from my hobby shop explaned to me that i need to buy an separate rheostat to put between my transformer and the train rails to have a speed control ,so i was found an 50 watts-30 ohms rheostat in my parts box and i install that one like this : I just cut the positive wire of my transformer and connecting one side to the wiper arm of the rheostat and the other piece of this positive wire (as the one that soldered to my positive rail ) to the wirewound terminal . The problem is that my train dont have any volume control at all , it is like no rheostat at all as soon i turn the knob ,the train start super fast like jack rabbit . A frien suggested to me to install an (motor speed regulator ) like the 2000w AC 50-220 25 amps but this device is a plug in wall input ,so, can i install (anyway ) that device directly from my transformer output and simply connect my rails wires to the output ? Thank’s in advance for any kind of tips . Kind regards . Dan.
If your transformer output is AC, and the train rail input also accepts AC, then you will have to use a triac based dimmer switch between the transformer and the tracks. if it is DC then you may have use a DC PWM motor controller in between the transformer DC output and the railway tracks.
But before all these you will have to make sure the voltage from the transformer is correctly rated according to the speed controller voltage specs.
Hi. Found this while googling.
I’m curious, what the purpose of the 100K pot for “fine tuning” (Controlling through Arduino Pwm)?
Is it threshold for the Diac in some way?
I usually don’t play with these kind of circuits, but I’m currently working on a washing machine which has a 3-phase controller circuit among a whole bunch of other stuff. TFT monitor, relay card (Which is where I’m thinking of swapping one pin for potentially this circuit) for water valves, heating element and more, and of course an Arduino Mega 2560 to control all the stuff.
I’m also curious, since this Triac seem very powerful, up to 25 Amps, which is quite a lot actually.
I’ve always found these amperage values to be quite dubious from time to time, or specifically wattage actually, depending on voltages and other circumstances which may throw the whole idea out the window for me.
Anyway, the question I wanted to ask is if there’s any other Triac which can handle, more perhaps, and not getting so hot?
To slam the breaks a bit here: First I don’t know even which package this Triac you have in your schematic, but I’m thinking at least TO220.
I’m looking at a heating element of at most 2kW, and as I’ve speed-read some folks are wondering about 4-5 kW and this circuit works just fine and all that you state.
What temperatures are we talking about, in celcius if you please?
I know it depends on the cooling surface, but I’d like to get a clue about what temps to expect.
Problem is that I have a limited space to put any flanges due to safety issues and also because of the other electronics, and I must keep wires as short as possible and all that.
Also, this machine is, unfortunately, a modern one, which means plastic everywhere, even the drum encasing.
Reason for this build was two things;
First; Free!
Second: Water damage and ordering a new card wasn’t certain would’ve fixed it since the control-panel was also damaged and unobtainable. µP on both cards, and I always wanted to do a project like this, so I did =0P
Sorry for the bla bla bla…
Hi, your answers are as follows:
1) The 100k pot sets the maximum and minimum range of control, yes the average firing threshold for the diac.
2) The current spec is as per the datasheet, the datasheet cannot be wrong, provided the conditions are appropriately met. You will have to employ large finned heatsink with fan cooling for accomplishing the 25 amp limit.
3) The package is TO-220 for the indicated triac. For BTA41 (41 amp) it will be TOP-3.
4) In a limited space and without adequate heatsink this circuit will not work.
Ok. That answered some of my questions.
Nothing about temps, so I was thinking how about several Triacs in parallel then?
This should, in my mind at least, lower the heat dissipation and energy-losses.
If, say, 3-4 were in parallel, they shouldn’t get so hot, and the cooling flange could be relatively smaller, and they should last longer/be more durable, I would think.
If I were to choose any other, like +50 Amps, the requirements for cooling would be a lot lower, right?
I just might try this design, but with a phat one and see how it goes. Would be nice not having to use relays and it might also save the lifetime of heating element too.
I’ve never played around with these Triacs since I’ve felt great respect for high voltage.
Much to do with bad experiences as a child (Like fingers in lamp sockets and similar – Damn that hurts! Just thinking of it makes me cringe! Like someone just twisted the finger with a torque wrench), and when stuff goes, they GO and take the magic smoke with ’em.
I’ve also had bad experiences with stated current limits (From datasheets/schematics) and then having it just turned ka-blooey for some reasons unknown to me.
Technically, parallel connections for Triacs is not recommended, however, if you can clamp them up on a piece of common heatsink, close to each other, then parallel connection may work. Still the heatsink will need to be adequately calculated.
Ok.
I’m thinking of putting resistors in series to even out the current drawn, like you do with ordinary transistors to avoid imbalance between them. Don’t remember what they’re called a.t.m.
Another question, if I attempt to do this, how about the RC and Diac values?
That gate current would be greater I think, so the values might be somewhat different in that case.
You stated the Diac had to have at least be able to handle 100 mA, so will this value have to increase in proportion, and if so, how do I solve that with the optocoupler?
For the diac you can try DB4 which is rated at 300 mA or you can use a neon lamp instead which has same working characteristic like a diac. For the diac use a small value resistor (10 or 20 Ohms) in series to protect it from sudden voltage spikes.
Just looked up a Triac, and realized one of the things that I’ve had some bad luck with in the past.
This particular that I’m currently browsing is marked “BTB16-800BRG TO-220 800V 16A triac”.
From what I’ve experienced, since I’ve never needed any more than 230V, is that the current rises due to lower voltage, but I’ve always stared myself blind (Swedish expression, bare with me) at the Amps for some reason.
I’m not a 100 % sure about this, I’m mostly self-taught when it comes to electronics, and I’ve had my share of experiences, mostly bad ones, and I don’t have any friends that share my interest so I’ve had no one to turn to, and add that to the mix of not needing any such devices, but only stayed as a interesting would-be-fun-to-make.
To top that off, I suck at math too =0/
I’ll look into that (You replied while I was writing this so I had to copy my text, refresh and paste).
I first thought that the Opto-coupler had to deliver these 100 mA, so I was browsing my local vendors equivalents, but didn’t find any that had 100 mA. All had 60 mA, and when I finally looked up the one you’re using I say it too delivers 60 mA :0L
I cannot find where I said 100 mA is required for the diac. If at all I said it, I might be referring to an extended 50 mA margin for the diac so that it remains well protected. The triac needs only 50 mA to fire optimally.
Btw, how about the opto-coupler, doesn’t it mean that it’ll be over-saturated if I hook up a bigger load to it? I mean, the current seem to flow through it and the need for a 100 mA Diac (Or more for my needs) which then is connected to the Triac, or am I missing something?
For 100 mA opto-coupler you can use VO3052
Hello sir,
I read your article its really good, but does this will work with Ceiling Fan to control the speed. Because i tried similar circuit for that but it makes humming sound, so by any modifications can i get the humming less circuit?
Thank you Rutvik, this circuit is recommended only for resistive loads, not for inductive loads like fans. For fan you can use a light dimmer switch as explained in the following article:
https://www.homemade-circuits.com/how-to-make-simplest-triac-flasher/
Thank you sir for reply. But I want to control the fan wirelessly so I used the Arduino and zero-crossing circuit to generate PWM, but the humming sound is coming. So please help me with the circuit. What modifications I have to me for inductive load.
Hi Rutvik, you can try adding the LC network (L1 and C1) as done in the light dimmer circuit and check if that helps to control the humming noise.
Hi Sir.. I want to control a 220V, 250 W heater using Arduino. Please tell the ircuit.
Hi Rajesh,
try the following circuit
https://www.homemade-circuits.com/arduino-pwm-signal-generator/
use the output to control a triac, and the heater as the load
Hi Swagatam,
How hot would this circuit get if running at 1500w?
Thanks!
Hi Marcus, The triac can get very hot therefore you will need to mount it on a large heatsink.
Hi, will this work on a carbon filament in convection cooker, and I’m also planning to control via arduino at a later stage any tips?
Thanks
Hans
Hi, yes it can be used for the mentioned heater.
For Arduino control I have updated the design at the bottom of the article
I purchased a Chinese voltage control module (MY12BAZC11000) hoping to make a 2 tube quartz radiant heater (1500W) more comfortable by adjusting for a comfortable glow of tubes rather then the on/off thermostat. My plan worked well until the triac got too hot and failed. I was thinking maybe the same module but providing a larger heatsink for the triac. What are your thoughts?
yes that will work, just add a large heatsink to the triac.
Hello, can I use neon light (little NEON lamp) instead of diac? Need to add, change other components? thank.
I am not very sure regarding the results, it might not be as efficient as diac, but no harm in trying it out
It’s because I only have DB3 DIAC (not 1W?). I’ll try with Neon, thank you very much for the quick response. All the best in this new year 2018!
yes in that case you can try a neon, wish you too a prosperous 2018
hi
How can i make 40 uH choke 5 amp?
Thanks
Hi, the 40uH and 0.1uf/400V is not crucial, you can eliminate it if you want, it is included to reduce RF interference in the atmosphere.
But if you intend to make it, you can roughly design it by winding 200 turns of 0.5mm magnet wire over a small ferrite core
Day. Do you maybe have a circuit for me to control the speed of a 2200 watt angle grinder using 220 Volt
board needs to be small so i can fit it in the grinder handle if possible
Shanks for everything you been teaching all of us.
kind regards
willem
thanks Willem, You can apply the same concept which is explained in the above article, it should work nicely!
Hi. Is the pot linear or audio? I'd assuming linear, but would like to make sure. Thanks.
It is a linear pot
Hello sir, can i replace 470k pot with another lowest res pot? Kinda 100k. And how aboit another resistor? Should i replace it?
Because i want to make a variable watt using slider potentiometer.
hello dektian, 100k will not do, because it will not allow full control of the heater, but you can try 220K instead…or you can use two 100K pot in series.
no other resistors will need to be changed.
it might work with pumps and ACs but it is not recommended…
yes it will reduce power consumption proportionately as the intensity of the load is reduced
Hi what kind of capacitors are these thanks
those are metalized polyester type or polypropylene (PPC) type will also do
https://www.homemade-circuits.com/2016/02/types-of-capacitors-explained.html
Hi I am very interested in this circuit
I wish to use it for a 5500 watt water heater. Would I be right in saying I would only have to upgrade the triac? And also what type heatsink would be appropriate? Thanks in advance
Hi, you can use the above circuit for your application, the same triac which is shown in the diagram can be used, or a BTA41/600V can also be tried, but make sure it is mounted on a large heatsink…..and also the diac should be rated to handle at least 100mA
Hi Sir,
What component/s should be replace to run this circuit with 4000 watts load/heat lamp.
Thank you!
Fritz, only the triac will need to be replaced with a BTA41/600V rest can be as is.
sir how to make 40uh chock??
don't use it… it's not important
sir i have done it but i am not able to adjest variable resistor(heatis not regulating), and my 40uh is heating.what i should do??
first test it using a 200 watt bulb to ensure that everything is correctly done in your circuit…after that you can use the heater coil…make sure the triac is mounted on a heatsink
what componets should i replace to work this ckt for 2000W,10A heating load, and what r the names of diac triac and its rattings
you can use the same design that's shown above.
preferably use a 220k pot instead of the shown 470k
Not sure what that is, but I'll do some googling. 🙂
Thanks for your time and help.
you are welcome 🙂
Sorry I wasn't that clear. Let me try this again. I'm asking for your help because your circuit here is close to what I would like.
I have a forced air heater that is rated at 1500 watts, 6.3 amps that I would like to control, on/off, with a MCU. It doesn't need any thermostat functions, I'll handle that via code. I don't have much room where the wiring is located in the wall so something small would be nice. An added bonus would be to combine a power AD/DC circuit into this design. I already have power, just need to convert it to DC. I don't what to have to run a AC/DC adapter for power as I don't have an outlet near the area I'll be accessing the power/wires for the heater.
I tried using a 25 amp SSR like this one http://www.ebay.com/bhp/ssr-25da but it failed. It got way too hot. I would rather not use a mechanical relay due to the clicking sound and the possible arcing of the relay. I also bought a 16 amp SSR but it gets too hot also. I read that the SSR should be twice the rating as the device it is controlling but I think I'm still missing something else to keep the circuit small and cool.
If this still isn't clear I can try again or if I'm asking for too much help I understand.
Thanks for your time and help.
From your explanation it appears that you intend to control the heater through some kind of predetermined algorithm through your MCU, that would periodically switch OFF and ON the heater and try to maintain the temp at the required level.
In that case the above circuit may be completely irrelevant to your need.
even the relay or the SSR won't be required.
You just have to feed your MCU trigger to a MOCxxx based circuit and enjoy a smooth implementation of the system.
Not sure if my other post went thru, but thanks. That link is a good start. I had a S216S02 and built the relay driver for it. It's working but I'm sure it isn't going to handle the 1500 watt heater, or will it? I'm not sure how to finish this so it can. I can't quite make out the parts needed for you circuit or how to get the relay driver to work with it either. Your help with this is appreciated.
Thanks
yes I have answered your previous comment, I may be late but I normally never miss any.
the relay is supposed to be at least 20amp rated, such as this one:
http://www.aqua-man.com/mmAM/images/row_num/49768.jpg
the relay driver transistor should be a 2N2222 for handling this type of relay.
actually you should have explained the entire sequence of the required operation, so far you have mentioned it in bits and parts…if possible tell me the whole sequence then probably I'll be able to help you in a better way.
That's a perfect start, thanks. Now, how do I integrate the relay driver with this circuit to drive the 1500 watt heater? Also, if it's possible, can I add to this circuit the ability to supply 5v DC to power the MCU?
Thanks for your time and help, I really appreciate it!
connect the relay pole to one of the AC inputs, it could be the phase or the neutral doesn't matter. connect the N/O contact with one of the input wires of the above circuit and let the other wire connect directly with the second mains supply input.
this will control the ON/OFF switching of the above circuit but the actual heat control can be implemented only through the given 470K pot
…the 5V could be derived from the 12V relay supply through a 7805 IC…and the 12V can be obtained from a 12V AC/DC adapter.
Swagatam, I'm hoping you can help me out with this type of circuit. I'm not an electronics expert so reading most circuit diagrams are just confusing, but I'm trying to learn.
I would like to create this circuit but I need it to control a 1500 watt, 6.3 amp restive load heater via a MCU. I have to watch the heat and would like the circuit to be as small as can be. Can you help point me in the right direction? Maybe a circuit design a preschooler could figure out? 🙂 I would love it if I could also pull 5v dc for the MCU at the same time?
What I'll have available at the mains wall is the line that completes the circuit. I would like to not have to rewire the the line to the heater for this circuit. Crude drawing below to help, hopefully.
AC from wall –> to heater
++ = this would be the relay/power circuit to complete the circuit to turn on the heater.
+ = ground is tied straight thru to heater
(common) ——- (++) ———
AC Heater
(ground) ———–+———-
Thanks for the help,
I appreciate your interest John , however my knowledge regarding MCU programming is not great so it would be difficult for me to program the coeds for you, so I am sorry I won't be able to help you with this implementation.
…or if you think I did not understand your requirement, I would request you to explain it with more detail.
Thanks for the response, What I'm after is just the relay/power circuit that would have a pin that I could connect to the MCU, so I would raise the pin high and it would trigger the relay. I'm good with coding the MCU just not with electronics so trying to figure out your circuit and modify it for my heat requirements and adding a pin for control on/off is beyond my skill set. This would be something like the link below but of course better and with the requirements above.
https://www.sparkfun.com/products/10684
Thanks for the reply. I'm actually just looking for help with the circuit. I was hoping your design could be modified to have a pin that the MCU would connect to so it could trigger the relay on/off. I can code the MCU just can't design circuits.
Thanks
OK, then I think the following article would help you to solve your problem quickly, please refer to this:
https://www.homemade-circuits.com/2012/01/how-to-make-relay-driver-stage-in.html
In the above referred relay driver stage, the base of the transistor could be connected with the MCU trigger, for activating or deactivating the associated relay… this is what you were looking for, right?
Sir, could you please tell me what changes are required in this circuit to make a heat controller circuit for about 500W-700W, 10-15A device powered from a DC source of 48V?
Sheri, you can try the following circuit:
https://www.homemade-circuits.com/2012/05/make-this-pwm-based-dc-motor-speed.html
just replace the fan with the heater system
Swagatam, Thank you for your prompt answer. One further question. Is this considered a "Constant Current" controller? I guess a typical thermostat control has a range when it switches on or off, a sort of fluctuation range? Is this a stable control when set? Sorry for the basic questions. Thank you.
Kurt Kenyon
It can be considered as a constant voltage controller, and if the voltage is constant current will be also constant.
so, a fairly good consistency can be expected using this circuit in terms of power output to the load.
Swagatam, Can this setup be used with 110v and 1500 watt element? What would need to be changed? The element I was thinking of is for a hot water heater. Thanks so much.
Kurt
Hi Kurt, yes it can be used with a 110V input, the 470k pot will need to be replaced with a 220k pot, that's all…rest can be as is
Dear sir,
I have eurotherm TS200A temperature controller.this is thyrister based. This required 0-5V control voltage. I want one temperature control circuit when temperature is 25deg C the voltage is 0V. Temperature reduces the control voltage increase from 0-5V. Please provide the circuit diagram.
Thank you.
Dear Suresh, I'll try to post it soon in my blog.
Sir,
I want to make it for 2000 W water heater/Gyger, before construction I want to make clear some points
1. Resistances are used here — what are there wattage value
2. Capacitor are used here are of micro farad or nano farad?
3. How to arrange/make the inductor, if we omit this will circuit work ? what is the wattage value of inductor, if possible mention the range of inductor(from this value to this value) which will work,
4. Both diac and triac needs heat sink
regards,
Akash
Akash,
all the resistors can be 1/4 watt rated.
capacitors are all uF (microFarads)
Inductor may be built by winding around 100 turns of 1mm magnet wire over a 1cm diameter ferrite rod
only the triac would need a heatsink, not the diac.
Thanks for the reply
Can't figure out what's wrong. The diac is not polarity sensitive.
no diacs are never polarized but here it should be a heavy duty type not the usual small blue colored ones, the right one would look quite like a 1N5402 diode.
try the circuit with the 200 watt lamp initially, once the dimming function is confirmed you can go ahead with the intended higher load
Thanks for reply
Can only find small coloured diac
Spec shows itrm=2A p=150mw
could this be the problem?
Any makers name part number etc
Thanks
You can try it out, probably use two of them in parallel with individual 100 ohm resistors, might just work.
Hi
Tried your circuit and blown two triacs. Please confirm the connection of triac.
You say the centre connection should go to the capacitors but the data sheet shows the centre is T2 which the diagram shows connected to 15K & choke. Tested using 40watt bulb as a load and each time it flickered few times and the triac failed.
I am sorry, it should be the left lead (A1) which must join with the capacitor common rail while the center lead goes up and joins with the 40uH choke.
you can try other lower values such as 0.022, 0.033. 0.047, 0.068 etc
use BTA04/600 triac
No, you will have to make it.
this circuit can use for as a 2000w motor dimmer swich?
yes, can be used.