If you are wondering if there's an easy way to implement an H-bridge driver circuit without using the complex bootstrapping stage, the following idea will precisely solve your query.
In this article I have explained how to build an universal full-bridge or H-bridge MOSFET driver circuit, using P-channel and N-channel MOSFETs, which can be used for making high efficiency driver circuits for motors, inverters, and many different power converters.
The idea exclusively gets rid of the standard 4 N-channel H-bridge driver topology, which imperatively depends on the complex bootstrapping network.
Advantages and Disadvantages of Standard N-Channel Full Bridge Design
We know that full bridge MOSFET drivers are best achieved by incorporating N-channel MOSFETs for all the 4 devices in the system. The main advantage being the high degree of efficiency provided by these systems in terms of power transfer, and heat dissipation.
This is due to the fact that N-channel MOSFETs are specified with minimal RDSon resistance across their drain source terminals, ensuring minimum resistance to current, enabling smaller heat dissipation and smaller heatsinks on the devices.
However, implementing the above is not easy, since all the 4 channel devices cannot conduct and operate the central load without having a diode/capacitor bootstrapping network attached with the design.
Bootstrapping network requires some calculations, and tricky placement of the components to ensure that the systems works correctly. This appears to be the main disadvantage of a 4 channel MOSFET based H-bridge topology, that common users find difficult to configure and implement.
An Alternative Approach
An alternative approach to making an easy and universal H-bridge driver module that promises high efficiency and yet gets rid of the complex bootstrapping is by eliminating the two high side N-channel MOSFETs, and replacing them P-channel counterparts.
One may wonder, if it's so easy and effective then why is it not a standard recommended design? The answer is, although the approach looks simpler there are a few downsides which may cause lower efficiency in this type of full bridge configuration using P and N channel MOSFET combo.
Firstly, the P-channel MOSFETs usually higher RDSon resistance rating compared to N-channel MOSFETs, which may result in uneven heat dissipation on the devices and unpredictable output results. Second danger may be a shoot-through phenomenon, which can cause an instant damage to the devices.
That said, it is much easier to take care of the above two hurdles than designing a dicey bootstrapping circuit.
The two above issues can be eliminated by:
- Selecting P-channels MOSFETs with lowest RDSon specifications, which may be almost equal to the RDSon rating of the complementary N-channel devices. For example in our proposed design, you can find IRF4905 being used for the P-channel MOSFETs, which are rated with an impressively low RDSon resistance of 0.02 Ohms.
- Countering the shoot-through by adding appropriate buffer stages, and by using oscillator signal from a reliable digital source.
An Easy Universal H-Bridge MOSFET Driver
The following image shows the P-channel/N-channel based universal H-bridge MOSFET driver circuit, which seems to be designed to provide maximum efficiency with minimum risks.
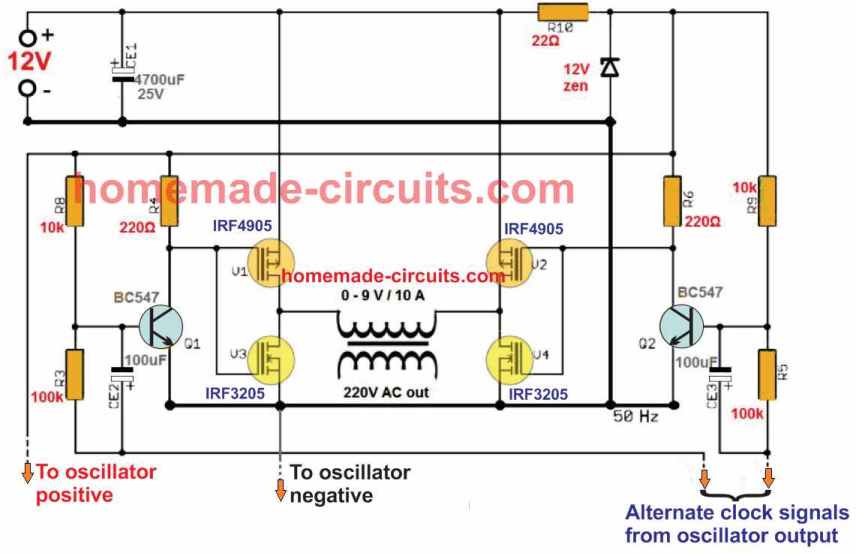
How it Works
The working of the above H-bridge design is pretty much basic. The idea is best suited for inverter applications for efficiently converting a low power DC to mains level AC.
The 12V supply is acquired from any desired power source, such as from a battery or solar panel for an inverter application.
The supply is conditioned appropriately using the 4700 uF filter capacitor and through the 22 ohm current limiting resistor and a 12V zener for added stabilization.
The stabilized DC is used for powering the oscillator circuit, ensuring that its working is not affected by the switching transients from the inverter.
The alternate clock output from the oscillator are fed to the bases of the Q1, Q2 BJTs which are standard small signal BC547 transistor positioned as buffer/inverter stages for driving the main MOSFET stage with precision.
By default, the BC547 transistors are in the switched ON condition, through their respective base resistive divider potentials.
This means that the in the idle condition, without the oscillator signals, the P-channel MOSFETs are always switched ON, while the N-channel MOSFETs are always switched OFF. In this situation, the load at the center, which is a transformer primary winding gets no power and remains switched OFF.
When clock signals are fed to the indicated points, the negative signals from the clock pulses actually ground the base voltage of the BC547 transistors via the 100 uF capacitor.
This happens alternately, causing the N-channel MOSFET from one of the arms of the H-bridge to turn ON. Now, since the P-channel MOSFET on the other arm of the bridge is already switched ON, enables one P-channel MOSFET and one N-channel MOSFET across the diagonal sides to get switched ON simultaneously, causing the supply voltage to flow across these MOSFETs and the primary of the transformer in one direction.
For the second alternate clock signal, the same action repeats, but for the other diagonal arm of the bridge causing the supply to flow through the transformer primary in the other direction.
The switching pattern is exactly similar to any standard H-bridge, as depicted in the following figure:
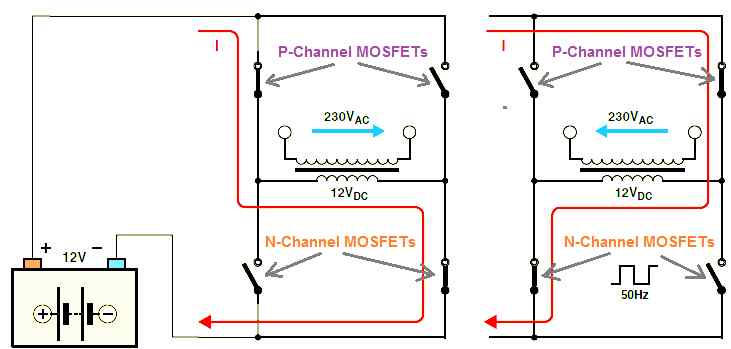
This flip-flop switching of the P and N channel MOSFETs across the left/right diagonal arms keep repeating in response to the alternate clock signal inputs from the oscillator stage.
As a result, the transformer primary is also switched in the same pattern causing a square wave AC 12V to flow across its primary, which is in correspondingly converted into 220 V or 120 V AC square wave across the secondary of the transformer.
The frequency is dependent on the frequency of the oscillator signal input which can be 50 Hz for 220 V output and 60 Hz for 120 V AC output,
Which Oscillator Circuit can be Used
The oscillator signal can be from any digital IC based design, such as from the IC 4047, SG3525, TL494, IC 4017/555, IC 4013 etc.
Even transistorized astable circuit can be used effectively for the oscillator circuit.
The following oscillator circuit example can be ideally used with the above discussed full bridge module. The oscillator has a fixed at 50 Hz output, through a crystal transducer.
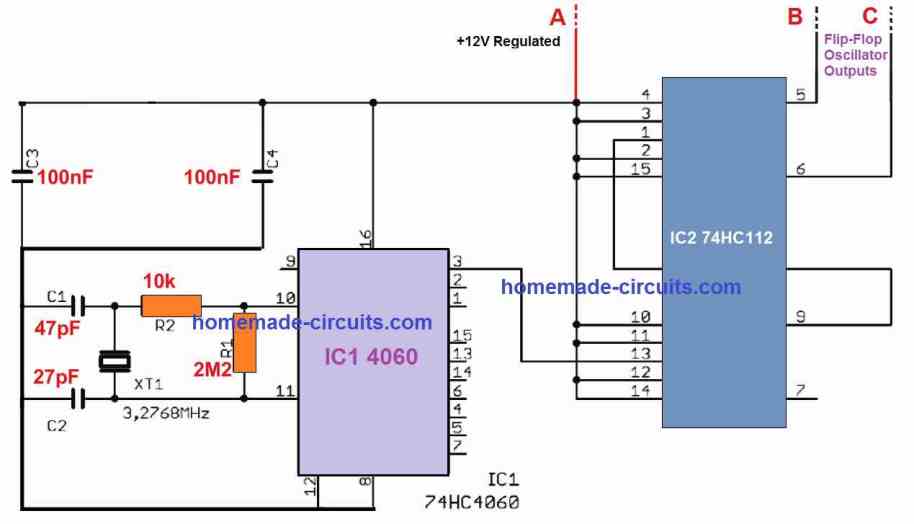
I have IC 4047 in stock pls which 24v h-brigde circuit that can work with it or with ic555 and 4017.pls I want a tested circuit pls I will be grateful for quick reply
You can use any 12V flip-flop oscillator with the previously linked circuit. Make sure to connect 12V zener diodes across gate/source of the P-channel MOSFETs as suggested earlier.
I connected the circuitry bc547 to a 12v regulator 7812 and the source of the p Channel MOSFET direct to a 24v battery because the irf4905 drain/source voltage is 55v, and not surpose to heating up and burning my mosfet. Pls am confused by you saying I should add a 12v zener diode to the gate/source of all the 4 MOSFET because I used mine as yours with same mosfet number. Can you pls show me with diagram pls it is on my neck now I want to power the inverter with a 24v 200ah*2 batteries
Actually modifying the above concept for 24V is almost impossible, instead you can try the following concept:
" rel="ugc">
Just make sure to add a 12V zener diode across the gate/source of the upper MOOSFETs, meaning, the P-channel MOSFETs.
Cathodes will go to the sources and the anodes will go to the gates.
The +310V DC can be replaced with your +24V supply, and the 4047 oscillator can be replaced with any 12V oscillator.
Pls how can I connect this circuit to a 24v battery because when I do it will be burning my mosfet
You can use 24V supply for the MOSFET H-bridge stage by connecting 12V zener diodes across the gate/source terminals of all the 4 MOSFETs
Hello Mr. Swagatam, I would like you to see a circuit for me and give me your personal opinion, it is the circuit of a three-phase electric bicycle controller box, but I took out the single-phase diagram.This scheme would also help me to implement it as an inverter power stage, greetings
Hello Adrian, you can send to
homemadecircuits
@gmail.com
I will check it out and let you know,….
Hello sir. I would like to ask you for an assembly of a 48v to 12v DC/DC converter of 40 amps. thank you very much, and good luck
Hello Ghoumrassi, you can try the second circuit from the following article:
https://www.homemade-circuits.com/5v-pwm-solar-battery-charger-circuit/
For 40 amp current you may have to replace Q2 with a 100 amp transistor, or add many transistors in parallel.
Swagatam,
We are using Hall Sensors to trigger the firing sequence, which work fine. We have both 3 pin and 4 pin hall sensors to work with. I’m not sure what is the best way to trigger the circuit. Can you please suggest hall sensors, encoder not sure what would work the best? The problem we seem to also find is as the rpm increases the timing of the firing circuit needs to change as well.
Thank you,
Scott
Hi Scott,
I can configure Hall effect sensors at the inputs of the 4049 IC NOT gates, however as far as the working sequence or the firing adjustments are concerned, I am not quite sure about them.
If you say, i can attach hall effect sensors at the inputs of the NOT gates in my previous circuit.
Let me know what you think about it.
Swagatam,
Thank you for your quick replies. I really appreciate you helping.
We have speed sensors to detect the position of the magnet above the three separate circuit poles. We want to use an “H-bridge” configuration for driving this motor, which normally would be 12 total mosfets, 4 for each circuit. This configuration takes advantage of all 3 circuits. Can you help configure this design or some configuration that uses all 3 circuit as I outlined above. Please show me how to configure this.
In addition, we need a circuit for each speed sensor to vary the timing of the pulse to the each of the 3 legs of the circuit, by using the actual speed of the motor for optimum performance.
Thank you,
Scott
Thank you Scott,
Are your motors 3 phase or single phase? If they are 3 phase then 4 MOSFET H-bridge cannot be used.
I am a little confused.
Moreover, designing a circuit for each speed sensor to vary the timing of the pulse to the each of the 3 legs of the circuit can be difficult, I have no idea how to do it.
Swagatam,
Yes, this is a 3 phase motor. I’m very thankful for your help. I’m in the process of designing my own H-bridge and your help in sorting things out about the difficulty in what I am attempting is actually reassuring too here.
This is a challenging problem and I need to do a little more work on my end so I can phrase my questions about the circuit better and clearer.
Thank you again for your support,
Scott
No problem Scott,
All the best to you.
Ghoumrassi,
My name is Scott, I am trying to build an “H” bridge system for controlling an inverter motor. I am not an EE and have struggled for years trying different designs. This is a very important project and I sure could use your help. Please let me know if you are willing to help. I am sure this is a simple problem for someone skilled in this area. I respect your time and would be willing to compensate you. If you are willing then I can give you all the information on the system.
Thankyou,
Scott
Hello Scott,
I guess the question was referred to me.
I can definitely help you to build an H-bridge PWM system to control a motor.
Please let me know the specifications of the motor and/or other related details about the system.
Swagatam,
Motor specs – “Y” configuration but can make it a Delta. I am open to a half bridge, but we seem to get a feedback that short out the mosfets on the switches or sometimes the power supply.
Thank you for your help.
Scott
Size and Poles
12” motor has 48 magnets, 36 poles, 3 – 12 pole motors with 4 to 3 ratio
7.5” motor has 24 magnets, 18 poles, 3 – 6 pole motors with 4 to 3 ratio
Wire size:
12” motor has: 0.0365” or 0.93mm Enameled Copper Wire – measured
7.5” motor has: 0.0335” or 0.85mm Enameled Copper Wire – measured
Inductance and Resistance:
12” motor has: 5.5 – 5.6 ohms and 16.76 – 16.79 mH
7.5” motor has: 4.7 – 4.8 ohms and 22.1 – 22.3 mH
Motor Spec – listed on housing
12” – 310VDC, 0.92HP, 2.8A, 1400 RPM 3F
7.5” – 310VDC, 0.87HP, 2.5A, 800 RPM 3F
Thank you Scott,
Did you try the basic 3 phase H-bridge circuit using IC IR2103, as given below?
" rel="ugc">
To ensure added protections to the MOSFETs, you can put external 1n5408 diodes across the drain/source of the MOSFETs.
Please let me know if you have any further doubts about the circuit.
Swagatam,
Thank you pointing me in the right direction. I will study it and ask question afterwards.
Scott
Hi Swagatam
I am trying to use mosfets to power 120 v to a generator (homemade). It is fired every 1/4 of a turn on the shaft with sensor (hall) and would like to know if you have a circuit for that.
I was using carbon brushes but would like to eliminate because of sparks, wear and excessive ozone generation.
Any thoughts?
Thanks!
Hi Steve,
did you try the configuration shown below? However for this configuration to work the voltage from the hall effect must be above 9V
I want to drive DC motor with H-bridge using just ,N-channel MOSFETs ,speed,and direction .
Using N channel only will be a complex design, using P channel and N channel will easy…or you can refer to the following article for more info:
Simplest Full Bridge Inverter Circuit
Hello sir. I would like to calculate an inverter, to supply an air conditioner which consumes 22A,
4.8kw. thank you for all your publications and your work. my greetings thank you again.
Thank you Cherfu, for a 4.8kW load you will need a 6 to 7kW inverter design. The transformer and battery voltage of the inverter would be around 48V, 150 amps and 1500 Ah
Hello sir and many thanks
My pleasure!
Good evening Sir,
I have built a force feedback rudder pedal unit for a flight simulator. it works well. Mostly.
The control portion consists an Arduino Uno providing a PWM signal to a BTS7960 motor controller. The motor circuit is 24v. The 24v path is Power supply > motor controller > motor. The motor control provides bi-directional movement of the motor. The motor is most often held in a stalled state, with the PWM signal varying pressure against my feet.
The issue I’m have is that the motor whines due to the frequency being generated in the 24v circuit between the motor controller and the motor. If I rasie the PWM output frequency above audible range (15.6 kHz) the motor is too weak. If I lower the frequency (8 kHz) the motor is stronger but noisy. If I use sub-audible frequency the motor creates a low frequency vibration that can be felt in the next room. I was wondering if the is a filter device that I can connect to the motor terminals/wires that will “absorb” the PWM pulses, thereby eliminating the whine.
I’m using off the shelf parts to keep the design simple as I share my designs with the flight sim community.
Thank you for your time,
John
Hi John,
As far as I know a high value capacitor connected right across the motor terminals should be able to suppress the PWM noise. You can try a 470uF capacitor and connect it across the motor terminals and check the response. I hope a freewheeling diode is already connected across the motor terminals.
I felt a capacitor was the answer too. Yet, all the answers I received in the forums (AAC, Arduino) stated that this was not possible with a bi-directional motor. But I’m going to give it a go.
how would I connect the flyback diode to a bi-directional motor? Do I need 2?
Sorry, I just missed the point that it is a bidirectional operation. However, I assume that the operation will be DC bidirectional right? meaning for some occasions the motor will spin in one direction, and for some occasion it will spin the other direction? In that case definitely a capacitor can be used, but the capacitor will need to be a non-polar type.
Capacitor cannot be the used if the bidirectional operation is an alternating current or AC type.
Diodes cannot be used across the motor in a bidirectional system.
Je cherche un circuit deja fait pour driver un circuit igbt . C’est pour driver un chargeur 3 phases sur le 600 V AC. J,ai essayé plusieurs circuit oscillant mais ca me Donne toujours *On* sans control de variation. Le circuit doit varier avec un potentiometre de 0 % a 100%. Pouvez -vous m’aider !
I have to see the 3 phase charge schematic, only then I will be able to figure out how to connect the dimming circuit with the 3 phase circuit.
I have project to feed 240 VAC Enphase micro inverters with grid simulated 240 VAC sine wave signal. The main problem I have is reverse current. I have to have Reverse Blocking IGBT . I feed from 240 VAC pure sine wave inverter to transformer 240 to 240 VAC to bridge rectifier for 240 vac to 240vdc to H bridge IGBT . What driver I need for IGBT to have sine wave 240 vac output. It is very crude circuits to simulate the grid 240 vac. only concern is reverse current to not blow the circuit
You will need an SPWM driver circuit so that you can chop the low side IGBTs with this SPWM, and convert the 240V DC into 240V sine AC.
3 Best Transformerless Inverter Circuits
Hi Swagatam,thanks for helping us to make our homemade projects.Is it possible to use more powerfull mosfets with (V drain-source = 200v or 500v) with the same V gate-source in this circuit?
Thank you tirdad, yes that’s possible, you can replace the mosfets with higher specification mosfet, however you will have to make sure that the RDsON spec of the P and N channel mosfets are almost similar.
The gate voltage can be the same for the higher voltage rated mosfets also, between 10 and 20 V
Hi sir,
i have a problem on how to use the datasheets in choosing the write components to use in my FULL BRIDGE CLASS D 500W SUPPLYING A LOAD OF 8 OHMS.can you please help me.
Hi Peter, are you referring to the MOSFET specifications for your 500 watt inverter??
Am I understanding this correctly, this 12V is being to 220V ? Can you clarify this a little bit more?
yes it is a DC to AC inverter circuit!
I found the solution in your posts.
Thanks again . ♥️
No problem!
this idea looks superb,i will try it out and give feedback. Thanks for your endless hardwork.
Glad you liked it, hope it works for you!
And how can i transform a dc voltage to frequency?
Dear Mr Swagatam
Is there any simple circuits which can measure duty cycle.
Thanks in advance for your kindness
Dear Ehsan, a DC voltmeter can be used for judging the duty cycle, since the average voltage value for the duty cycles will be directly proportional to the DC volts on the meter.
very interesting, i have a lot of questions for you, I need you send me an a mail for me to send you some circuits I.ve got to do and easy simple welder inverter to 160A