In this post I have explained some basic facts about DC to DC buck converters and also learn how to build a simple buck converter circuit. A buck converter is also popularly known as a step-down converter, since its basic function is to step down a higher input voltage level to a lower output voltage level, with high efficiency.
- Advantages of Buck Converters Compared to Linear Regulators
- Basic Working of a Buck Converter Topology
- Modes of Operation
- Making a Practical Buck Converter Design
- Upgrading the Circuit for Higher Loads
- Simple Two Transistor Buck Converter Circuit
- Parts List
- How to Build
- How to Test
- How to Measure the Efficiency
- Adjustable PWM Buck Converter Circuit
The practical buck converter circuit explained here uses only 3 transistors and is extremely easy to build. Even though the circuit is simple, it has a high efficiency.
The circuit can be used to drive 3.3 V LEDs from a higher input supplies such as from 12 V, or 9 V supply inputs.
The buck converter design can be also easily upgraded to operate higher rated loads instead of an LED.
Advantages of Buck Converters Compared to Linear Regulators
The main advantage of a DC to DC buck converter compared to a linear regulator is that buck converters are hugely efficient than linear regulators.
Linear regulators such as IC 7812, IC 7805, LM317, LM338 waste a lot of energy through heat dissipation, whereas heat dissipation in buck converters is minimal.
Due to minimal heat dissipation, a heatsink may not be required in buck converters, or this may be very small in size.
The efficiency of linear regulators may range between 25% and 50%, the efficiency of buck converters is mostly around 90%.
Basic Working of a Buck Converter Topology
Referring to the figure below, let's try to understand how a 'buck' or a 'step-down' converter works. With a buck converter circuit, a higher input voltage can be transformed into a lower output voltage. Its basic mode of operation is described as follows.

As soon as switch S is pressed, a positive voltage develops across the inductor L. This is because UIN is higher than Uout. The coil initially tries to resist the instantaneous current flow. As a result, the current in the coil increases linearly, and energy begins storing in the coil.
Next, as soon as switch S is opened, the stored current flows through the coil into the output capacitor through diode D.
Since the voltage UL across the coil is now negative, the current through the coil reduces linearly. The output receives the energy that was captured and stored in the coil. Now, if Switch S is closed once again, the procedure begins afresh and keeps repeating as the switch is operated ON/OFF.
Modes of Operation
The voltage that appears at the output is determined by how the switch S is operated. According to figure below, there are three basic types of current flow.
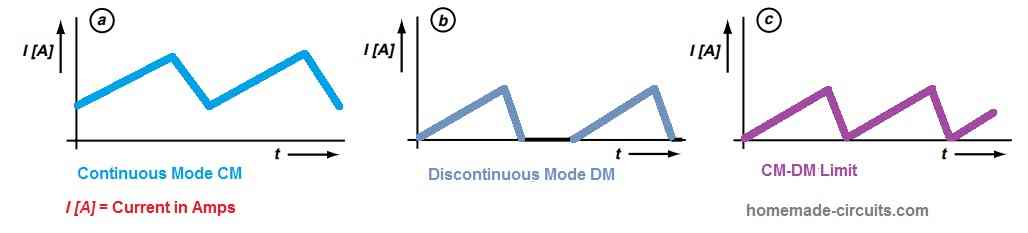
- Referring to the figure (a) above suppose, the switch S is closed and opened such that the current flowing inside the coil isn't able to reach zero. In this situation a constant flow of current will be experienced through the coil. This is referred to as "continuous mode" (CM).
- Now let's imagine the switch S is closed and opened such that current is able to reach zero for part of the cycle, as illustrated in Figure (b). Then the circuit can be assumed to be operating in 'discontinuous mode' (DM).
- In the third scenario if suppose the switch is closed and opened such that the coil current is able to exactly reach zero as shown in figure (c), then we call this as CM/DM limit operation.
This means that, in a buck converter both the output voltage and power could be varied by adjusting the "on" periods of the switch. This is also called the mark-space ratio.
That's enough theory; now let's examine a straightforward real-world circuit.
Making a Practical Buck Converter Design
The following figure shows a simple practical DC to DC buck converter circuit using only 3 transistors and a few other passive elements.
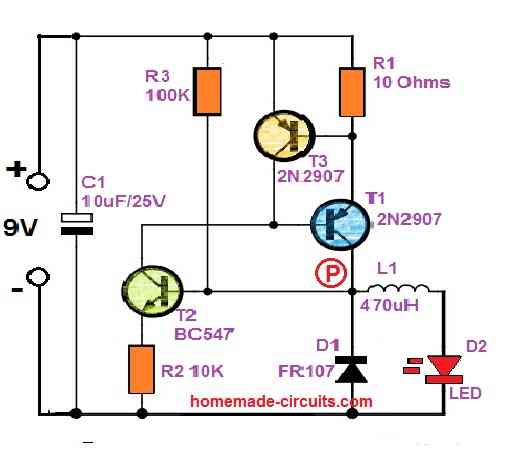
It works in the following manner:
Switch S in this circuit is represented by transistor T1. The other components of the step-down converter are diode D1 and coil L1.
As soon as the circuit is powered, R3 supplies a base current to T2 (because D2's forward voltage spec is larger than 0.7 V) and T2 is switched ON.
With T2 conducting, T1 gets a base bias and it also begins conducting. In this situation, point P experiences an increase in voltage, which causes T2 to conduct even harder.
Now as point P's voltage reaches 9 V, the current through L1 starts to increase. The voltage across the coil and its inductance both influence how quickly the current inside it increases.
As the current across the coil increases, the voltage across R1 decreases. As soon as this potential hits 0.7 V (about 70 mA) causes T3 to turn ON. This quickly removes the base current of T1.
Since the current in L1 can now no longer increase, the voltage at point P starts to decrease. T2 as a result is switched off, followed by T1.
The current via L1 now travels via D1 until it drops to zero. This causes the voltage on T2 to increase again, and the process repeats afresh.
The transistors work as a thyristor with positive feedback, resulting in an oscillation. T3 makes sure that T1 is shut off at the predetermined current and that the circuit operates in CM/DM limit mode.
Upgrading the Circuit for Higher Loads
Instead of illuminating an LED, you could employ this circuit to operate a higher rated load. But with a higher load you will find the buck converter not oscillating.
This is due to the load preventing R3 from turning on T2 at startup.
This issue may be avoided by placing a capacitor (0.1uF) between point P and the base of T2.
Another smart move would be to smooth the voltage by connecting a 10 F electrolytic capacitor across the output.
The buck converter functions as a current source instead of a voltage source and is unregulated. However, for most straightforward applications, this will be more than sufficient.
Simple Two Transistor Buck Converter Circuit
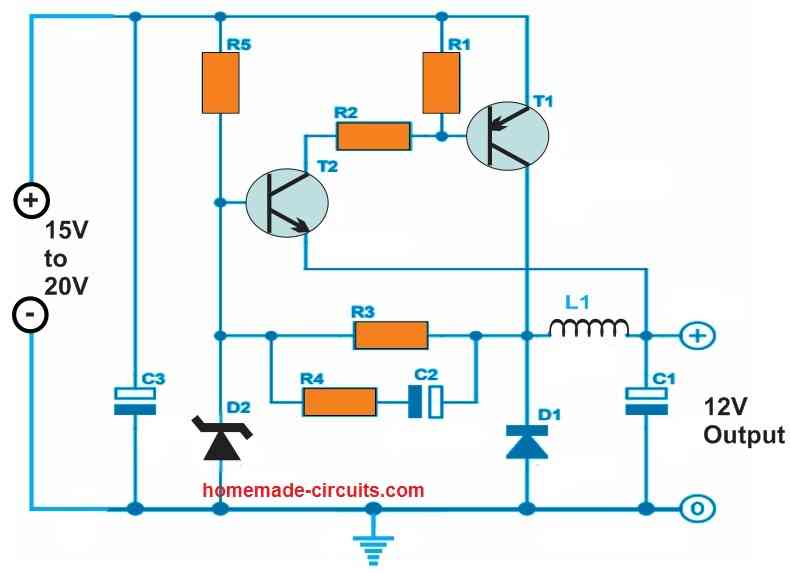
Parts List
- All resistors are 1/4 watt 5%
- R1 = 470 Ohms
- R2, R4 = 100 Ohms
- R3, R5 = 2.2 K
- Capacitors
- C1, C3 = 1000 uF/ 25 V
- C2 = 220 uF / 25 V
- Semiconductors
- D1 = FR107
- D2 = 12 V 1 watt Zener diode
- T1 = 2N2907
- T2 = BC547
- L1 = 120 uH
We can make the above design much simpler using just two transistors? Referring to the circuit diagram above, we can see a regulated step-down converter, which can generate 12 V DC from a 20 V DC. The main components of this design are transistor T1, diode D1 and coil L1.
The circuit works using the feedback between a combination of the PNP/NPN transistors. Here, the working of T1 is not dependent on the maximum coil current. Instead it is determined by the RC network of R4/C2.
The voltage regulation for this simple buck converter circuit is determined by the zener diode D2, associated with the emitter of T2.
This DC to DC buck converter design is highly efficient, which may be as high as 90%.
How to Build
- Step#1: Take 20 mm by 20 mm general purpose strip board.
- Spep#2: Clean the copper side with a sand paper.
- Step#3: Take the resistors and the diodes and bend their leads leaving 1 mm distance between their body and the leads.
- Step#4: Insert the resistors into the PCB and solder them. Cut the excess lead lengths.
- Step#5: Insert the transistors as per the same layout position as indicated in the schematic. Solder their leads, and trim the extended leads.
- Step#6: Now, insert the inductor, solder it, and trim its leads.
- Step#7: Finally insert, the capacitor and the LED, solder the leads. Cut the excess leads
Once the above assembly is done carefully interconnect the leads of the various components by referring to the schematic diagram. Do this using the pieces of the trimmed lead wires, previously cut.
If you are unable to connect the leads directly from the copper side, you can use jumper wire from the component side of the PCB.
How to Test
- Keep the LED disconnected at the start.
- Apply 9 V DC to the circuit.
- Measure the voltage across the points where the LED is supposed to be connected.
- It must be around 3 V to 4 V.
- This will confirm that you have build the buck converter correctly, and it is working correctly.
- You can switch OFF power and connect the LED back in its position.
- Now switch ON the DC again, you will find the LED illuminated brightly from the 9 V DC input with maximum efficiency.
How to Measure the Efficiency
To measure the efficiency you can connect an ammeter in series with the positive line of the 9 V DC.
Then you can multiply the current reading with the voltage (9 V).
The result could be somewhere around 20% higher than the watt specification of the LED.
This might prove an 80% efficiency for the buck converter circuit, and likewise.
Adjustable PWM Buck Converter Circuit
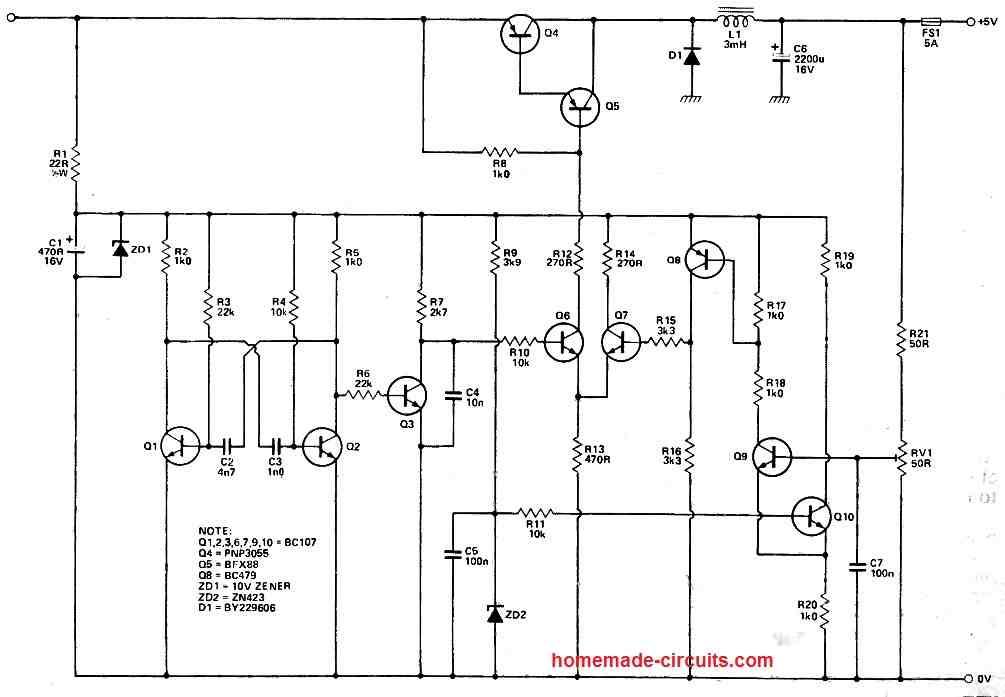
This circuit was initially designed with the purpose of generating a 5V power supply from a car battery to operate a BBC microcomputer.
Notably, the design refrains from employing integrated circuits (ICs), utilizing instead readily available discrete semiconductors salvaged from miscellaneous parts.
Efficiency Considerations
Achieving efficiencies surpassing 80%, this circuit outperforms linear regulators which generally exhibit maximum efficiencies ranging from 33% to 42%.
Astable Multivibrator and Pulse Generation
The operation commences with transistors Q1 and Q2 configured in an astable multivibrator arrangement.
This configuration yields a brief positive pulse at the base of Q3 at intervals of 50µs.
Consequently, the capacitor C4 discharges, subsequently recharging through the 2.7 kΩ resistor. This process delivers a gradually ascending voltage to the base of Q6.
Voltage Comparison and Regulation
Transistors Q9 and Q10 undertake a voltage comparison task, juxtaposing the reference voltage from the ZN423 with a segment of the regulator's output voltage.
This voltage slice derives from a potentiometer serving as the output voltage adjustment feature.
It's crucial to avoid substituting a zener diode for the ZN423, as the former's slope resistance reacts adversely to fluctuating battery voltages.
Adjustable Voltage Control and Pulse Width Modulation
As the potentiometer wiper voltage exceeds the reference voltage, Q8 activates.
Consequently, the ascending ramp at the base of Q6 must escalate to align with the voltage at the base of Q7.
This delay in activating the Darlington pair (Q4 and Q5) results in a narrower power output pulse to the choke.
This mechanism, known as pulse width modulation (PWM), in turn reduces the output voltage.
The nominal operating frequency is 20kHz, although it can vary considerably due to battery voltage fluctuations.
Output Stage and Energy Dissipation
The BY229-600 diode is specified for the catch diode, but in the prototype, a high-current rectifier proved effective.
The frequency of 20kHz seems manageable for these components.
Most wasted energy dissipates as heat in Q4, necessitating a suitable heat sink.
Output Voltage Feedback and Stability
The output voltage feedback attenuator incorporates 50Ω resistors to draw a minimum of 50mA from the output, essential for maintaining stability.
Alternatively, a 100Ω resistor could be shunted across the output, alongside a resistor and potentiometer (up to approximately 10kΩ each) to establish the correct feedback voltage.
When drawing 5A, a drop of 200mV in output voltage corresponds to an output resistance of 40 milliohms.
Grounding and Wiring
Designating the ground points with bold lines signifies their role as conduits for substantial currents.
These points necessitate robust connections, such as thick wiring or PCB tracks, tied back to a location proximate to the incoming battery's negative terminal.
This adherence to high-current grounding practices is a standard convention.
Output Regulation Strategies
The circuit does not currently encompass mechanisms for current limitation or crowbar protection.
Implementing a crowbar mechanism is straightforward, and current limiting can be achieved by manipulating Q9's base, thereby altering the power pulse's mark-space ratio.
hey sir can you tell me more about mp4560dn stepdown module !
Salman, all the details are given in the datasheet.
Please go through it. If you have any difficulty understanding it, let me know, i will try to solve it:
https://www.monolithicpower.com/en/documentview/productdocument/index/version/2/document_type/Datasheet/lang/en/sku/MP4560/document_id/305/
Hi Mr Swagatam;
On my SMPS circuit primer input side, after the rectifier bridge there are serial one resistor 220K and a capacitor (50V 100uF). The positive pole of this capacitor is also being fed by one leg of the transformer after a diode. And this capacitor is for the UC3548 PWM IC. The voltage here is about 17V. My question is the voltage as the 17V is OK or slighly higher for the IC?
And also could you please share your comment about that what kind of step down topology this is (300V DC to 17V DC)?
Hi Suat,
The max input supply voltage for UC3548 is 22V, so 17V looks fine to me…
If the SMPS has a transformer with primary/secondary winding then the topology is flyback converter topology…
I’m having a hard time figuring out how to adjust the design you have. I need a DC-DC converter with a wide 40-60 volt input to a 12-14 volt 10A output. How I got my Amatuer Extra license I don’t know. I do not understand the math and the simulators have to many variables that I am getting no where. Do you have any suggestions?
The above circuits cannot be adjusted for 40 to 60V inputs. For 40 to 60 V you can probably try the following design:
https://www.homemade-circuits.com/lm317-variable-switch-mode-power-supply/
I need some way of keeping power to my Internet router to 12v when the alternator on my boat is charging the battery bank at 14.6v.
Possibly using a zener? I have searched in vain for other solutions….any ideas? Thanks, Paul.
You can simply use a 7812 IC regulator to regulate the voltage to 12V DC.
Dear Swagatam.
Firstly thank you for this website and the depth of explanations it provides. It has boosted my confidence to try projects of my own. I would like to build a circuit to deliver a steady 5v upto 2a for a USB charging port using Lifepo4 battery 3.2v either single or 6.4v in parallel. The aim of the project is to build these for developing communities using as many sustainable or recyclable materials where possible and allow for field maintenance and a long life span. Recharging the battery is a another project as we would like the modules to be separate and plug able to make replacement easy. I have looked at the LM7805 IC but believe the input voltage would be to low?
Any advice would be very welcome.
Kind regards
Warren
Thank you so much Warren,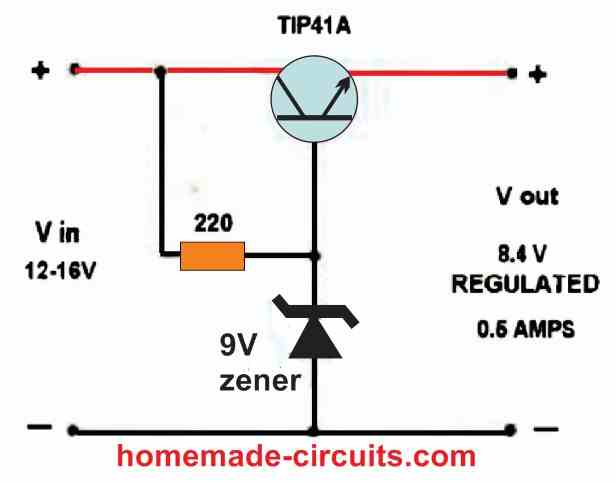
I would be glad to help you.
Did you consider using a transistor emitter follower configuration for converting your 6.4V into a regulated 5 V output?
Here’s the diagram which you can try:
" rel="ugc">
You can replace the zener diode with a 5.6V zener diode for getting approximately 5V at the emitter side of the transistor.
That is fantastic thank you. Could I ask what wattage the zener / resistor should be for safe handling of 2amp possibly more?
Thank you in advance.
Warren
Both, the zener and the resistor can be rated at 1 watt each. The transistor will require a heatsink for maintaining an optimal working temperature.
If you want to avoid the heatsink you can perhaps replace the transistor with a TIP3055 or a TIP35
Amazing, your help has made a huge difference.
Thank you
The pleasure is all mine!
Dear Swagatam.
I have built the circuit provided using the 220 resistor and ran into a problem. Under higher loads (1amp) the circuit drops to much voltage. As I am using a 5.6v zener I wonder if the 220 resistor is to high for my purpose? I have done some very basic calculations. Could you give them your professional eye please?
1w rated zener so max power is 1w/5.6v = 0.178amps
using 7.4 power pack resistor needs to handle the remaining 7.4-5.6 = 1.8v
So 1.8v/0.178a = 10ohms minimum without any margin of error / tolerances in components.
Thank you in advance.
Warren
Hi Warren,
I think the base resistor can be calculated using the following formula:
R = (Supply – 0.7) x hFE / Load current
= (5.6 – 0.7) 30 / 1 = 147 ohms
For the exact value of the resistance, the hFE of the transistor will need to be known accurately.
The zener diode calculation is much more complicated. It is provided in the following article
https://www.homemade-circuits.com/how-to-calculate-zener-diode-resistor/
Dear Swagatam.
Thank you very much for pointing me in the right direction. I think the drain is more from the rapid prototype board I am using rather than your excellent diagram and values. I will construct a soldered version and test again. Many thanks.
Warren
No problem Warren! Thank you for updating the info. I hope the problem is solved once you build the soldered version of the circuit. All the best to you.
Thank you!
Good day Swag, please can this buck converter work for 100v, 500mA to 14V system? How Sir? Likely modifications.
What will be likely current output?
Thanks Sir.
Hello Dayo, the above circuit cannot be modified to convert 100 V to 14 V, and unfortunately I do not have any other alternative circuit to do this.
Hi Swagatam,
I am so sorry to bother you with another of my questions as I am sure that you are very busy but I do not have anyone else that I can ask.
Some years ago I built a variable power supply from a kit, 0-30 volts 3 amps and it has served me well for a long time now. However I have always been disappointed with the coarsness of the voltage adjustment. The pots used are 10KA on both the voltage and current adjustments. When I need an accurate adjustment eg 3.3 volts I can never get closer that 1/10th of a volt each side of the target.
So I had an idea to replace the pots with 10 turn pots so I ordered a couple of 10K multi turn pots and fitted them both. It didn’t work how I expected it to. On the voltage pot I now go from 0 volts to 34 volts in less than a 1/2 a turn and the other 91/2 turns do nothing. I am now very puzzled.
Could you please try and explain where I have made a mistake and perhaps offer me a solution to my requirement?
Again I am very sorry to trouble you with my problem but I do hope that you can help me.
Thank you very much
Best regards.
Patrick
No problem Patrick,
I will try to help you!
If you are getting 0 to 34V in less than half a turn that means your pot range is not matching with the power supply circuit. It means 10K is a high value pot. To rectify this you can try using a 4.7K pot or a 2.2K pot. An ordinary linear pot should also work.
You can also try adding a 1K pot pot in series with the main pot. This additional pot can be used to make the coarse adjustments.
Hope this works for you.
Hi Swatam,
Thank you for your words of encouragement regarding the LM2576t-adj switching regulator. I will try and design a suitable PC board for an adjustable power suppl and see if I can get it to work. If you have the time and inclination then perhaps you could also design a 0-30 volt 3 amp adjustable power supply using this regulator and post it on your site. I am sure that it will be better and more efficient than mine. Slso I am certain that many people out there that frequent your site will have a great time building a laboratory grade power supply using this regulator as it looks much easier and a lot cheaper than a standard supply.
One more question if I may, For many years I have been receiving an email on my gmail account which informs me when you post a new circuit. Recently these emails have stopped coming. Have you stopped supplying this very valuable service or have I done something wrong? I would really like to continue to receive these notifications if at all possible. Please let me know when you can. Also when you reply to me it show on my gmail but it will not let me reply to you so I never know where to go to reply to you. Please help if you can.
Keep well and best regards
Patrick
It’s my pleasure Patrick, I will certainly think about writing an article describing how to build a 0-30V 0-50V power supply using the IC LM2576.
Presently my website is hosted on a shared hosting plan, which does not allow sending bulk emails to subscribers. That is why unfortunately I had to remove the subscribe feature and stop sending bulk emails whenever a new post is posted. I even had to delete all my 2000 subscribers because of this restriction. Earlier my site was hosted on a VPS account which allowed me to send bulk emails but since I could not manage my VPS account I migrated to a shared hosting plan with the above restrictions.
Regarding the email reply feature for the comments I will check the issue, and if possible try to find a solution, presently I seem to be clueless, but I will surely look into it and try to solve it soon.
Hi Swagatam,
Again I could not reply to you on my gmail and I had to come to your site to reply. I look forward to you possibly finding a solution to this issue.
I now understand why I do not receive notifications as I used to and that is OK. I will visit your site regularly to see what is new.
I will be very interested to see what your LM2577t -adj looks like asc I think this will make a very up to date efficient variable power supply.
Look at Aliexpress LM2596 CC/CV board for a very cheap price. I have ordered a couple of them to see what they are like. I will change the trim pots for 10k conventional pots and see how it goes.
Instant variable power supply with adjustable current with next to no work. I don,t know what the middle trim pot is for so if you have a look at it then perhaps you could explain it to me.
Thanks again, always a pleasure to communicate with you.
Stay well
Best regards
Patrick
Hi Patrick,
I checked the comment reply system by commenting as an external user to my gmail and outlook accounts, and I could see the reply button available for the both the email notifications. So it seems the comment reply is working perfectly in my computer.
Unfortunately Aliexpress does not open in India so I am not able to open view this website.
No issues, the LM2576 circuit which you referred earlier can be also built into a very compact unit.
I am working on it, will try to finish it soon…
Hi Swagatam,
I am sorry to have troubled you with this comment reply system issue and wasted your time. Thank you for checking into it for me. Now that you have informed me that it is working I have taken another look at it and at the very bottom of the email is a reply button. When I use this button to reply I get a notification that tells me that the reply did not go through. Slightly further up is a blue message that say “click here to reply” and I am using that now. Being 68 years old I can tell you that I am not an expert with my computer (not an excuse) so occasionally I need to be pointed in the right direction.
The LM2576t board is also available on Banggood and ebay so I don’t know if that helps.
Going through my box of bits, I have found a CC/CV board with an LM2596 chip on it. It is complete with capacitors and an inductor and will handle an input voltage of 45V and 3 amps. Apparently this chip is an upgrade on the LM2576 but looking at the data sheet I think that you would use one or the other depending on your requirement. The frequency is different and the accuracy and ripple and noise is slightly different but all of these values are better than my old Smartkit 1138 supply.
Also it is tiny. The board measures 48mm x 23 mm with a total height of 12.25 mm. I will be removing the trim pots from the board and adding some wires and adding 2 10k panel mount pots. It is through hole construction so this will be quite simple. I will also use a 10 amp 100 volt block type rectifier and add a small heat sink. Later if I am happy I will put a 10 turn pot on the voltage adjustment. The board also has surface mount LED’s which indicates whether it is in CC or CV mode and a third one which I think shows when it is balanced between the two. I will find that out when I test it. The whole thing goes in a box less than a quarter of the size of my existing supply obviously with the transformer externally mounted. When I have finished I would like to send you a picture but I don’t know how to do that so perhaps one day you could walk me through that.
Stay well and have a nice weekend
Best regards
Patrick
Not a problem at all, Patrick! Glad you could figure out the reply button for the comments.
I checked the LM2576 module on Banggood, it is indeed very neatly built and very compact.
The trimpots should be actually replaced with a potentiometer for enabling easy control of the parameters.
I hope you are able to implement the modifications correctly and achieve the intended results.
For sending the pics would you able to upload it to a free image hosting site and provide me the link here? I will check it out quickly. Here’s one of those sites where you can upload the images:
https://imgur.com/upload
All the best to you!
Hi Swagatam,
When I have finished I will try and send you some pictures. I will be using the LM2596 for this experiment. There is also an XL4015 module CC CV PWM module which I have been using for the last year to charge 12 volt 5ah lead acid batteries for when we have load shedding here. (usually twice a day and sometimes more) and it works really well and that module would also work well as a power supply. It requires 7 to 35 volt supply and it delivers 3 amps. I wish I had thought of this sooner. I don’t know what the benefits are between PWM and a switching regulator so maybe one day you can explain that to me so that I can make a more informed decision as to which is best in this application.
If I struggle to upload picture then I will enlist the help of my daughter, she is much smarter than I am.
Stay well
Best regards
Patrick
Thank you Patrick,
I appreciate your valuable feedback.
Yes, the XL4015 is also an efficient buck converter power supply, that can handle upto 5 amps.
In a PWM power supply the average output can be adjusted to lower values as desired but the problem is that, the peak voltage will be always equal to the input supply, which can be bad for sensitive electronic circuits. Another problem with PWM power supply is that the output will be in a pulsed form and not a constant DC. In a switching power supply such as a buck converter the peak voltage is also reduced to the desired value and the output DC will be without any ripples….so switching regulators are the most efficient. However, a PWM is also invariably used in switching regulators to control the inductive voltage of the inductor. So basically PWM is a tool which is most efficient when used with a switching (inductive) power supply regulator circuit.
Hi Swagatam,
I could not reply to your last message so this one might be out of sequence. I hope that it finds toy OK.
So the XL4015 I will use as a lead acid battery charger and the LM2596 I will try as a variable power supply. That should keep my sensitive aircraft instruments safe from damage.
I really appreciate you sharing your valuable knowledge with me, I have learned so much from you aver the years so thank you.
I have removed the trim pots from the LM 2596 module already which was quite easy to do and I am busy replacing them with 10k panel mount pots. I will let you know later how it turns out.
Keep well
Best regards
Patrick.
That sounds great Patrick! Glad you found my suggestions helpful.
And thanks for updating the progress! I hope you will be able to finish the project soon and get the best results from it.
In the meantime I will try to finish the LM2576 (1.2V to 50V) power supply circuit article.
Hi Swagatam,
Again no reply button on your last message so it seems that there is still a problem. I had to reply to an earlier message which has a reply button. All of my messages to you have a reply button but I don’t really want to reply to myself.
I have made good progress on this project and I am now just putting together the transformer/rectifier/smoothing circuit so I will report back to you soon.
Best regards
Patrick
Hi Patrick,
As per the settings, each comment thread can have upto 10 comments. After 10 comments the reply button is no longer available, then you will have to start a new comment thread.
Sure, do let me know when you have finished.
Thanks for updating the information.