Are you wondering if it was possible to build a very simple MPPT circuit using ordinary parts like IC 555 and IC 741, which would work most efficiently imitating a true MPPT? The answer is yes, it is possible, and we will learn about it details, in the following article.
- What Happens When Sunlight is Strong:
- What Happens When Sunlight Goes Weak:
- IC 741 Stage — Solar Panel Voltage Tracking and MPPT Adjust
- How it Works:
- Now Suppose Panel Voltage Drops Suddenly:
- What This High Output Does:
- Final Effect:
- Buck Converter Inductor Formula
- Example: Based on Your Circuit
- Example:
- Step 1: Calculate Duty Cycle
- Step 2: Plug in Formula
- Final Answer:
- Bro Tip:
- Summarizing:
In this design I used the IC 555 as a variable PWM generator. That means the IC 555 here is continuously creating a train of pulses at its pin#3. These pulses decide how fast or slow the MOSFET IRF540 is switching, which means how much power is allowed to reach the battery.
But now the trick part—this PWM pulse width is not fixed, it is controlled from solar panel voltage. That is done using pin#5 of the 555 which is connected to solar panel output through a preset.
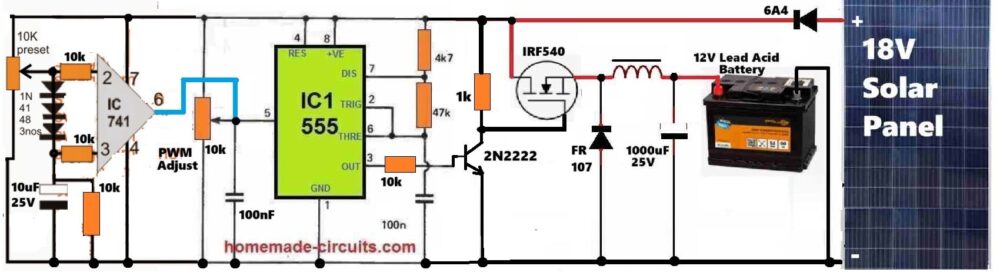
What Happens When Sunlight is Strong:
- Solar voltage increases.
- The voltage at pin#5 of IC 555 also increases.
- Because of internal modulating function, PWM duty cycle at pin#3 increases (pulse width widens)
- This means MOSFET gets more ON time, but wait...
This wide PWM from 555 goes to the 2N2222 inverter, and inverter flips the logic, so final PWM reaching MOSFET gets narrowed!
So result:
- At high sunlight, MOSFET duty cycle reduces.
- Buck converter takes less power.
- This makes sure solar voltage does not drop too much.
- Panel keeps running at optimal voltage level (around MPP).
What Happens When Sunlight Goes Weak:
- Solar voltage drops.
- Voltage at pin#5 of 555 drops.
- PWM at pin#3 of 555 becomes narrow.
- 2N2222 flips it again → output becomes wide PWM to the MOSFET gate.
- So now MOSFET stays ON longer.
Which means:
- Buck converter pulls more current.
- Tries to keep power flow steady.
- But because panel is weak, the circuit starts dropping PWM again to stabilize the panel voltage.
- This is a balancing act – done continuously.
IC 741 Stage — Solar Panel Voltage Tracking and MPPT Adjust
Now bro, this second part is what makes your circuit behave like real MPPT.
This part uses an opamp 741, which is comparing solar panel voltage drops with a memorized older solar voltage. This "memory" is stored using a capacitor and diode trick.
How it Works:
- Pin#2 (inverting input of opamp) gets real-time solar panel voltage.
- Pin#3 (non-inverting input) gets the same voltage, BUT passed through 3 diodes.
- These 3 diodes drop about 1.6V total.
- So pin#3 always stays ~1.6V below pin#2, as long as solar voltage is stable or increasing.
- There is a 10uF cap at pin#3 side – so voltage drops slowly.
Now Suppose Panel Voltage Drops Suddenly:
- Due to some load pulling high current (battery very discharged).
- Pin#2 voltage drops instantly.
- But pin#3 cannot drop that fast, because it is held by the capacitor.
- Now pin#3 becomes higher than pin#2.
- So opamp output goes high.
What This High Output Does:
- Sends high voltage to pin#5 of 555.
- Makes PWM duty cycle wide at 555 pin#3.
- After 2N2222 inverter, the gate of MOSFET gets narrow PWM.
- MOSFET ON time reduces.
- Buck output power reduces.
- Load current reduces.
- Solar panel voltage recovers back up.
Final Effect:
This 741 stage creates a feedback loop that senses when panel is dragged too hard and then immediately cuts load, lets panel recover and then slowly increases PWM again.
This action is just like real MPPT sampling technique, reduce power when panel voltage drops and try to maintain panel always at its maximum power voltage point (MPP).
Buck Converter Inductor Formula
L = (Vin - Vout) × D / (f × ΔI)
Where:
- L = Inductance in Henry (H)
- Vin = Input voltage from solar panel (V)
- Vout = Output voltage to battery (V)
- D = Duty cycle = Vout / Vin
- f = Switching frequency (Hz)
- ΔI = Ripple current through inductor (A), usually 30% to 40% of load current
Example: Based on Your Circuit
Let us assume:
- Vin = 18V (solar panel under full sun)
- Vout = 13V (for charging 12V battery)
- Load current = 4A (so ripple 30% of 4A = 1.2A)
- f = 50kHz (PWM frequency of 555 IC)
Example:
Let us assume:
- Vin = 18V (solar panel under full sun)
- Vout = 13V (for charging 12V battery)
- Load current = 4A (so ripple 30% of 4A = 1.2A)
- f = 50kHz (PWM frequency of 555 IC)
Step 1: Calculate Duty Cycle
D = Vout / Vin = 13 / 18 = 0.72
Step 2: Plug in Formula
L = (Vin - Vout) × D / (f × ΔI)
= (18 - 13) × 0.72 / (50000 × 1.2)
= 5 × 0.72 / 60000
= 3.6 / 60000
= 0.00006 H
= 60 µH
Final Answer:
L = 60 µH inductor
That means, for best performance of your buck converter with 18V solar input and 12V battery output at 4A load, you should use around 60 microhenry inductor.
You can use toroidal or iron core inductor rated at least 5A current with low resistance for best results.
Bro Tip:
If switching frequency is lower like 20kHz then L will go up:
L = 3.6 / (20000 × 1.2) = 150 µH
So lower frequency = bigger inductor and higher frequency = smaller inductor, but more EMI.
Summarizing:
- 555 makes PWM, controlled from solar voltage.
- 2N2222 flips it, feeds it to MOSFET gate.
- When sun is strong, MOSFET gets less ON time (voltage maintained).
- When sun is weak, MOSFET gets more ON time (current increased).
- 741 compares present and previous solar voltage.
- If voltage falls too fast, it makes 555 give max PWM.
- After inverter, this cuts down MOSFET PWM.
- Load current reduces, panel voltage goes up again.
- Then again PWM increases slowly... cycle repeats.
Need Help? Please Leave a Comment! We value your input—Kindly keep it relevant to the above topic!